BACK
Does Voltage or Amperage Kill You?
Tool Selection: Electrical Meters
The Extension Cord Puzzle
What Causes Voltage Drop and How to Deal With It
High Capacity Amperage Measurement
Testing Run Capacitors the Smart (and Easy) Way
#amperage
Tech Tips:
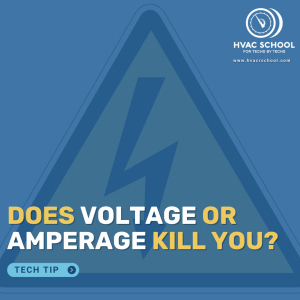
I hear the following phrase a lot: It's the amperage that kills you, not the voltage. While there is truth to the statement, it is sort of like saying, “It's the size of the vehicle, not the speed that kills you when it hits you.” OK, so that's a pretty bad example, but hopefully, it […]
Read more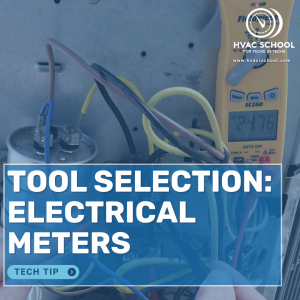
I'd like to give a special thanks to Tony Gonzalez from Fieldpiece for providing technical guidance about the SC680's power measurement capabilities, as well as VAC and AAC measurements on ECMs. We’ve talked through specifications, applications, and features for a few tools, but none of them have been quite as hardcore as electrical meters. Like […]
Read more
Suppose you have two extension cords. One is a nice, thick #10 50′ cord with good ends, and the other is a crappy #14 25′ cord. Unfortunately, you need to connect them both to get to your drill 75′ away. Which do you connect to the plug, and which to the drill? Come up with […]
Read more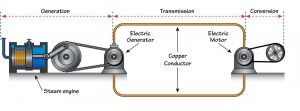
Voltage drop is one of those topics we often mention but seldom think about in-depth. From a very basic standpoint, we need to know whether or not the rated voltage is being delivered to the device or appliance while under full load, which is as simple as running the equipment and measuring the voltage at […]
Read more
We had a situation a few months back where we needed to monitor amperage on a grocery store panel over a period of time. The trouble was that we needed data-logging capability AND accurate measurement at 600+ amps. Finding an all-in-one solution proved to be quite expensive. Luckily, my friend Jim Bergmann happens to own […]
Read more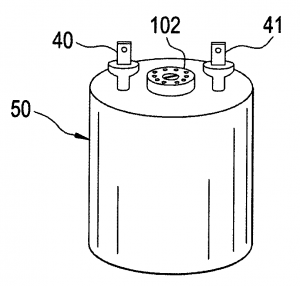
When testing a run capacitor, many techs pull the leads off and use the capacitance setting on their meter to test the capacitor. On a system that is not running, there isn't anything wrong with this test. However, when you are CONSTANTLY checking capacitors as a matter of regular testing and maintenance, that extra step […]
Read more