April 2019
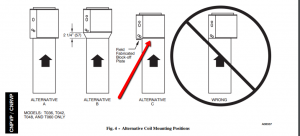
On occasion you will either find a furnace or be tasked with installing a furnace where the coil overlaps the edge of the furnace because the coil is wider. In the case of a Carrier CNPVP coil you need to ensure that you align the coil according to manufactures specs or you risk cutting off […]
Read more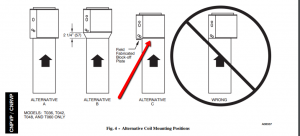
On occasion, you will either find a furnace or be tasked with installing a furnace where the coil overlaps the edge of the furnace because the coil is wider. In the case of a Carrier CNPVP coil, you need to ensure that you align the coil according to the manufacturer's specs, or you risk cutting […]
Read more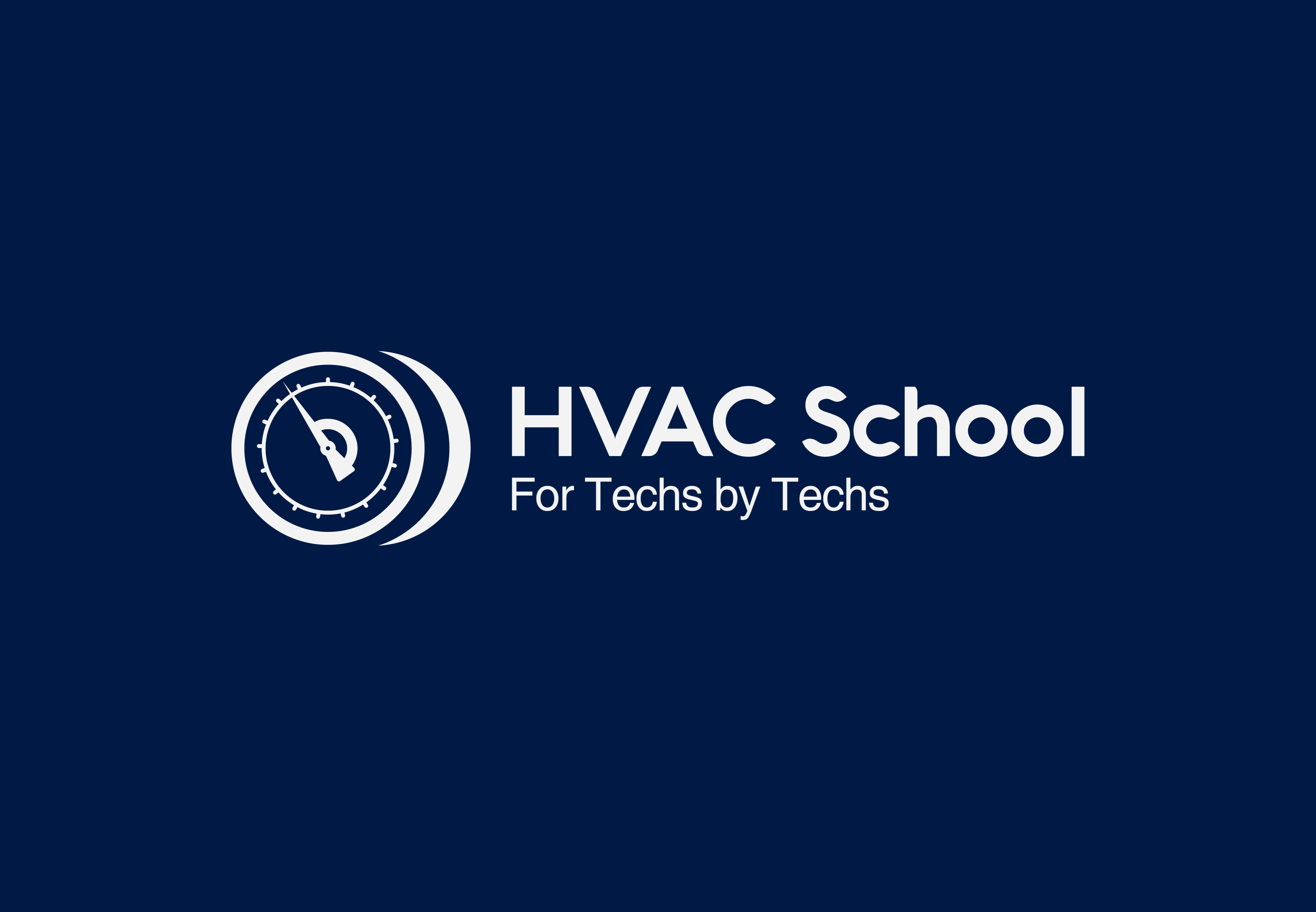
Jim Devlin from Weil-McLain joins us to talk high efficiency and cast iron boilers and how you can use them together in a “hybrid” configuration to serve your customers
Read more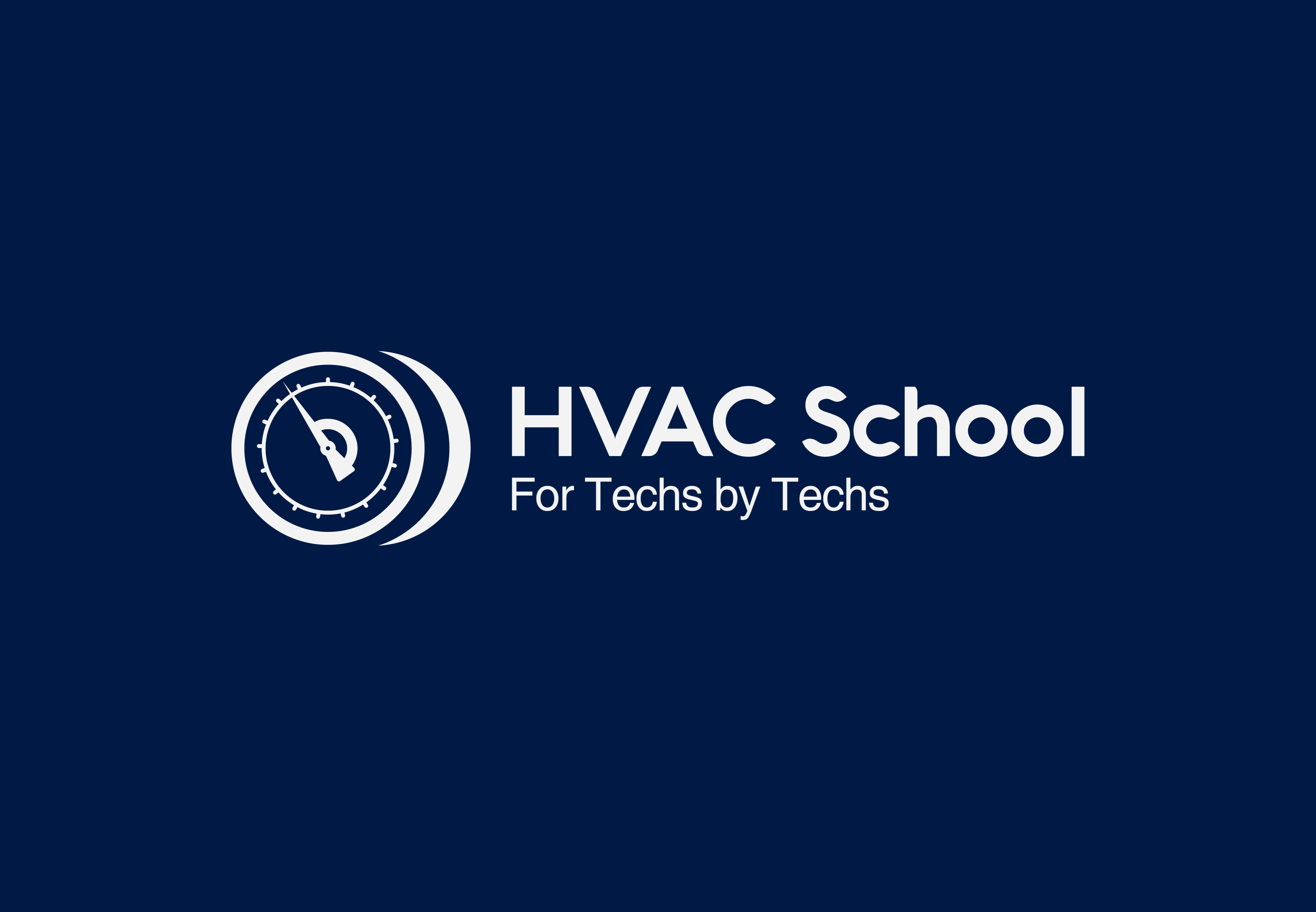
Do you need different gauges for each refrigerant? We discuss.
Read more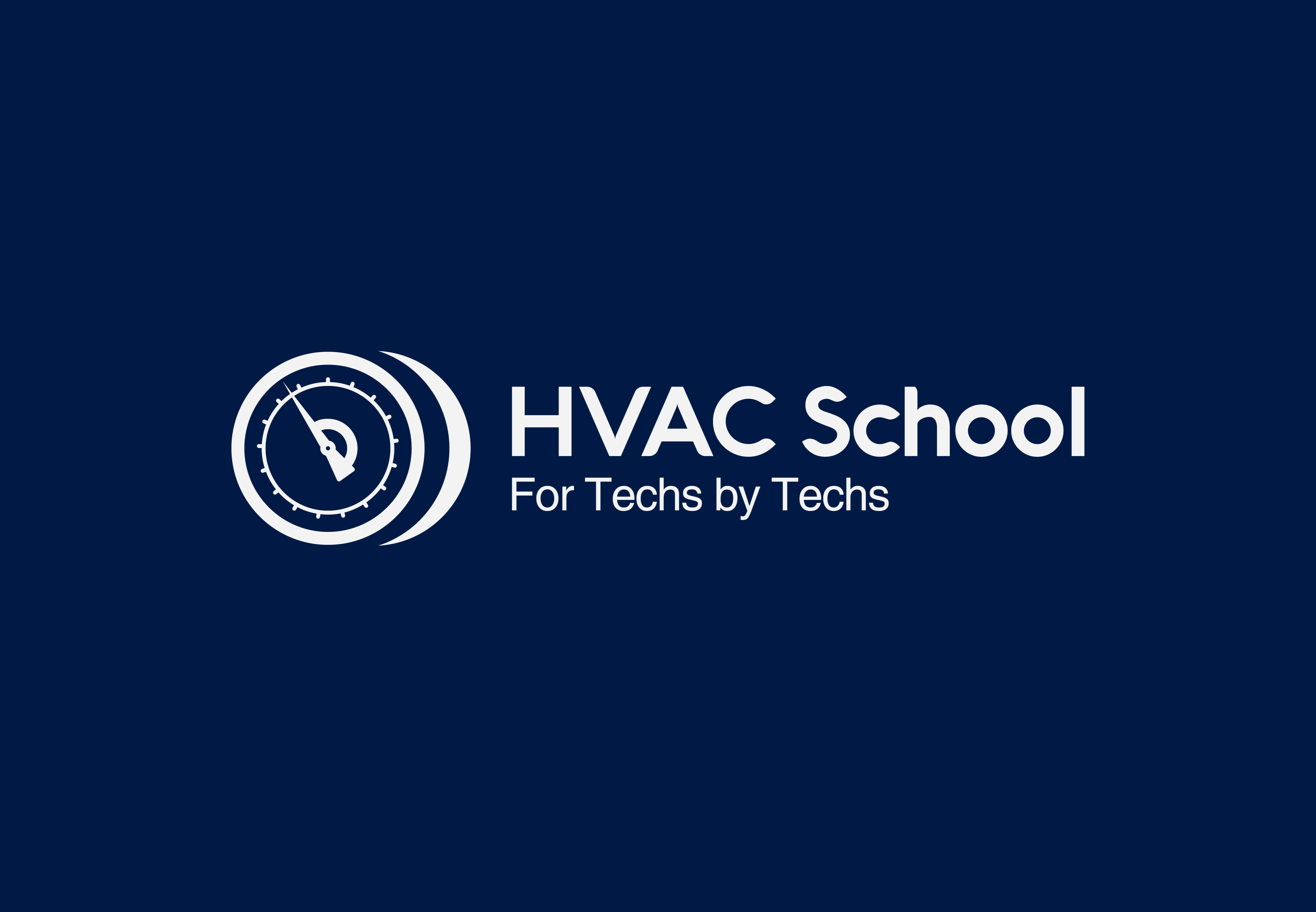
In this two part interview Moe Hirsch goes deep an wide on buffer tanks and strategies for “parking” btus in hydronic systems
Read more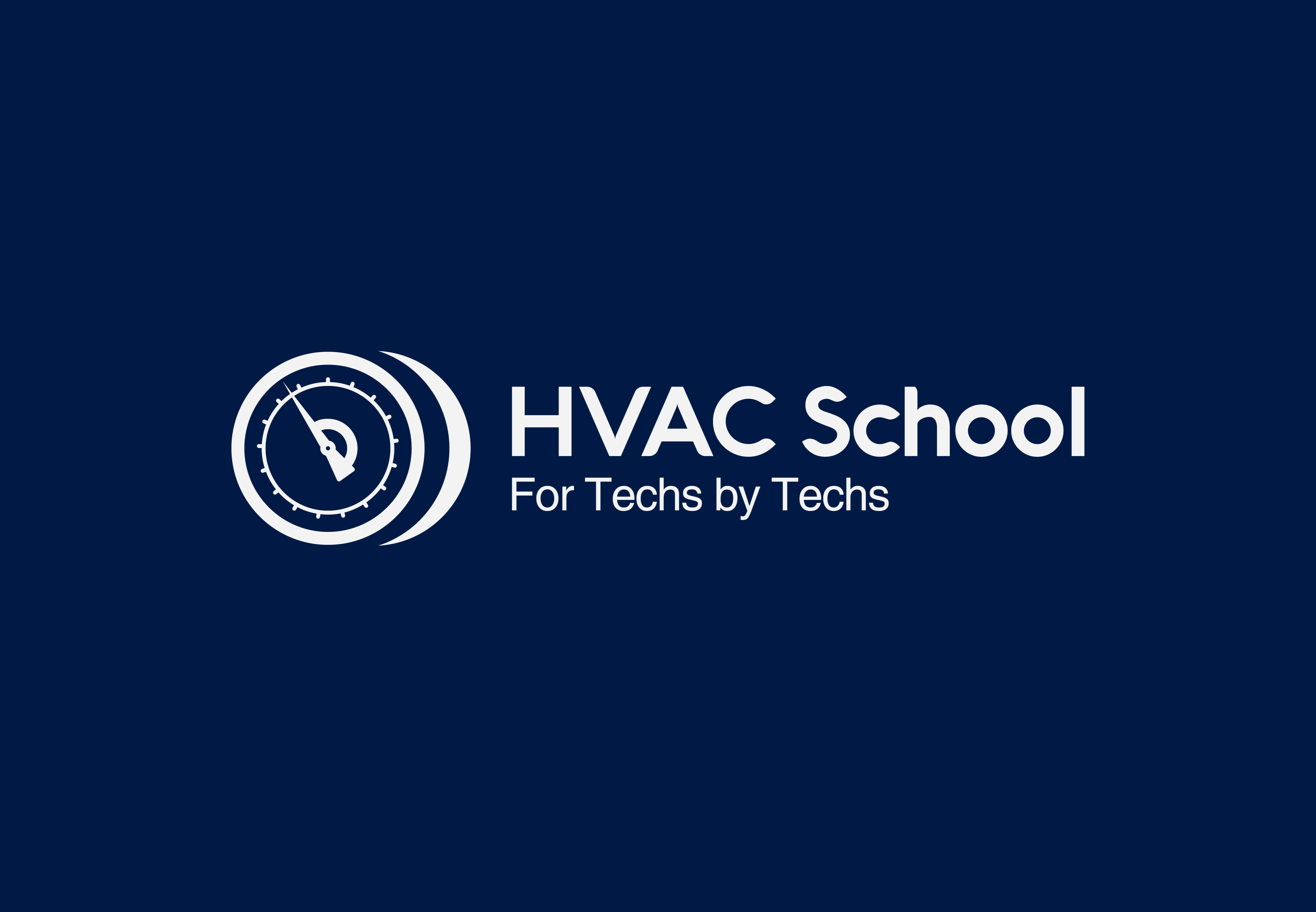
In this two part interview Moe Hirsch goes deep an wide on buffer tanks and strategies for “parking” btus in hydronic systems
Read more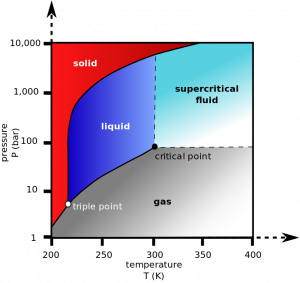
Illustration Courtesy of Emerson CO2 is a pretty nice refrigerant. It has zero ODP (ozone depletion potential) and a GWP (global warming potential) of 1. CO2 has been used as a refrigerant almost from the very beginning of refrigerants, and it's been making a big comeback in market refrigeration (especially in colder climates). CO2 […]
Read more