January 2018
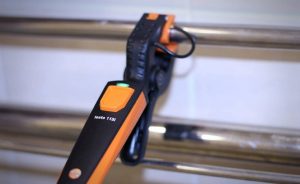
Jim Bergmann and I recorded a podcast for HVAC School that covered when and how to check the refrigerant circuit without connecting gauges. Listener Joe Reinhard listened several times and wrote up this summary of what he gained from the episode. I edited it lightly, but most of this is his work. Thank you so […]
Read more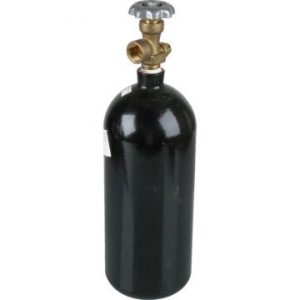
The gas laws. We all learned about them in school and promptly forgot all about them. I really think that we need to dig our books out, dust that information off, and work to understand and apply it. Many will say that nitrogen pressure doesn't change with pressure like other gasses. That is false, but […]
Read more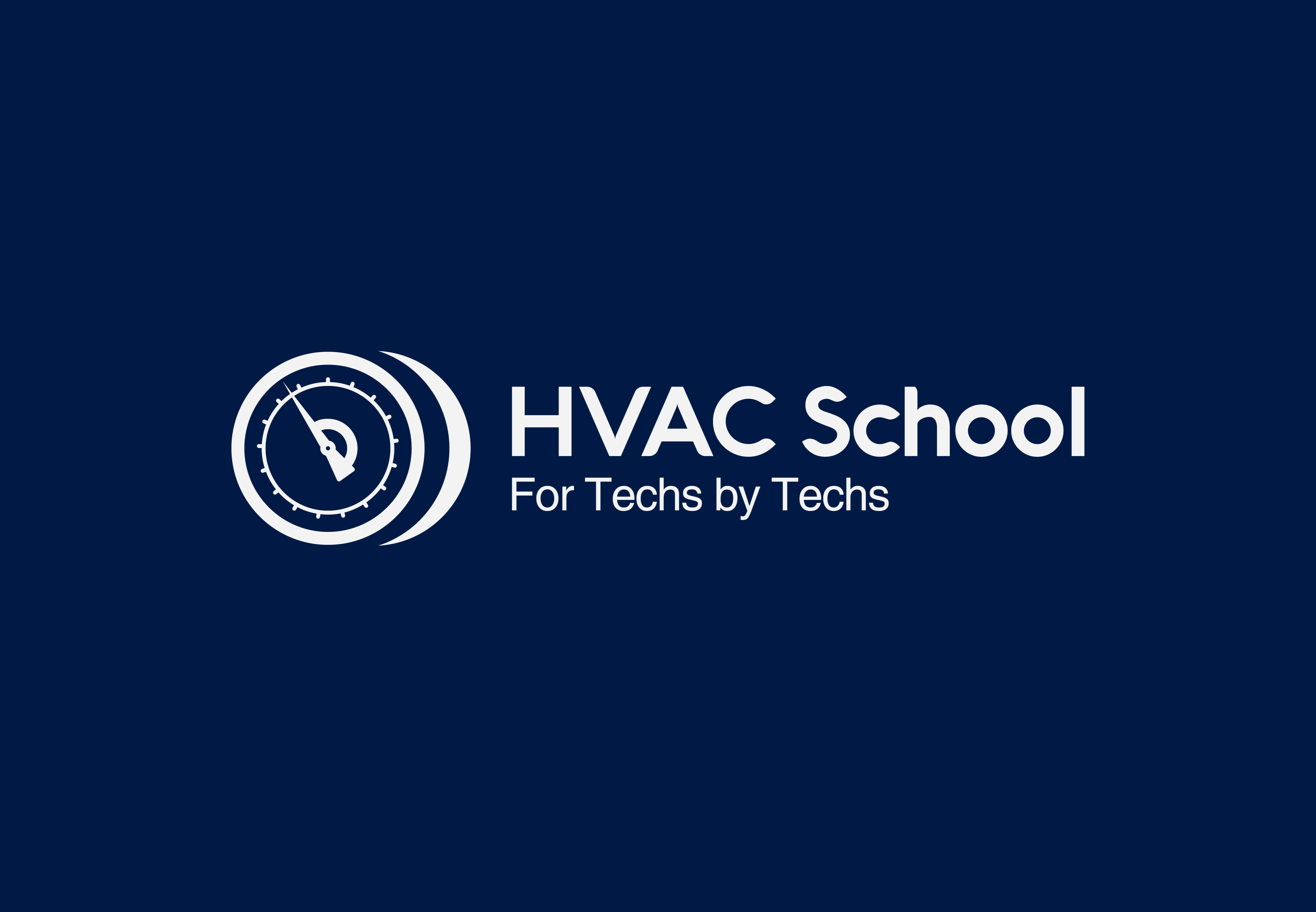
We talk to west coast commercial tech Jim Loring about pneumatic controls and VAV
Read more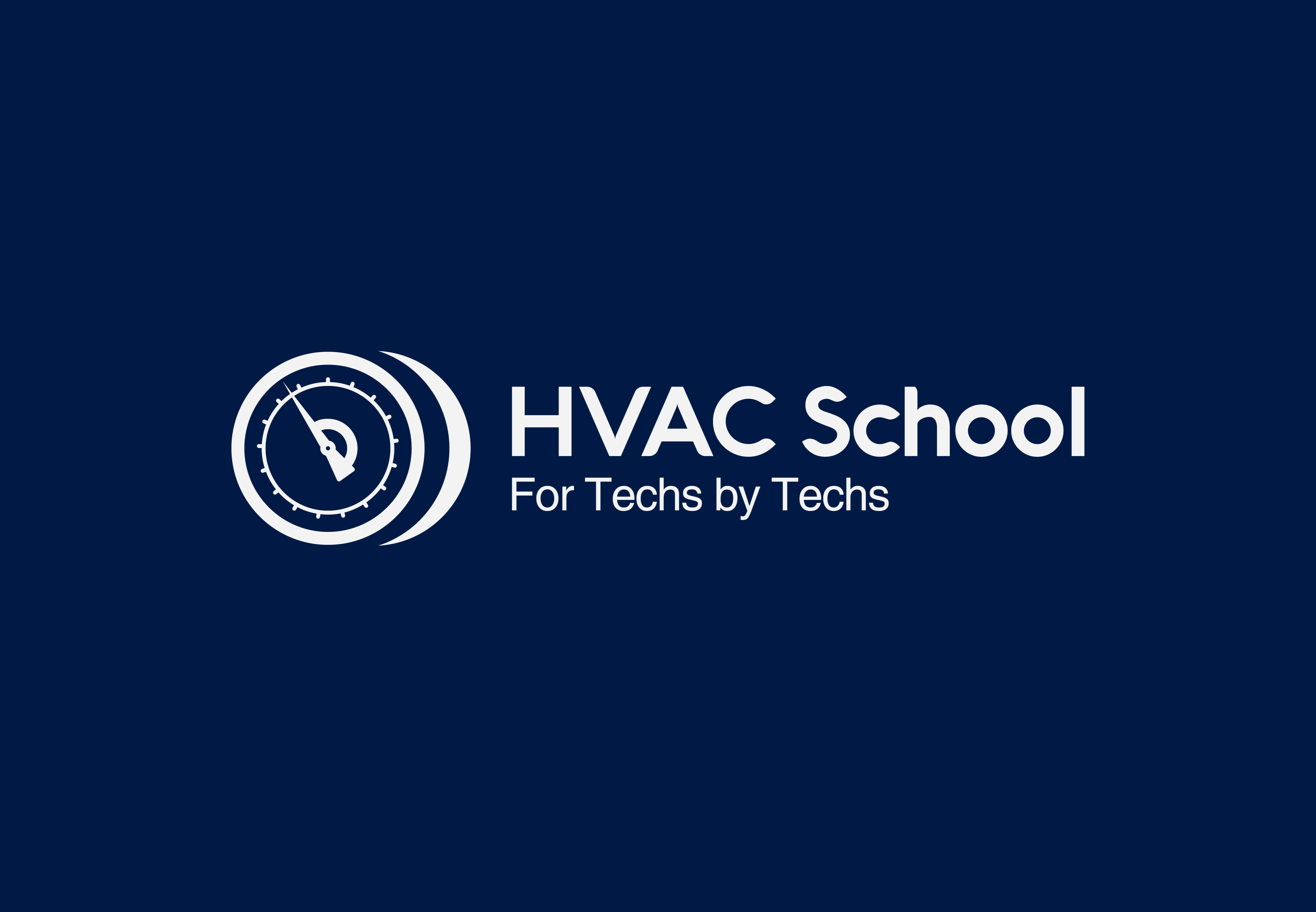
Jeremy Smith goes over floating suction and floating head refrigeration strategies as well as some more on low ambient operation.
Read more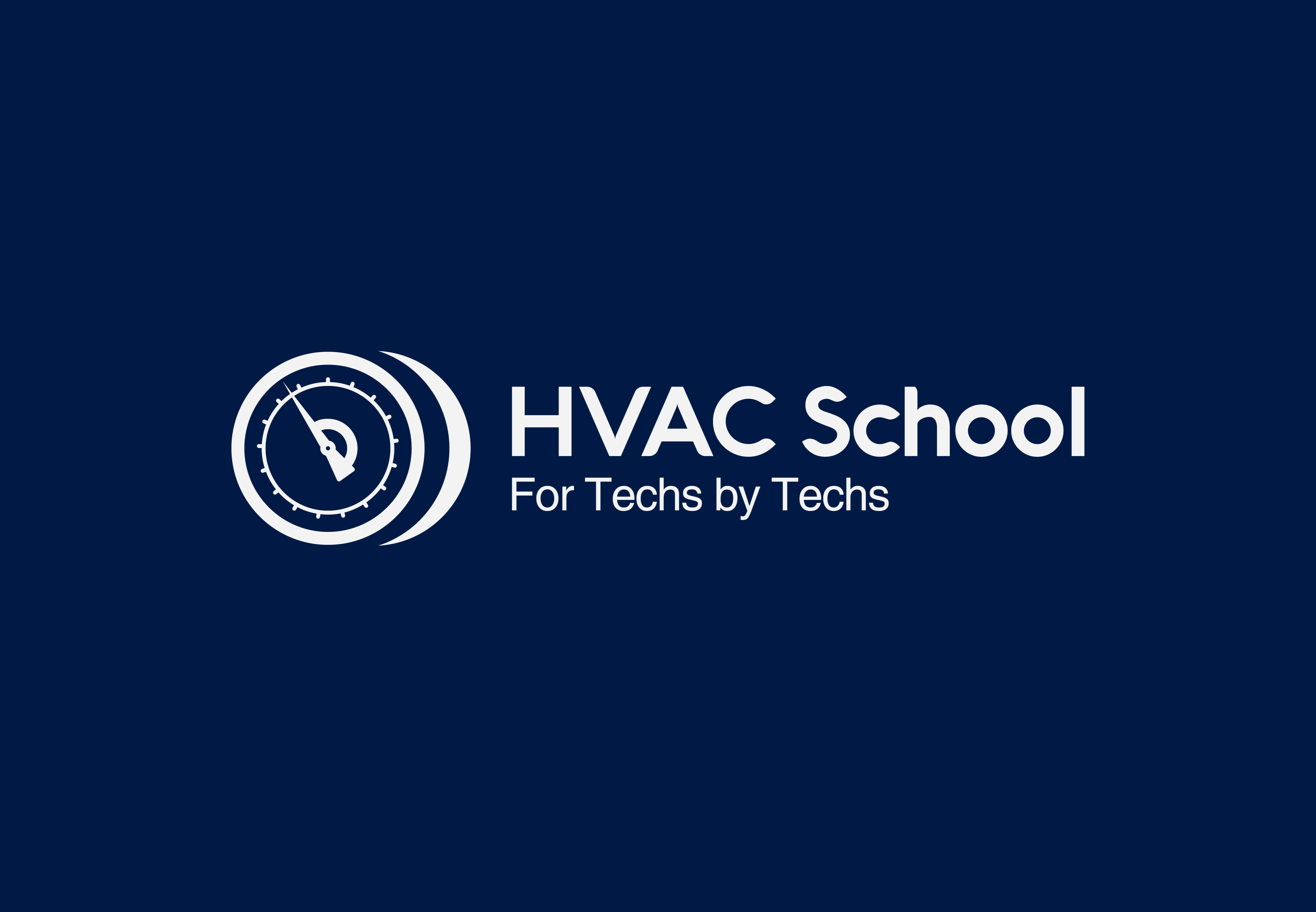
Bryan talks with Jesse and Nathan about setting up dehumidification for residential equipment in general as well as some of the required and recommended settings on an EcoBee thermostat
Read more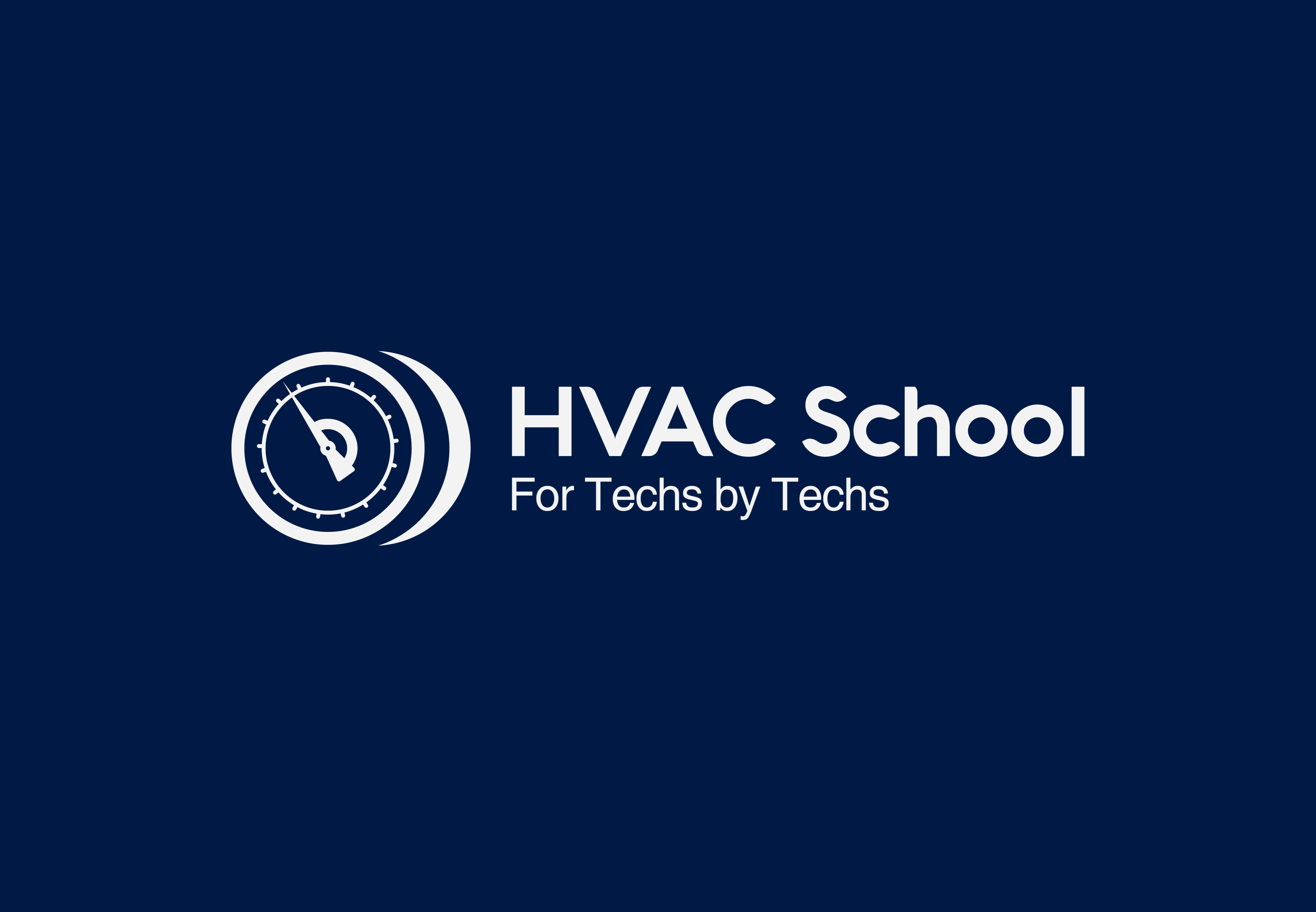
In this episode we cover the skills and traits needed to be the best residential service tech you can be.
Read more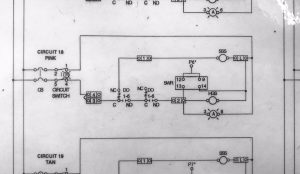
We don't work in a trade of dreamers and unrealistic New Years' resolutions. We are doers who know that nothing worthwhile comes easy, and 2018 is no different. We have some “threats” entering the residential segment of the trade. Amazon and Google are looking to make a bigger entry into the home services trades, standardizing […]
Read more