November 2018
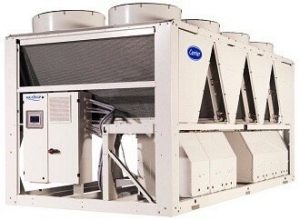
I get emails from time to time with questions that stem from the articles or the podcast. This was a great question, but I was not the best person to answer it. I reached out to Jeff Neiman, our resident HVAC School chiller tech, and he answered it. Here is the question: Hello Bryan, Thanks […]
Read more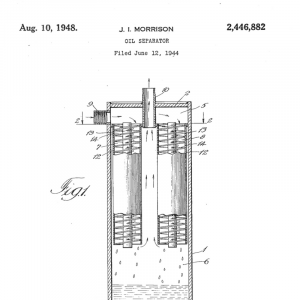
This is a subject that even many commercial guys don’t have to consider. For the majority of equipment, even refrigeration equipment, all that is required for proper oil return is to size the suction line properly, trap the suction line as needed, and allow for proper slope towards the compressor. Then we get into larger […]
Read more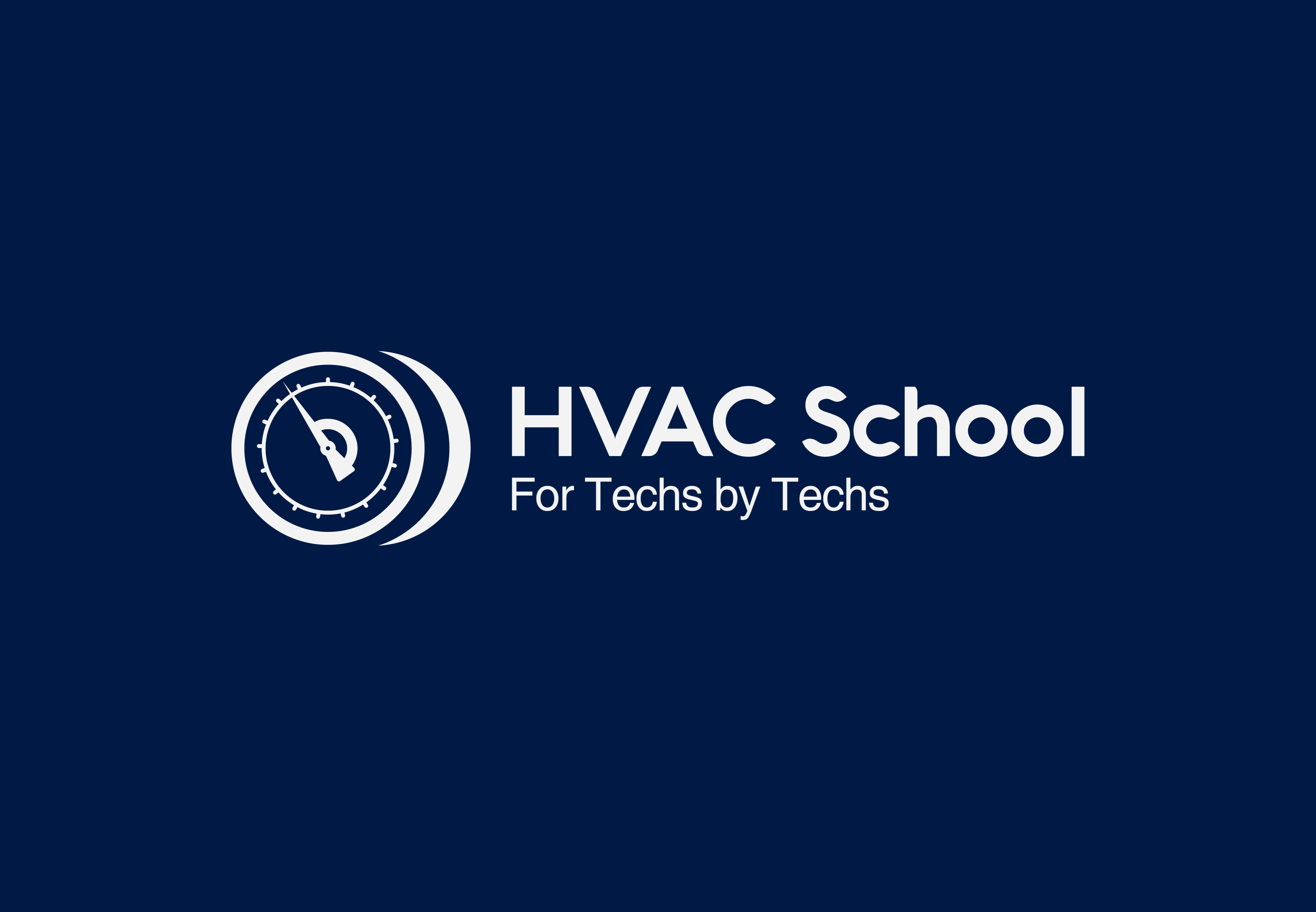
Eric is back and this time we cover hot gas as a dehumidification strategy with all of the broad strokes you should be aware of
Read more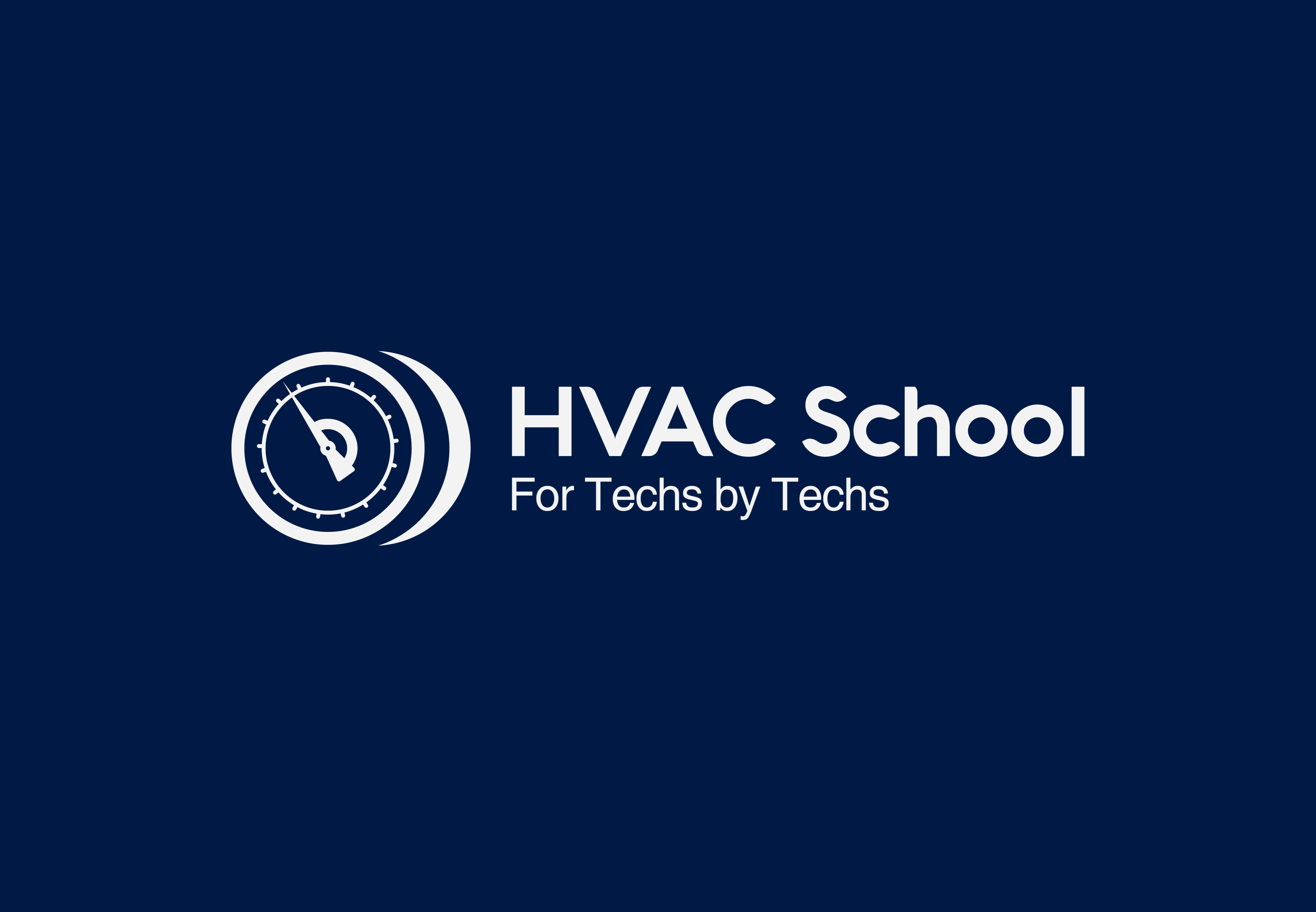
This episode Bryan covers three things you can do to make you a much better tech tomorrow and everyone will notice
Read more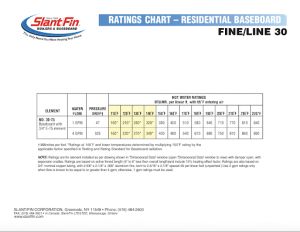
Another follow-up article by Michael Housh… Enjoy! In this article, I thought I would show a pump curve and match it up with our system head-loss curve that we created in the last article, but before I do that, I thought I would talk a little bit more about the system head-loss curve and why […]
Read more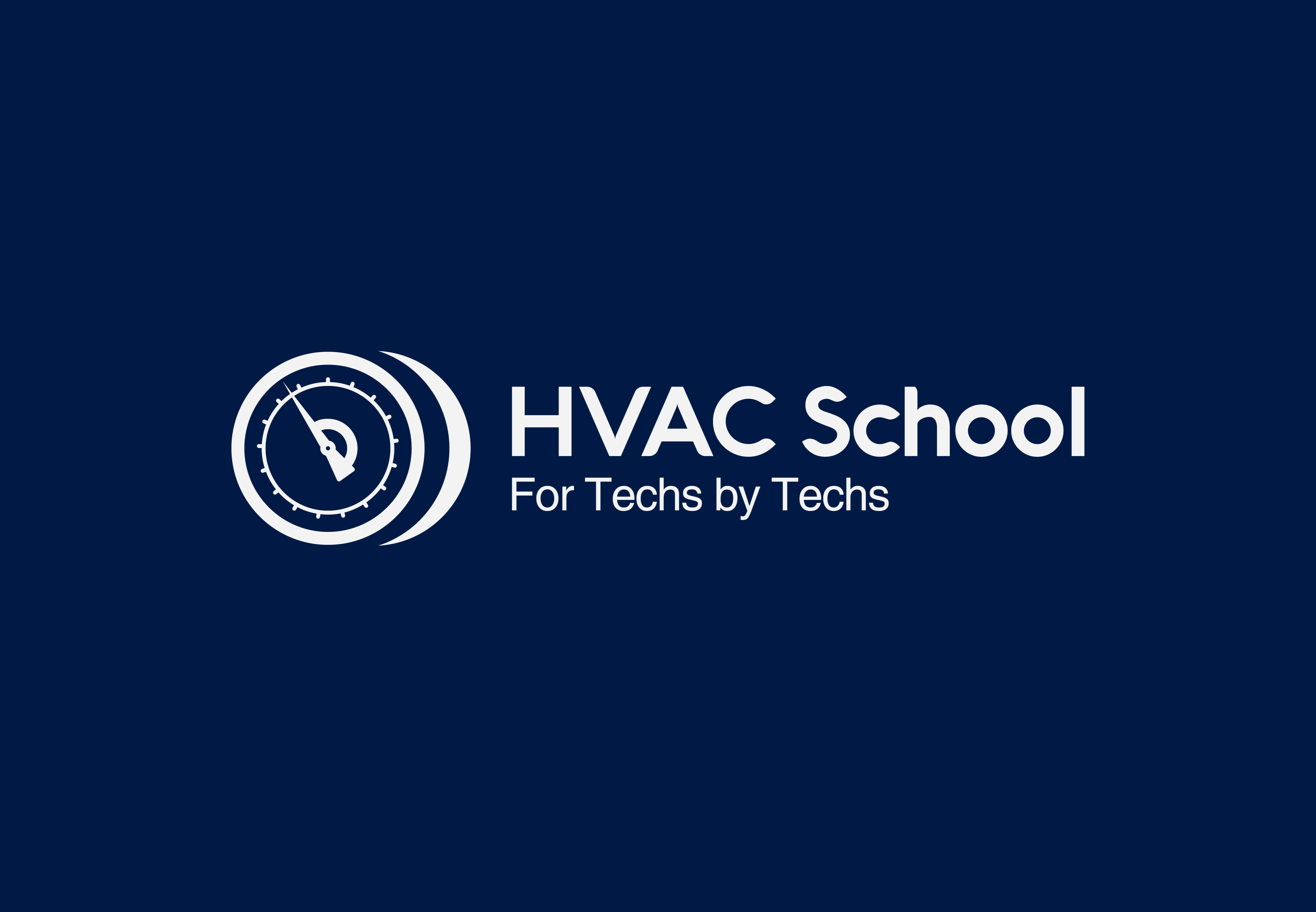
In this episode Jim Bergmann does a deep dive into combustion analysis and covers everything you need to know to keep a furnace running safe and efficient
Read more