BACK
The Limitations of Diagnostic Charts
Angry Air
The HVAC/R Diagnosis Pyramid of Skill
Troubleshooting for HVAC/R – Repairs, Reevaluation and Wrap up
Troubleshooting for HVAC/R – Data Analysis
Troubleshooting For HVAC/R – The Don’t List
Tunnel Vision and How to Avoid It
Troubleshooting Advanced Systems
TXV Troubleshooting – Short #245
Are you using AI to Troubleshoot w/ Refrigeration Mentor
#troubleshooting
Tech Tips:
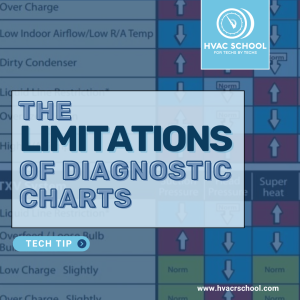
This tech tip is based on the podcast with Joey Henderson, “Using Refrigerant Troubleshooting Charts w/ Joey Henderson.” You can listen to that podcast HERE. The HVAC trade is very much a visual one; I wouldn’t recommend doing a drinking game where you take a shot each time you read “Do a thorough visual inspection” […]
Read more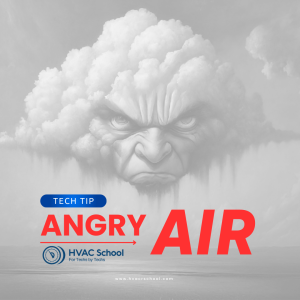
About a month ago, one of my techs went on a “no heat” call. The house is a rectory for the church next door. The call came in, and after he ran it, I assumed the problem was solved since I hadn’t heard otherwise. A few weeks later, they called back, saying the boiler was out […]
Read more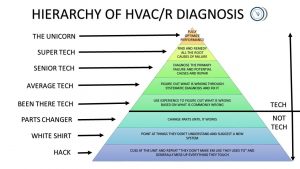
WARNING: THIS ARTICLE CONTAINS GENERALIZATIONS. IT DOES NOT APPLY TO EVERYONE, AND WE HAVE ALL PROBABLY BEEN ALL OF THESE AT ONE POINT OR ANOTHER. IF YOU FEEL PERSONALLY ATTACKED, I SUGGEST FINDING A SAFE SPACE AT A WEST COAST UNIVERSITY AND BORROWING A BINKY FROM A NEARBY TODDLER. ALSO, MY CAPS LOCK BUTTON IS […]
Read more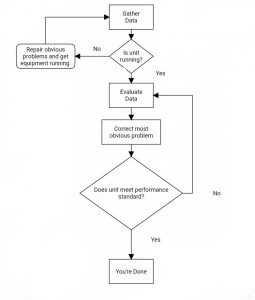
This article is part 5 of a 5-part series on troubleshooting by Senior Refrigeration and HVAC tech Jeremy Smith. This step might be the most challenging part of troubleshooting. We've got a “Most Likely candidate” for the trouble, but we don't know for certain that's what is wrong. So, we have to combine our customer […]
Read more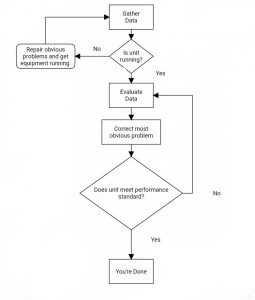
This article is part 4 of a 5-part series on troubleshooting by Senior Refrigeration and HVAC tech Jeremy Smith Ok, so we've got our data scribbled and scratched out on paper. Maybe a bit of grease, dirt, and oil, too, if you're doing things right—blood if you're doing it wrong. Now, time to take a […]
Read more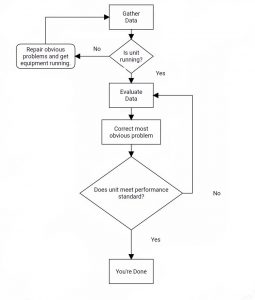
This article is the second in a 5-part series by Senior Refrigeration and HVAC tech Jeremy Smith. The Ground rules I've spent some time thinking about troubleshooting and the processes and procedures that I use to find problems. Not the “why isn't my air-conditioner running?” problems, but the “Things just aren't quite right”-type problems—the really […]
Read more
How many times has the following situation happened to you? You're on your way to that final service call. While you're listening to the customer explain their complaints over the phone, there's this precise moment where you've thought: “I know what it is already. This will be a quick one.” Sometimes, intuition proves to be […]
Read more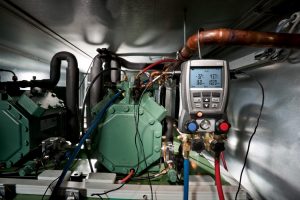
This article was written by Senior Refrigeration Tech Jeremy Smith. Before we get to it, I want to remind you that ALL of the tech tips are available in chronological order HERE, and you can sort through them alphabetically by selecting the letters and numbers above the tips. It's a great link to share with […]
Read moreVideos:
Podcasts:
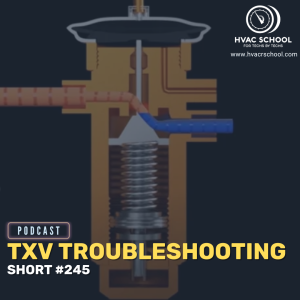
In this short podcast episode, Bryan walks through some common thermostatic expansion valve (TXV) troubleshooting scenarios. Many of the same principles apply to troubleshooting electronic expansion valves (EEVs). These dynamic metering devices maintain a constant superheat. Troubleshooting does NOT start and end with the TXV. First, you need to inspect components (especially filters, ductwork, […]
Read more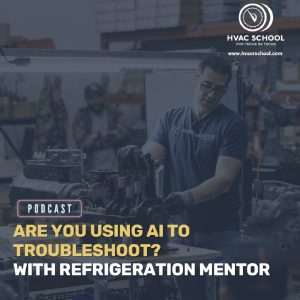
In this episode of the HVAC School Podcast, Trevor Matthews and Bryan dive deep into the transformative potential of artificial intelligence (AI) in the refrigeration and HVAC industries. They explore how AI is not a new concept in their field, discussing how manufacturers like Copeland, Sporlan, and Danfoss have long incorporated AI-driven tools and […]
Read more