July 2020
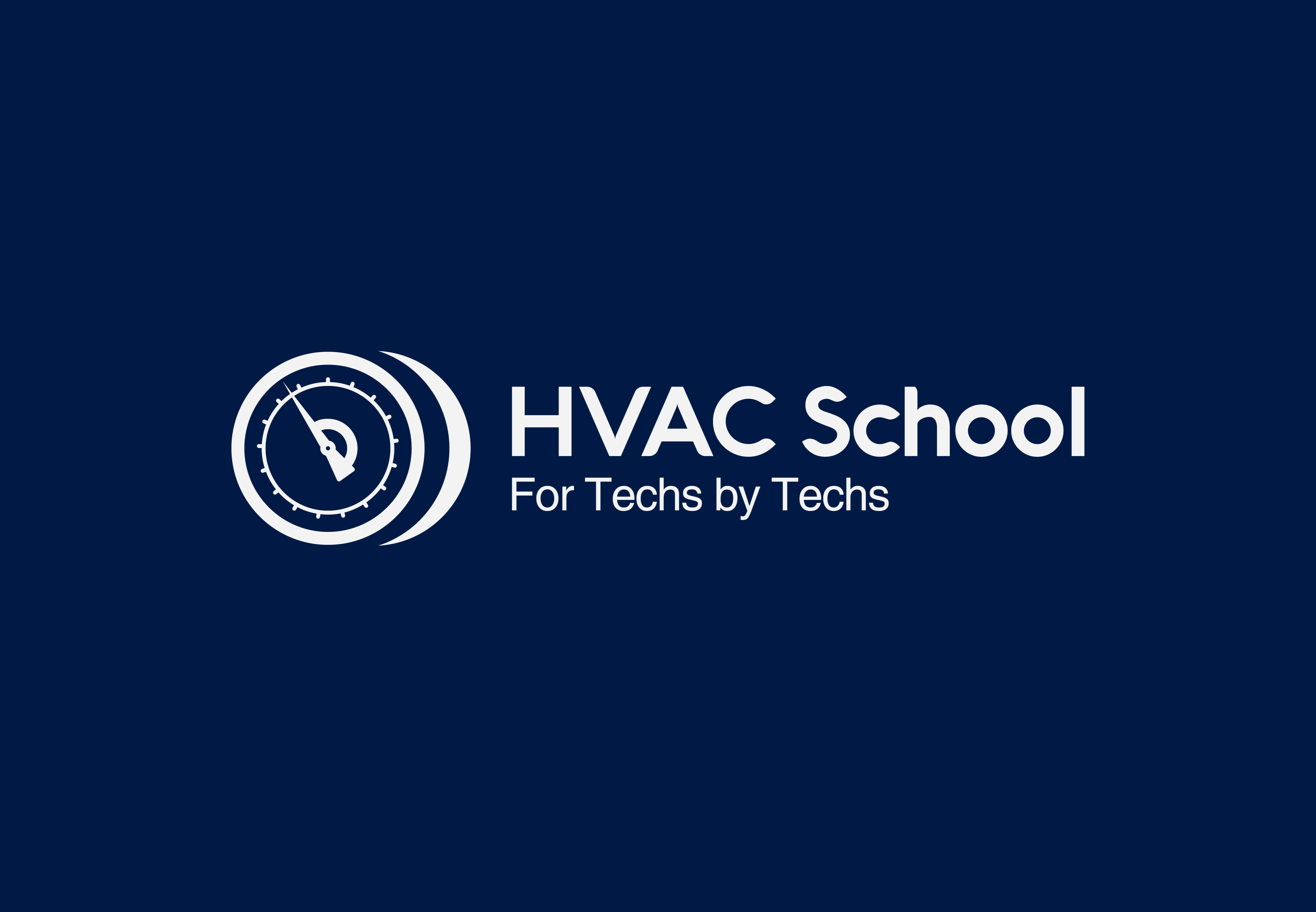
Our Main man Bill Spohn joins us again to talk specifically about combustion and how to select and properly utilize an analyzer
Read more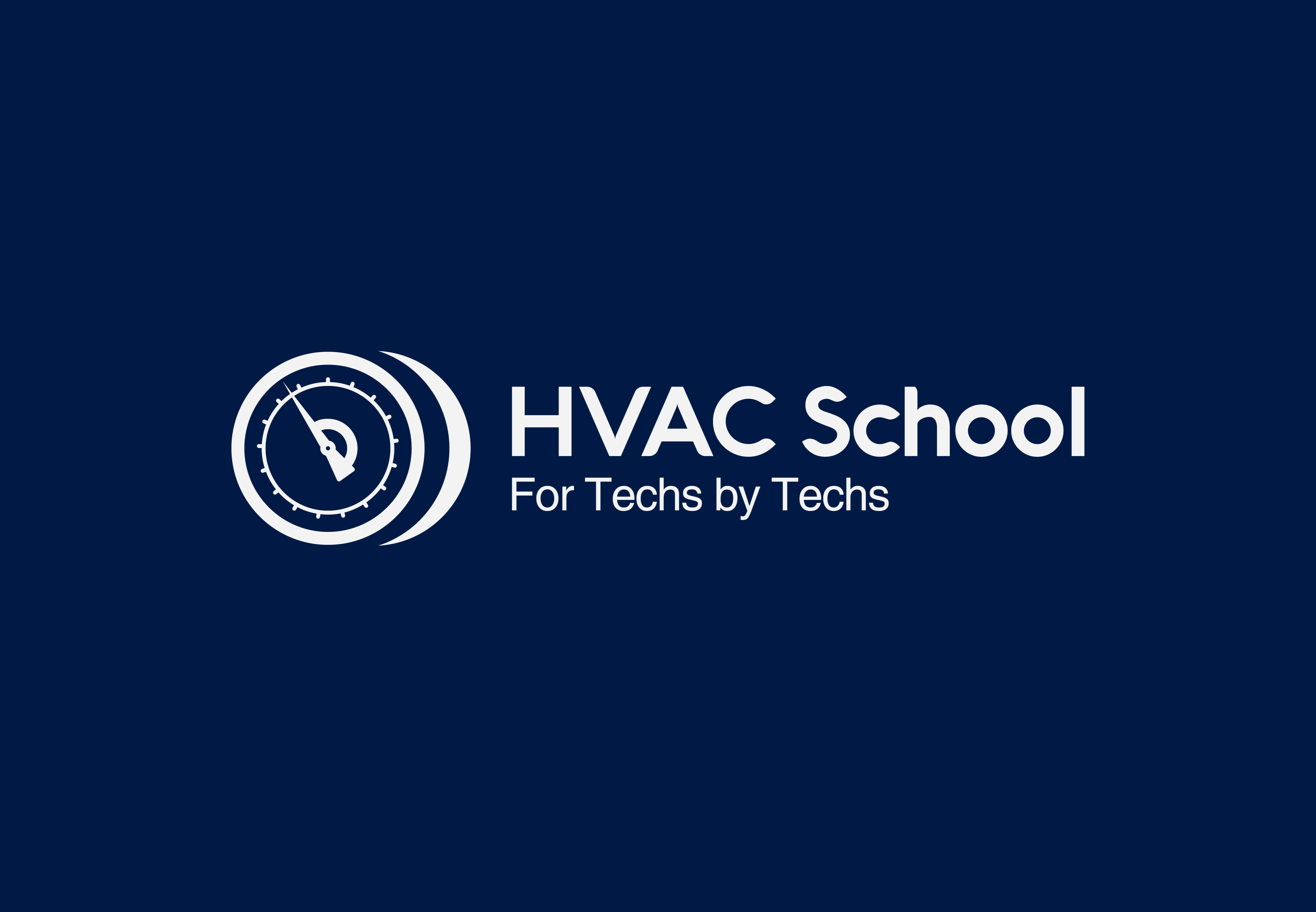
Jaden Lane joins us to discuss some best practices when using hoods and how the Dwyer Smart is innovating in the hood space
Read more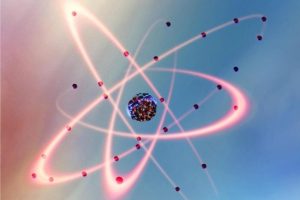
As HVAC/R Technicians, we use tools and instruments to take measurements every day. In fact, 90% of our job could not be done efficiently without some kind of measurement. “How do we measure?” “With what instruments?” “How accurate are these measurements?” These are all questions a thoughtful technician should ask before spending money on a […]
Read more
Image Courtesy of Eaton SNAP ‘N SHIELD Piping support is covered in Section 305 of the IMC (International Mechanical Code). Once again, the IMC isn't binding, but it is what most local codes are based on. Piping / Tubing Material Maximum Horizontal Distance Between Support Maximum Vertical Distance Between Support Copper Tubing 1 1/4″ […]
Read more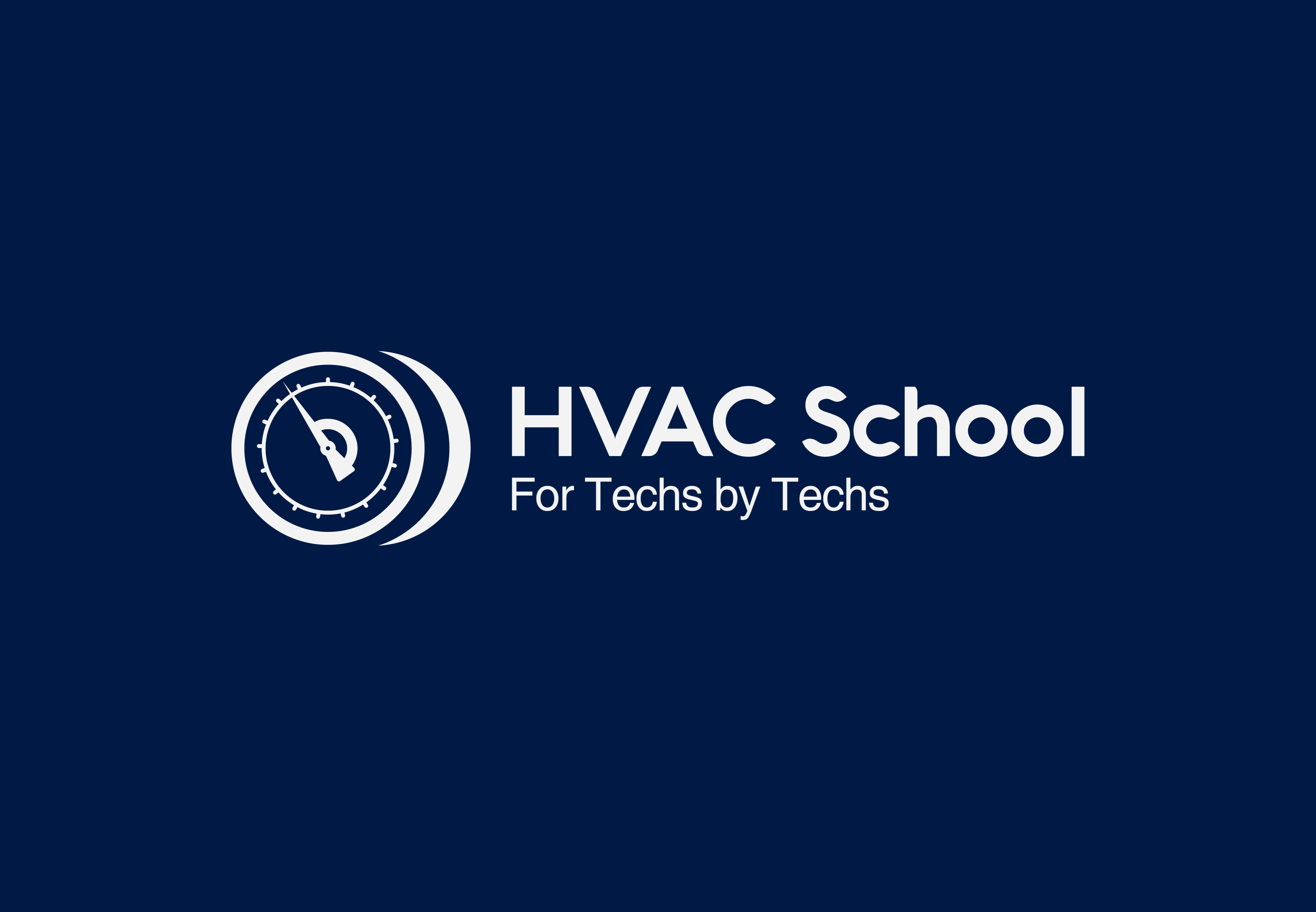
Russ King joins us to discuss simplifying duct design for residential contractors
Read more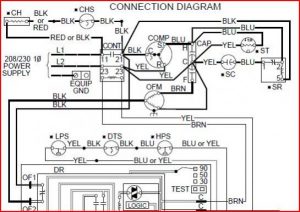
We keep two-pole, 40-amp 24v coil contactors on all of our vans. They are versatile and reliable, and you can replace most residential A/C contactors with them. There are a few things to watch for, though, especially when you have a crankcase heater. Many brands power the crankcase heater constantly and shut it on and […]
Read more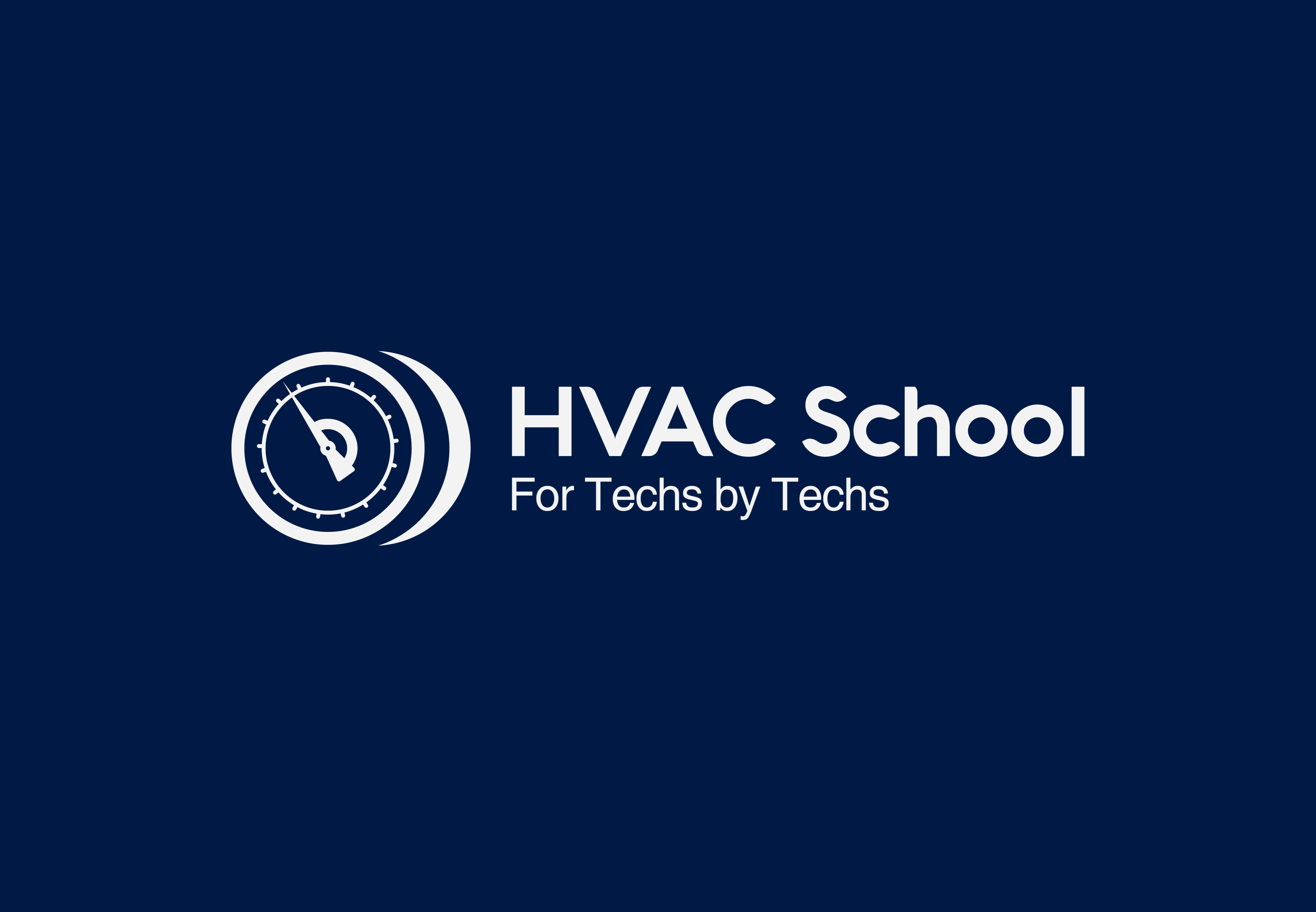
Bill Spohn w/ TruTech joins us to talk about why being “approximately correct” is better than being “exactly wrong” and how that applies to test instruments
Read more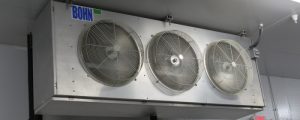
We have discussed DTD (design temperature difference) quite a bit for air conditioning applications, but what about refrigeration? Let's start by defining our terms again. Suction Saturation Temperature The saturation temperature is the temperature at which the refrigerant will be at a given pressure if it is currently changing state. This change of state would […]
Read more