July 2018

Evacuation Start to finish with some of the best evacuation practices. Click below to see the video. –Bryan
Read more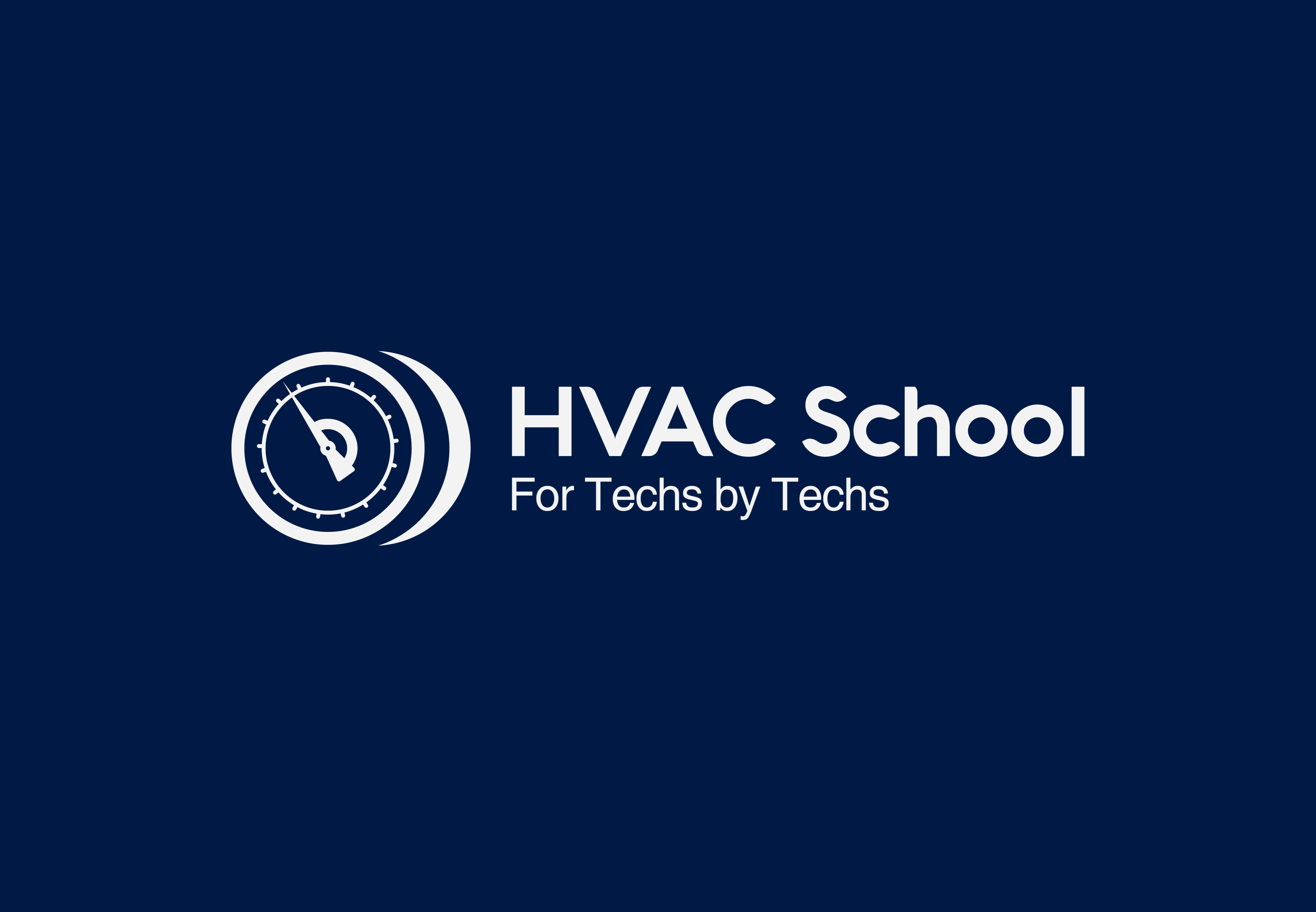
Many techs have said “That's the first thing you should have learned in school” These 4 rules are my vote for the first things to learn in school.
Read more
The year was 1774, and a man named Tom traveled the Atlantic from England to visit his friend Ben in Philly. Tom was 37 years old, and he had already been through a failed business and lost his wife and child during childbirth. He was a troublemaker by some accounts—a free spirit at the very […]
Read more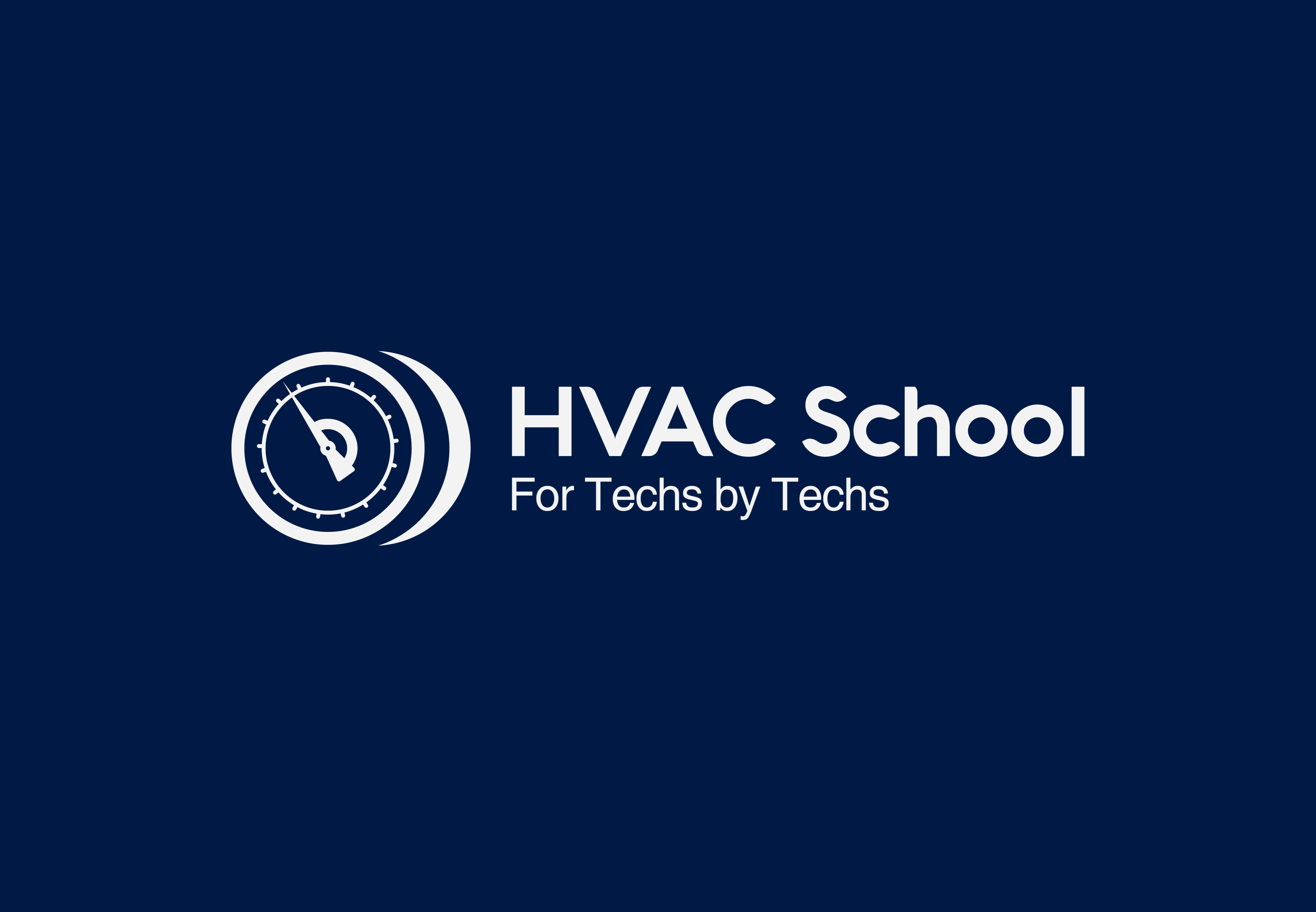
In this episode we speak with founder of Refrigeration Technologies John Pastorello all about chemicals and cleaners and how to best clean a coil
Read more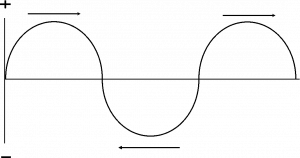
This article (and many other great training articles) was written by my friend and great educator Jamie Kitchen. This article was originally posted on LinkedIn HERE and has been republished for your benefit with his permission. Thanks, Jamie! I remember back in college I was immersed in a particularly challenging problem dealing with poly-phase circuits. […]
Read more