May 2019
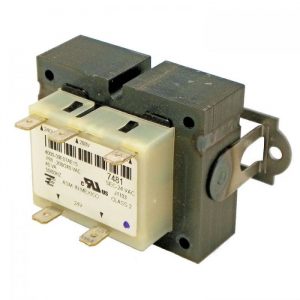
Have you ever seen a low-voltage transformer like the one shown above? It has multiple input (primary) taps for a good reason. It is common to find three-phase and single-phase equipment rated to operate on both 240v and 208v power. That is because three-phase power can either be 208v leg to leg when the building […]
Read more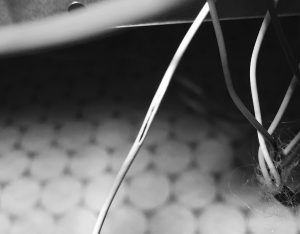
Erich Vinson is a tech from Colorado and one of the most entertaining people I interact with online. He wrote this quick tech tip on stripping back the outer jacket properly on control wires, and it happens to also be something I preach. Thanks, Erich. In the first picture (above), you can see what happens […]
Read more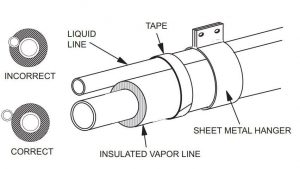
The primary role of setting an appropriate level of subcooling is to ensure that we deliver a full line of liquid refrigerant to the metering device. We want to do this at: A pressure differential required by the metering device At a temperature and pressure no higher than required for maximum capacity and efficiency But […]
Read more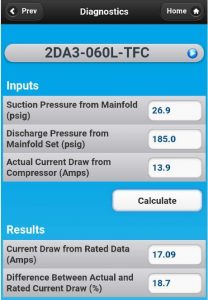
This article is written by a regular contributor, experienced rack refrigeration tech, and RSES CM Jeremy Smith. Thanks, Jeremy. Also, there is a podcast out about what kills compressors HERE. A technique that you can use to diagnose compressor problems and help differentiate them from other possible issues is compressor performance analysis. Manufacturers do extensive […]
Read more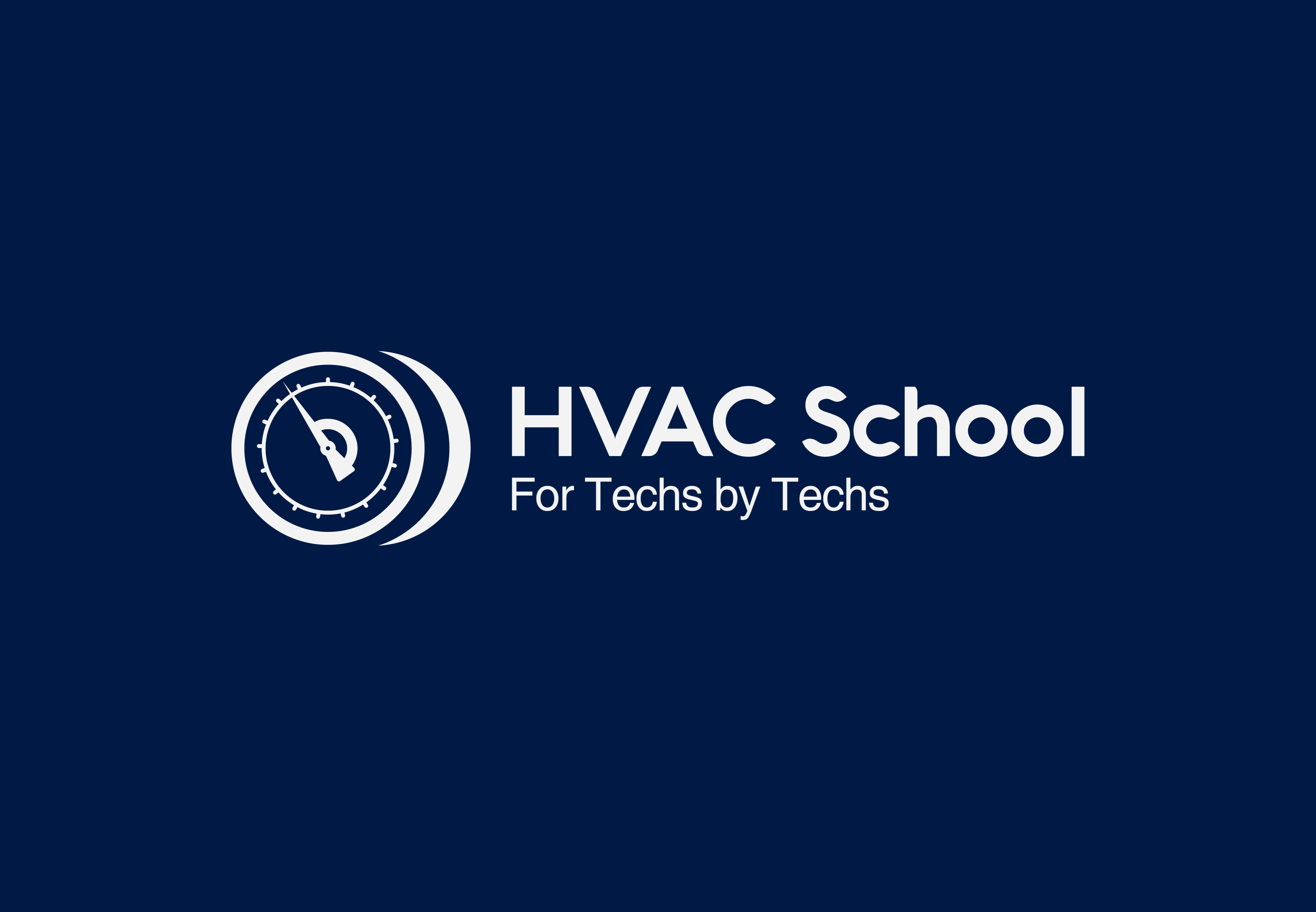
Colleen Keyworth from Women in HVAC/R joins us to talk about the importance of getting women excited about our trade.
Read more
A good leak detector is a big investment and one of the more important tools a tech has on the truck. I've had the same leak detector for years, and I've replaced everything on it, from sensors to pumps to the probe. And no, the one shown above isn't mine. One thing that I have […]
Read more