BACK
Ain’t No Fooling With Free Cooling (Tales of the Economizer)
Cleaning Condenser Coils Still Matters
Q&A – How to Learn Superheat & Subcooling – Short #191
How to Save Energy with Grocery Store Refrigeration
#efficiency
Tech Tips:
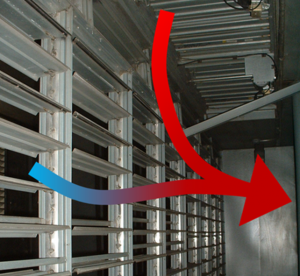
This article was written by Gary McCreadie from “HVAC know it all.” You can learn more about Gary and his tips and growing community on Facebook and LinkedIn. What is an economizer? Simply put, it is a mechanical device designed to reduce energy consumption, whether it be fuel, electricity, or other. According to Wikipedia, the first […]
Read more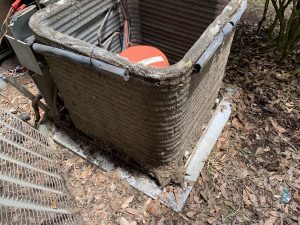
There was a story that came out recently based on an ASHRAE study performed by David Yuill from the University of Nebraska. The study appeared to indicate that condenser coil cleanliness makes no difference on system performance and efficiency. Those of us who have worked in the field know that coil cleaning matters because most […]
Read morePodcasts:
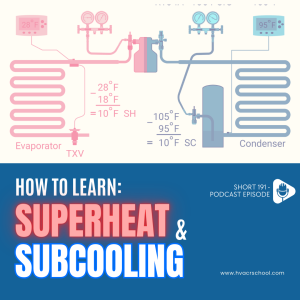
In this short podcast episode, Bryan answers an audience member's question and explains how to learn superheat & subcooling, two fundamental aspects of the HVAC/R trade. You can submit questions of your own at https://www.speakpipe.com/hvacschool. Saturation is when a substance is in the liquid and vapor state in the same place. Eugene Silberstein likes to […]
Read more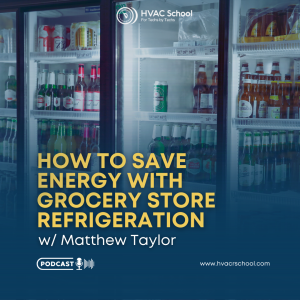
This podcast episode focuses on practical ways to save energy with grocery store refrigeration systems, with Matthew Taylor from Kalos Services sharing insights from both a technician and business owner perspective. The hosts emphasize that proper, consistent operation and preventing short cycling of compressors can have a major impact as the largest power consumers. […]
Read more