BACK
How To Do a Heat Maintenance That Actually Matters
Gas Furnace Maintenance Procedure
The Basic Residential Maintenance for a Heat Pump / Electric System
Pull The Condenser Top
The Case For Pulling The Blower Housing
Something You May Want to Consider on Every Call
Don’t Overfill Refrigerant Recovery Cylinders The Easy Way
Something You May Want to Consider on Every Call
#maintenance
Tech Tips:
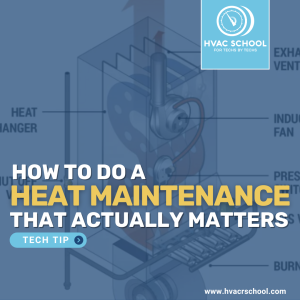
I know I’m not the only one who has sometimes felt a little bad doing heat maintenance. I remember many a day when my lead technician and I (as an apprentice) would crawl into an attic, clean the flame sensor, and then play FarmVille on our phones for 15 minutes before crawling down, giving the […]
Read more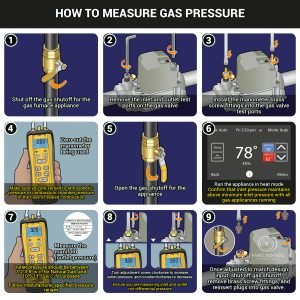
This gas furnace maintenance procedure in this article was developed by Michael Housh. Michael is the owner of Housh Home Energy in Ohio. He regularly works on natural gas equipment and is an active contributor to the HVAC School Facebook group. Thanks, Michael! Gas-fired equipment has a different set of components than your typical straight-cool […]
Read more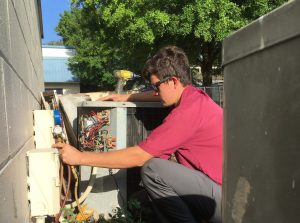
I need to warn you… The following list is the actual process we use at the company I own for our typical “standard” residential maintenance. I'm sure you will find some things you do differently. Take it for what it is, and I'm happy to get any feedback you may have. Read the call notes, […]
Read more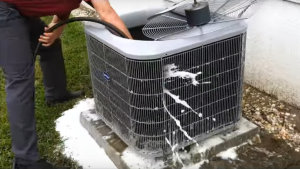
The photo above is from a video one of my techs took of proper condenser cleaning. I must say, he did a GREAT job of cleaning the coil, and he was very careful with the top. However, I STILL would have liked to see him pull the condenser top completely during a full maintenance procedure. […]
Read more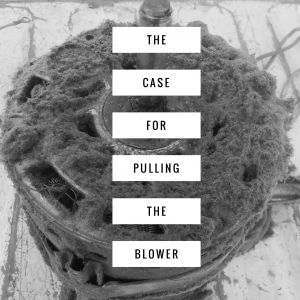
When I started in the trade in 1999, there were still many oilable blower motors in service. As part of the maintenance, we would remove the housing and oil the motor. We would also vacuum the motor and wipe it down. As oilable motors have become extinct, I see fewer and fewer techs pulling the […]
Read more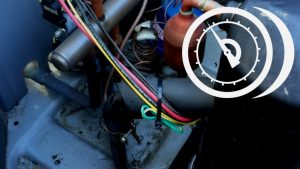
There are a few important things that I suggest checking on every service call to reduce callbacks and increase customer satisfaction. One of them that often gets missed is preventing wire rub-outs. One of my area managers and experienced tech Jesse Claerbout shot a video showing the simple step he takes to prevent major damage. […]
Read moreVideos:
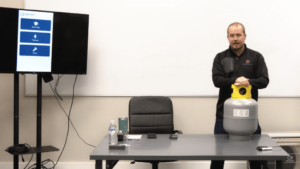
In this video we review the HVAC School app tank fill calculator and how to use it to prevent the overfilling of refrigerant recovery cylinders.
Read more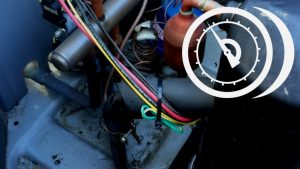
There are a few important things that I suggest checking on every service call to reduce callbacks and increase customer satisfaction. One of them that often gets missed is preventing wire rub outs. One of my area managers and experienced tech Jesse Claerbout shot a video showing the simple step he takes to prevent major […]
Read more