March 2019
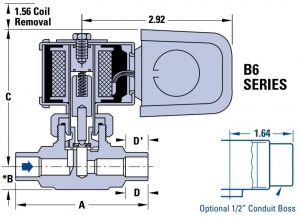
Do you know how a solenoid valve works? Really? On the surface, I think we all understand how a solenoid valve works. The coil energizes, creating an electromagnet. That temporary magnetism lifts an iron plunger within the valve allowing refrigerant to flow. But is it really that simple? It turns out that the answer isn't […]
Read more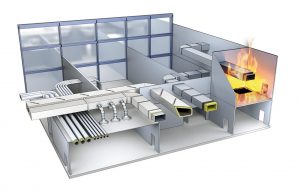
I heard a great presentation by Ron Auvil on VAV systems, and it got me thinking… Can you size a commercial system/perform a block load by the number of occupants? Yes! No, I'm just kidding. That's crazy talk. There is way more to it than that. However, in a commercial environment, while the building's perimeter […]
Read more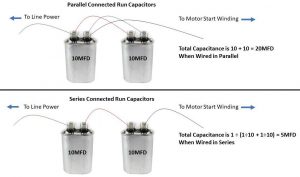
Knowing how to combine capacitors in series and parallel properly is a great practical field skill to employ when you need to get a customer up and running, but you don't have the exact size. Increasing in size is easy. Just connect in parallel and add the two sizes together. For example, if you needed […]
Read more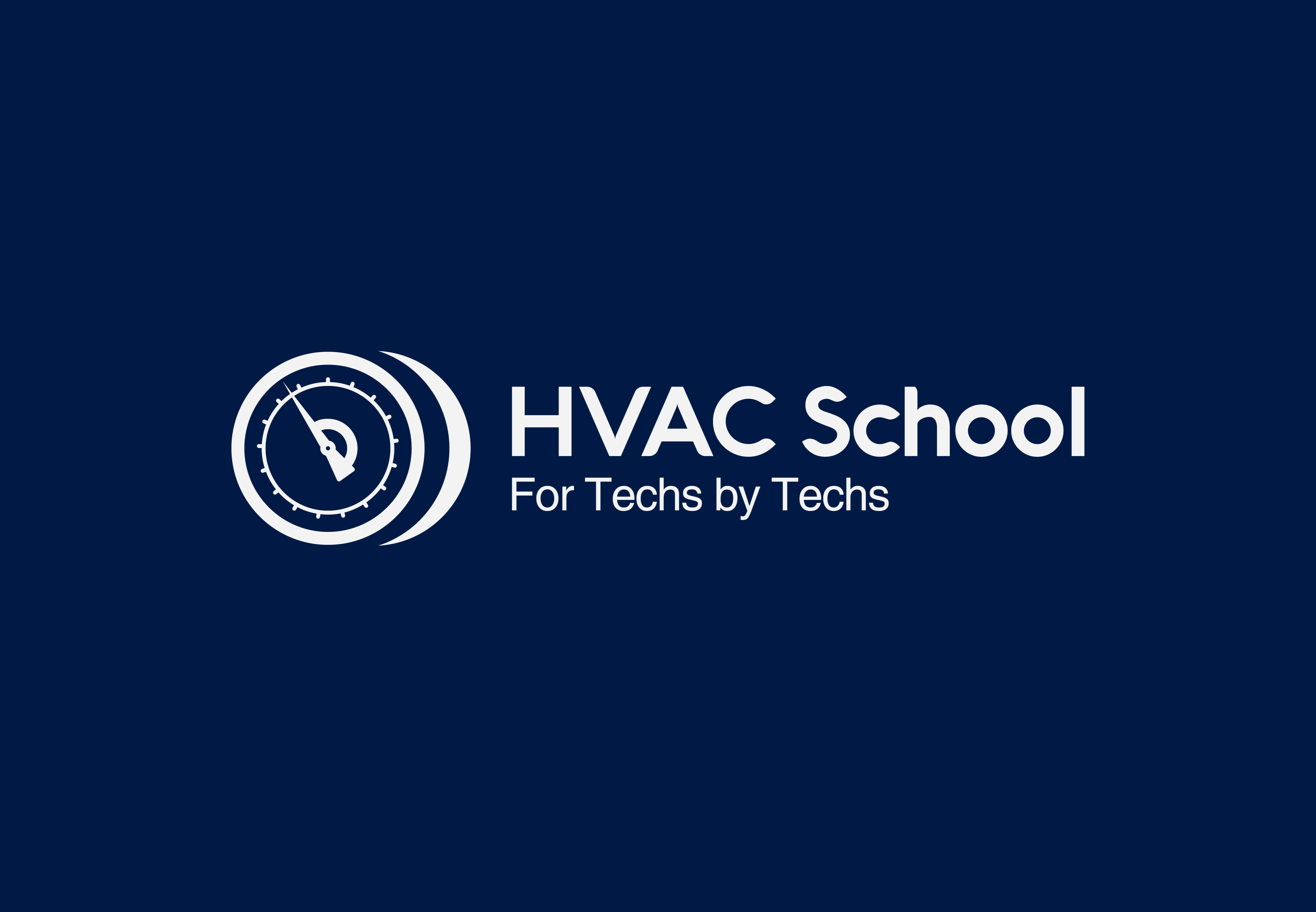
Bert and Bryan discuss the commonly repeated phrase “refer to manufacturers specs” and when it works and when it feels like a crutch.
Read more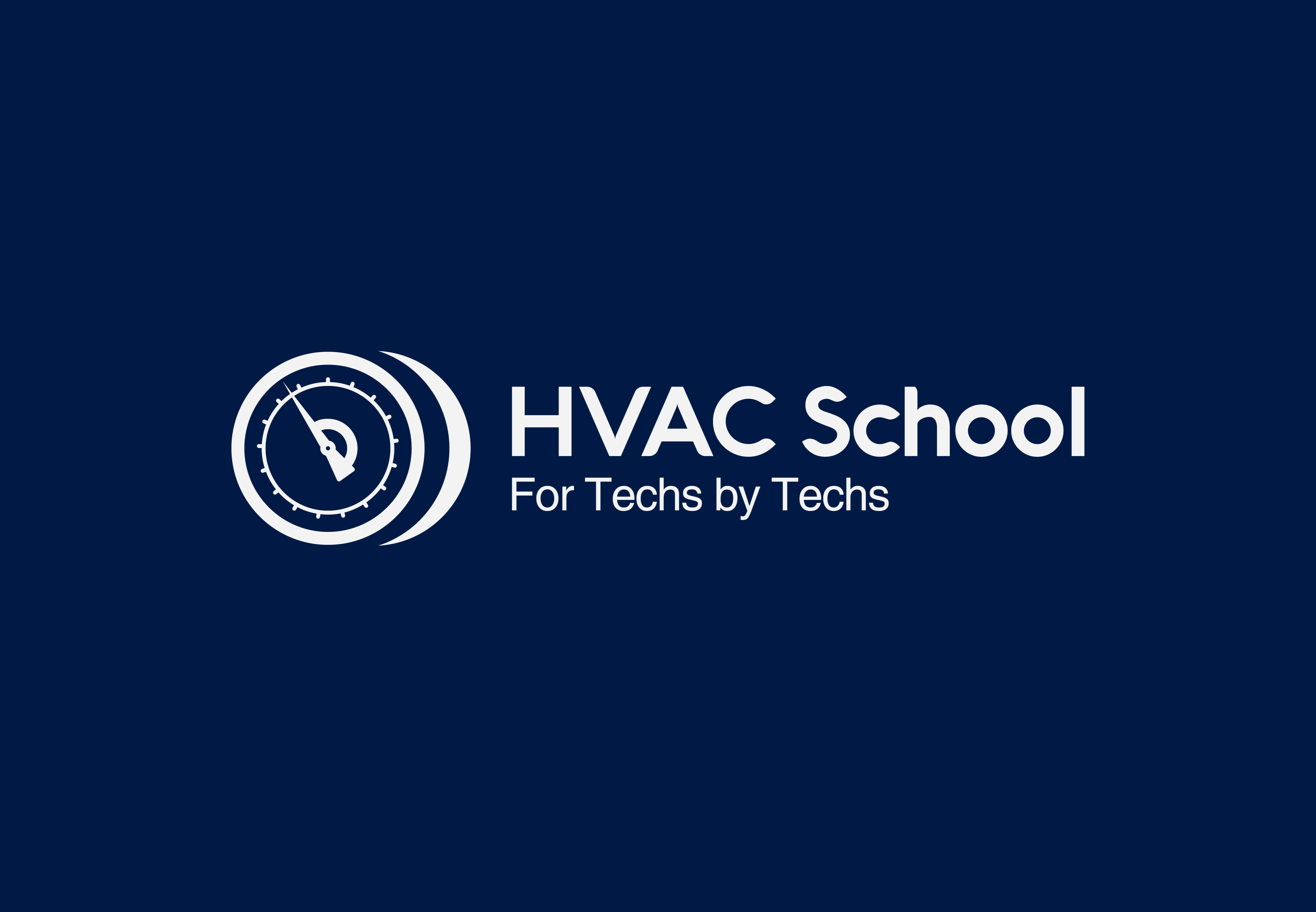
Duct and system design are two of the BIGGEST needs among technicians, salespeople and contractors. Matt Milton has generously agreed to teach a small online mastermind class on design, load calculation, the math of the trade and much more. While this training may be at “no charge” it certainly isn't FREE. It will require a […]
Read more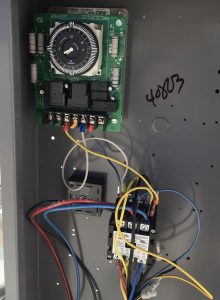
This article is a quick, real-life diagnosis/find by Kalos Services senior commercial HVAC/R tech Eric Mele. Improper Defrost Timer installation While servicing this display cooler for an unrelated problem, I noticed the defrost timer installed in a way that will almost certainly cause early compressor failure. Because this is a cooler (not a freezer), it […]
Read more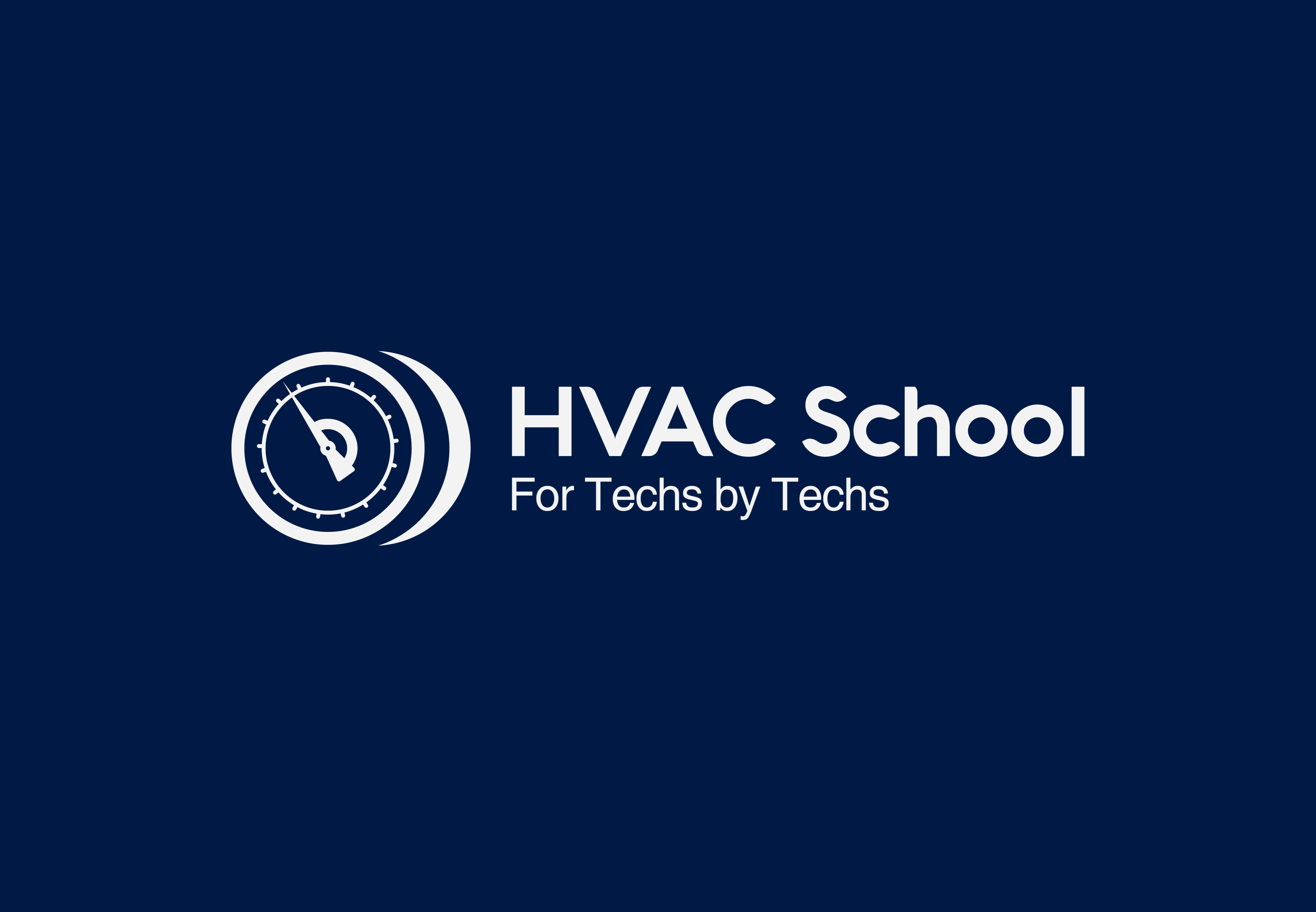
Bryan and Bert talk through a real-life issue we all face as techs. Bert’s recent video “triggered” Bryan a bit and they talk through it.
Read more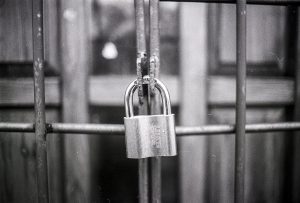
Before we jump into the stuff that will make folks angry, let's start with some common ground. Most of us can probably agree that the desired result of education in the trades is: Knowing what you are doing and doing it as safely, efficiently, and correctly as possible. If we can agree that we all […]
Read more