BACK
Remove “Weep” Plugs on Motors
The 3 Fan Laws and Fan Curve Charts
How to Replace a Condensing Fan Motor
Blowers, Props, and How They Behave (or Misbehave)
Ball Bearing vs. Sleeve Bearing Motors
Aftermarket Motor Selection & Considerations
3-Wire and 4-Wire Condensing Fan Motor Connection
Remove “Weep” Plugs on Motors
Remove “Weep” Plugs on Motors
#fan motor
Tech Tips:
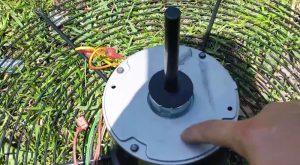
In this 60-second tech tip video by Brad Hicks with HVAC in SC, he shows us how and why to remove the weep port plugs on a condensing fan motor. I know from experience that motors can fail prematurely when this practice isn't followed. Remember that motor orientation dictates which weep port plugs are […]
Read more
This article was written by Tim De Stasio with Southern Comfort Consulting and Service. It was originally published on his blog, which you can access by clicking THIS link, but he permitted us to republish it on HVAC School as well. Thanks, Tim! It is critical for an HVAC technician to understand airflow and how […]
Read more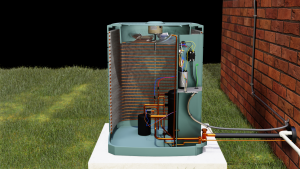
Service calls about condensing fan motor failure are quite common. Even though fan motor replacement is a standard procedure for residential split systems, it requires careful attention to safety and detail. This article will give you a step-by-step guide to replacing condensing fan motors. Along the way, we will also explain a few best practices […]
Read more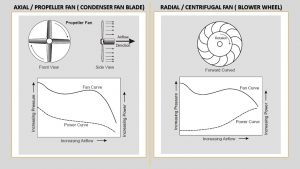
Fan laws and fan curves are a deep subject with a lot of nuance and variation. Just to get our heads around the subject, let's focus on two different types of fans that we see all the time in HVAC: the prop/axial type and the radial/centrifugal type. Centrifugal/Radial As we increase the pressure differential across […]
Read more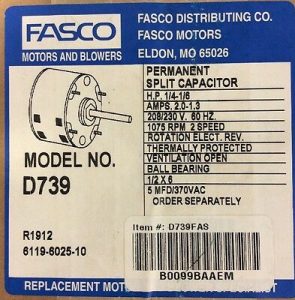
One aspect of motor selection that can get overlooked is motor bearings, and it can have big consequences. Sleeve bearings are most common in residential and light commercial applications because they are less expensive and quieter. They don't have rolling “balls” but rather rely on a thin film of oil on metal sleeves. Sleeve bearings […]
Read more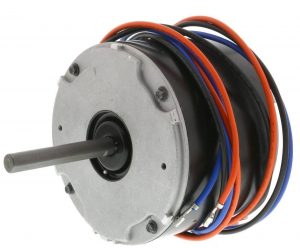
This article was written by technician and HVAC School community star Kenneth Casebier. Thanks, Kenneth! When looking at replacing a single-phase A/C motor with an aftermarket motor from your van, there are a few things you should know and pay attention to. First, the factory OEM motor will always be the best option, especially when […]
Read more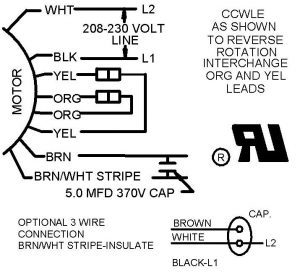
Diagram courtesy of Emerson New techs have a common question of how to wire a condensing fan motor for 3 vs. 4 wires. Jesse Grandbois submitted this tech tip to help make it simple. Thanks, Jesse! This tech tip is a quick one on the difference between wiring universal condenser fan motors and why brown […]
Read more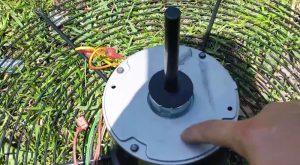
In this 60-second tech tip video by Brad Hicks with HVAC in SC. he shows us how and why to remove the weep port plugs on a condensing fan motor. I know from experience that motors can fail prematurely when this practice isn't followed. Remember that motor orientation dictates which are removed. It (generally) the ports […]
Read moreVideos:
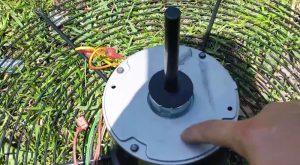
In this 60-second tech tip video by Brad Hicks with HVAC in SC, he shows us how and why to remove the weep port plugs on a condensing fan motor. I know from experience that motors can fail prematurely when this practice isn't followed. Remember that motor orientation dictates which are removed. It (generally) the […]
Read more