BACK
Discovering Mental Reference Points
Electric Heat & Blower Interlock
What does “RES” mean on a contactor or relay?
Understanding Relays With the 90-340
How I Failed to Re-diagnose: The Lesson I Learned
What is a DIN Rail?
#relay
Tech Tips:
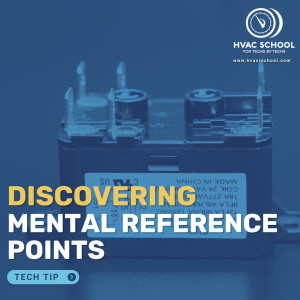
Trying to wrap your head around HVAC can feel like a constant firehose of new info, right? Whether you're in class or on the job, there's just so much to soak up. And when you finally think you've got one thing down, BAM, here comes another concept. For me, remembering everything can be a real […]
Read more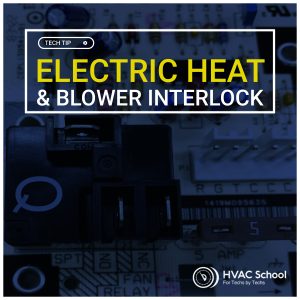
In residential air handler/fan coils, it is common to use a high-voltage interlock between the blower and the electric heat strips to ensure that the blower comes on whenever the heat is on. The problem is that it CANNOT work the other way around where the heat comes on with the blower. Heat strips are […]
Read more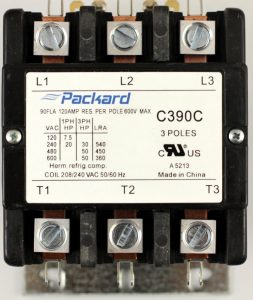
Go to your truck, pick up a contactor, and look at it closely. You may find some interesting ratings you never noticed—things like terminal ambient temperature ratings and torque specs. One reading you may overlook is the RES AMPACITY of the contactor or relay. The RES rating is the RESISTIVE LOAD AMPACITY (amperage capacity) or rating. […]
Read more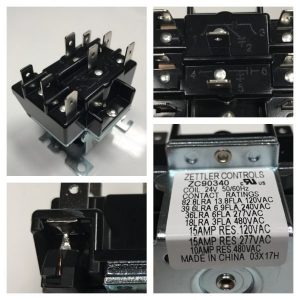
Relays can be used for many different control applications, including controlling fans, blowers, other relays, or contactors, valves, dampers, pumps, and much more. A 90-340 is a very common, versatile relay that many techs have on their truck. So, we will use it as an example. A relay is just a remotely controlled switch that […]
Read more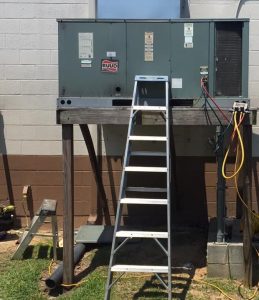
This is the tale of how I found myself stuck on a service call for over 12 hours on a weekend due to my failure to re-diagnose an issue. I was working for a service company that had many accounts with local gas stations. These were large customers, and we did everything we could to […]
Read more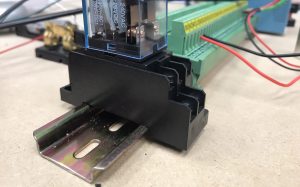
If you do any larger commercial work, you've probably seen a DIN rail without knowing what it is called. It is simply a mounting standard that originated in Germany in the 80s and slowly worked its way over here. DIN rails can be used to mount terminal blocks, relays, starters, breakers, and just about anything […]
Read more