December 2018
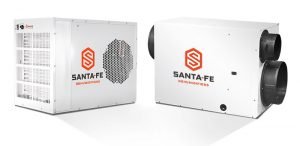
This article is written by tech and business owner Genry Garcia from South Florida. I met Genry at a Solderweld demonstration, and he later offered to write this excellent article. Thanks, Genry! Though dehumidifiers have increased in popularity, thanks in part to the implementation of new building codes, they have become a kind of red-haired […]
Read more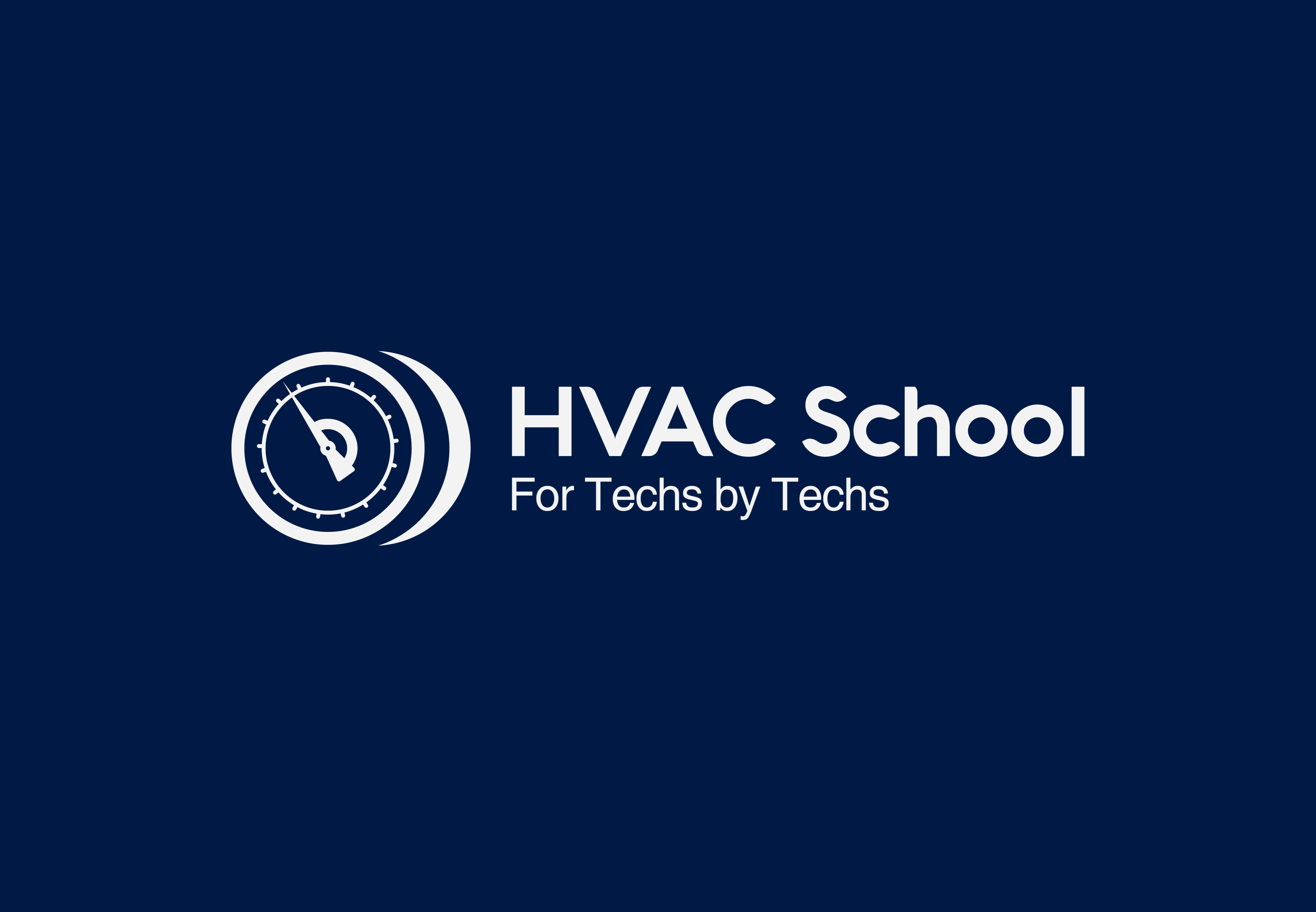
John guides us through all aspects of ventilation and ventilation design with a review of point ventilation, ASHRAE 62.2, whole home ventilation strategies and much more
Read more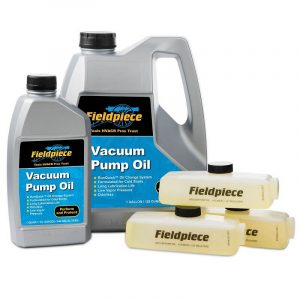
This article is written by Sal Hamidi, founder of Productsbypros.com, an innovative manufacturers representative agency that promotes great HVAC/R products through training and media. You can reach Sal at Sal@productsbypros.com. If we are going to discuss vacuum pump oil, it's important to understand what it is first. Most HVAC application vacuum pumps are rotary […]
Read more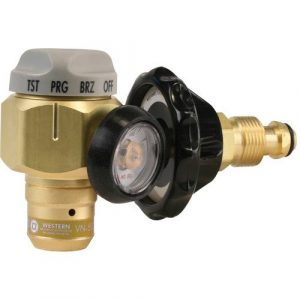
This article was written by longtime contributor and RSES CM Jeremy Smith. Thanks, Jeremy! Nitrogen doesn’t absorb moisture like many techs think that it does, and I think that we, as technicians, need to reevaluate the reasons for the “triple evacuation” process. OK. Hold on, now. Put down the pitchforks and torches, and give me […]
Read more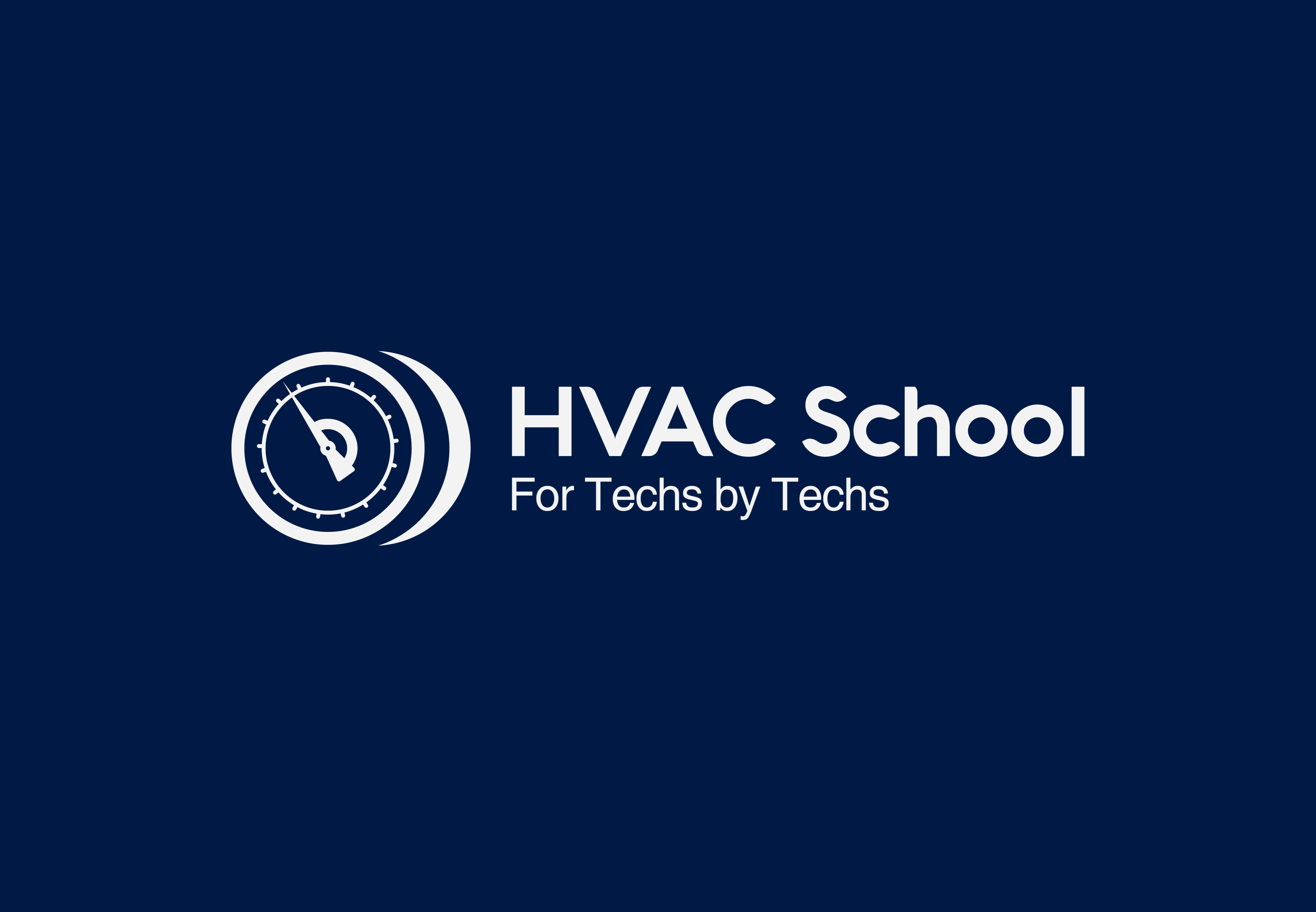
Bill and Bryan discuss manometers, combustible gas detectors, personal CO detectors, draft gauges and combustion analyzers
Read more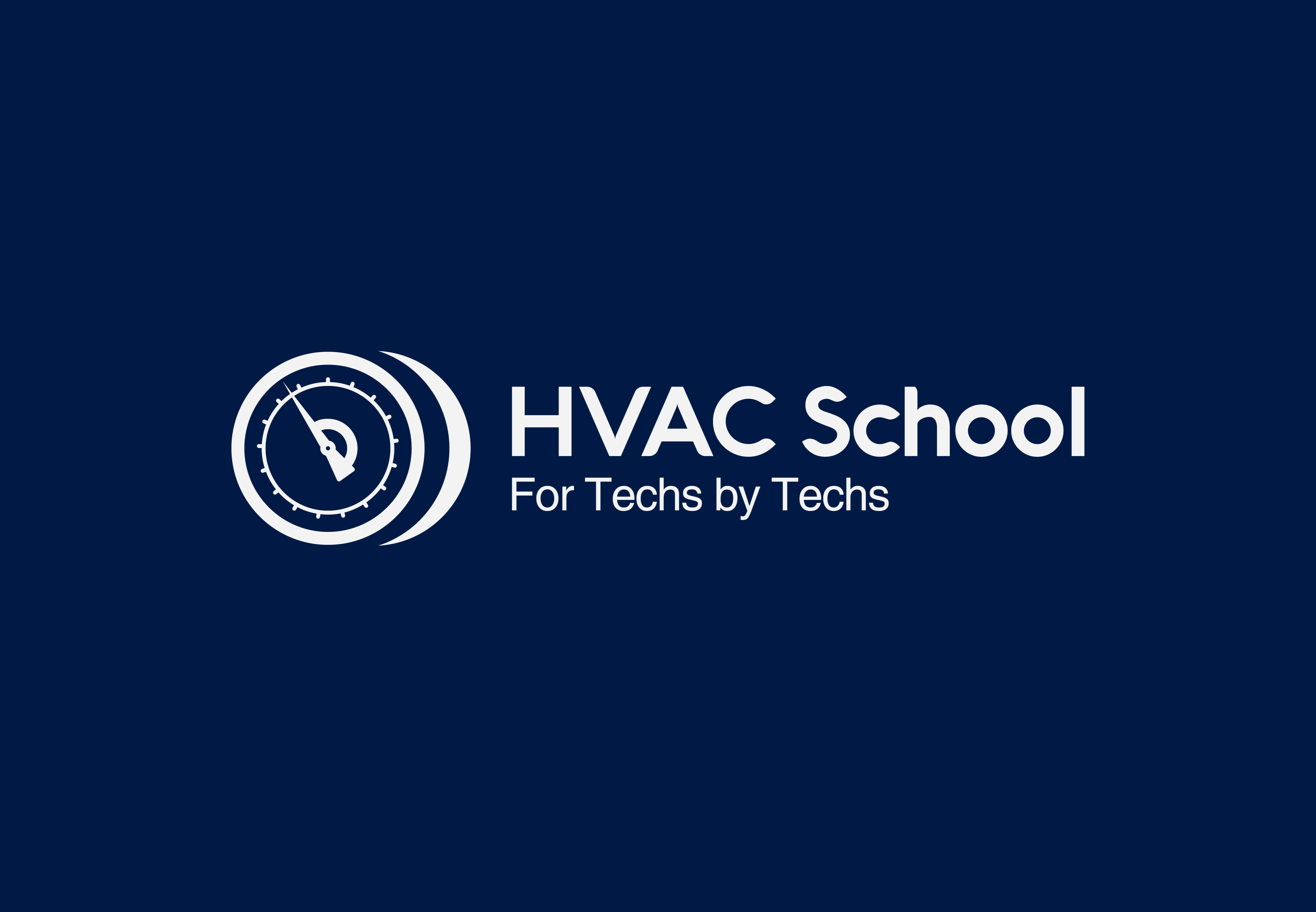
In this episode Bryan speed talks through all the basics of a heatpump and how it functions.
Read more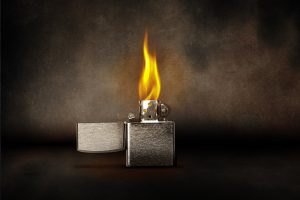
Does heating the air cause the humidity in the air to decrease? Yes and no. Heating air causes the RELATIVE humidity percentage to decrease, but it does not change the overall moisture content in grains of moisture per lb of air. Many old-timers will swear a blue blaze that oversizing a furnace will directly result […]
Read more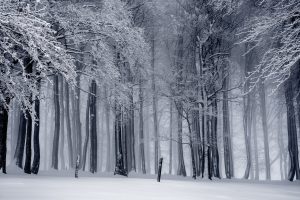
I was listening to someone talk about air relative humidity the other day while looking at a psychrometric chart, and he commented that the chart ends down at freezing (32°F) because “all the water freezes out of the air at that point.” I think I made this Jed Clampett face: The psychrometric chart is designed […]
Read more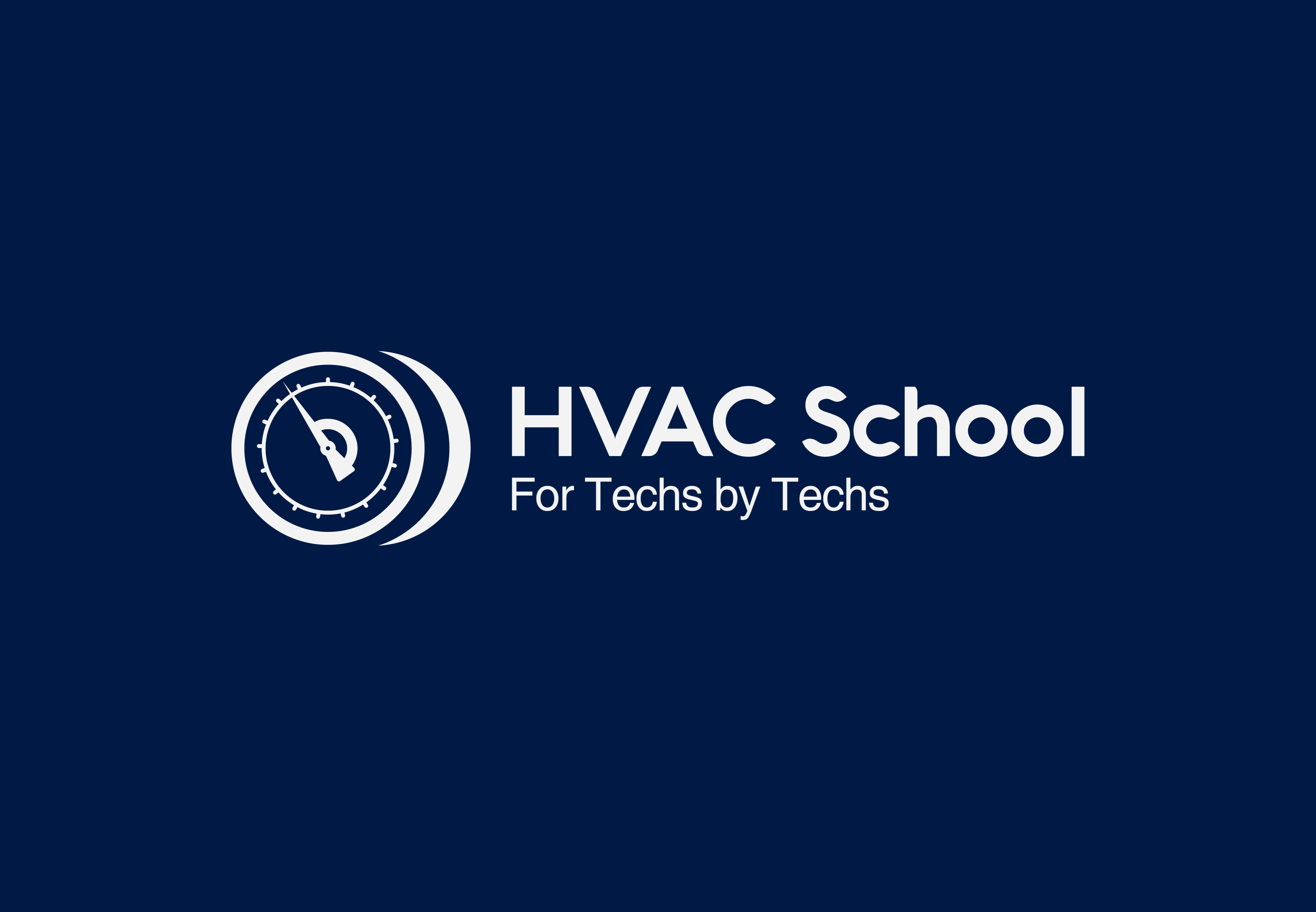
Jason from ESCO and Cengage comes on to talk about the varying landscape of EPA 608 regulations with what you need to know for now
Read more