June 2017
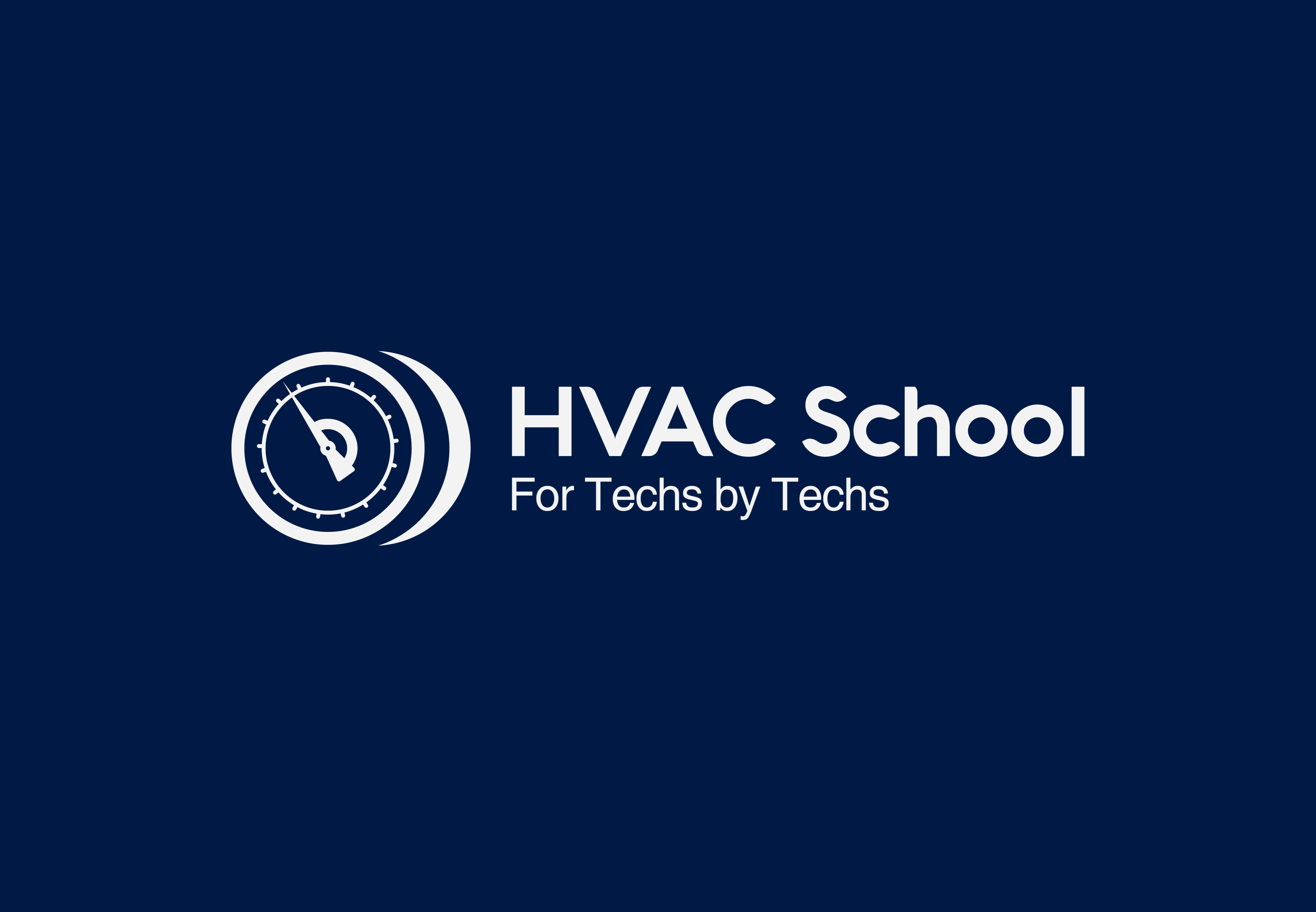
If you have ever been curious about working on restaurant equipment and cooking equipment we have a fun conversation with some of the basics. P.S. – Don't pull the fire alarm
Read more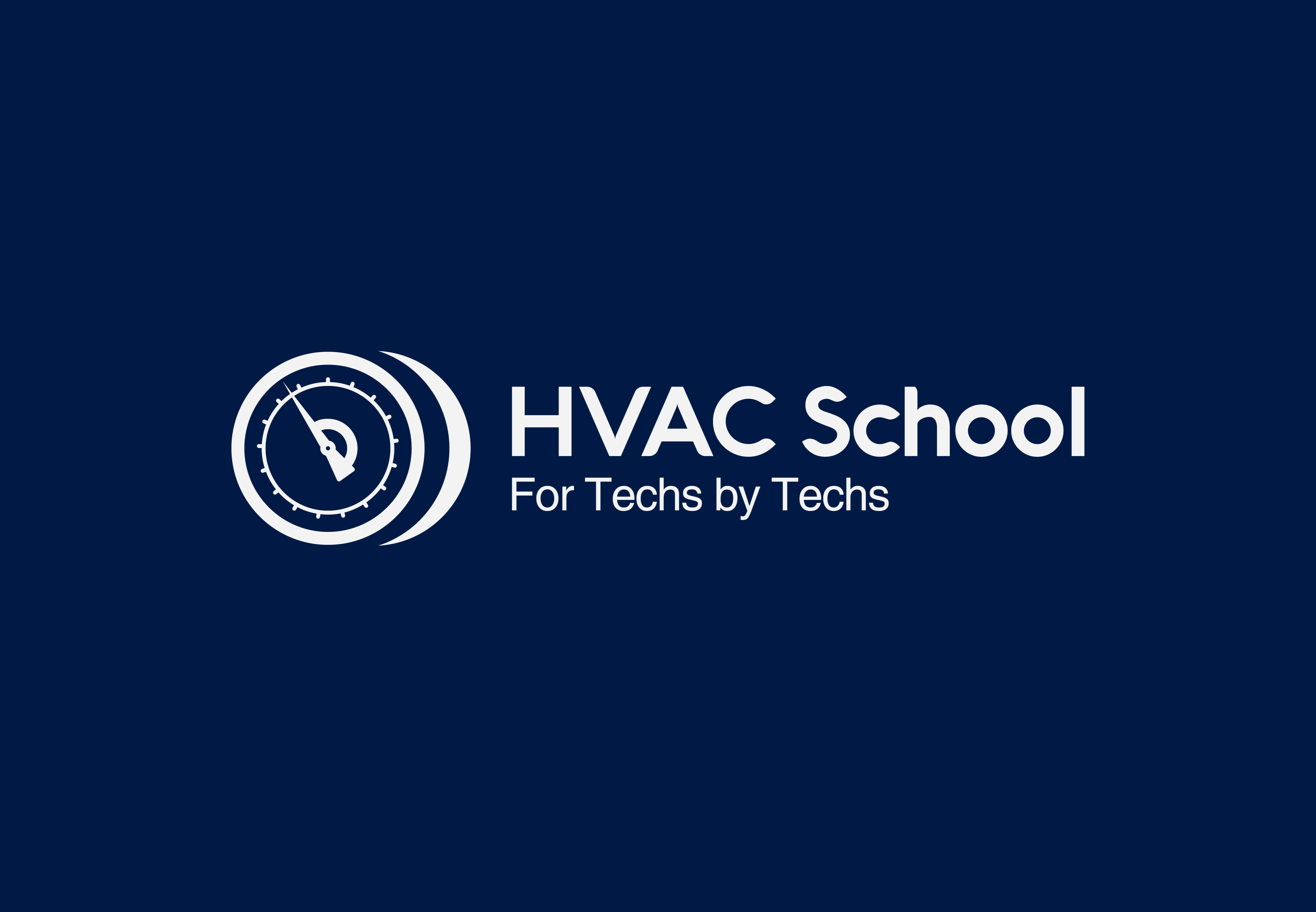
Bryan talks with Phil Zito from BAS monthly about Building Automation and EMS. What it is, how it works and why it might be something to learn more about.
Read more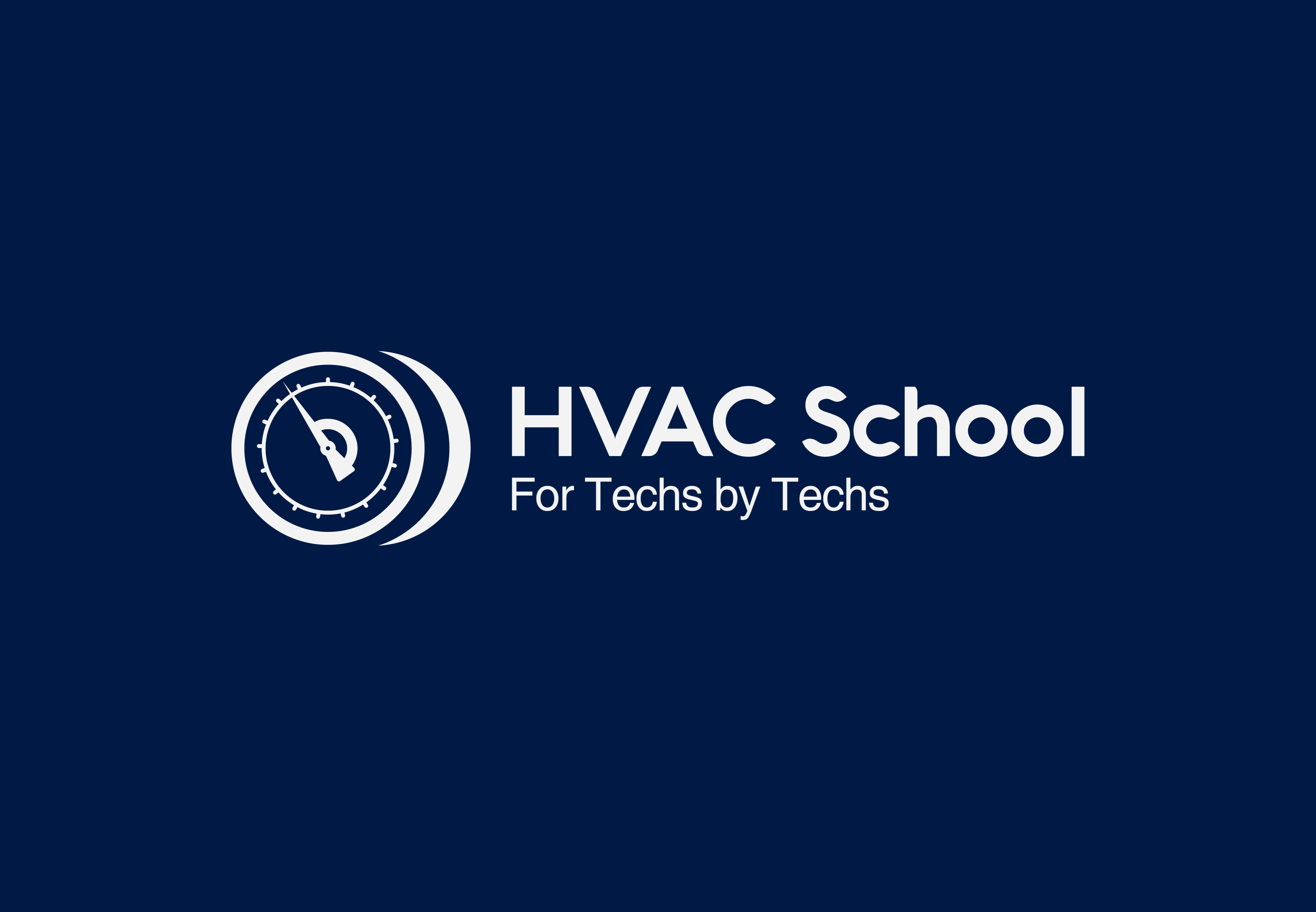
In this episode of the HVAC school podcast Jamie Kitchen from Danfoss talks about common causes of TXV failure, how they function and how to set them. He also explains that a TXV isn't TRULY a constant superheat valve.
Read more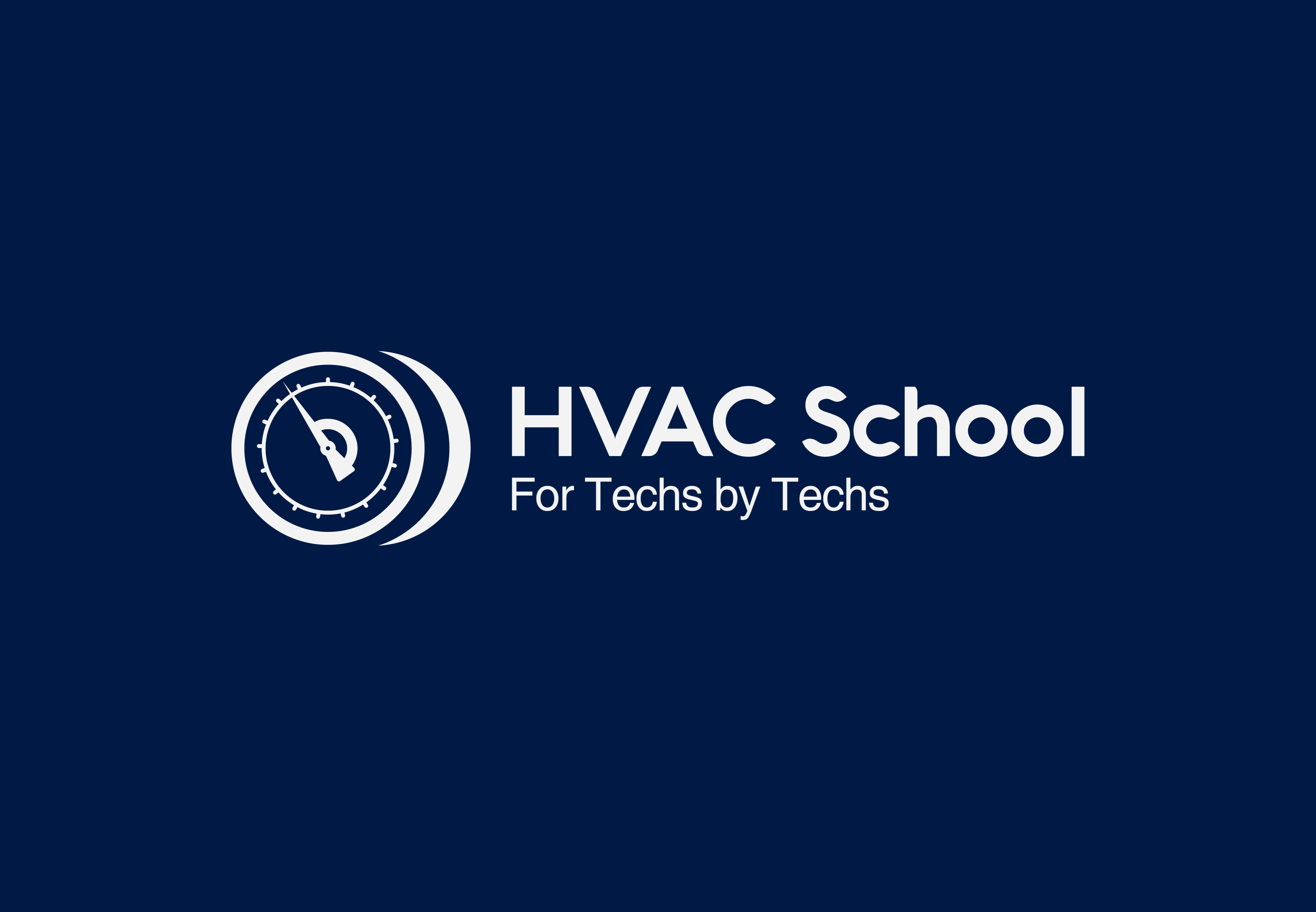
In Part 2 – Jim Bergmann wraps up the steps to check a system charge without connecting a gauge manifold
Read more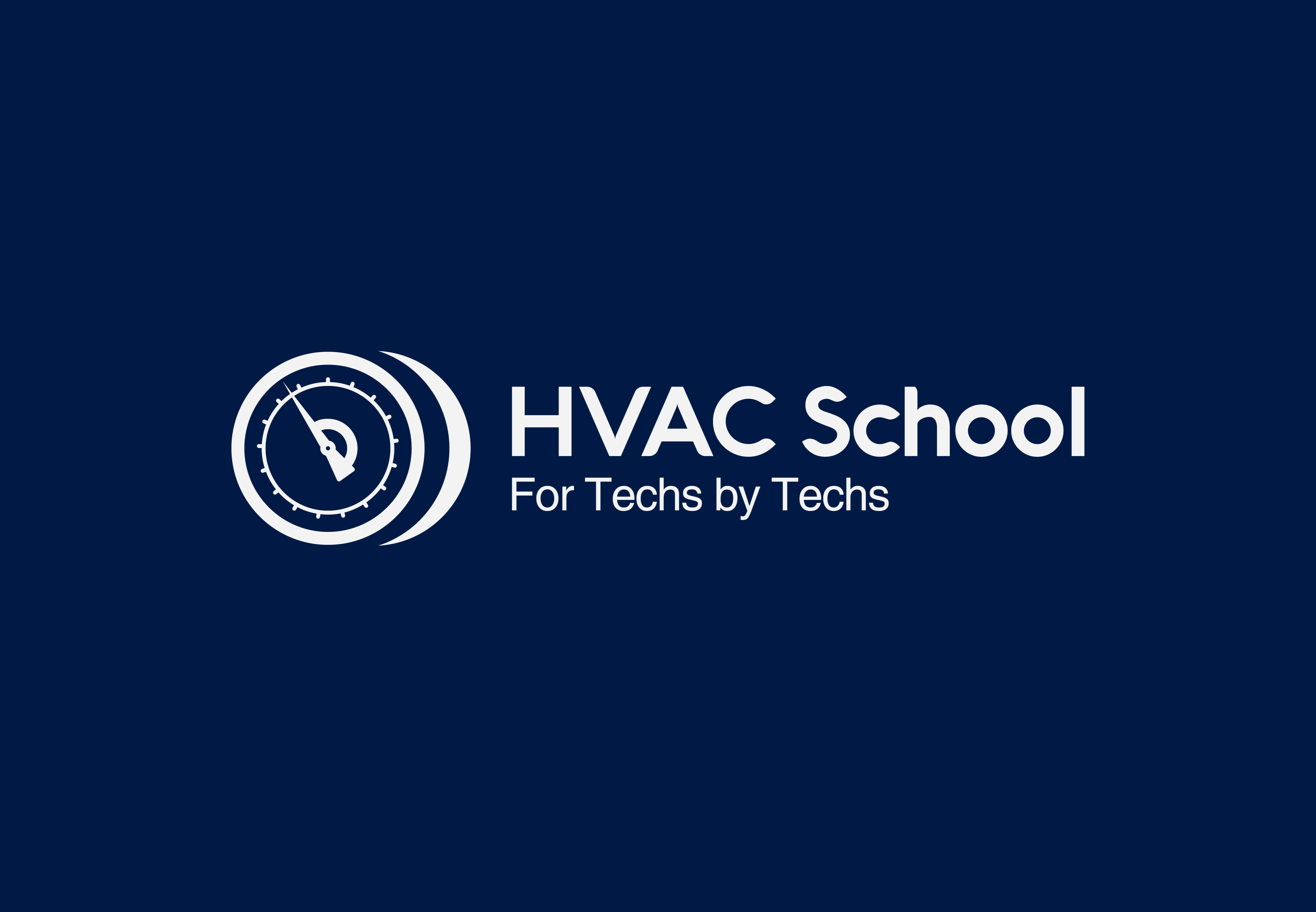
In this episode Jim Bergmann lays the groundwork for checking a system charge without ever connecting a manifold.
Read more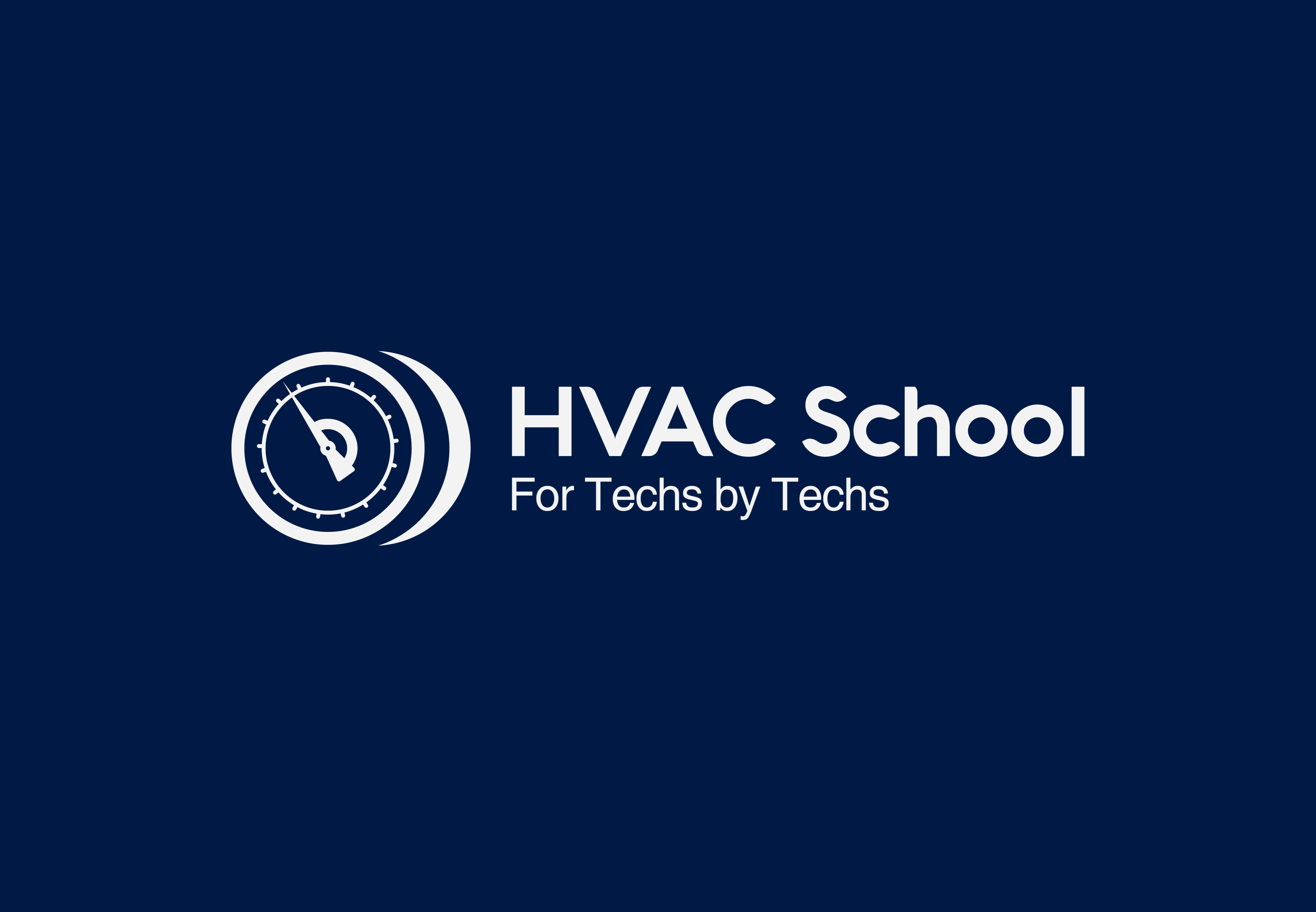
Popular speaker, trainer and writer Jack Rise comes on and talks about ACCA manual D, duct design, common mistakes and much more.. You can find the book at http://www.acca.org/store
Read more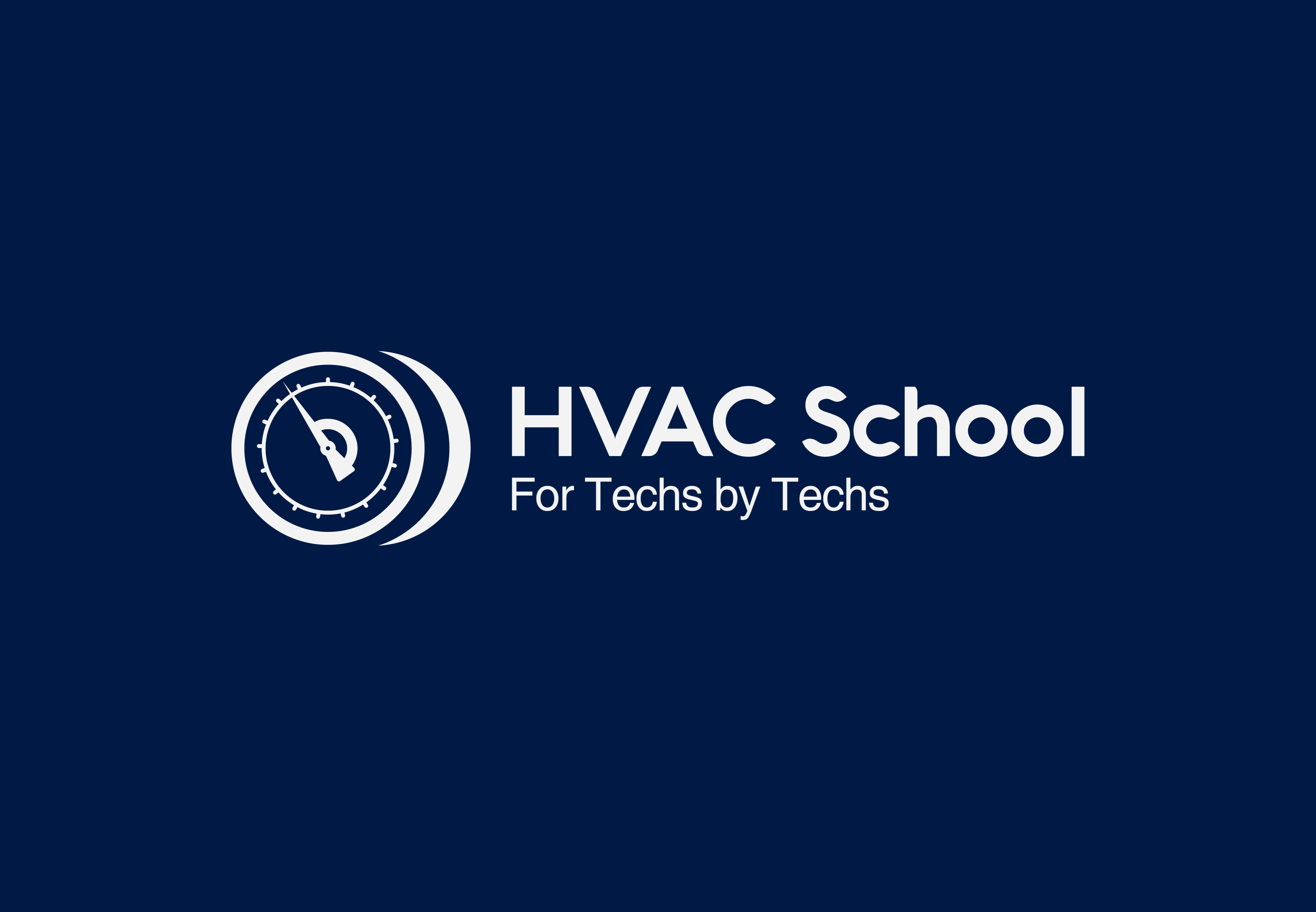
In this episode of HVAC School Bryan talks with Eric Shidell about the most causes of system freeze up and some of the things you can do about it
Read more