November 2017
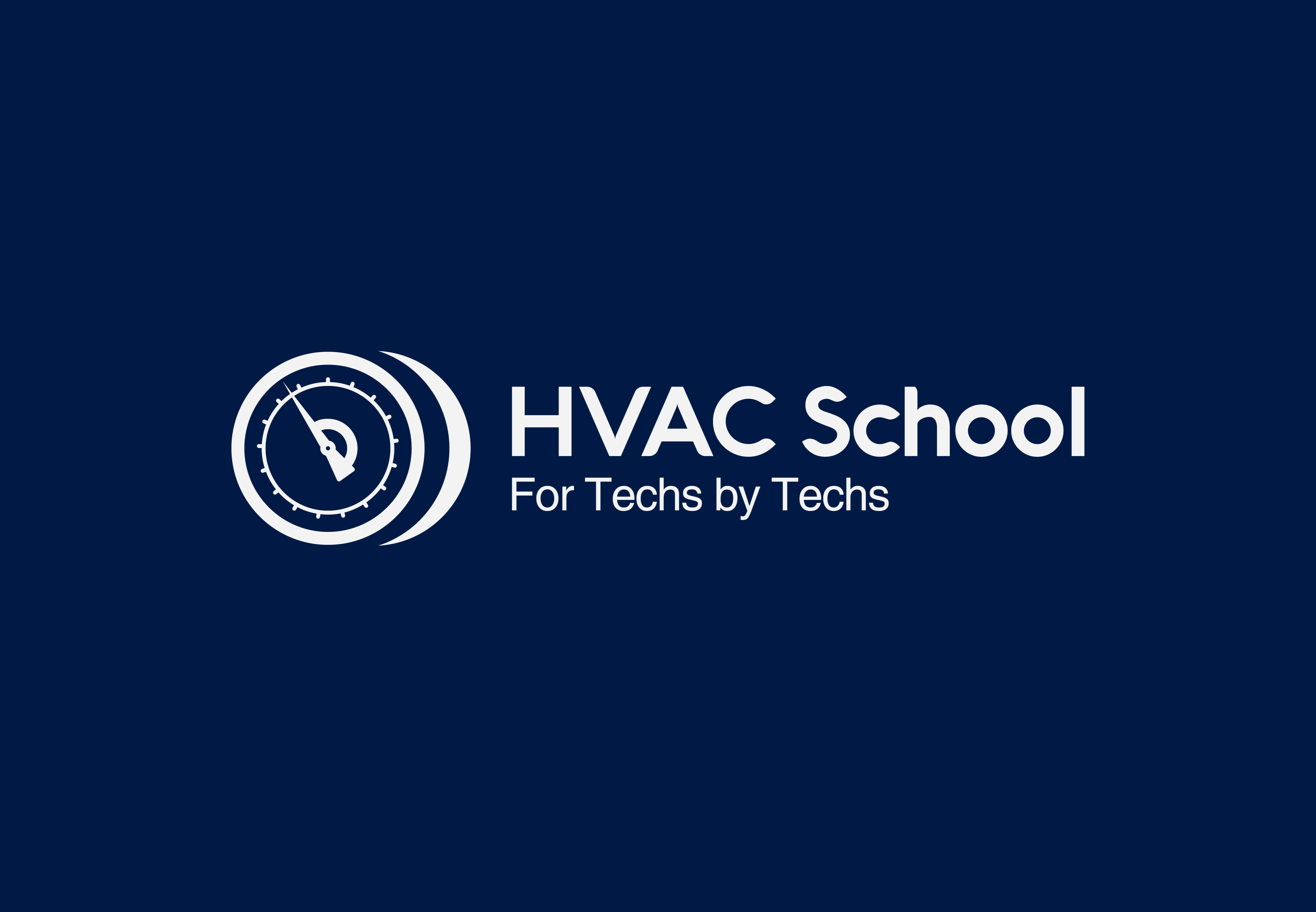
Jamie Kitchen from Danfoss talks all about variable speed motor technology. Why it exists, what it does and how to think differently about the future of HVAC/R
Read more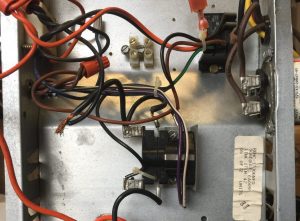
We've seen it before. A tech diagnoses a failed blower relay or board. They leave the blower jumped out by putting a terminal multiplier on the common terminal of the relay/board and connecting the fan speed tap right to power. There can be an issue with that. Some electric heat fan coils have a heat/blower […]
Read more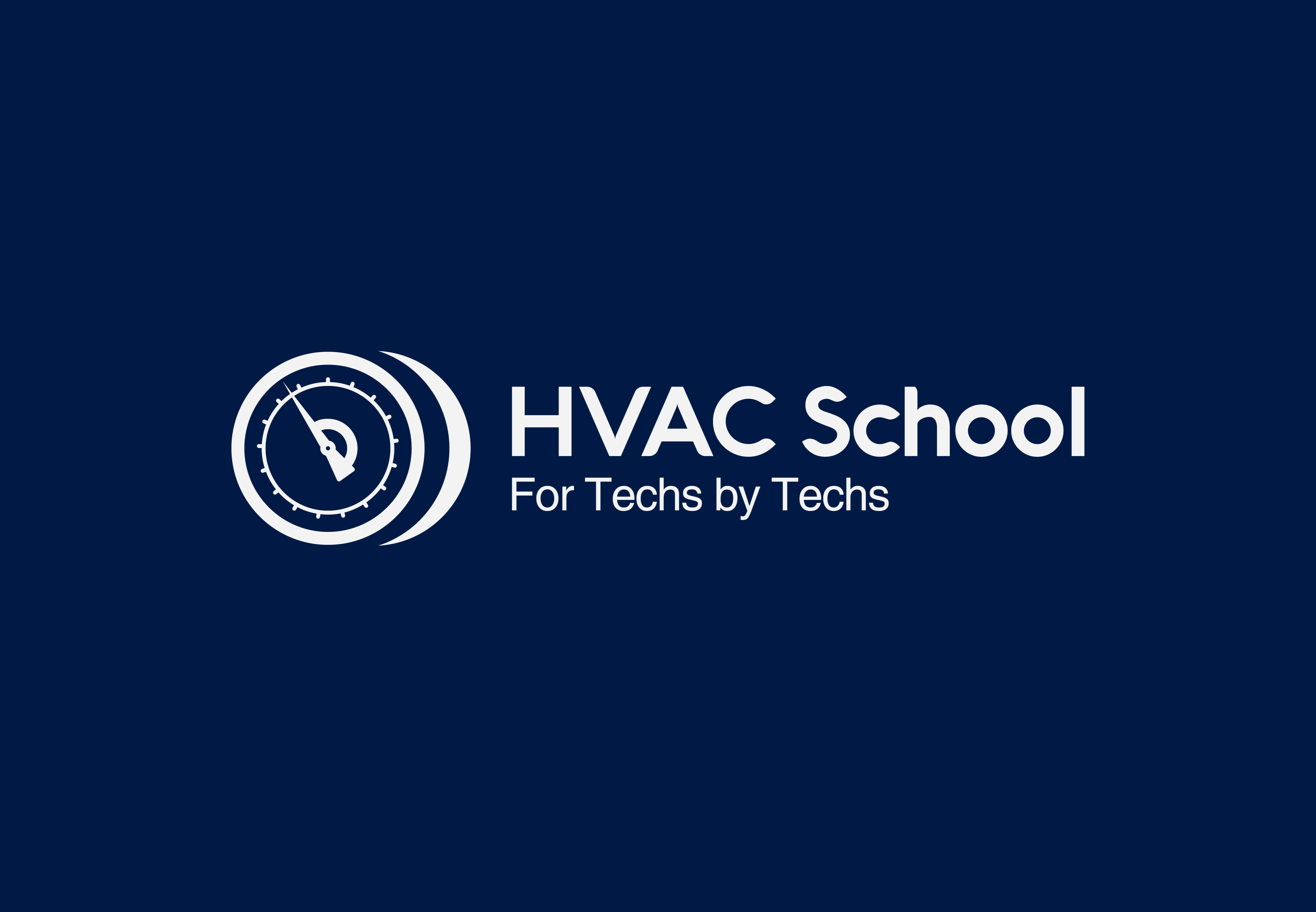
this is the second episode with Jack Rise. Jack is one of my favorite authors and educators in HVAC and you will enjoy his tips in this podcast.
Read more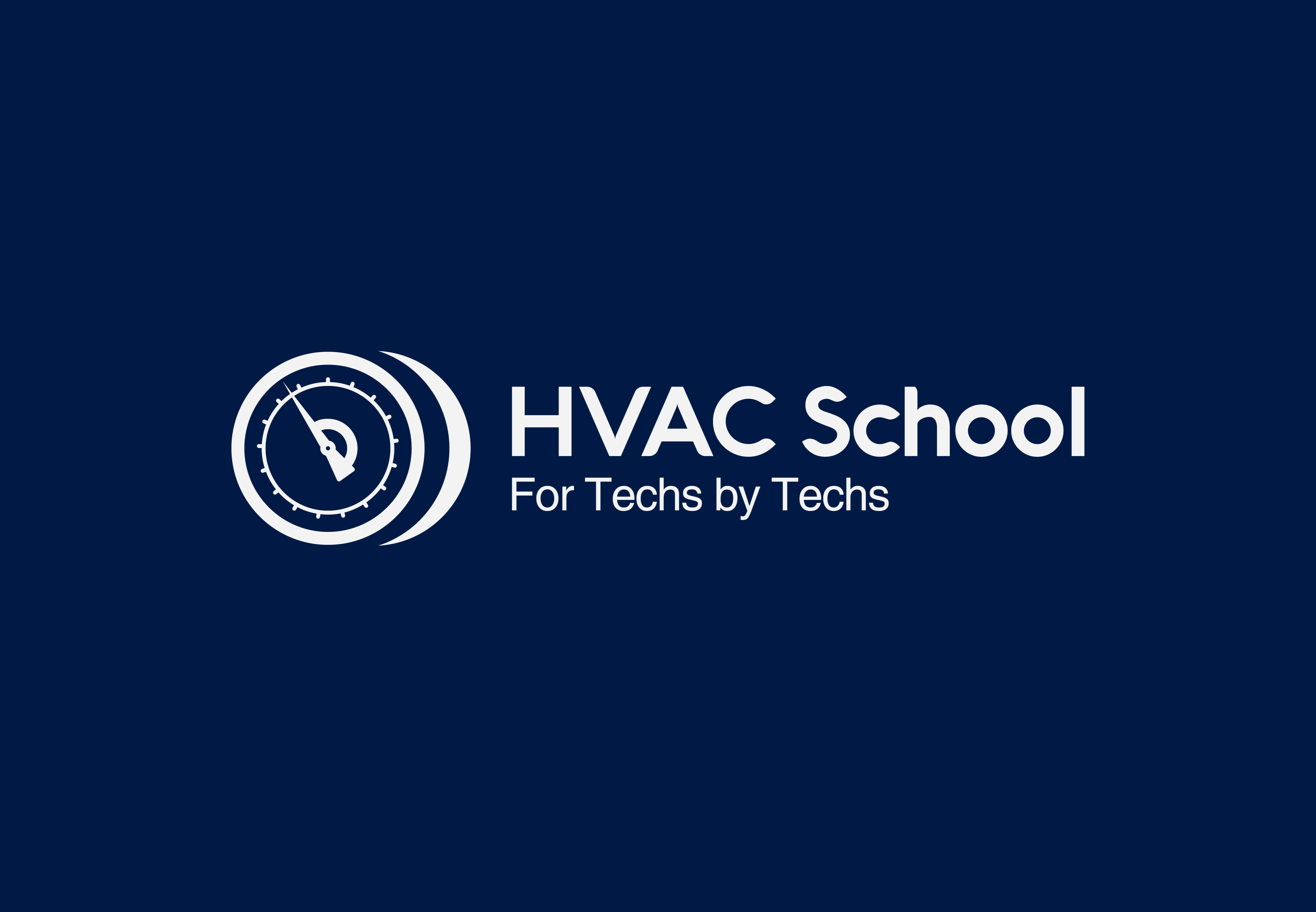
Nate Adams loves to eliminate gas meters and install high-performance heat pumps on high-performance homes in Ohio. Learn his secrets and whether or not he is as crazy as it sounds.
Read more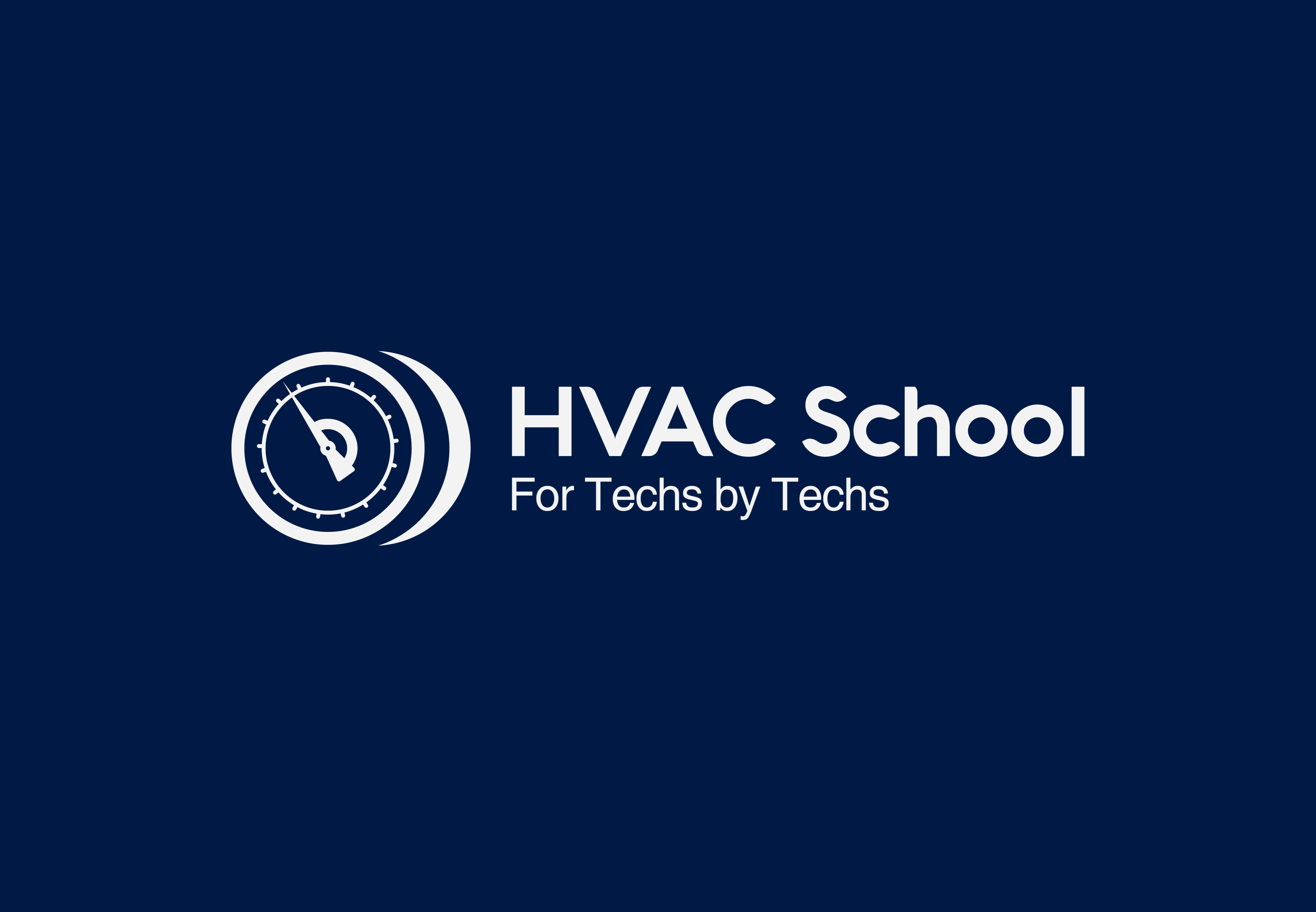
Bill Johnson is one of the great educators and writers of our time in HVAC/R and he shares about his career and some of his top tips on keeping systems leak free.
Read more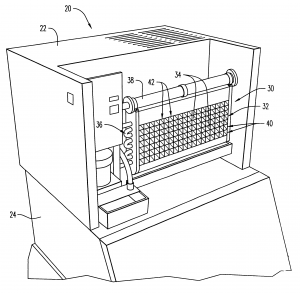
There are several types of ice machines, but in this article, we will focus on cuber style and flaker or nugget style. Both types produce ice, but the process of freezing and harvesting is a little different. The application in which the ice will be used will determine what style of machine is needed. I […]
Read more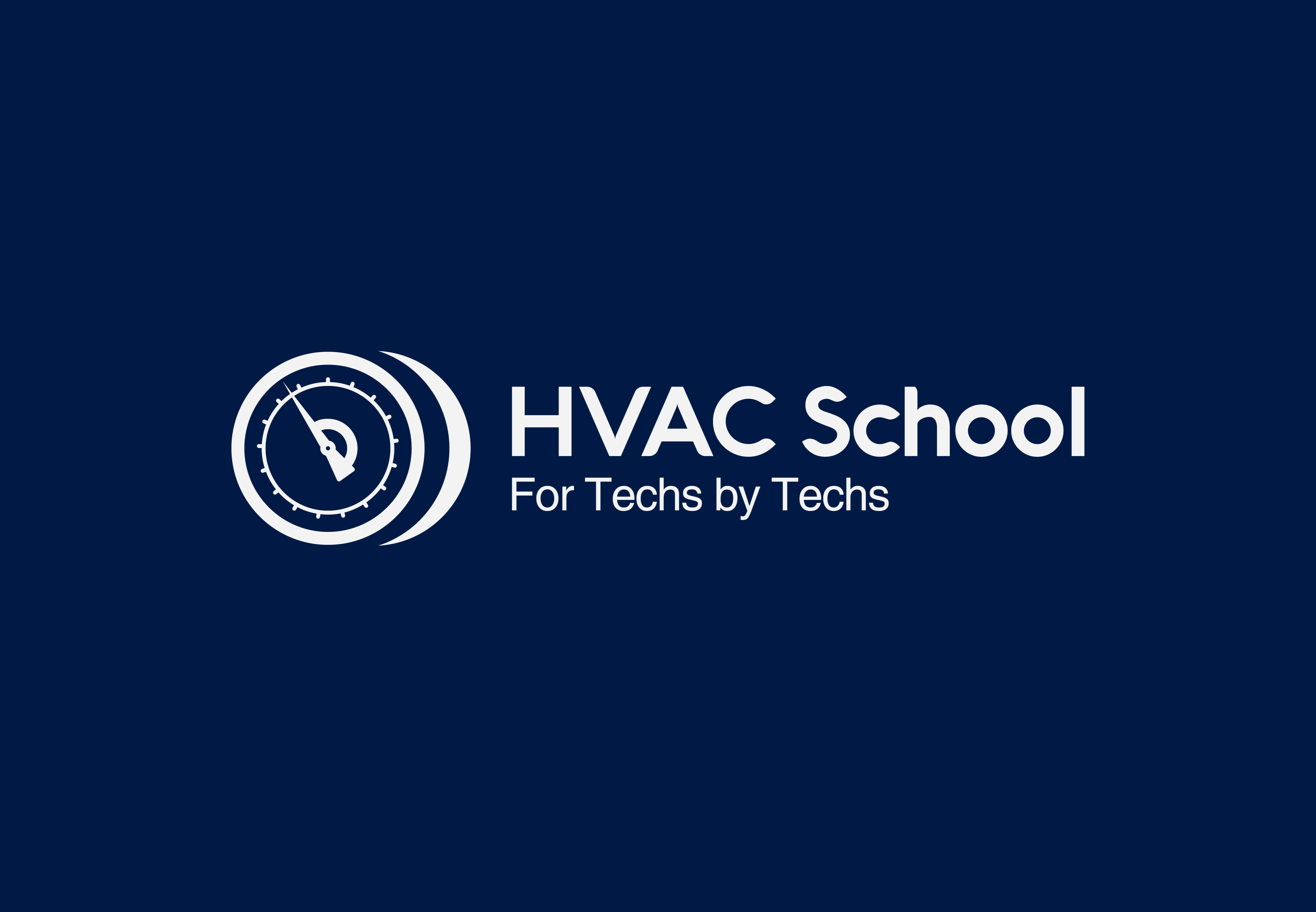
Jim takes us all the way through the history of furnaces from the stone ages when he was a child all the way to modern modulating condensing furnaces.
Read more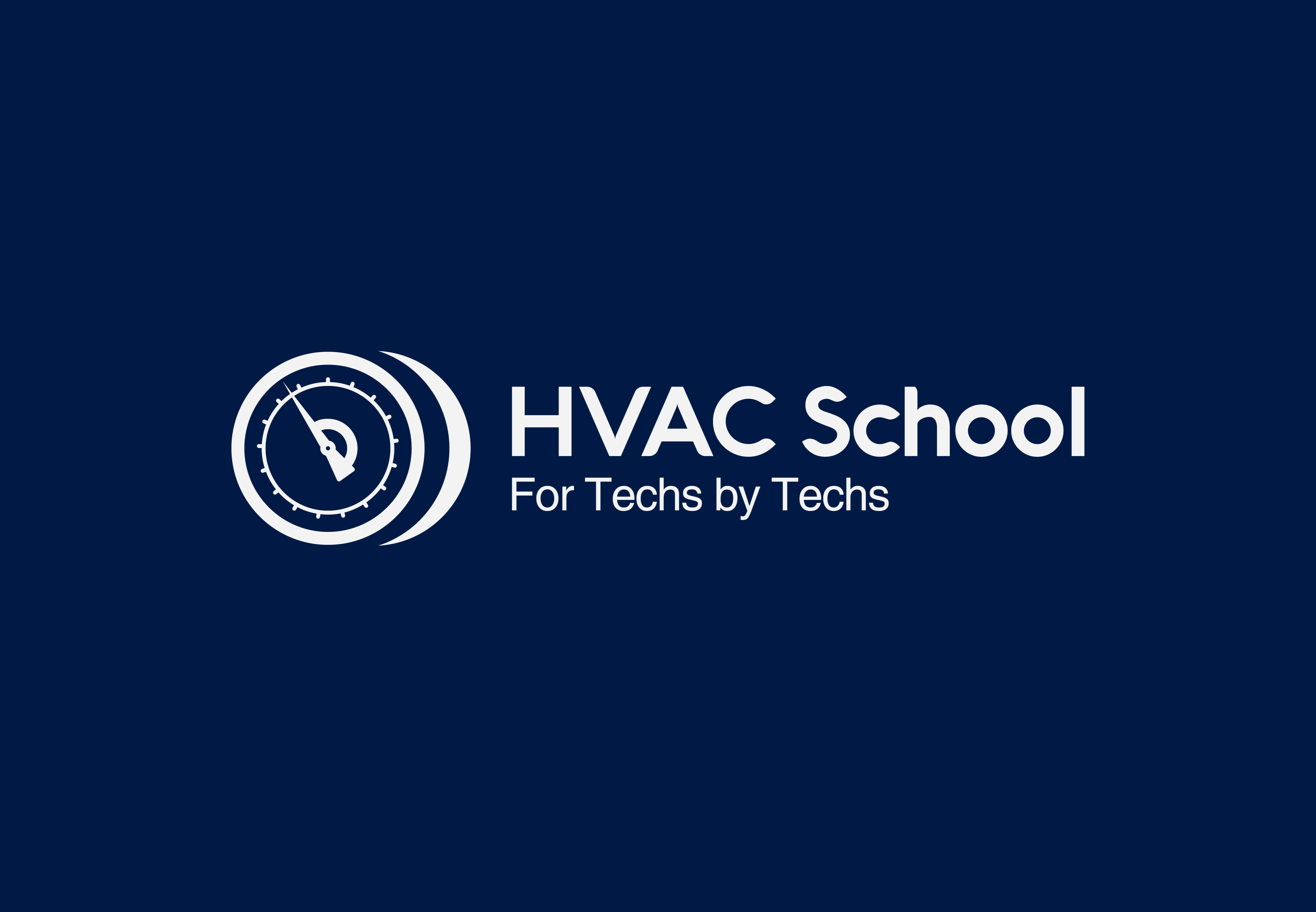
This class recording discusses transformers, ground, common, and line vs. load sides of a circuit.
Read more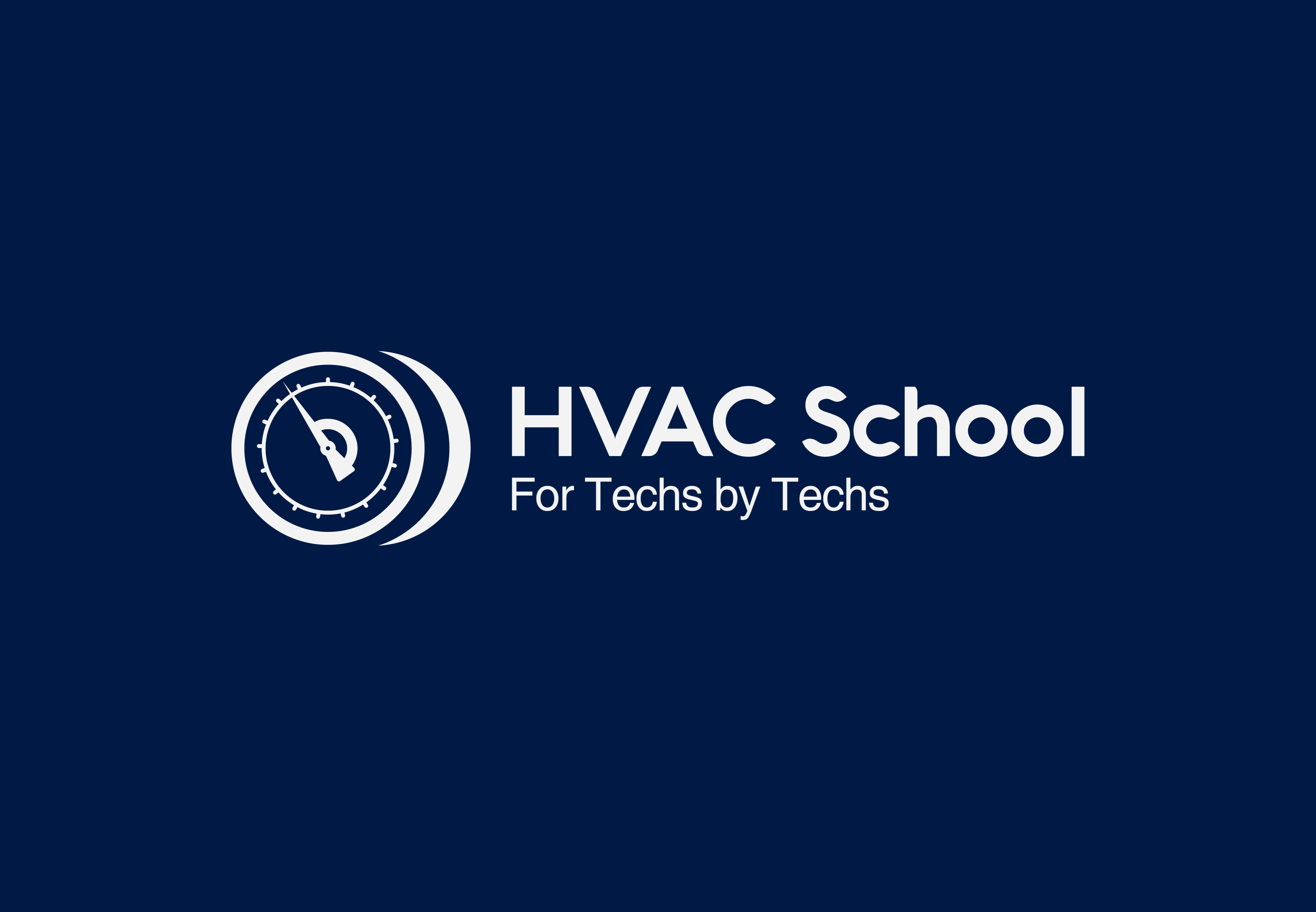
Where does electricity come from and why do electrons move? In this epsiode we talk about differential charges, sine waves and some voltage measurement basics.
Read more