2019
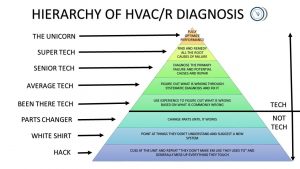
WARNING: THIS ARTICLE CONTAINS GENERALIZATIONS. IT DOES NOT APPLY TO EVERYONE, AND WE HAVE ALL PROBABLY BEEN ALL OF THESE AT ONE POINT OR ANOTHER. IF YOU FEEL PERSONALLY ATTACKED, I SUGGEST FINDING A SAFE SPACE AT A WEST COAST UNIVERSITY AND BORROWING A BINKY FROM A NEARBY TODDLER. ALSO, MY CAPS LOCK BUTTON IS […]
Read more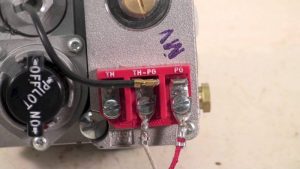
Jesse Grandbois is a tech who reads the tech tips, and he wrote a few tips that he wanted to share on some gas furnace control basics. This tip is about how to use a fancy digital stat on a millivolt system. For those of you who don't know, a millivolt system uses a thermocouple/thermopile […]
Read more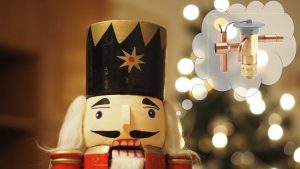
There's a moral to this story, though it is a bit more of a cautionary tale than most I write. While it doesn't rank with the story of three wise men or even Frank Capra's Christmas classic “It's a Wonderful Life,” you may find some common threads with both learning wisdom and remembering why throwing […]
Read more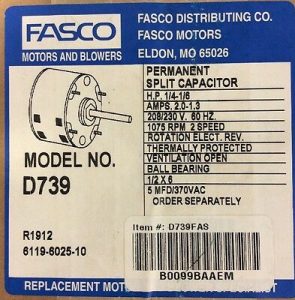
One aspect of motor selection that can get overlooked is motor bearings, and it can have big consequences. Sleeve bearings are most common in residential and light commercial applications because they are less expensive and quieter. They don't have rolling “balls” but rather rely on a thin film of oil on metal sleeves. Sleeve bearings […]
Read more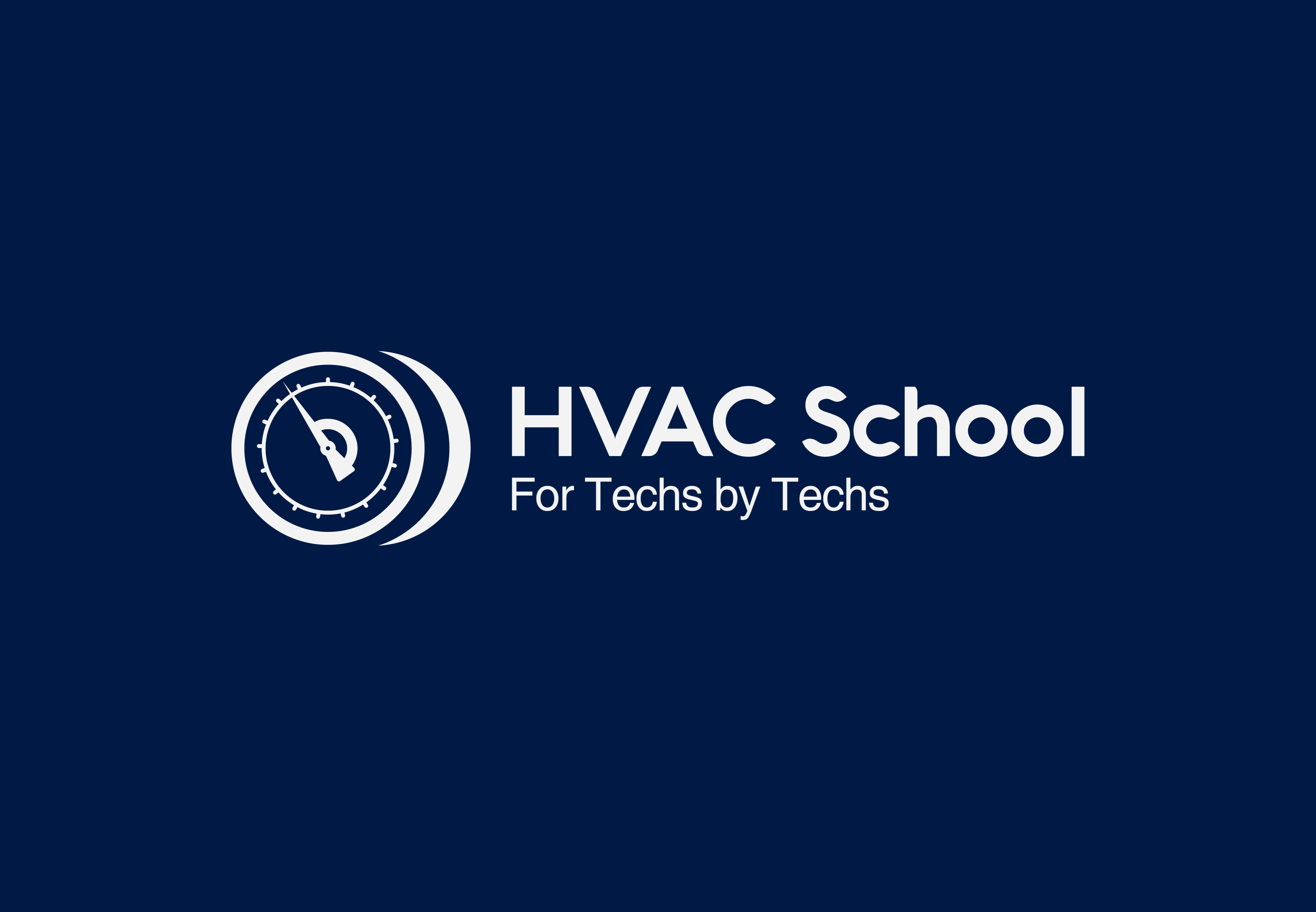
We have four techs join us to talk common furnace issues and best practices
Read more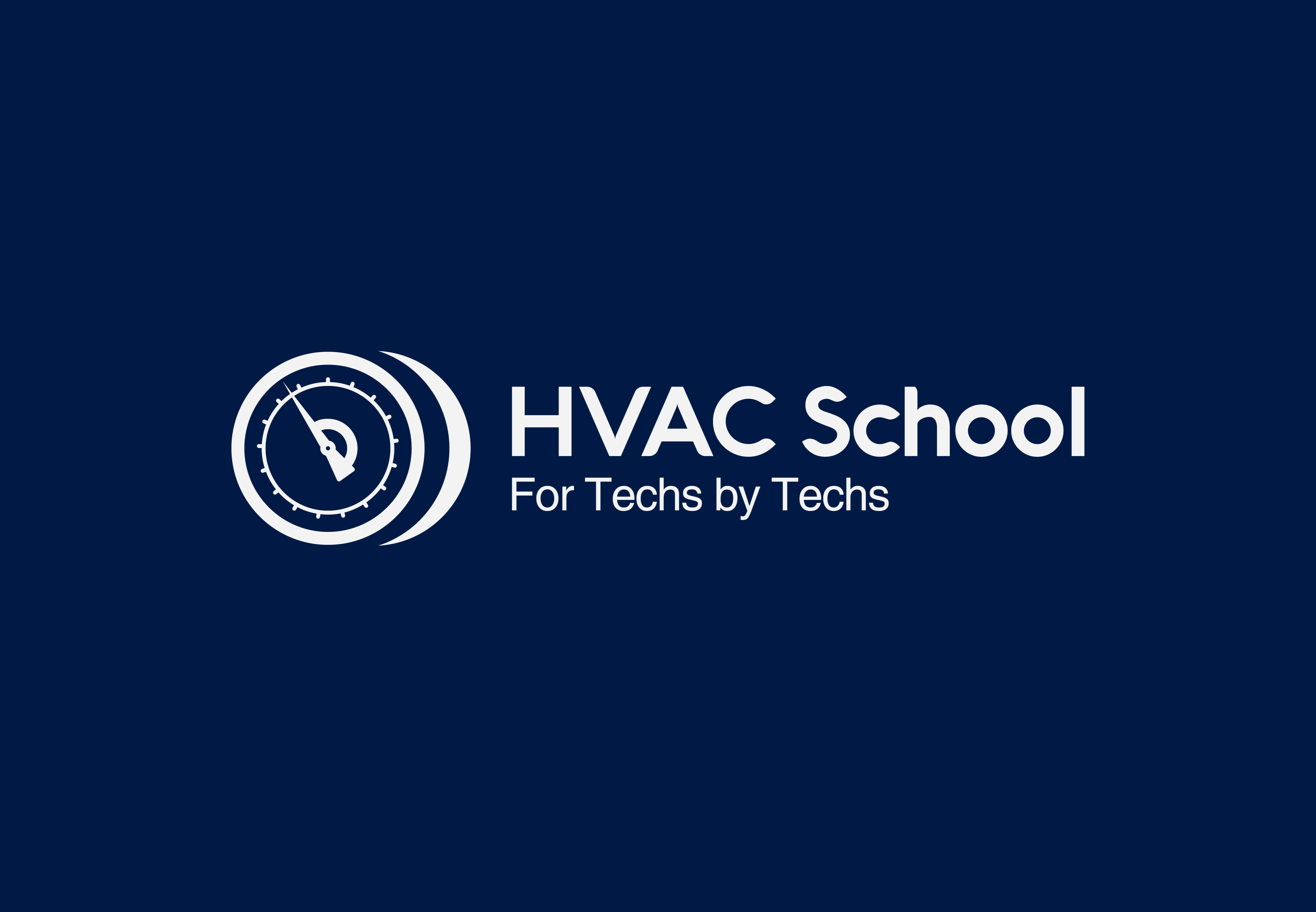
David Richardson with NCI joins us on the podcast to talk mixed air temperature and more Nationalcomfortinstitute.com
Read more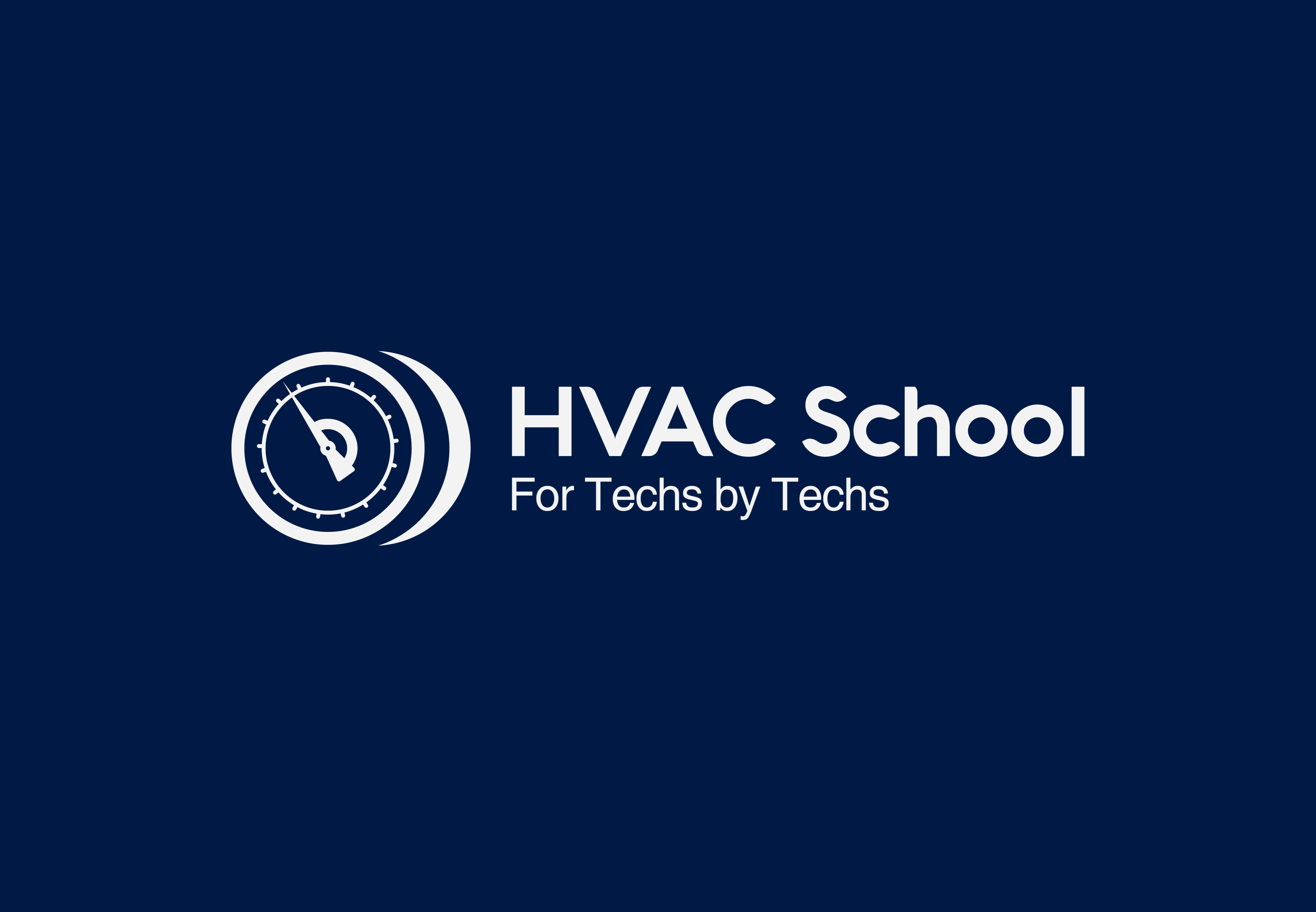
A quick conversation on using a voltmeter to measure “voltage drop” across loads and switches and some of the differences
Read more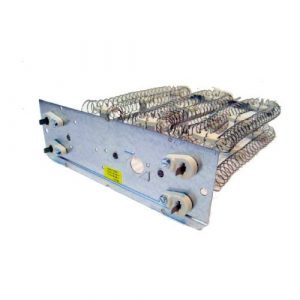
I started working as a tech when I was 17 years old, fresh out of trade school. My first winter out on my own, I went to a service call in an older part of Orlando, a part of town I had never worked in before. It was an especially cold winter that year, and […]
Read more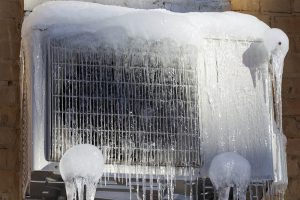
Here's another quality tech tip from senior refrigeration and HVAC tech Jeremy Smith. Jeremy lives in Ohio, so he knows a thing or three about the cold. As HVAC/R techs, we're often called on to work in some of the worst weather conditions. With the cold weather, I thought it timely to share some tips […]
Read more