BACK
3 Ways to Reduce Compression Ratio in a Heat Pump
Why Discharge Line Temperature is a Useful Reading
Why Compression Ratio Matters
Commercial Refrigeration Compressor Operation
Heat Pumps / Comfort and Electrification w/ Copeland
#compression ratio
Tech Tips:
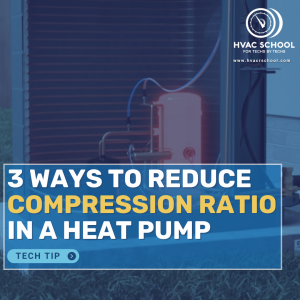
We’ve talked about compression ratio a lot over the years. Compression ratio is the number you get when you divide the absolute head pressure (PSIG + 14.7) by the absolute suction pressure (PSIG + 14.7). It measures the efficiency of a compressor, and lower numbers indicate that the compressor is moving more refrigerant while consuming […]
Read more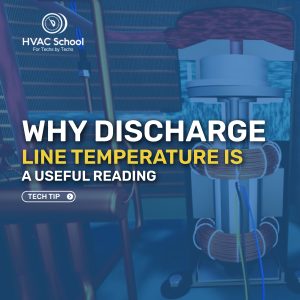
I’d like to give special thanks to Roman Baugh for the section about compressor superheat. It’s not something we talk about very often outside of chiller and commercial refrigeration applications, but it definitely has value in the HVAC world as well. Thanks, Roman! Since I started in the trade, we would take discharge line temperature […]
Read more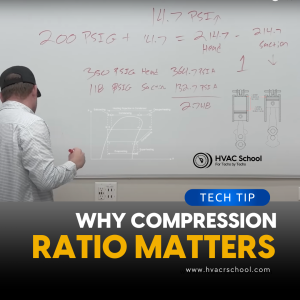
In HVAC/R, we are in the business of moving BTUs of heat, and we move BTUs via pounds of refrigerant. The more pounds we move, the more BTUs we move. In a single-stage HVAC/R compressor, the compression chamber maintains the same volume no matter the compression ratio. The thing that changes is the number of […]
Read more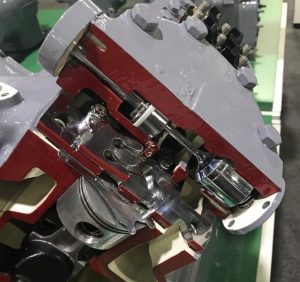
Basic Compressor Functions The compressor's job is to circulate refrigerant through the system by means of vapor compression, similar to the way your heart moves blood through your circulatory system. Refrigerant circulation is measured in lbs/min or lbs/hour; this is called mass flow rate—the mass flow rate changes depending on the density of the refrigerant […]
Read moreVideos:
Podcasts:
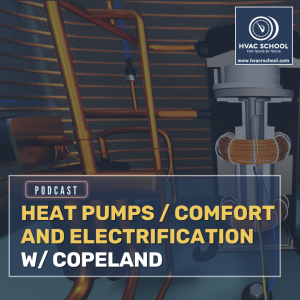
In this informative episode, Josh Souders from Copeland joins Bryan to dive deep into heat pump technology, discussing everything from basic operations to advanced features in cold climate applications. The conversation begins with a fundamental explanation of how heat pumps work, describing them as essentially air conditioners with a reversing valve that allows them […]
Read more