BACK
Heat Doesn’t Rise
Second Law of Thermodynamics
Air Flow and Ice – A Thought Experiment
An Electric Heat Mistake
The Good Old Heat Anticipator
How “Hot” Does That Get?
The PATH to High Performance HVAC w/ David Richardson
The Basics of Moving Heat (Thermodynamics)
#heat
Tech Tips:
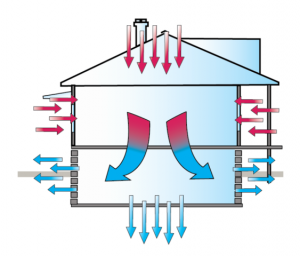
We've all heard some version of the phrase “heat rises,” but is that really true? First, we need to remember that heat is energy, not matter. Heat is a force, not a thing. So, while heat may result in changes to matter (stuff), it isn't matter itself. When we add heat to stuff, the molecules […]
Read more
The second law of thermodynamics puts the first law into context and establishes entropy as a concept. We can simply define entropy as a state of disorder that can only increase or remain the same in natural processes. Processes in which entropy remains the same are reversible, but ones that result in an entropy […]
Read more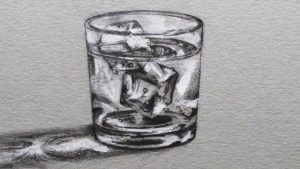
Imagine a glass of ice sitting on a table. Now, imagine you place a lid on the glass so that all the water and ice are contained in the glass. If the ice and water are well mixed, the water and ice will both be at 32°F because the ice is slowly changing state from […]
Read more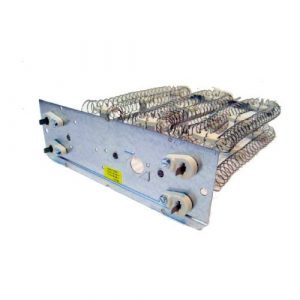
I started working as a tech when I was 17 years old, fresh out of trade school. My first winter out on my own, I went to a service call in an older part of Orlando, a part of town I had never worked in before. It was an especially cold winter that year, and […]
Read more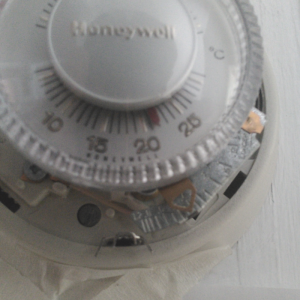
As a technician, you most likely know some customers who still have an oldie thermostat (you know, those old mercury bulb things, like the round Honeywell CT87 and such). Keep in mind that those usually have an adjustable heat anticipator. If you’re newer in the field, you may not have seen or worked with those […]
Read more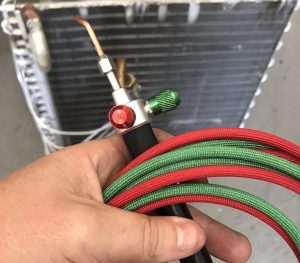
I got in one of these tiny torches the other day to experiment with brazing aluminum in tight spots, and one of the techs walked in and asked, “What type of torch is that?” I answered, “It's oxy/acetylene.” He picked it up and looked at it a bit, then asked, “Does that get hot enough […]
Read morePodcasts:

In this engaging session, David Richardson breaks down the concept of high-performance HVAC, offering a clear roadmap for industry professionals looking to elevate their craft. Richardson argues that the HVAC industry has long been focused on equipment rather than complete systems, leading to widespread inefficiencies. The average system delivers only about 57% of its […]
Read more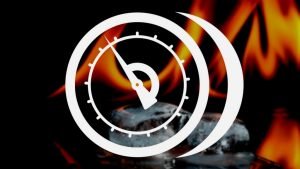
In this episode of HVAC School, Bryan talks to some apprentices about basic thermodynamics. That is the fancy scientific way of saying that we're moving heat. The way we think of “hot” and “cold” is relative to our comfort. However, the scientific concepts of “hot” and “cold” are very different from our relative understandings of those […]
Read more