BACK
Two Ways to Prevent Freezing in 90%+ Furnace Condensate Lines
Condensate Drain Codes & Best Practices
Condensate Switch Controversy
Trap and Vent – A Drain Debacle
Traps, Vents & Drains – Short #177
#drain line
Tech Tips:

This tech tip came from an email sent by Adam Blunkall, a Tennessee-based HVAC technician. He shared some tips to help overcome this issue in his market, and we appreciate his insight. Thanks, Adam! If we’re draining our 90% furnaces (or any condensing heating system) outside the structure in a similar fashion as we would […]
Read more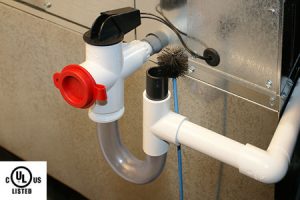
It should be stated and restated that codes and code enforcement vary from location to location within the US. The IMC (International Mechanical Code) is one of the most widely utilized and referenced. The 2015 version of the IMC section 307 is what I will be referring to in this article. Condensate Disposal The code […]
Read more
Condensate overflow prevention devices or float switches, as they are often called, are such simple devices that you wouldn't think there would be much room for controversy. In my experience, there are few areas of the trade where technician and installer preferences and opinions vary greatly. Let's start with some float switch basics. Float (condensate) […]
Read more
This picture is from a recent call I ran that clearly had an interesting past. It had a condensate pump to pump the water just a few feet up to a drain that went to a common drain. The “cleanout” after the trap is supposed to be a vent, not a cleanout, which means it […]
Read moreVideos:
Podcasts:
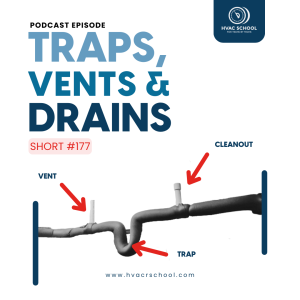
In this short episode, Bryan covers traps, vents, and drains. He explains some common misconceptions and best practices for fabricating drains, especially in residential and light commercial structures in Florida. Cleanouts and vents are commonly confused with each other, and people often cap vents and leave cleanouts open. However, cleanouts (which must be capped) […]
Read more