BACK
A Steam Heating Primer
Boiler Basics Part 4 – Piping
Boiler Basics Part 3 – Steam
Redux – The Lost Art of Steam Heating w/ Dan Holohan
Pumping Away & More w/ Dan Holohan (Podcast)
#steam
Tech Tips:
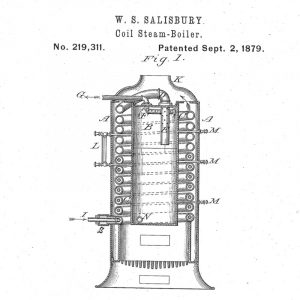
With cold temperatures right around the corner, it is a good time to brush up on our steam now, and there's no better way to do that than by reading an article by Dan Holohan. This article was written by Dan Holohan and published at HeatingHelp.com HERE. It has been reposted here with permission. This […]
Read more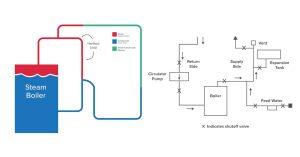
Please note: There have been some legitimate questions about a few of the points in this article and the diagrams. While Justin Skinner is an experienced tech and totally qualified to write this article, we will be specifically looking into the question of the best location of the circulator pump and addressing the “point of […]
Read more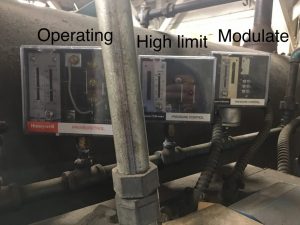
This article was written by Senior Boiler Tech Justin Skinner. Thanks, Justin. Steam plays a very important part in all of our lives, whether we know it or not. Virtually every article of clothing and accessory you are wearing right now relied on steam for either manufacturing or packaging. Hospitals use large steam boilers for […]
Read morePodcasts:
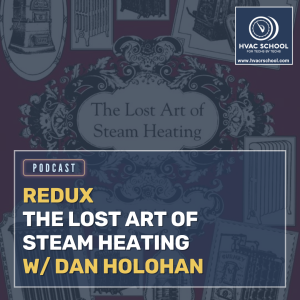
In today's podcast, Bryan talks with legendary Hydronics author and trainer Dan Holohan about the history of steam heating and some practical applications of old ideas. Recently, Dan has been working on more novels, having published two of them over the past few months. Steam heating is a “lost art” nowadays; it has become […]
Read more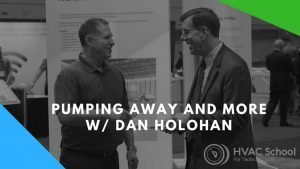
Dan Holohan speaks to Bryan about his background and journey as a writer. He also dives into his book, Pumping Away, and describes classic hydronics as he does in his book. Bryan and Dan also briefly discuss the difference between search and research. Dan is a prolific writer, and one of his most famous works […]
Read more