BACK
5 Capacitor Facts You Should Know
Start Capacitor and Inrush Facts & Myths – Part #2
#run capacitor
Tech Tips:
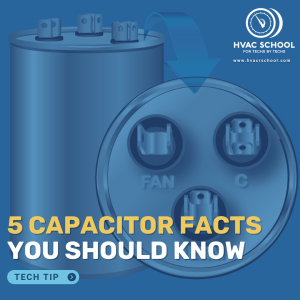
One of the most common parts to fail on a single-phase HVAC system is the run capacitor, so much so that we sometimes refer to junior techs as “capacitor changers.” While capacitors may be easy to diagnose and replace, here are some things many techs may not know: Capacitors Don't “Boost” the Voltage A capacitor […]
Read more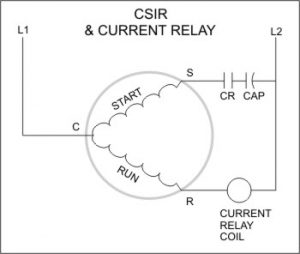
Thought Experiment #3 – The Start Winding Has No “Inrush” with a run capacitor only The name “start winding” is an antiquated term for the single-phase residential industry. It came from the days when CSIR (capacitor start, induction run) motors were still used commonly. In a CSIR motor, the start relay removes the start winding […]
Read more