BACK
Watch Out for Fire Sprinklers
Brazing in TXVs: Best Practices
What is Flux?
Start Flowing Nitrogen Sooner
HVAC/R Brazing Indicators
Refrigerant Leak Detection and Prevention: Epic Article
5 Install Mistakes that Kill Systems
Thermal Expansion & Dissimilar Metals
Is Flowing Nitrogen While Brazing Really Important? – Live Video 2/4/2017
Fire Sprinklers – Short #239
Flow Nitrogen Great Again
#Brazing
Tech Tips:
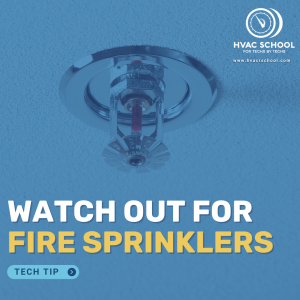
Our company recently had an incident where someone was operating a scissor lift and hit a fire sprinkler with it. The sprinkler activated, and the area flooded. This issue, unfortunately, isn’t that uncommon in the electrical, construction, and HVAC trades, but it’s preventable with proper training and attention to detail. Those of you who work […]
Read more
This is a quick tip from the “Expansion Valves – What Does and Doesn't Matter?” livestream on our YouTube channel featuring Joe Shearer, Matthew Taylor, and Corey Cruz. It’s time to talk about brazing again! Even though rehashing “flow nitrogen” and “use a wet rag” gets a little old, bad TXVs and callbacks also get […]
Read more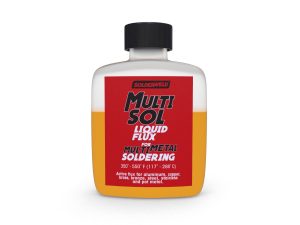
In HVAC, you will hear the word “flux” used in two totally different parts of the trade. You may have heard of magnetic flux before. Magnetic flux is the lines of force that emanate from a magnet. You often hear about magnetic flux lines in discussions of motor theory. Transformers also use electromagnetic flux to […]
Read more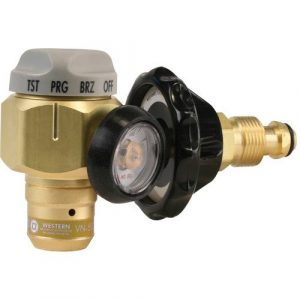
My technician (and brother-in-law), Bert, made a good point. (It's hard for me to admit it, but it's true.) When he needs to open the refrigerant circuit to make a repair, regardless of whether he is recovering or pumping down, he pulls out his nitrogen tank and his regulator. (We like the Western Enterprises VN-500 […]
Read more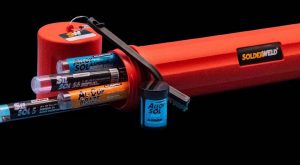
When brazing and soldering, we have a few things we need to accomplish to make a proper connection: We can't overheat the joint until it overheats the base metal or the flux where applicable. We must bring the entire joint above the melting temperature of the brazing alloy. Draw the alloy deep into the joint. […]
Read more
Let’s face it, refrigerant leak detection and prevention will always be important in our trade. Whether we’re dealing with leaks from corrosion or poor connections, we will always run into them in some form. We’ve touched on refrigerant leak prevention and detection quite a lot at HVAC School. Many of our articles, podcasts, and videos […]
Read more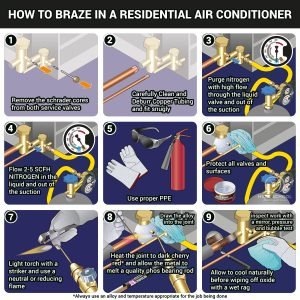
When we install systems, we should have three main goals in mind: maximizing longevity, efficiency, and capacity. We want our units to work as long as possible, use the lowest amount of energy, and move the greatest amount of BTUs possible with a proper mix of sensible and latent heat transfer. Unfortunately, some installation practices […]
Read more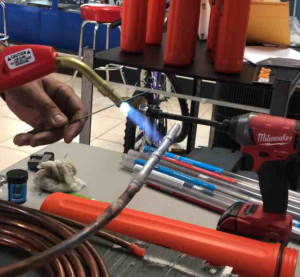
Dissimilar metals, like aluminum, copper, brass, and steel, are some of the main metals one may experience in their trade, and few people are comfortable working with dissimilar metals. They don’t trust their brazed joint, or they are afraid of melting away material. To put some of the nerves of those in the field at […]
Read more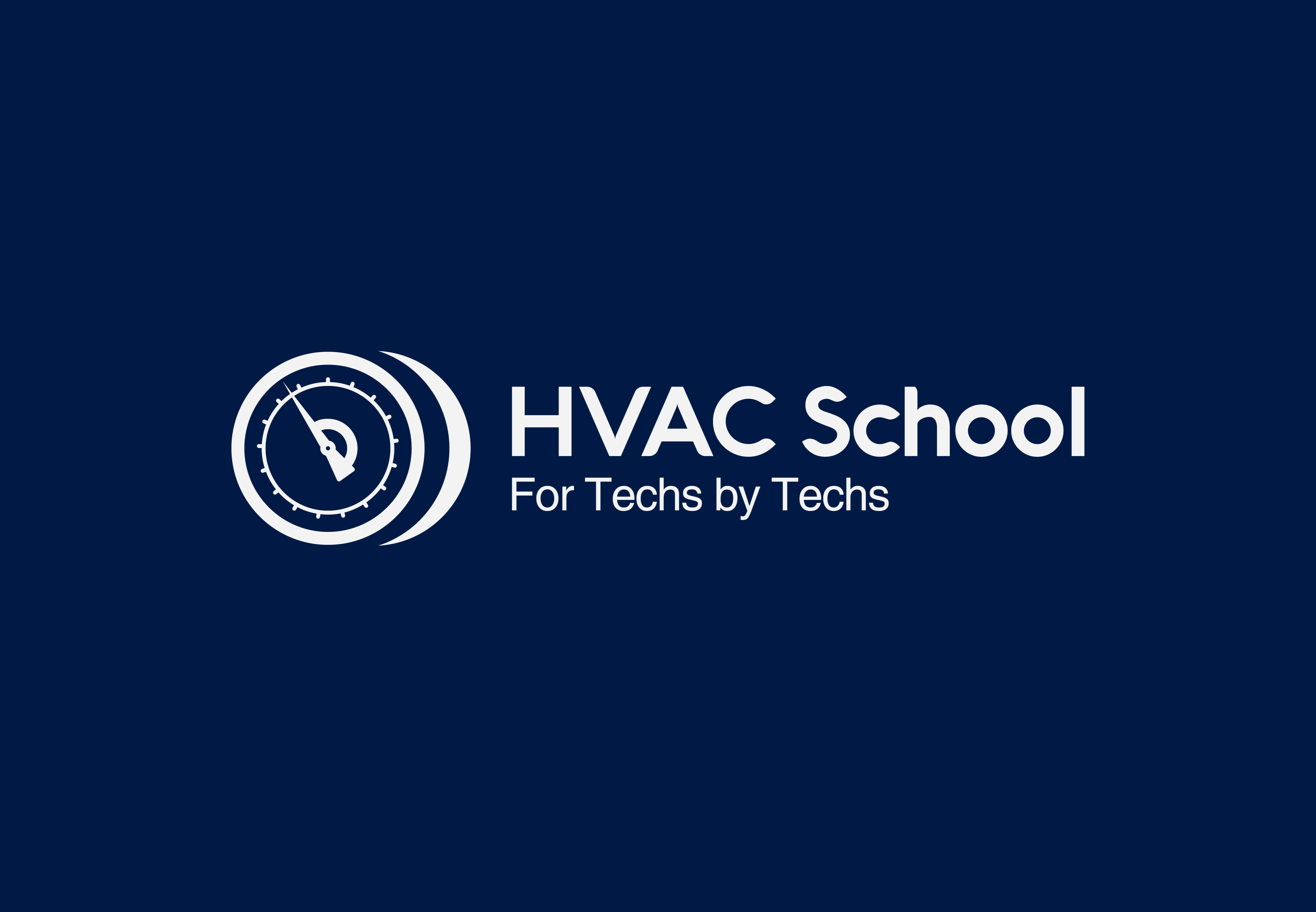
In this live video Bryan talks about Flowing Nitrogen Reasons techs give not to flow nitrogen Reasons that some cases create more carbon than others Demonstration video by Tim Bagnall
Read moreVideos:
Podcasts:
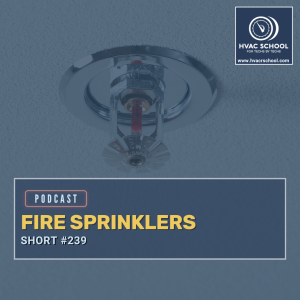
In this short podcast episode, Bryan talks about fire sprinklers and how to avoid setting them off on job sites. Fire sprinklers have an element in the center that expands when exposed to heat (like a TXV sensing bulb) and breaks the glass. When the glass breaks, the fire sprinkler starts pouring out water. […]
Read more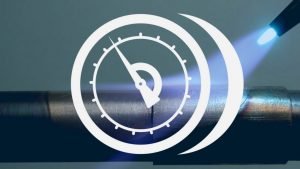
In this episode of the HVAC School Podcast, Bryan talks with Tim Bagnall about flowing nitrogen. Many techs don't flow nitrogen. Some may say that it is overkill, but it has been shown that flowing nitrogen displaces oxygen while brazing and prevents harmful scale from forming on the copper. Scale is very problematic, and it will likely […]
Read more