February 2020
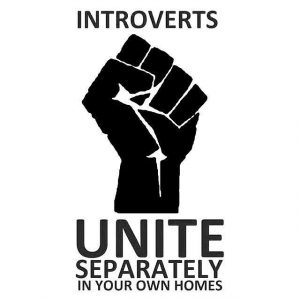
When you think of a salesman, what comes to mind? Do you imagine a quiet person who helps you solve your problems by listening and evaluating you as a customer? Probably not. When most people hear the word ‘salesman,' they imagine a flashy personality who will talk to you for hours to try to get […]
Read more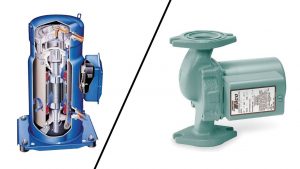
Let's go with dictionary definitions of each one first. pump noun 1. A mechanical device using suction or pressure to raise or move liquids, compress gases, or force air into inflatable objects such as tires. compressor noun 1. an instrument or device for compressing something. Both compressors and pumps move fluids, and a fluid: Yields or […]
Read more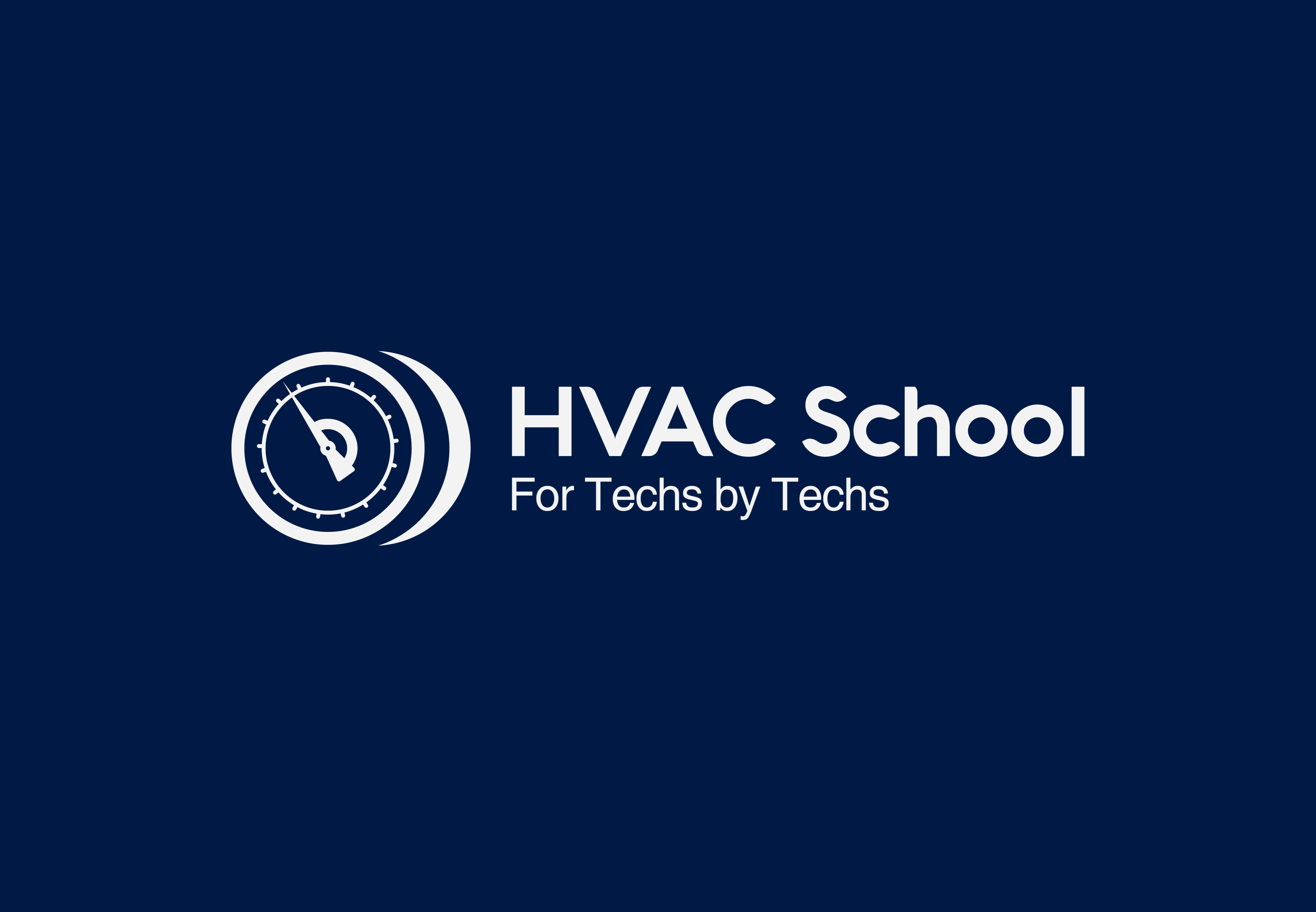
Rick from Certified Refrigerant Services joins us to talk recovery and refrigerant management and what to look for and do to get the most from your program
Read more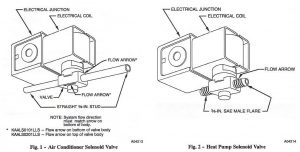
Pump down solenoid valves are commonplace for any refrigeration technician. They are energized with the compressor still running, shutting off flow in the liquid line so that the refrigerant is pumped into the condenser and receiver. The compressor will then shut off once a low-pressure switch opens the circuit when the pressure falls below a […]
Read more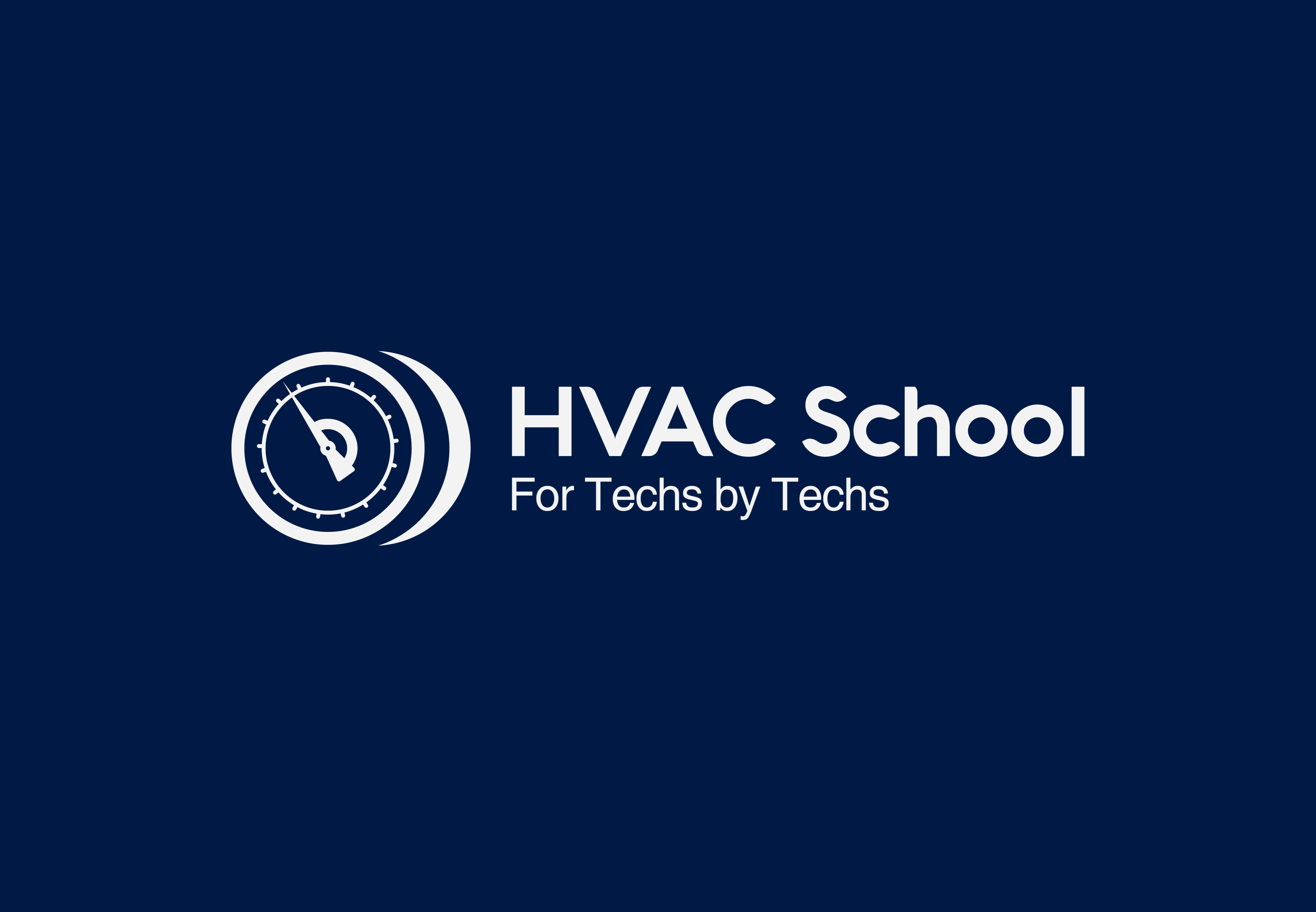
Chris LaPietra, vice president and general manager, Honeywell Stationary Refrigerants joins us to talk some new releases from Honeywell and refrigerants in general
Read more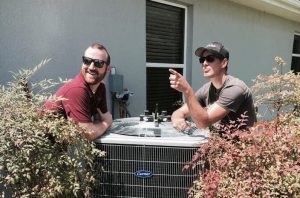
When you walk up to a piece of equipment, you want to follow a process to ensure that you accomplish five things: #1 – You diagnose the fault correctly. #2 – If possible, you find the “why” of the failure. #3 – Find any other problems or potential problems with the system that can cause […]
Read more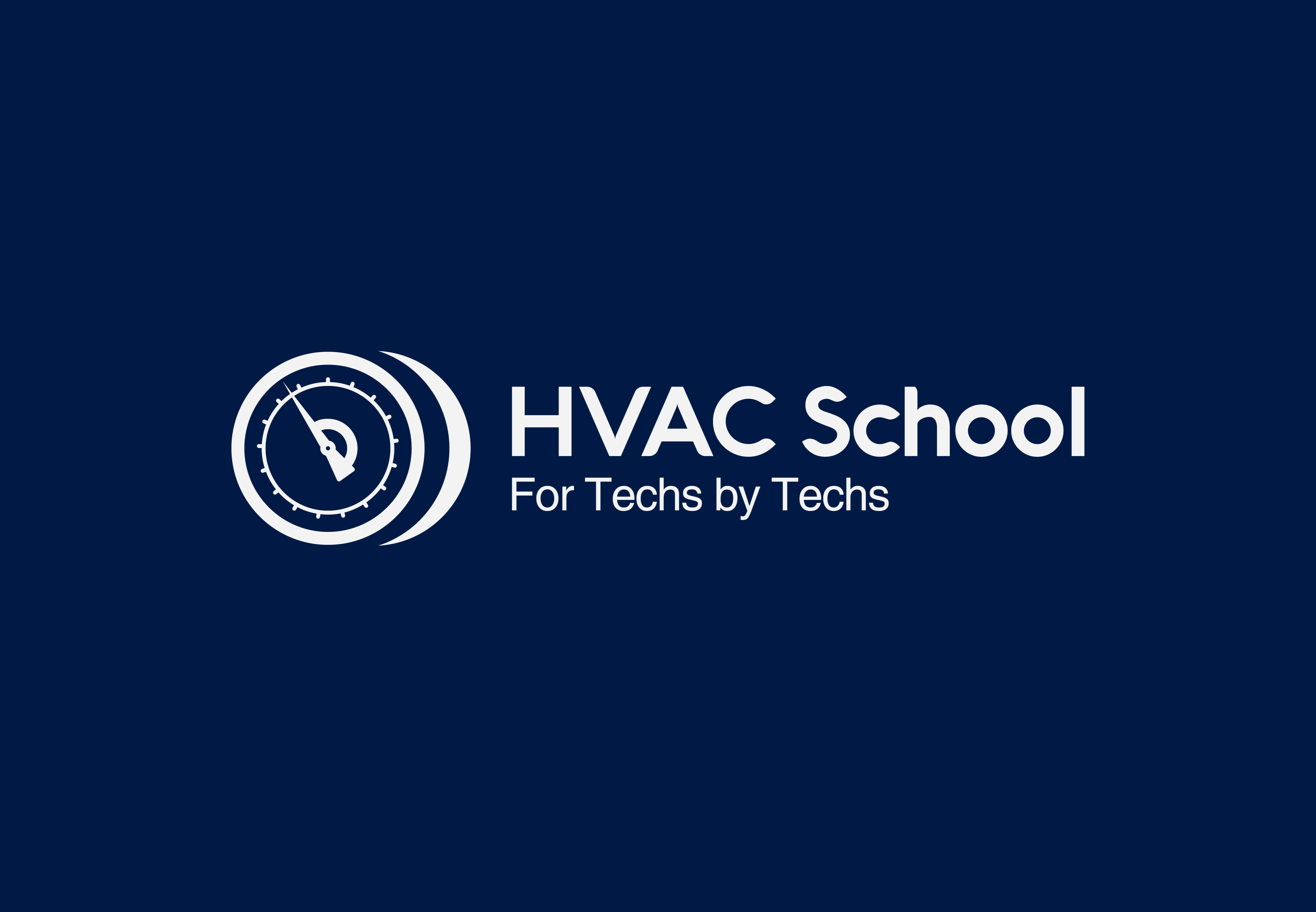
Eric Kaiser joins me live to talk through some commonly repeated EPA myths and how to get the most from your recovery machine and tanks
Read more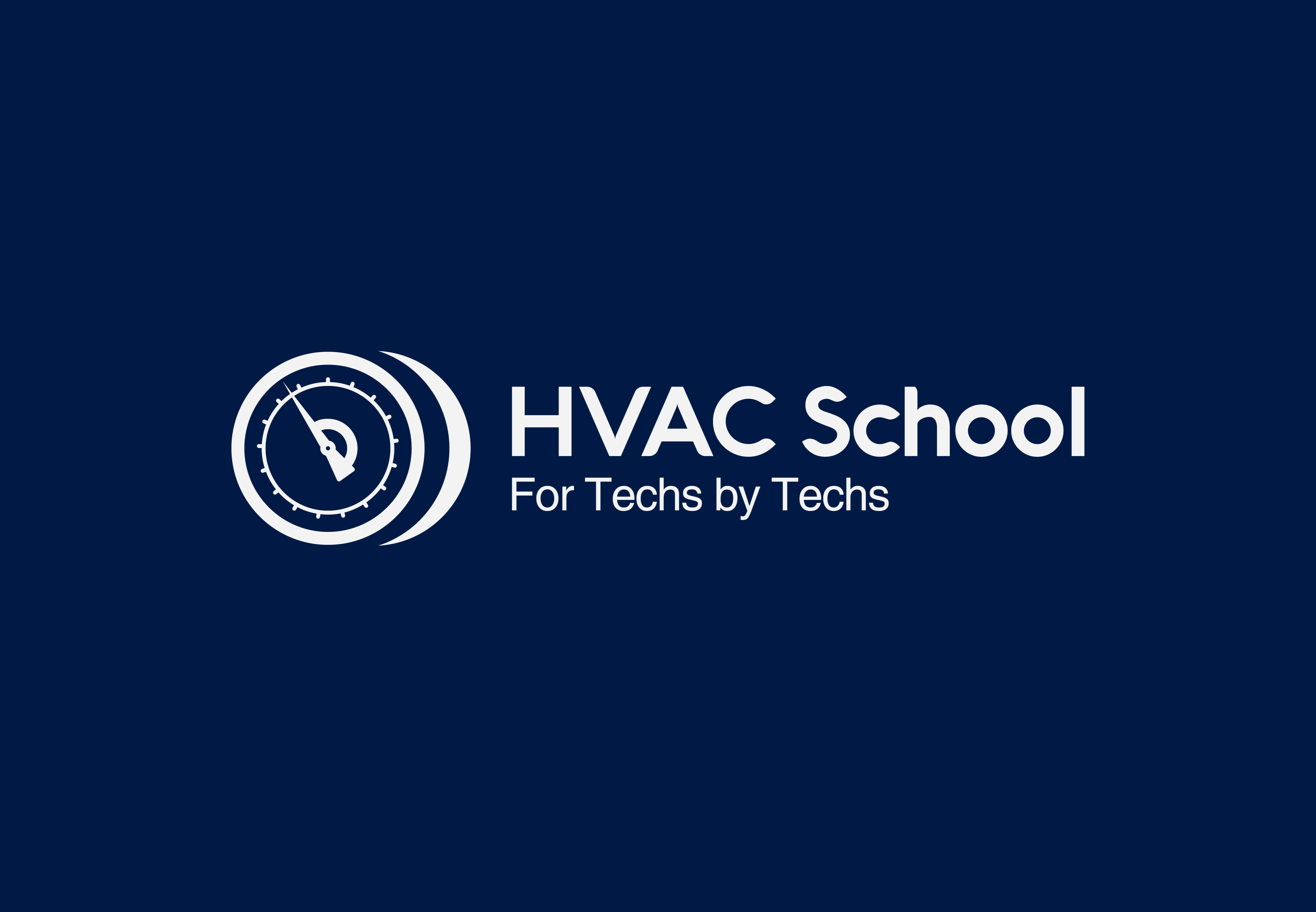
Gurminder Sidhu joins us from NATE to talk about what NATE is all about and some of the new changes and improvements
Read more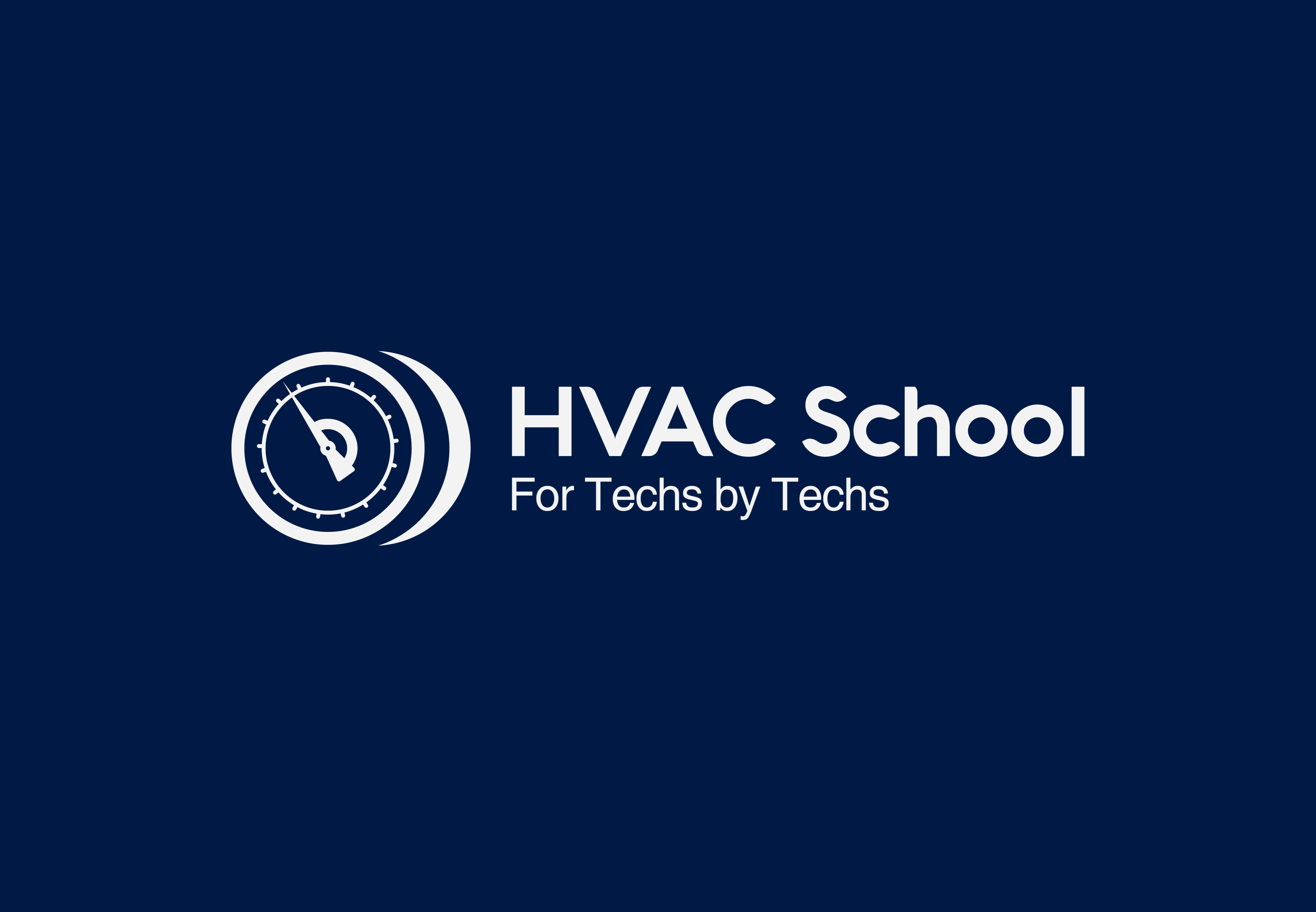
Alex Meaney from Mitek/Wrightsoft joins us to talk about some HVAC design myths and how to bust them in your mind. Fun talk from a great guy.
Read more