April 2018
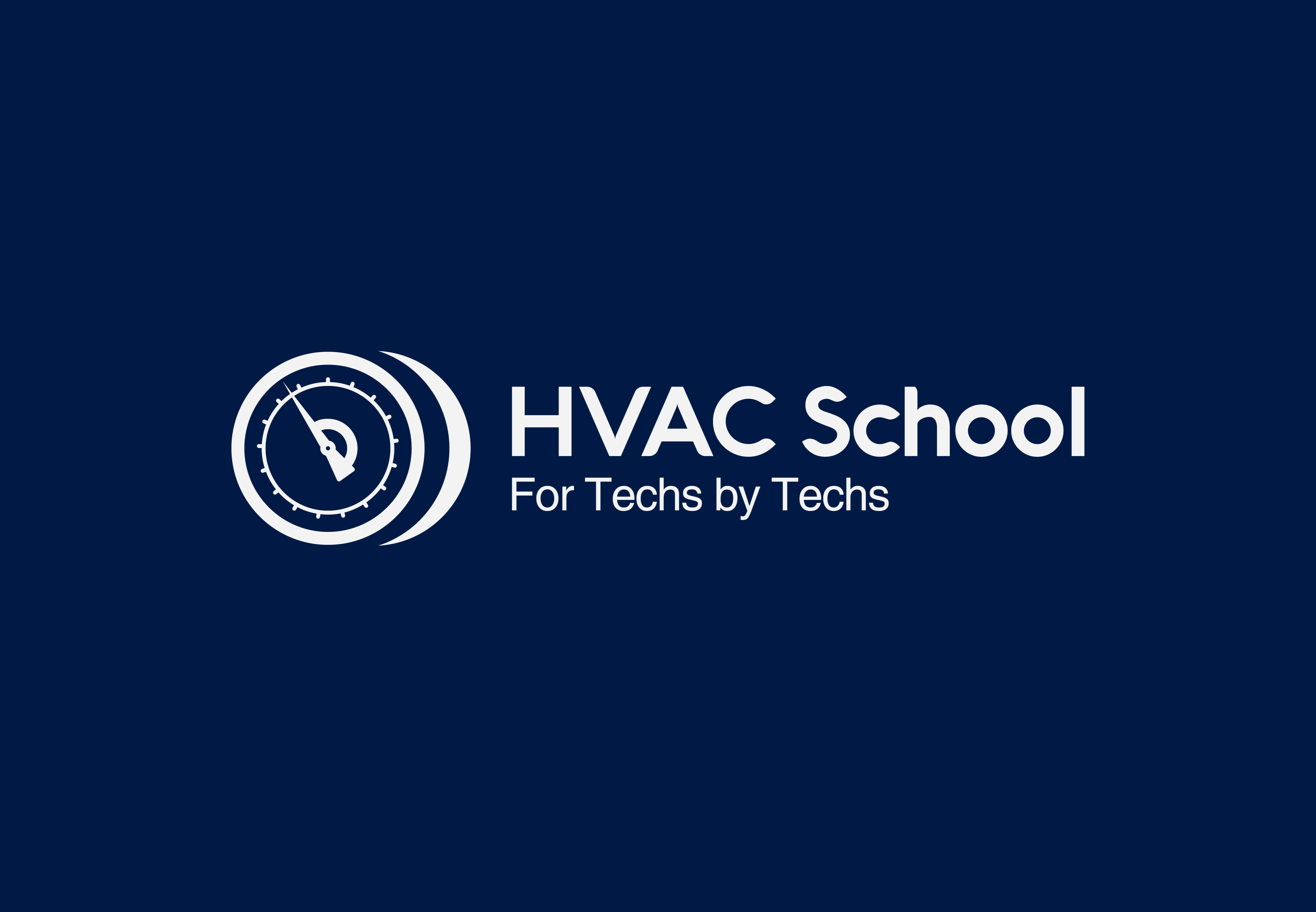
A dirty M word replaced with another M word that gets to the root of the problem
Read more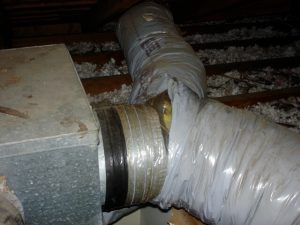
This tech tip was written by one of the best all-around HVAC minds out there: Neil Comparetto. I think that we all can agree that duct leakage is not ideal. Our job is to condition the space. If we can’t control the air, that becomes difficult. On top of that, anytime the ducts leak, you […]
Read more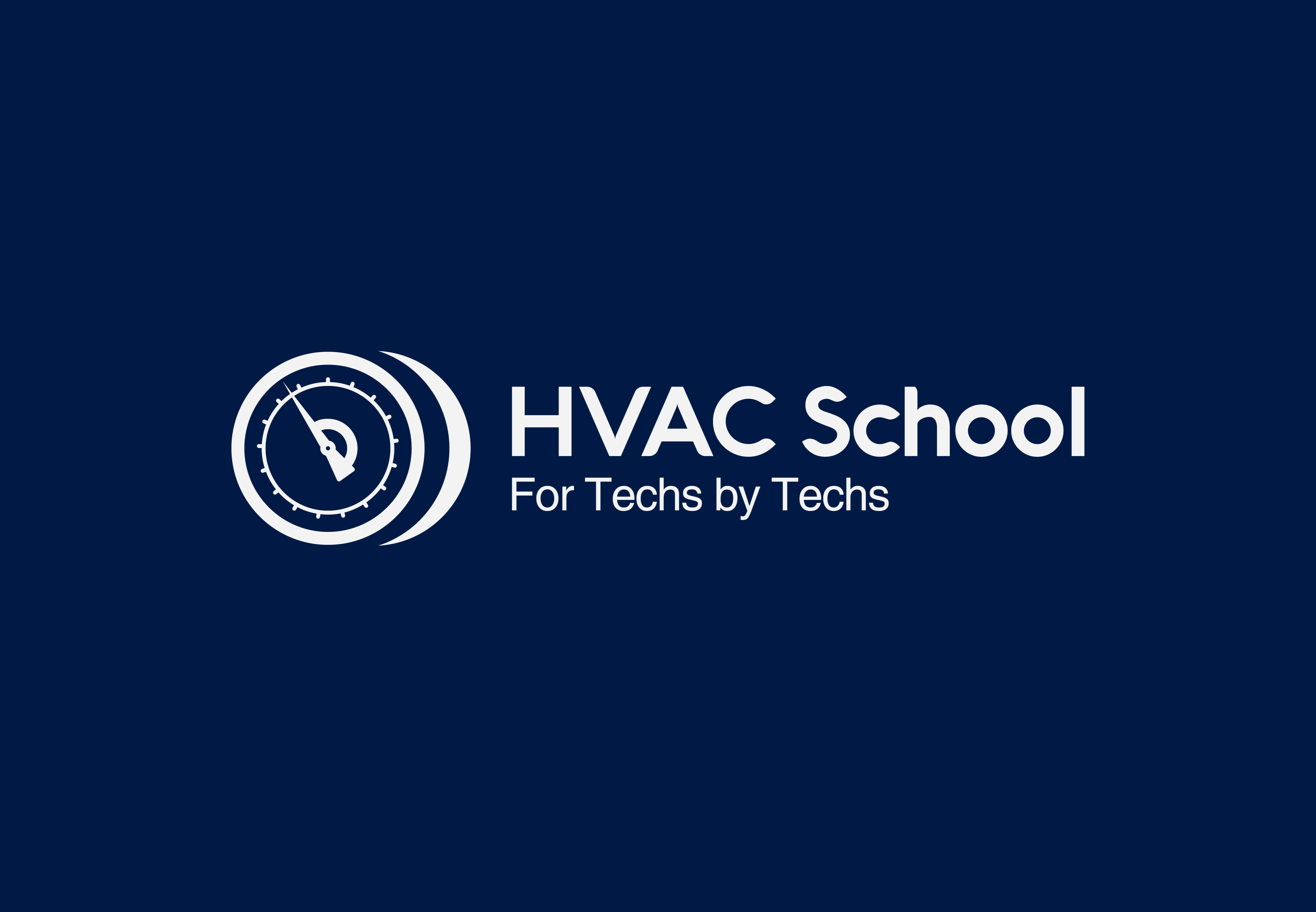
Part 2 of the discussion with Trevor Matthews with Emerson about causes of air conditioning and refrigeration compressor failure and the causes Verifying System Operation Sheet from Emerson https://hvacrschool.com/EmersonVerify Diagnosing Compressor Failures from Emerson https://hvacrschool.com/CompFailuresWe talk with Trevor Matthews with Emerson about causes of air conditioning and refrigeration compressor failure and the causes Verifying System […]
Read more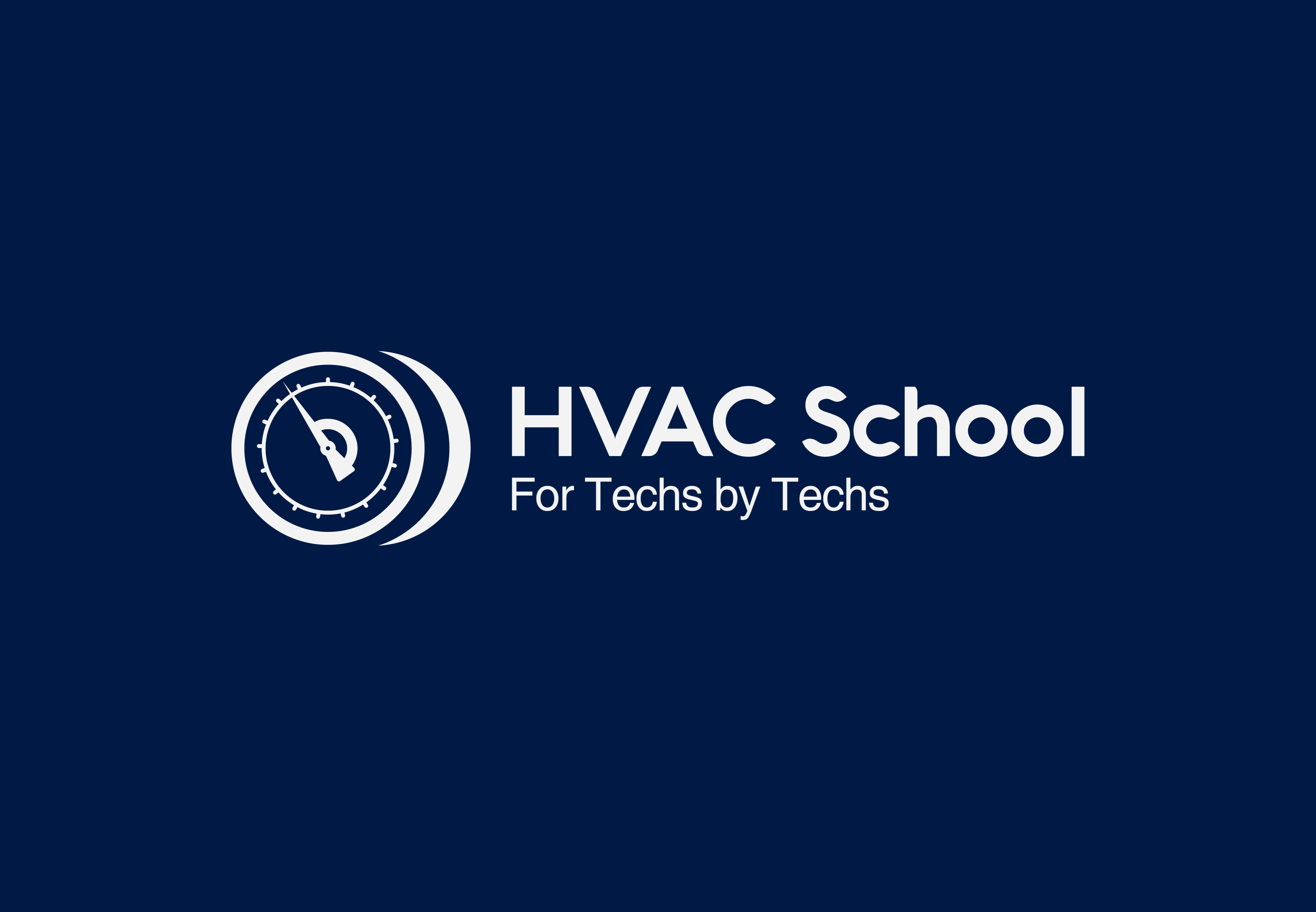
In this short we start the conversation about “Energy? Compared to What?” where we explore all of the energy comparison examples and examples of comparison of energy.
Read more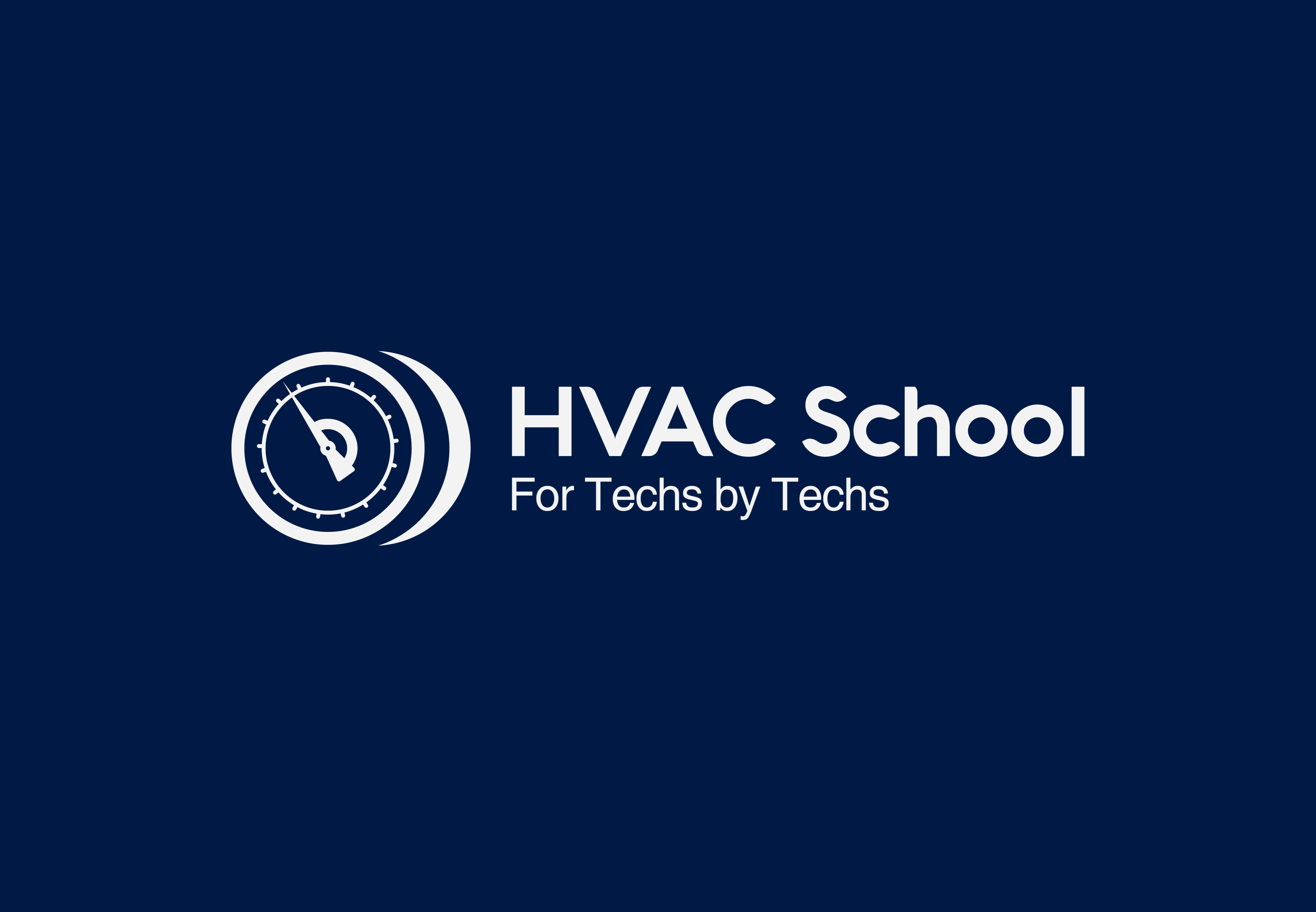
We talk with Trevor Matthews with Emerson about causes of air conditioning and refrigeration compressor failure and the causes Verifying System Operation Sheet from Emerson https://hvacrschool.com/EmersonVerify Diagnosing Compressor Failures from Emerson https://hvacrschool.com/CompFailures
Read more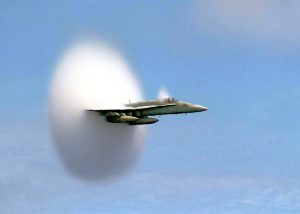
Breaking the Sound Barrier So, what do you think of when you hear an “ideal gas?” R22, R12 maybe… natural? Take a look at the F-18 above. It's breaking the sound barrier, and that cloud is a shockwave. It has nothing to do with this article, but I think it's pretty darn cool! An ideal […]
Read more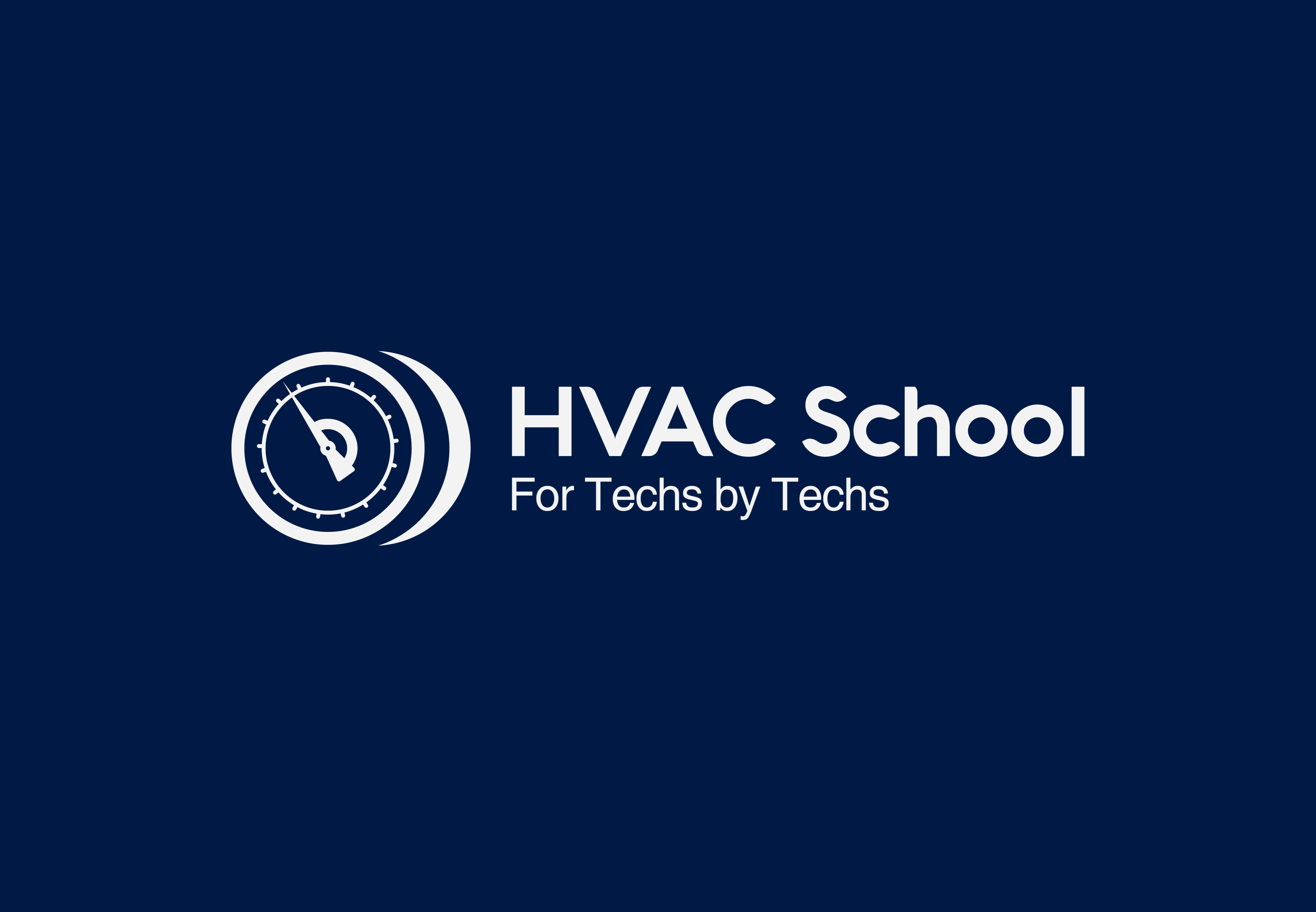
We talk with system and duct design educator Jack Rise about ACCA Manual J load calculation and Manual S system selection
Read more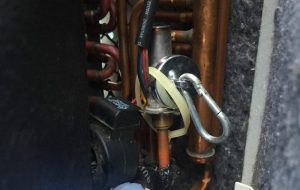
This tech tip comes from our contributor, compressor decapitator, and super tech Ulises Palacios. Many ductless systems and some high-efficiency unitary systems have electronic expansion valves. If you find one that is stuck closed, you may be able to get it open temporarily by putting a strong magnet like the one shown above on the […]
Read more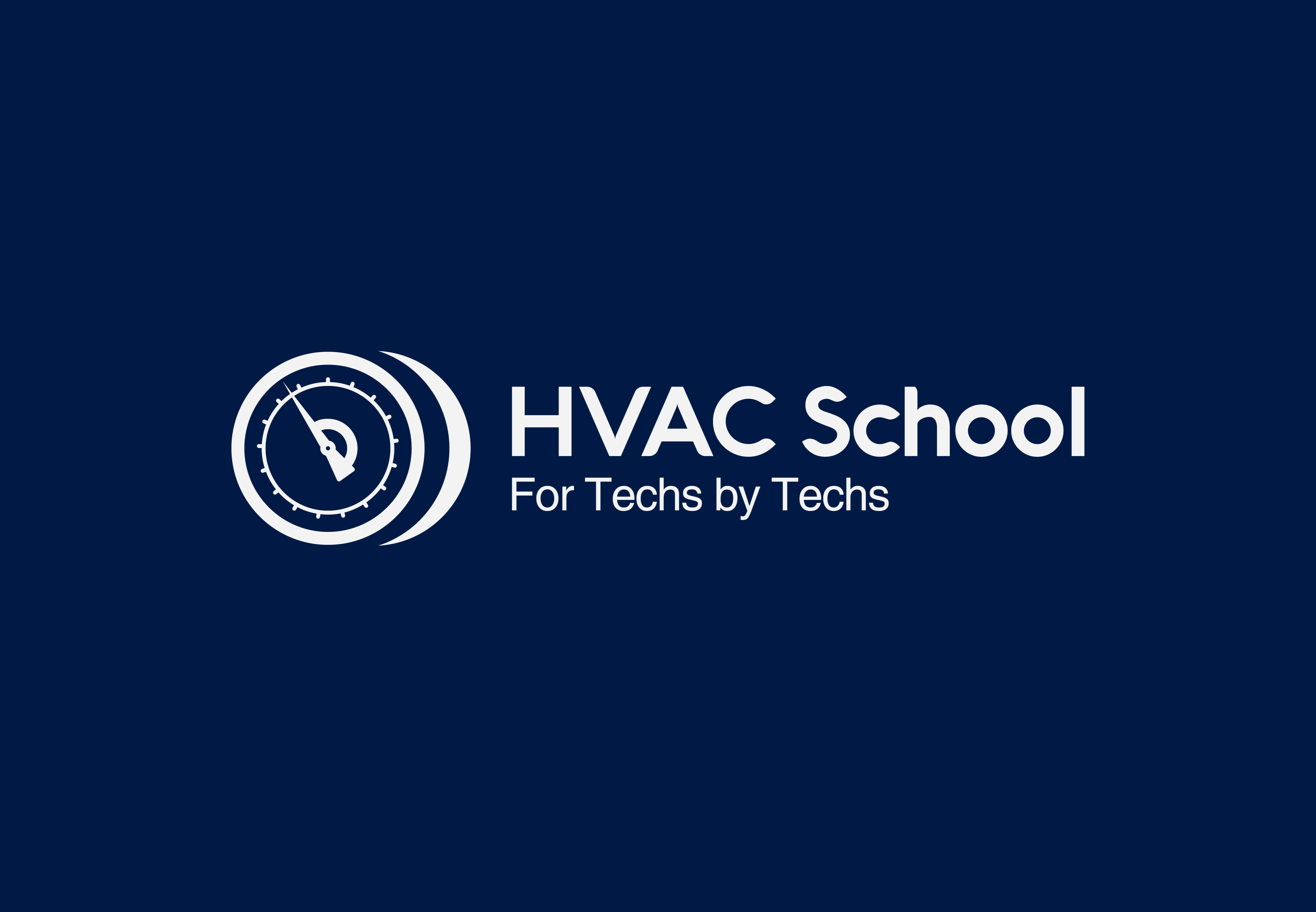
Bill Johnson shares his practical tips to make low voltage electrical diagnosis easier
Read more