BACK
Does Voltage or Amperage Kill You?
Tool Selection: Electrical Meters
Three-Phase Voltage Imbalance
Switch Voltage
Beware of “Ghost” Voltage
Does a Motor Draw More or Less at lower Voltage?
Multimeter Categories
Testing Run Capacitors the Smart (and Easy) Way
When 0V Isn’t Safe – Short #242
Deploying Surge Protection & Voltage Monitoring w/ DITEK
Preventing Low Voltage Issues
#voltage
Tech Tips:
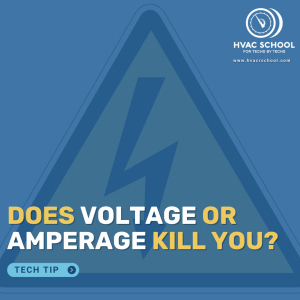
I hear the following phrase a lot: It's the amperage that kills you, not the voltage. While there is truth to the statement, it is sort of like saying, “It's the size of the vehicle, not the speed that kills you when it hits you.” OK, so that's a pretty bad example, but hopefully, it […]
Read more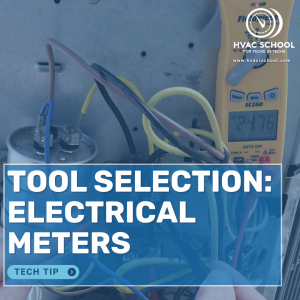
I'd like to give a special thanks to Tony Gonzalez from Fieldpiece for providing technical guidance about the SC680's power measurement capabilities, as well as VAC and AAC measurements on ECMs. We’ve talked through specifications, applications, and features for a few tools, but none of them have been quite as hardcore as electrical meters. Like […]
Read more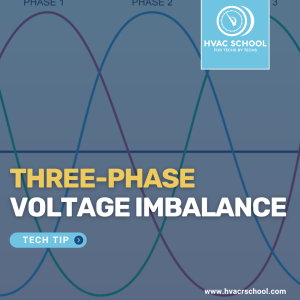
When reading ANY article about electrical theory or application, keep in mind that it will only scratch the topic's surface. You can dedicate years of your life to understanding electrical theory and design the way many engineers do and still know just enough to be dangerous. In HVAC, we rarely need to have a DEEP […]
Read more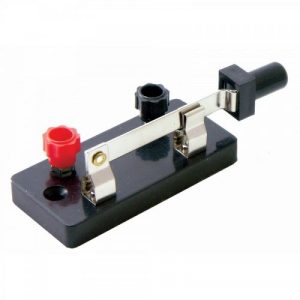
On an energized, intact circuit, you will read voltage across an OPEN switch when testing with a voltmeter. However, you probably won't read significant voltage across a CLOSED switch. Both sides of a closed switch are electrically identical (or at least very close). Therefore, there should be no movement of electrons between the leads of […]
Read more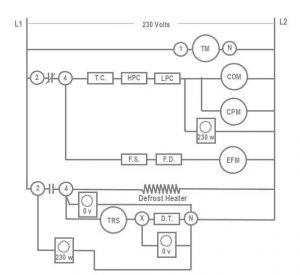
Disclaimer: “Ghost voltage” is a term used by techs to explain a phenomenon where they measure voltage they don't expect or when the voltage they see doesn't do the work they expect. More advanced techs know how to use the Lo-Z (low impedance) mode on their voltmeter if it has one to help eliminate this. […]
Read more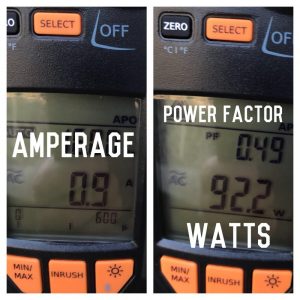
Have you ever noticed that a blower motor rated for 120V draws about twice the amperage of the same horsepower motor rated at 240V? That is because motors are rated in watts or horsepower, and according to Watt's law, Watts = Volts x Amps. To keep the wattage output the same at 120V, it draws […]
Read more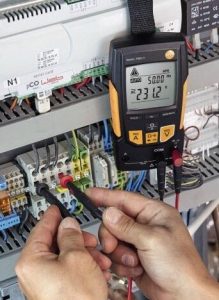
Testo 760 Category IV Multimeter I was standing at a booth at the HVAC Excellence Educators conference, and an instructor walks up, grabs a meter, and asks me, “What's the difference between a category 3 and a category 4 meter?” Well, I really wasn't sure, but I knew that the category 4 meter is rated […]
Read more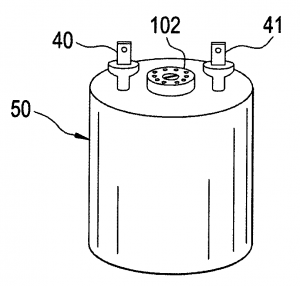
When testing a run capacitor, many techs pull the leads off and use the capacitance setting on their meter to test the capacitor. On a system that is not running, there isn't anything wrong with this test. However, when you are CONSTANTLY checking capacitors as a matter of regular testing and maintenance, that extra step […]
Read morePodcasts:
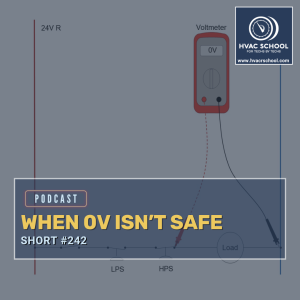
In this short podcast episode, Bryan covers some unique electrical cases: when 0v isn't safe. When you measure voltage, you're finding out the electrical potential between two points. Just because there is 0v between one point and another doesn't mean there will be 0v between those points and other points. Non-contact voltage detectors are […]
Read more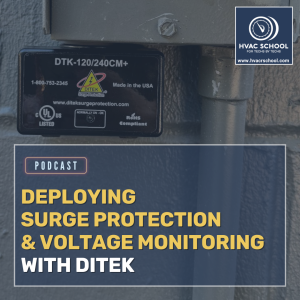
Bryan discusses surge protection devices (SPDs) with Mike from DITEK, focusing on practical applications for HVAC contractors and how to provide value to clients. Mike emphasizes that surge protection is essential for modern HVAC systems, particularly given that they are typically the most expensive appliance in a home and increasingly rely on sophisticated electronic […]
Read more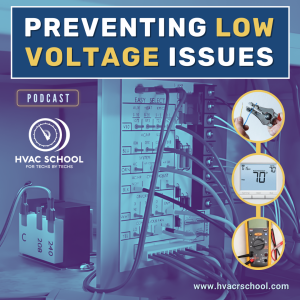
In this episode, Bryan and Bert dive deep into the world of low voltage wiring in HVAC systems. They discuss common mistakes, best practices, and troubleshooting techniques that technicians and contractors should be aware of when dealing with control wiring. The conversation begins with a focus on mechanical issues, such as running wires in places […]
Read more