BACK
Short Cycling
HVAC/R in 2024 & Beyond
4-20ma Control Basics
W1, W2, & E
Modulation Motors
The Good Old Heat Anticipator
Commercial Contactor Considerations
Chillers for the Chillerphobic – Podcast
#controls
Tech Tips:

A friend of mine was telling me that a utility had the idea that they could reduce energy consumption by turning HVAC equipment on and off rapidly during times of high load. In their minds, wouldn't it be better to spread out the off time rather than keeping the system off for longer periods and […]
Read more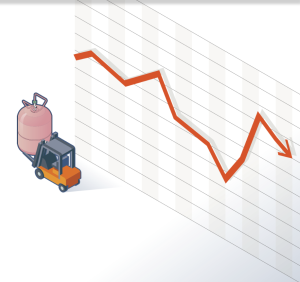
2023 was a big year for HVAC between the EPA’s final rule about the installation of R-410A split systems and the rise of artificial intelligence (AI) in seemingly all aspects of life. With an ever-changing regulatory landscape, 2024 is bound to bring even more changes. This tech tip will recap the changes we’ve seen in […]
Read more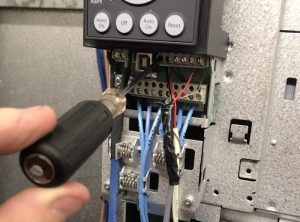
Back in the “good old days,” controls were all analog and mechanical; that simply means they acted in a directly connected and variable manner based on a change in force. Both pneumatic (air pressure) and hydraulic (fluid pressure) systems are examples of mechanical or analog controls. When the pressure increases or decreases on a particular […]
Read more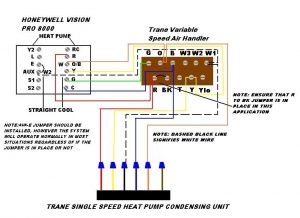
I got this question via email (edited slightly for length): Some things I've done because I've been taught to do them yet I don't know why I do them. One of those things is putting a jumper between w1/e and w2. Sometimes, in the case of a Goodman for example, I've been taught to combine […]
Read more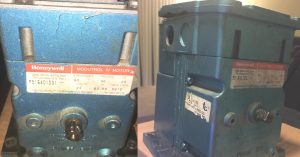
Modulation motors are not often seen in residential equipment, but we see them a lot in commercial and industrial applications on many different types of equipment. I see them primarily on larger burners to control the fuel firing rate, but they also control water flow through heating coils, the water level on cooling towers, and […]
Read more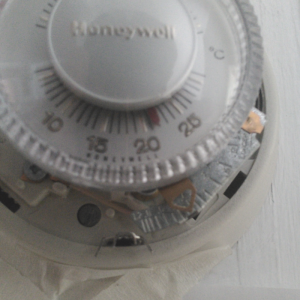
As a technician, you most likely know some customers who still have an oldie thermostat (you know, those old mercury bulb things, like the round Honeywell CT87 and such). Keep in mind that those usually have an adjustable heat anticipator. If you’re newer in the field, you may not have seen or worked with those […]
Read more
This tip was created by Jason Pinzak and originally posted on the HVAC Technician's Facebook group. It is reposted here with permission from Jason. Thanks! Contactors are useful in commercial and industrial applications, particularly for controlling large lighting loads and motors. One of their hallmarks is reliability. However, like any other device, they are not […]
Read moreVideos:
Podcasts:
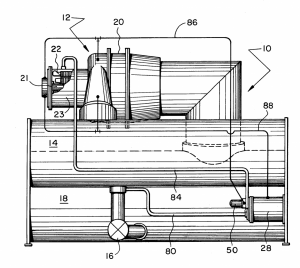
In this episode, we talk with Jeff Nieman about chillers and how they work. For those of you who primarily work in residential or light commercial HVAC, chillers may be unfamiliar at best and terrifying at worst. However, centrifugal chillers' parts are actually quite similar to those of HVAC units. They have an evaporator, […]
Read more