BACK
Inches of Water Column
Drain Trap Depth and Negative Pressure
Angry Air
Zonal Pressure Diagnostics—The Backtalk Series (Pt. 1)
Oxyacetylene Torches: Tips and Operation
Pressure / Enthalpy Diagram Example
Does Nitrogen Pressure Change with Temperature – Practical Application of Gas Laws
The PATH to High Performance HVAC w/ David Richardson
Using the Roomulator w/ Chris Hughes
Absolute vs. Gauge Pressure (Micron Gauge vs. Manometer) – Short #184
#pressure
Tech Tips:

Low pressures are often measured in inches of water column or “WC. Like most units of measure, it has a very simple origin; in a water manometer, 1″ of water column is literally the amount of force it takes to raise the column of water by 1”. While some water manometers (water tubes) are still […]
Read more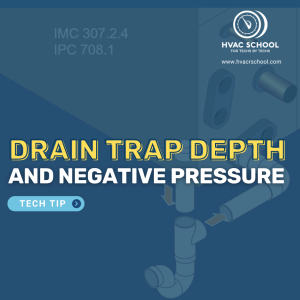
We recently received a Speakpipe question for the podcast about a common nuisance call on straight-cool A/C units and heat pumps. The systems, often retrofit units, were backing water up into the secondary drain pan and overflowing it. This issue isn’t happening on furnaces, which are positively pressurized, which means we have to take a […]
Read more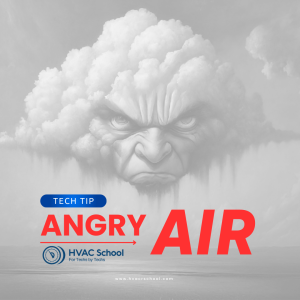
About a month ago, one of my techs went on a “no heat” call. The house is a rectory for the church next door. The call came in, and after he ran it, I assumed the problem was solved since I hadn’t heard otherwise. A few weeks later, they called back, saying the boiler was out […]
Read more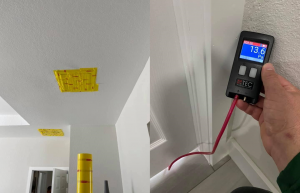
This article was submitted by Genry Garcia of Comfort Dynamics, Inc. It is the first part of his series on zonal pressure diagnostics. Thanks, Genry! Zonal pressure diagnostics have been around for a while. Here is a brief description of ZPD from the website redcalc.com: Formerly known as the “Blasnik methods” in a nod to […]
Read more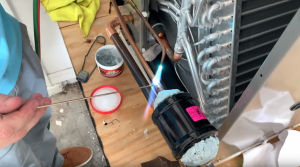
Everyone in the HVAC/R trade uses some type of torch to braze or solder alloys together. So, what is the proper way to handle an oxyacetylene torch? It turns out that there’s more than one right answer. Depending on which torch rig you use, the manufacturer’s manuals for operation may vary. Everyone (hopefully) knows […]
Read more
This article was written by my buddy and Canadian Supertech Tim Tanguay. Thanks, Tim! This P/E chart shows R410a at 100°F saturated condensing temp, 10°F SC, 40°F saturated suction temp, 20°F SH at the compressor. The green highlighted thumb shape is the saturation zone. Everything that occurs in the saturation zone is a latent (change […]
Read more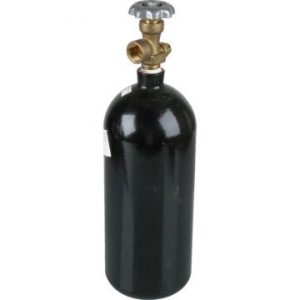
The gas laws. We all learned about them in school and promptly forgot all about them. I really think that we need to dig our books out, dust that information off, and work to understand and apply it. Many will say that nitrogen pressure doesn't change with pressure like other gasses. That is false, but […]
Read morePodcasts:

In this engaging session, David Richardson breaks down the concept of high-performance HVAC, offering a clear roadmap for industry professionals looking to elevate their craft. Richardson argues that the HVAC industry has long been focused on equipment rather than complete systems, leading to widespread inefficiencies. The average system delivers only about 57% of its […]
Read more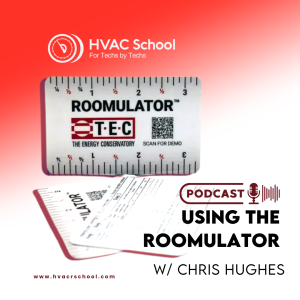
In this episode of the HVAC School Podcast, host Bryan Orr speaks with Chris Hughes of The Energy Conservatory (TEC) about using the Roomulator card and DG-8 manometer for room pressurization testing. Chris provides background on how he came up with the idea for the Roomulator. He wanted an easy way for technicians to […]
Read more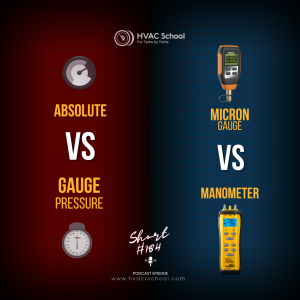
In this short podcast episode, Bryan covers the differences between absolute and gauge pressure, as well as measuring pressure with a micron gauge or a manometer. Compression ratio deals with absolute suction and absolute discharge pressures. Absolute pressure requires us to add atmospheric pressure to the gauge pressure. We usually measure gauge pressure in […]
Read more