BACK
Don’t Forget the Suction Filter Drier
Proper Liquid Line Drier Location
Contaminant Controls – System Clean Up with Filter-Driers
#filter drier
Tech Tips:
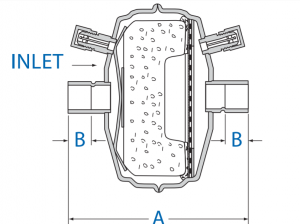
Courtesy of Emerson It is important to have refrigerant free from debris and contaminants, and we control these issues on many different fronts. 1. Proper tubing handling prevents copper shavings, dirt, and water from entering while installing. 2. Flowing nitrogen while brazing prevents carbon build-up. 3. Deep vacuum of 500 microns or less removes air, […]
Read more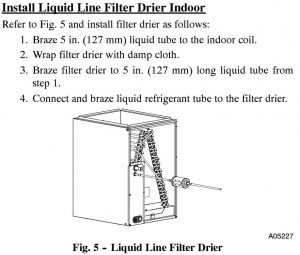
Diagram above by Carrier It's really easy to put a liquid line drier in the proper location, but it's still more commonly installed in the WRONG location. Namely, people install it right at the condensing unit. (OK, it isn't that big of a deal, but I needed some dramatic emphasis.) Installing it at the indoor […]
Read moreVideos:
Events:
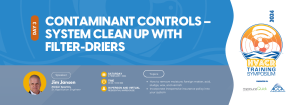
NOTE: If you cannot view the recording, the video may still be processing. The maximum wait time is 24 hours. We apologize for the delay and appreciate your patience.
Read more