BACK
Decoding Measurement Lingo
Troubleshooting for HVAC/R – Repairs, Reevaluation and Wrap up
Troubleshooting for HVAC/R – Data Analysis
Turning IAQ Data Into Dollars
The Devil is in the Data
#data
Tech Tips:
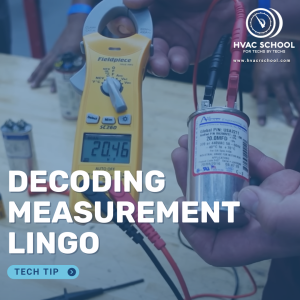
Troubleshooting and commissioning are entirely data-dependent processes. How can you know that a system is undercharged unless you measure the superheat and subcooling? How can you know how much static pressure a blower motor has to overcome? In both cases, we use tools to help us determine the next steps. However, using the right tools […]
Read more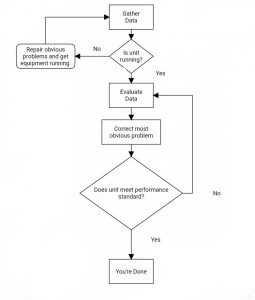
This article is part 5 of a 5-part series on troubleshooting by Senior Refrigeration and HVAC tech Jeremy Smith. This step might be the most challenging part of troubleshooting. We've got a “Most Likely candidate” for the trouble, but we don't know for certain that's what is wrong. So, we have to combine our customer […]
Read more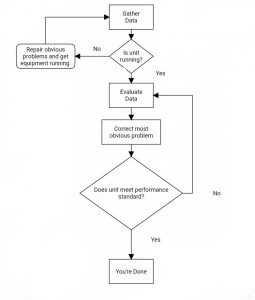
This article is part 4 of a 5-part series on troubleshooting by Senior Refrigeration and HVAC tech Jeremy Smith Ok, so we've got our data scribbled and scratched out on paper. Maybe a bit of grease, dirt, and oil, too, if you're doing things right—blood if you're doing it wrong. Now, time to take a […]
Read moreEvents:
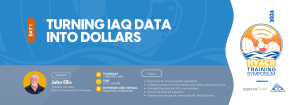
NOTE: If you cannot view the recording, the video may still be processing. The maximum wait time is 24 hours. We apologize for the delay and appreciate your patience.
Read more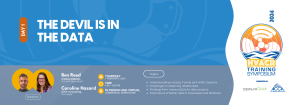
NOTE: If you cannot view the recording, the video may still be processing. The maximum wait time is 24 hours. We apologize for the delay and appreciate your patience.
Read more