August 2017
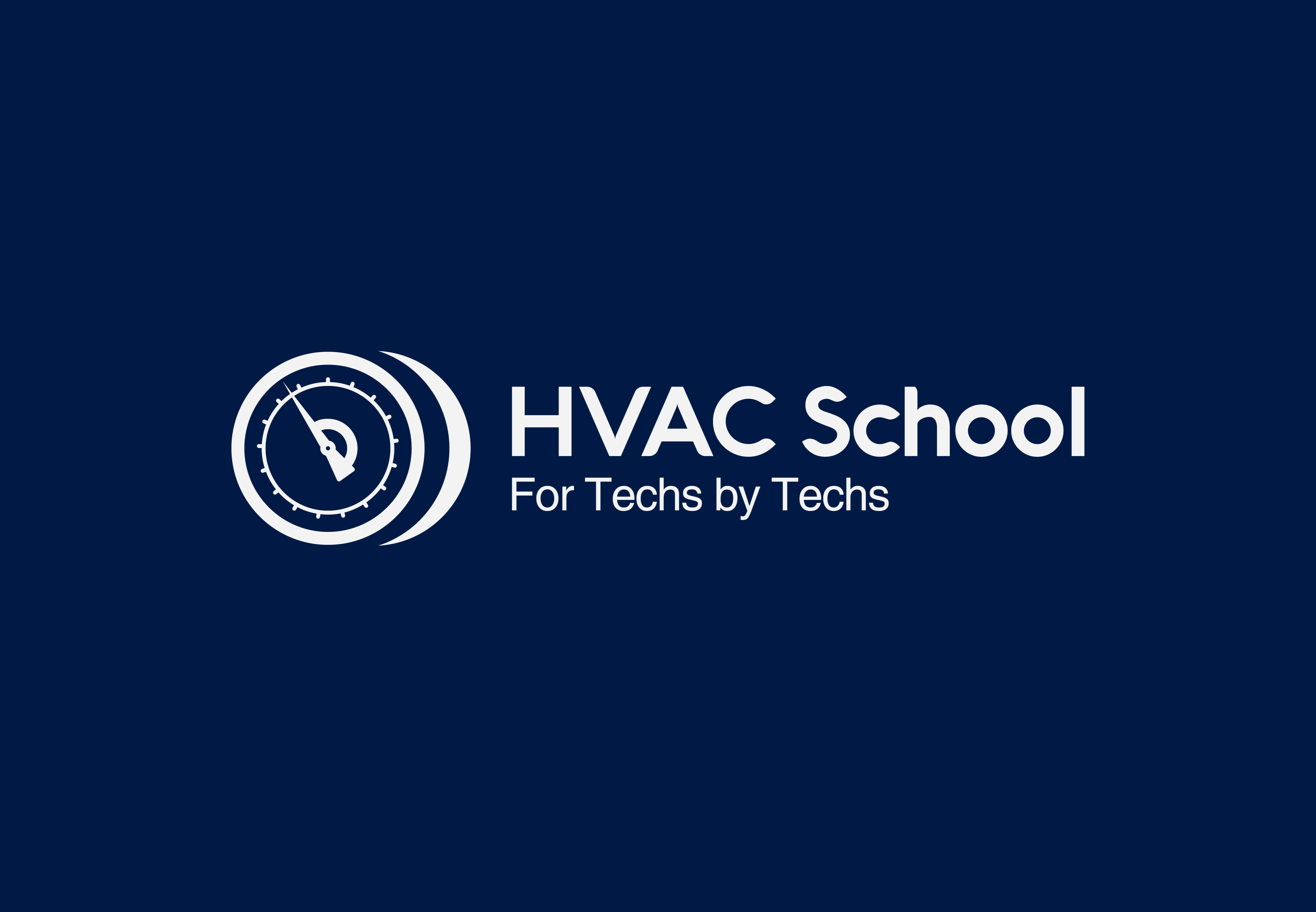
Dick Wirz, author of “Commercial Refrigeration for Air Conditioning Technicians” talks about making the switch to refrigeration, Evaporator split, defrost and more…
Read more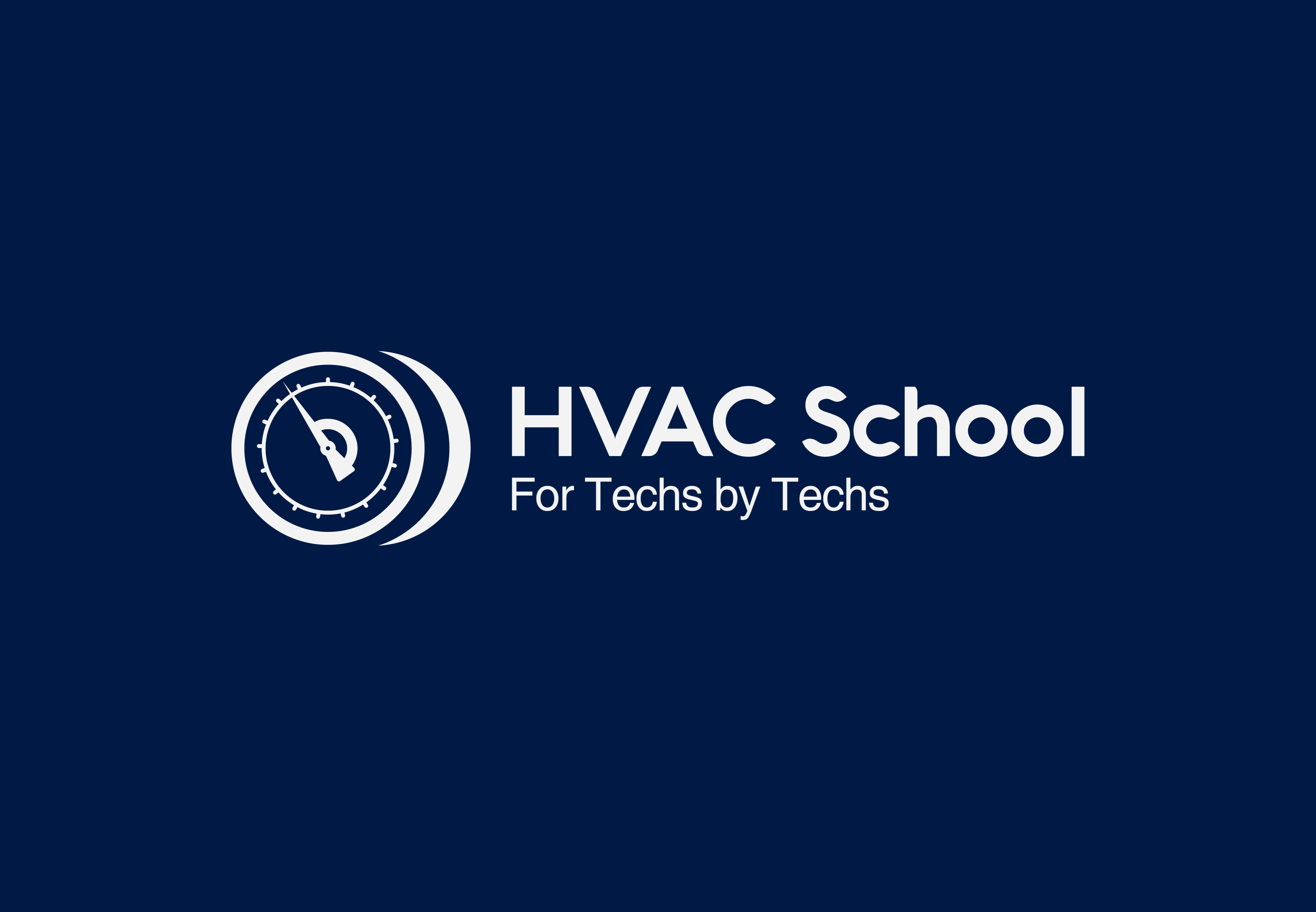
In This episode I talk with Camron Conlee about the world of ammonia refrigeration. How the circuit is set up, what it's like to work with a poisonous refrigerant and much more. Find out more about TDI at http://www.tdirefrigeration.com/
Read more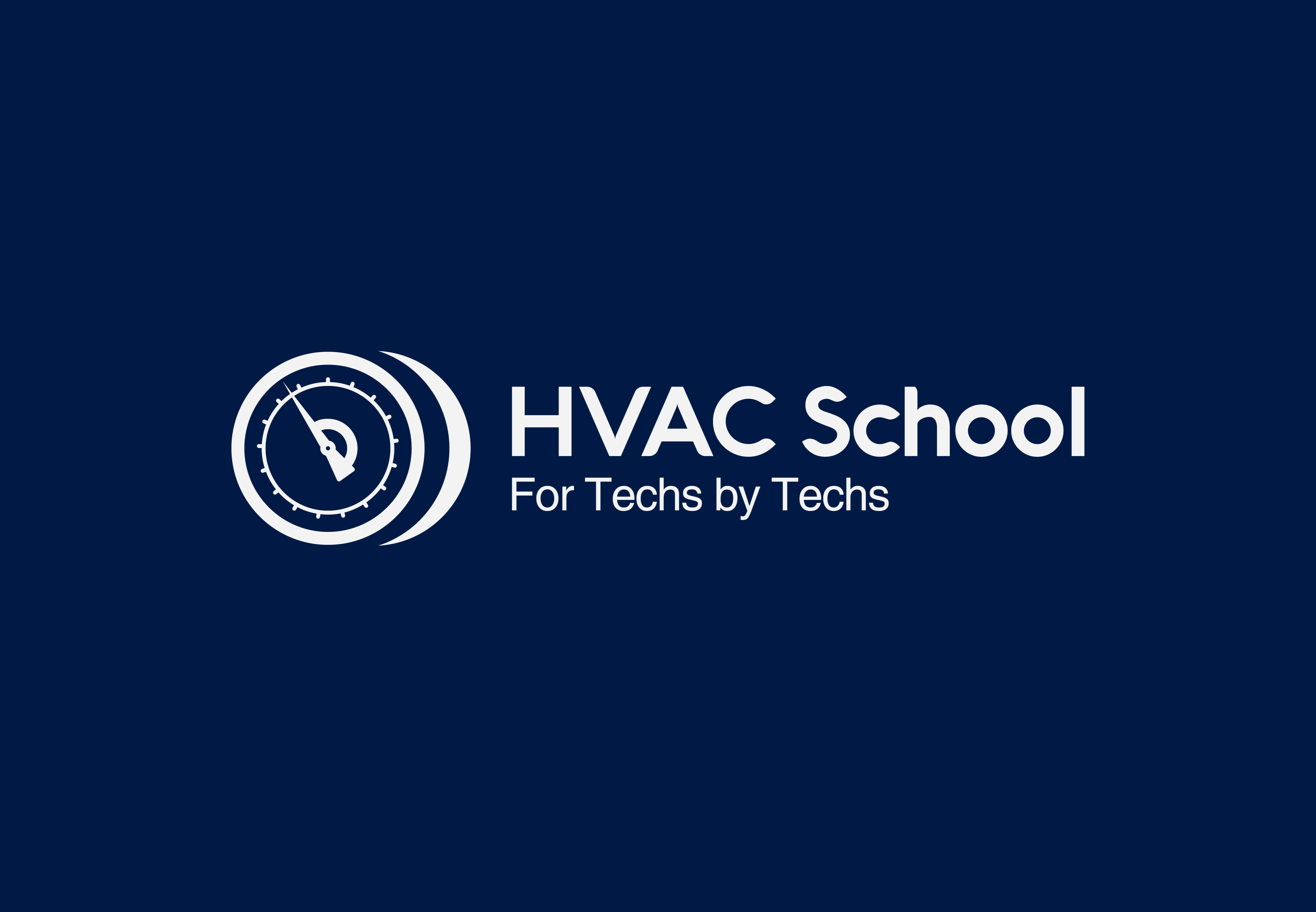
In this episode we talk scales. Weighing refrigerant in, weighing refrigerant out and the new UEI WRS110, WRS220 and WRSX that may be the best and most Vulcan in appearance of all the scales available.
Read more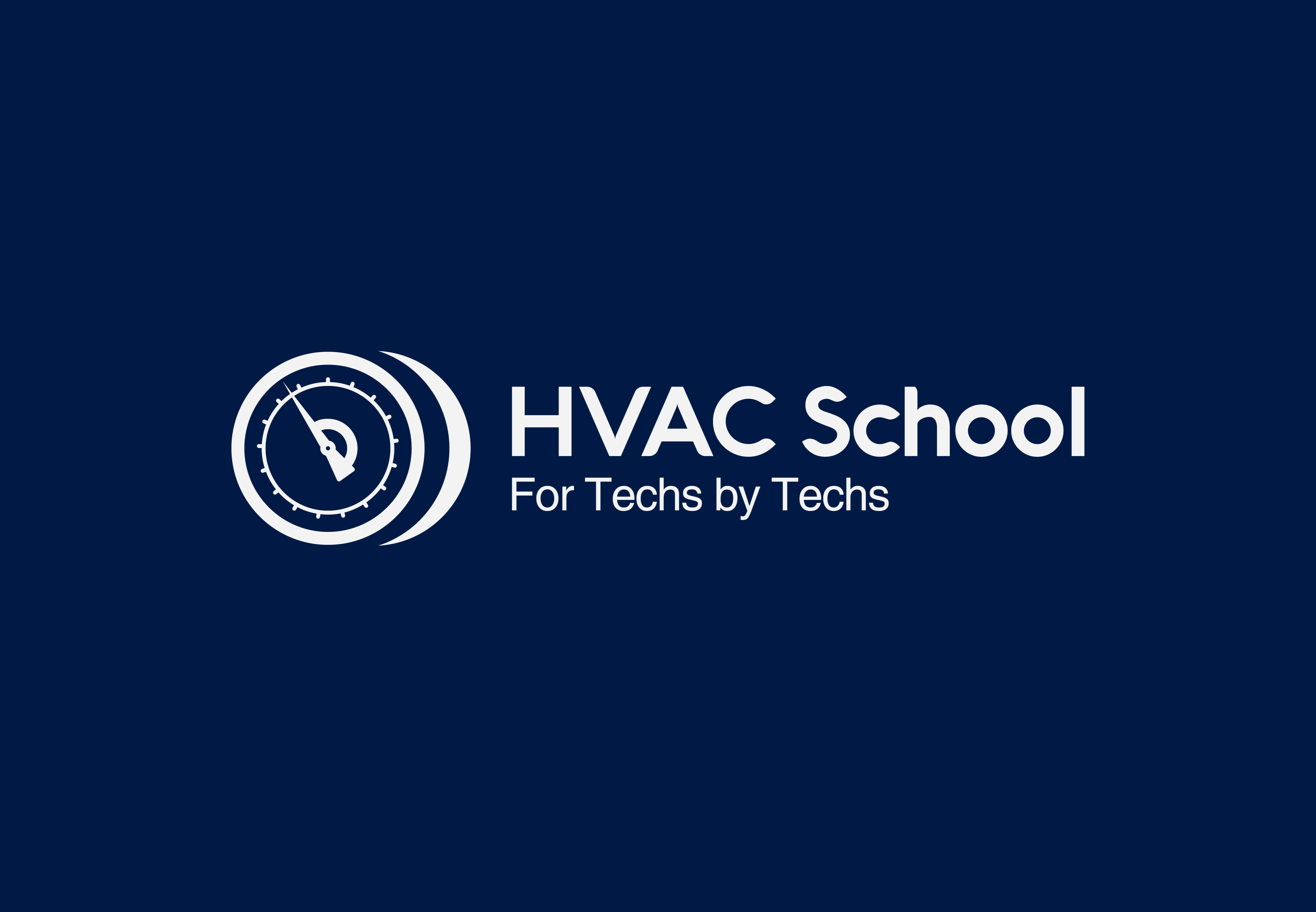
In this quick announcement I talk about the launch of the revolutionary diagnostic and data management tool MeasureQuick
Read more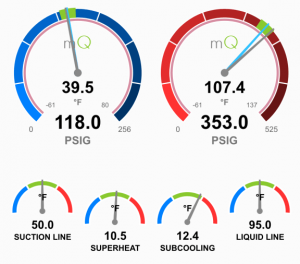
For those of you who follow the podcast, you know how excited I am about the new MeasureQuick app and what it will do to help technicians make better measurements and diagnoses. The app is NOW AVAILABLE on Android and will be available within hours on iOS (Apple). To find out more and to download, […]
Read more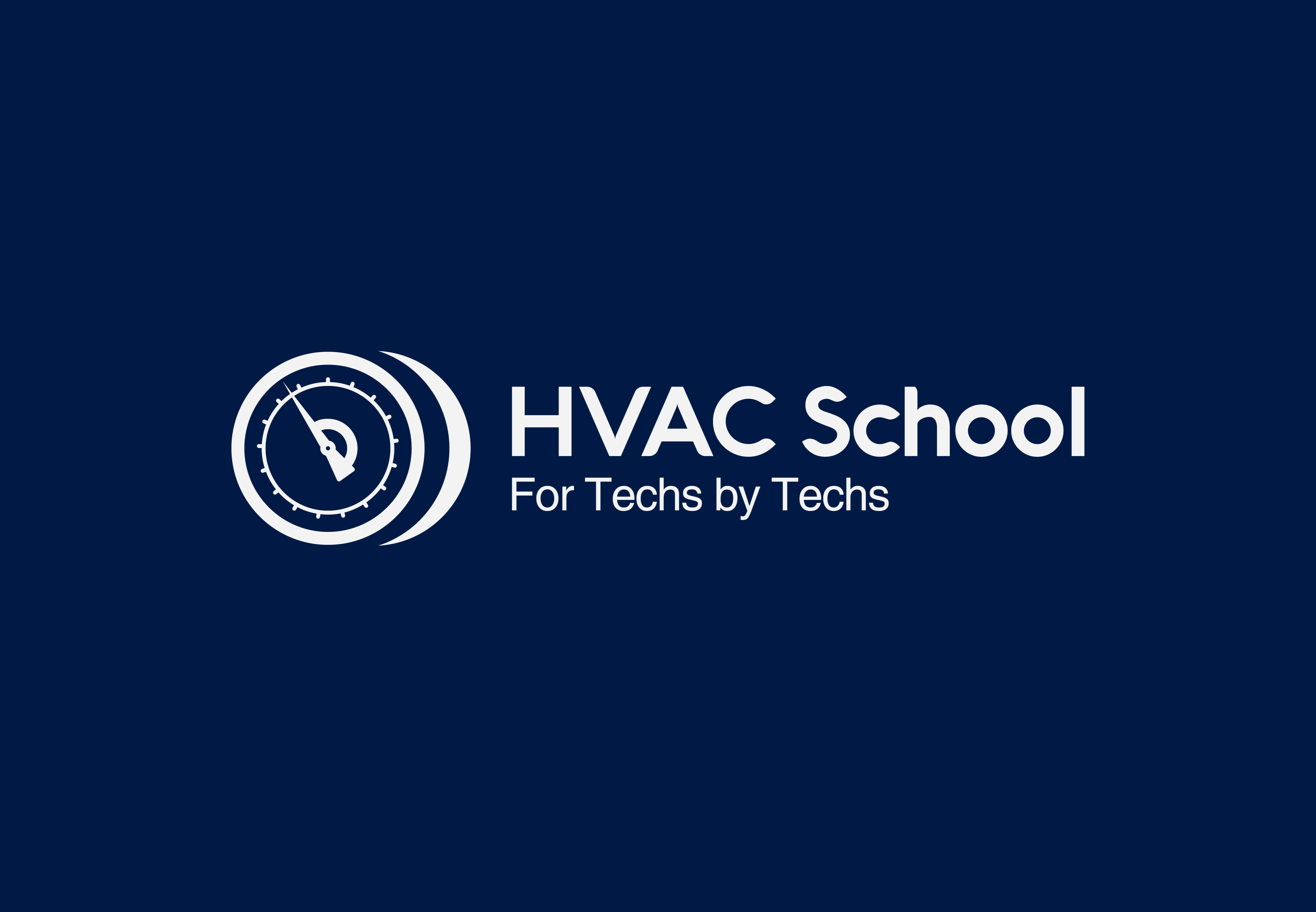
In this episode we talk to Todd Liles from Service Excellence training about techs who shouldn't be on commission, looking to the future and making the most of your career.
Read more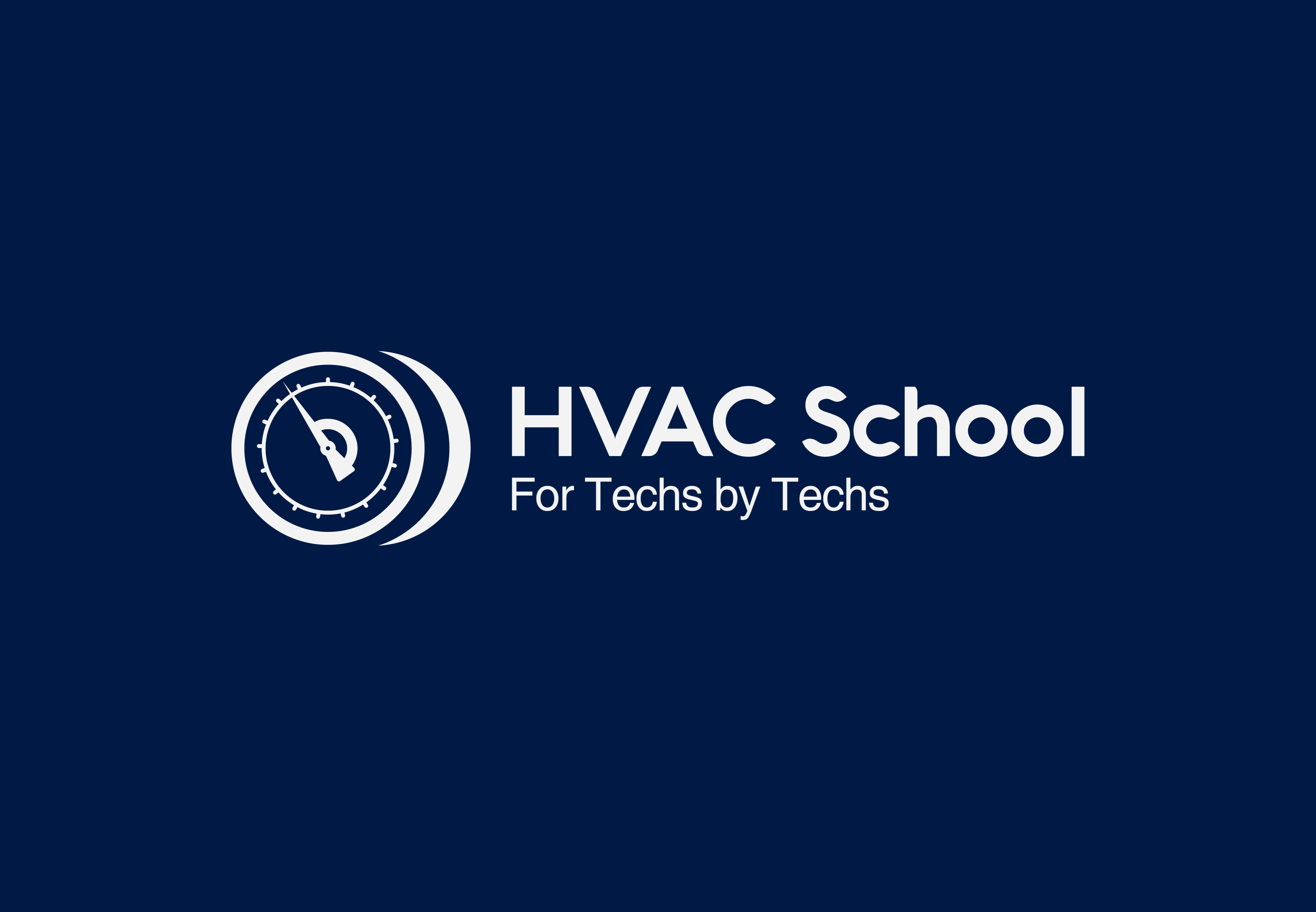
In the episode, Jim Bergmann takes us through evacuation soup to nuts, rig setup, pumps, pump oil, gas ballasts, sweeping nitrogen (triple evac) and much more…
Read more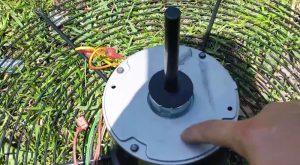
In this 60-second tech tip video by Brad Hicks with HVAC in SC. he shows us how and why to remove the weep port plugs on a condensing fan motor. I know from experience that motors can fail prematurely when this practice isn't followed. Remember that motor orientation dictates which are removed. It (generally) the ports […]
Read more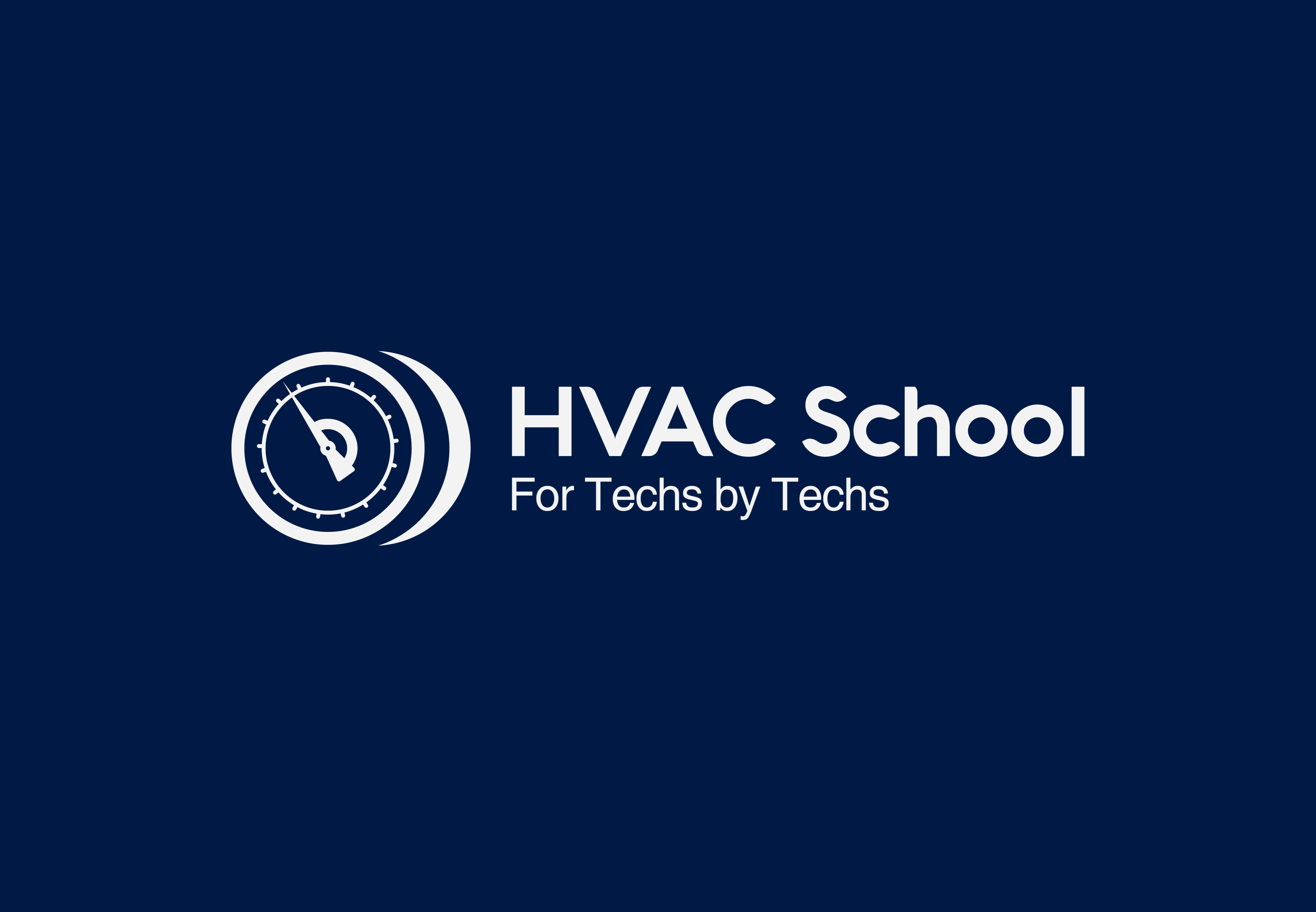
In this episode Brent Ridley talks about the flame free Zoomlock fittings and tool from Parker and why he is using it for almost everything to replace brazing.
Read more