BACK
Ice Machine and Scale (Limescale)
Ice Machines – Cuber, Flaker & Nugget Basics
Ice Machines and Tech Support w/ Nick Messick
#ice machine
Tech Tips:
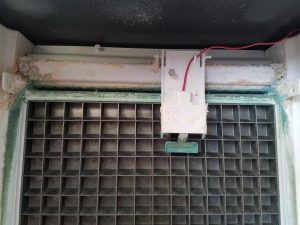
This article was written by Austin Higgins, an experienced commercial service tech from Iowa. Thanks, Austin! Ice machines and limescale Any seasoned refrigeration technician knows that ice machines can be extremely finicky contraptions. Modern commercial ice makers have become a complex symphony of tubing, valves, pumps, and water directed by advanced microprocessor control boards. Newer […]
Read more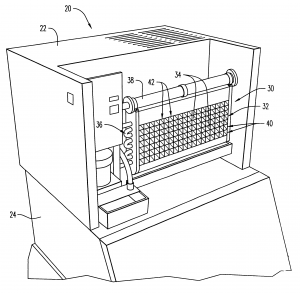
There are several types of ice machines, but in this article, we will focus on cuber style and flaker or nugget style. Both types produce ice, but the process of freezing and harvesting is a little different. The application in which the ice will be used will determine what style of machine is needed. I […]
Read morePodcasts:
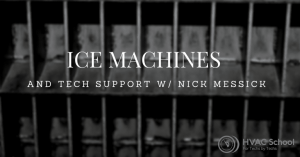
Bryan talks with Nick Messick about some ice machine basics. They also discuss how to determine when to pick up the phone and call tech support. Ice machines have the same basic refrigeration circuit as HVAC systems. However, ice machines require a much different cleaning regimen. Many maintenance people neglect ice machines by using incorrect […]
Read more