BACK
Work Vehicle Entropy
Wet Bulb and Enthalpy – The Left Side of the Chart
Why Compression Ratio Matters
Where Do I Measure Delta T?
Adiabatic Cooling, Blower Settings, and Why You Care
What is Enthalpy?
Pressure / Enthalpy Diagram Example
A Bit of Adiabatic Air Science For Techs – FB Live Video
Psychrometrics Without Tears
#enthalpy
Tech Tips:
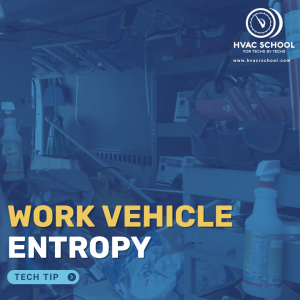
Have you ever noticed that the more you're required to speed up to get all your work done in a day, the more the cleanliness of your work vehicle suffers? Some techs won't clean their vans, no matter how slow or busy the schedule gets, but most of us prefer a clean and organized vehicle. […]
Read more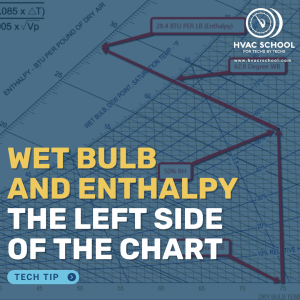
It's incredibly useful to understand wet-bulb temperature and air enthalpy when calculating actual system capacity and human comfort. Dry-bulb temperature is a reading of the average molecular velocity of dry air. However, it does not account for the actual heat content of the air or the evaporative cooling effect of the air. When air is […]
Read more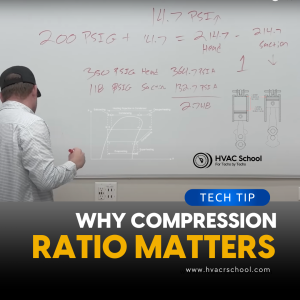
In HVAC/R, we are in the business of moving BTUs of heat, and we move BTUs via pounds of refrigerant. The more pounds we move, the more BTUs we move. In a single-stage HVAC/R compressor, the compression chamber maintains the same volume no matter the compression ratio. The thing that changes is the number of […]
Read more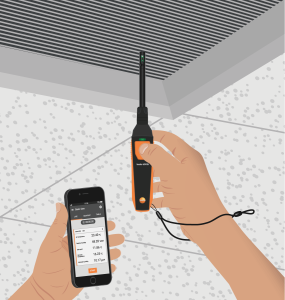
Over time, I’ve seen people use just about every type of temperature-measuring device in just about every location imaginable. From drilling tiny holes into rooftop unit panels to sticking a K-type wire into a piece of flex duct (I don’t remember why), I’ve done it all. Coming up through the trade, I’ve been TOLD to […]
Read more
Just so you don't get bored and quit reading, let's get straight to the point. When the blower runs for more than a few minutes after the system has cycled off in cool mode, the air may continue to be “cooler” (lower sensible temperature) coming out of the supply. However, the heat content of the […]
Read more
Enthalpy is easy. It's just a state function that depends only on the prevailing equilibrium state identified by the system's internal energy, pressure, and volume. It is an extensive quantity. Simple. Like most things, the scientific definition is as clear as mud. In HVAC/R, we use enthalpy measurement to come up with the total heat […]
Read more
This article was written by my buddy and Canadian Supertech Tim Tanguay. Thanks, Tim! This P/E chart shows R410a at 100°F saturated condensing temp, 10°F SC, 40°F saturated suction temp, 20°F SH at the compressor. The green highlighted thumb shape is the saturation zone. Everything that occurs in the saturation zone is a latent (change […]
Read more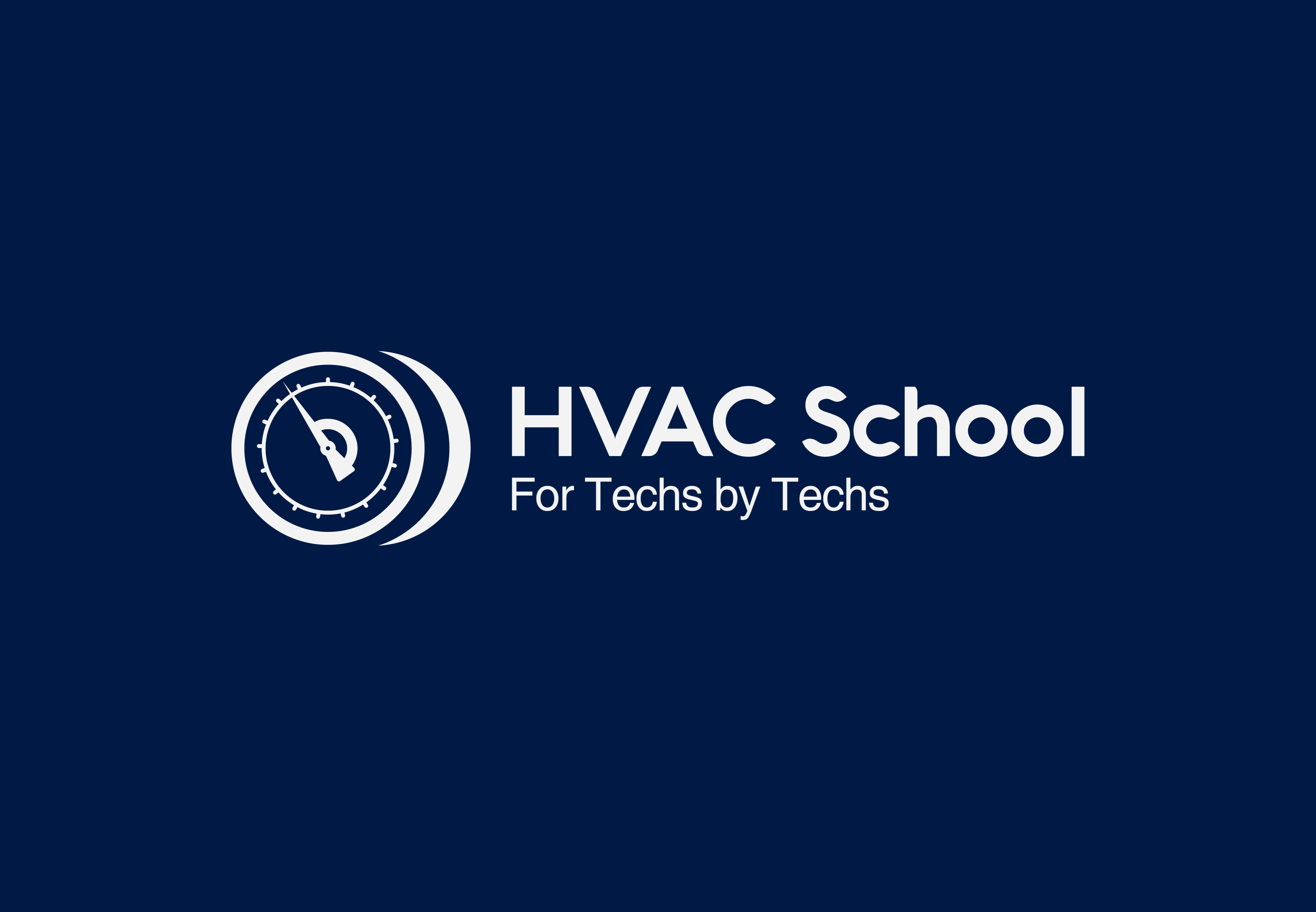
In this video Bryan talks about Heat (Enthalpy) Adiabatic cooling Latent and Sensible heat Evaporative Cooling Humidity Blower Off Delay
Read moreEvents:
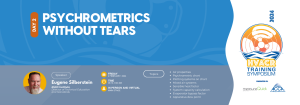
NOTE: If you cannot view the recording, the video may still be processing. The maximum wait time is 24 hours. We apologize for the delay and appreciate your patience.
Read more