BACK
Ramping Your Team Up for CO2
Common Causes of Compressor Failure
Nomenclature and How to Use It
Removing a Blower Motor
Dielectric Grease: What It Is and How To Use It
Sensors, Measurements, and Physics
Coil SHR, Ventilation, and Bypass Factor – Advanced Psychrometrics Part 2
Room Sensible Heat & CFM – Advanced Psychrometrics Part 1
How to Use a Manufacturer Fan Table and Why They are Important
Pumping vs. Compression – Short #218
Building Tech Confidence w/ Refrigeration Mentor
Residential & Rack Startup and Commissioning (Part 2)
Improving Changeout Outcomes
Spidey Sense – Airflow – Short #205
Preventing Low Voltage Issues
STOP Overthinking! – QA Short #204
Stewarding Younger Techs
Duct Smoke Detector Facts and Wiring – Short #203
#HVACR
Tech Tips:
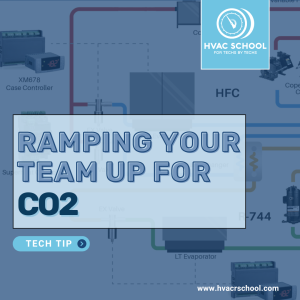
This tech tip is based on a podcast with Andre Patenaude from Copeland. You can listen to that podcast episode HERE, and we encourage you to check out some of the resources at the end of this tech tip—whether you’re all in on ramping your team up for CO2 or just CO2-curious. Carbon dioxide (CO2) […]
Read more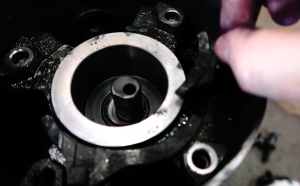
This article was written by Don Gillis, the technical training manager at Chemours. Thanks, Don! Refrigerant compressors are essential components of air conditioning and refrigeration systems, as we all know. They work by compressing refrigerant vapor, which then flows through the system and changes state as pressure and temperature conditions rise and fall. Unfortunately, these […]
Read more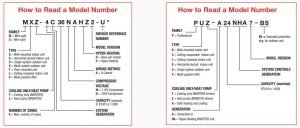
Nomenclature on HVAC/R equipment is a sequence of numbers and letters a manufacturer uses to speak directly to the technician. Lots of initial upfront information is handed to the technician by the manufacturer the moment the technician reads the nomenclature in the model and serial numbers. So, how do we make sense of these seemingly […]
Read more
I’ve seen a lot of guys recently who reach for the motor puller tool first thing when attempting to remove a blower motor from a wheel/fan blade. Motor puller tools are an awesome backup tool when needed, but using a motor puller tool shouldn’t be the go-to method of removing a motor. The main issue […]
Read more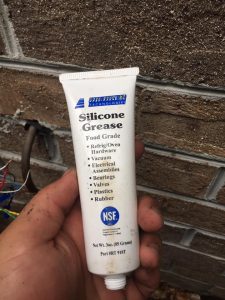
Dielectric grease is an often misused and misunderstood product that could easily benefit HVAC/R technicians in various ways. From food service to electrical connections, dielectric grease can help lubricate mechanical components and prevent corrosion on electrical connections. But we need to understand what it is in the first place before we can properly apply it […]
Read more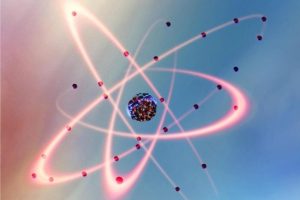
As HVAC/R Technicians, we use tools and instruments to take measurements every day. In fact, 90% of our job could not be done efficiently without some kind of measurement. “How do we measure?” “With what instruments?” “How accurate are these measurements?” These are all questions a thoughtful technician should ask before spending money on a […]
Read more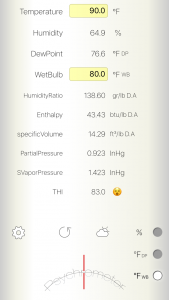
This is the second article in a three-part series where we explore advanced psychrometrics. The source material for each of the articles in this series is ACCA Manual P Sections 3, 4, and 5. This article is based on information found in Section 4. If you followed the previous advanced psychrometrics article, you now know […]
Read more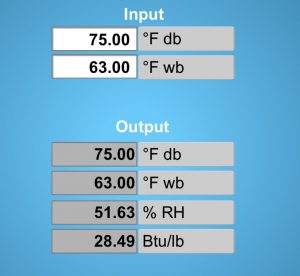
This is the first of a three-part series of articles that will dive deep into advanced psychrometrics. The source material for each of these articles may be found in ACCA Manual P Sections 3, 4, and 5. This article is based on information found in Section 3. Psychrometrics is the study of the physical and […]
Read more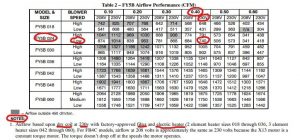
Many installers and service technicians know how to read and use a manufacturer fan table, but this is a quick review with a few extra tips for newer techs. It’s also a good reminder to senior technicians about how this easy-to-use practice can also be easily abused. At installation, properly setting up airflow is imperative to the […]
Read moreVideos:
Podcasts:
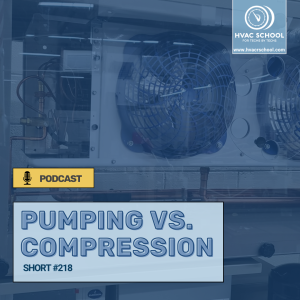
In this short episode, Bryan clears up the confusion behind pumping vs. compression. Pumping is usually associated with liquid. Liquid, like vapor, is a fluid, but it's a lot denser and is essentially incompressible because the molecules are close together. Liquid volume varies based on temperature and density, but we can't squish the molecules […]
Read more
Trevor Matthews returns to the HVAC School Podcast to discuss building tech confidence and personal growth in the HVAC and refrigeration industry. The conversation explores the transformative power of self-investment, continuous learning, and maintaining a positive mindset. Trevor shares his personal journey from a hesitant technician to a successful business owner, highlighting the importance […]
Read more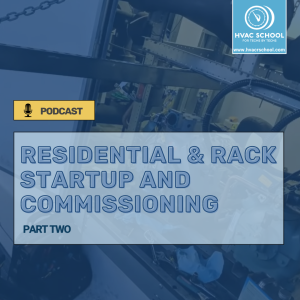
In this episode, Bryan and Max discuss commercial supermarket startup and commissioning with comparisons to residential HVAC work. Max, who has transitioned from residential air conditioning to supermarket refrigeration, shares his insights on the unique challenges and requirements of this specialized field. The conversation begins by emphasizing the critical importance of safety in supermarket […]
Read more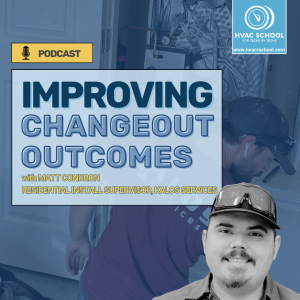
In this episode, we dive deep into the world of residential HVAC installations with Matt, a senior technician and residential install supervisor at Kalos Services. Matt brings a wealth of experience from both the service and installation sides of the business, offering valuable insights into improving installation processes and workmanship. The conversation highlights the importance […]
Read more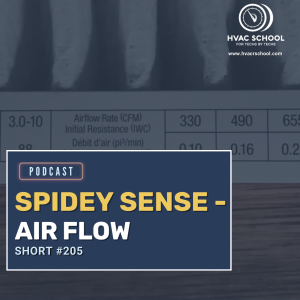
In this short podcast, Bryan talks about how to pay close attention to airflow issues and use your “spidey sense” when you're doing a visual inspection or commissioning a system. He also covers some causes of common airflow problems and some services and upgrades you can offer to your customers. The skill of being […]
Read more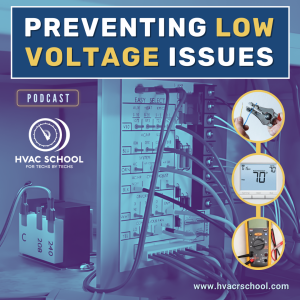
In this episode, Bryan and Bert dive deep into the world of low voltage wiring in HVAC systems. They discuss common mistakes, best practices, and troubleshooting techniques that technicians and contractors should be aware of when dealing with control wiring. The conversation begins with a focus on mechanical issues, such as running wires in places […]
Read more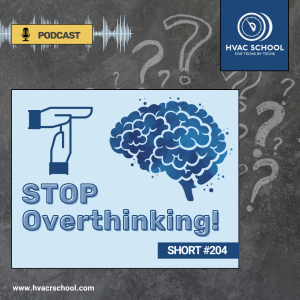
In this short podcast from our Q&A series, Bryan answers a viewer question and implores you to STOP overthinking in the trade! He also shares a parable and some tips to help stop overthinking, especially if you're just starting out in the trade. In many cases, the simplest assumption is the right one (this is […]
Read more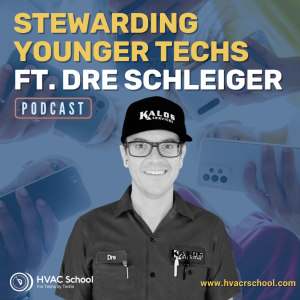
In this insightful podcast episode, Bryan and Dre discuss the challenges and opportunities of managing young technicians in the HVAC industry. They explore the growing interest among young people in trades like HVAC, noting a shift away from traditional four-year college paths. The conversation highlights the satisfaction that comes from working with one's hands and […]
Read more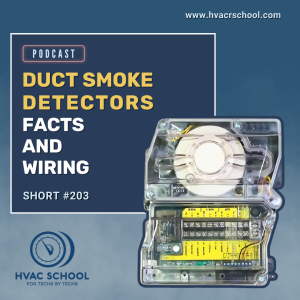
In this short podcast, Bryan answers a listener-submitted question about duct smoke detector facts and wiring. He focuses on Honeywell duct smoke detectors (namely the D4120W), but there are some general best practices that can be applied to most duct smoke detectors. The power supply may be 24v or 120v AC or DC and may […]
Read more