BACK
Refrigerant Oil Basics
Oil Management and Diagnosis
#refrigerant oil
Tech Tips:
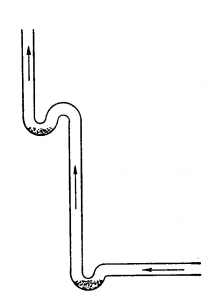
First, here's a quick summary of the role of oil in the refrigerant circuit: The compressor requires oil for the lubrication of the moving parts in the compressor. We would keep 100% of the oil in the compressor if we could. However, that is generally unrealistic. So, we need to utilize oils and oil strategies […]
Read more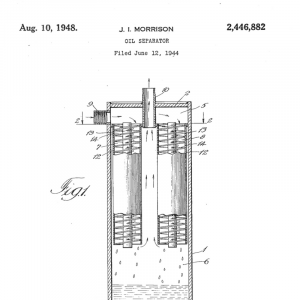
This is a subject that even many commercial guys don’t have to consider. For the majority of equipment, even refrigeration equipment, all that is required for proper oil return is to size the suction line properly, trap the suction line as needed, and allow for proper slope towards the compressor. Then we get into larger […]
Read more