Uncategorized
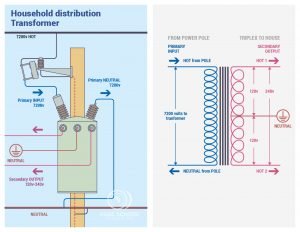
Why is it called single-phase 240 when there are two opposing phases (or legs)? I wondered why we called two 120v opposing legs “single-phase 240” for years. Then someone pointed out to me that a typical “single-phase” pole transformer only has one power leg entering and two coming out. That freaked me out. How can […]
Read more