BACK
Solving Delta T
Heat Pump Defrost Troubleshooting Tips
The Limitations of Diagnostic Charts
Underlying Problems That Get Missed
How I Failed to Re-diagnose: The Lesson I Learned
Wide, Narrow, Wide Diagnosis
The HVAC/R Diagnosis Pyramid of Skill
Famous Last Words (Before a Callback)
Use Your Senses First
Delta T Talk w/ JD Kelly
MeasureQuick Talks with Bert
Diagnosis, Reconfirmation, Parts Changers, and YOU
The 5 Readings Every Tech Must Know Well
Full System Diagnosis – There is More to Check
#Diagnosis
Tech Tips:
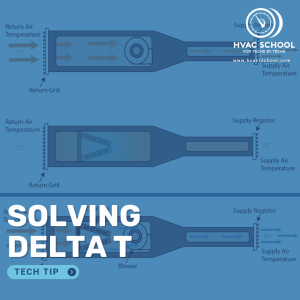
Delta T is the difference in temperature between two points of the same medium. It is commonly used by scientists and engineers to analyze the amount of heat transfer in a system. In general HVAC terms, it is the measurable change in temperature between an air input and air output. However, it could also be […]
Read more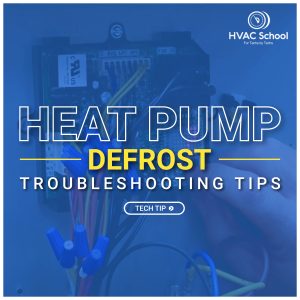
We’ve entered that season of service calls for “smoking heat pumps,” and I figured now is as good a time as any to share a few quick tips for troubleshooting defrost. Of course, the “smoking heat pump” calls can be solved over the phone with a quick explanation of normal defrost conditions—as can the service […]
Read more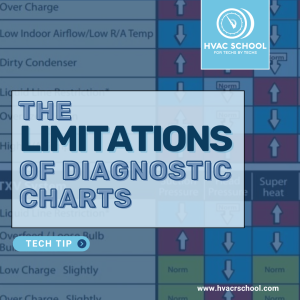
This tech tip is based on the podcast with Joey Henderson, “Using Refrigerant Troubleshooting Charts w/ Joey Henderson.” You can listen to that podcast HERE. The HVAC trade is very much a visual one; I wouldn’t recommend doing a drinking game where you take a shot each time you read “Do a thorough visual inspection” […]
Read more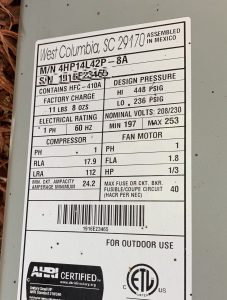
Today, I ran a service call with another tech where the previous tech had diagnosed an intermittent piston restriction. I read the history beforehand. For the past several years, there were many assorted comfort complaints and a lot of minor charge adjustments in both the summer and winter. It is worth noting here that the […]
Read more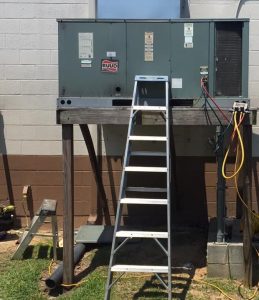
This is the tale of how I found myself stuck on a service call for over 12 hours on a weekend due to my failure to re-diagnose an issue. I was working for a service company that had many accounts with local gas stations. These were large customers, and we did everything we could to […]
Read more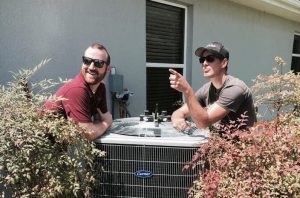
When you walk up to a piece of equipment, you want to follow a process to ensure that you accomplish five things: #1 – You diagnose the fault correctly. #2 – If possible, you find the “why” of the failure. #3 – Find any other problems or potential problems with the system that can cause […]
Read more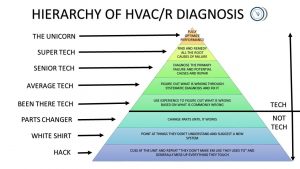
WARNING: THIS ARTICLE CONTAINS GENERALIZATIONS. IT DOES NOT APPLY TO EVERYONE, AND WE HAVE ALL PROBABLY BEEN ALL OF THESE AT ONE POINT OR ANOTHER. IF YOU FEEL PERSONALLY ATTACKED, I SUGGEST FINDING A SAFE SPACE AT A WEST COAST UNIVERSITY AND BORROWING A BINKY FROM A NEARBY TODDLER. ALSO, MY CAPS LOCK BUTTON IS […]
Read more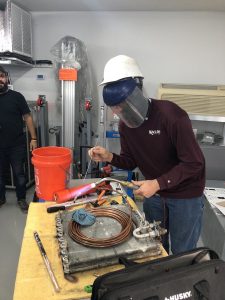
You've probably heard the famous last words, “Dude, watch this,” before a concussion, burn, shock, broken bones, or some other bodily harm. This phrase has become synonymous with young guys doing something dumb to impress their friends. Technicians have two common phrases that may not lead to bodily harm (although sometimes they might), and […]
Read more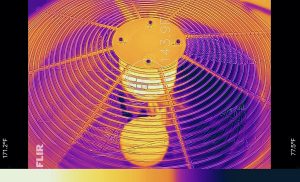
A good technician uses their senses before they use diagnostic tools. Is your suction line abnormally cold? Make sure the evaporator coil isn't frozen, and inspect for obvious airflow issues like a dirty filter or evaporator coil. Is your liquid line abnormally warm to the touch? It could be a dirty condenser, condensing fan issue, […]
Read moreVideos:
Podcasts:
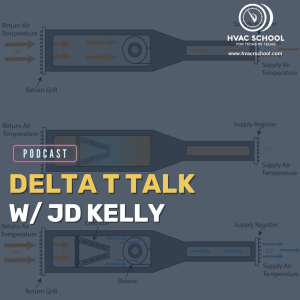
Bryan from HVAC School interviews JD Kelly, known as “student of HVAC” on Instagram, about Delta T measurements in HVAC systems. This episode dives into the fundamentals of Delta T, common misconceptions, and proper measurement techniques. JD explains that Delta T is simply a temperature difference between two points of the same medium, which […]
Read more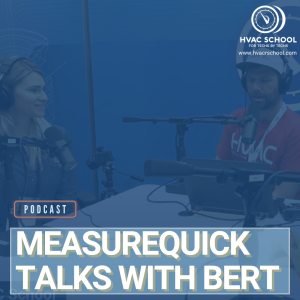
In this livestream MeasureQuick Talks with Bert. This is an impromptu Talk with industry leaders, including Shelby Breger from Conduit and Joe Medosch from MeasureQuick, about how mobile technology is revolutionizing HVAC diagnostics and training. Featuring special guests discussing how modern tools like MeasureQuick and other diagnostic apps are making it easier for technicians […]
Read more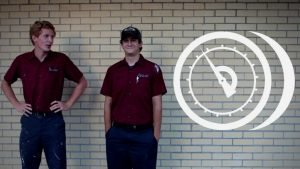
This episode of HVAC School is a Kalos meeting where Bryan talks to his team about an incident where a leak was erroneously detected on the evaporator coil. The system was three months old, and one of our junior techs diagnosed a leak on the evaporator coil. (What?? That never happens!) So, the customer was […]
Read more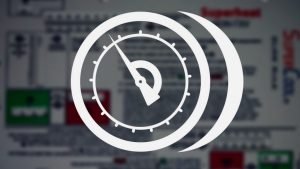
In this episode of HVAC School, Bryan covers the “5 pillars of refrigerant circuit diagnosis” and why they matter. They are: Superheat Subcool Suction pressure Head pressure Air temp split (delta T) These 5 readings give you a holistic idea of the A/C system. Instead of getting hooked on checking only superheat and subcool […]
Read more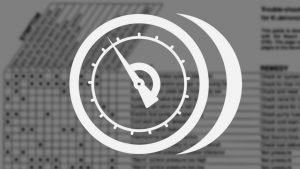
In this episode, Bryan goes back over the basics and stresses the importance of diagnosing the whole system. I'll cut to the chase: inspection is NOT overrated. Inspections help you become more familiar with HVAC systems and can help you catch on to minor issues before they spiral out of control. Check air filters, check […]
Read more