July 2018
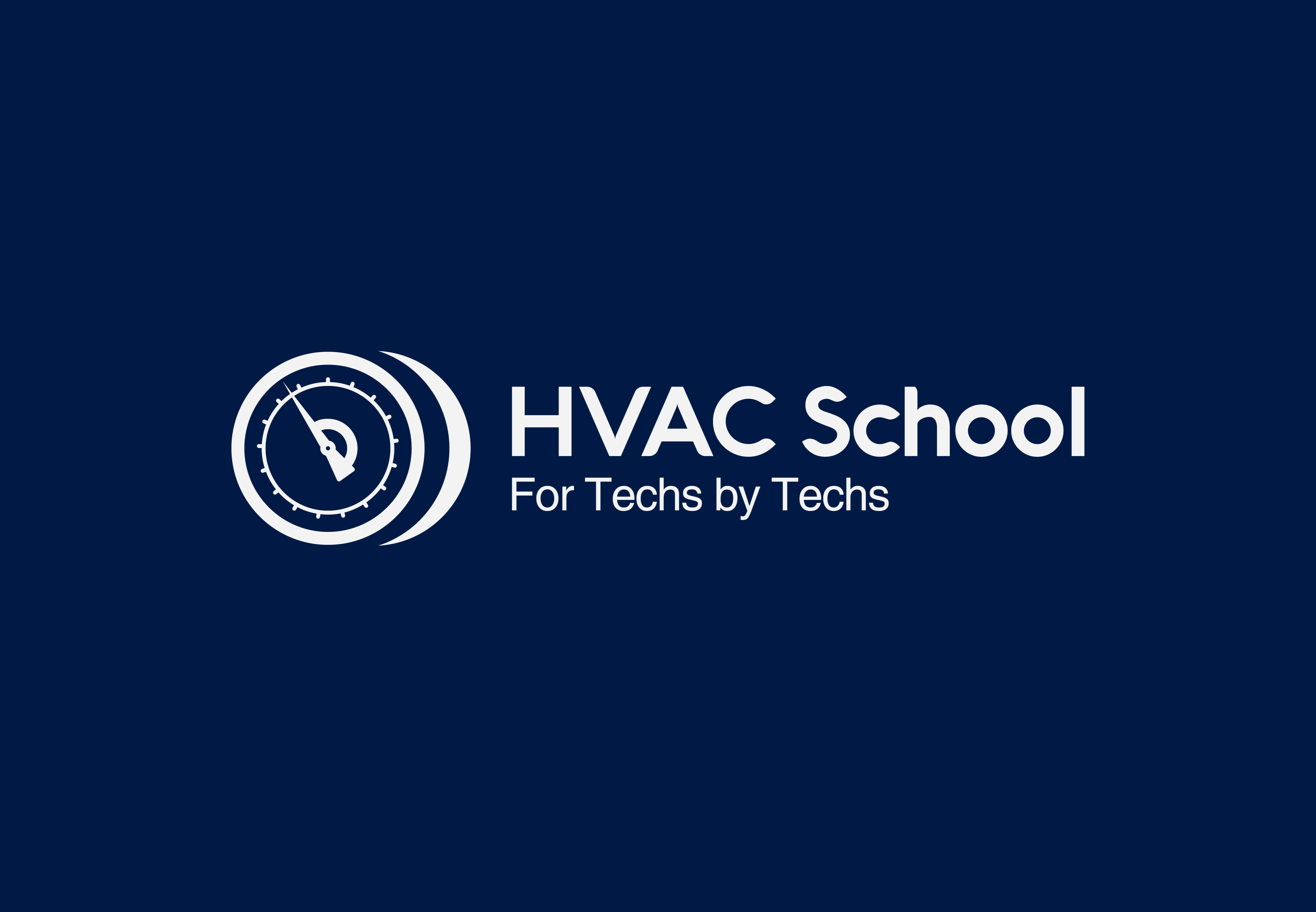
In this episode Bryan covers how to measure air velocity directly at a return or supply and what it tells you
Read more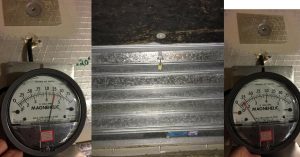
Tech Brandon Livingston posted about fire dampers and took some photos shown here. He gave me permission to share this here, and his original post inspired this tip. Thanks, Brandon. The picture on the left shows the situation before the damper was opened. The right image show what happened after it was opened and a […]
Read more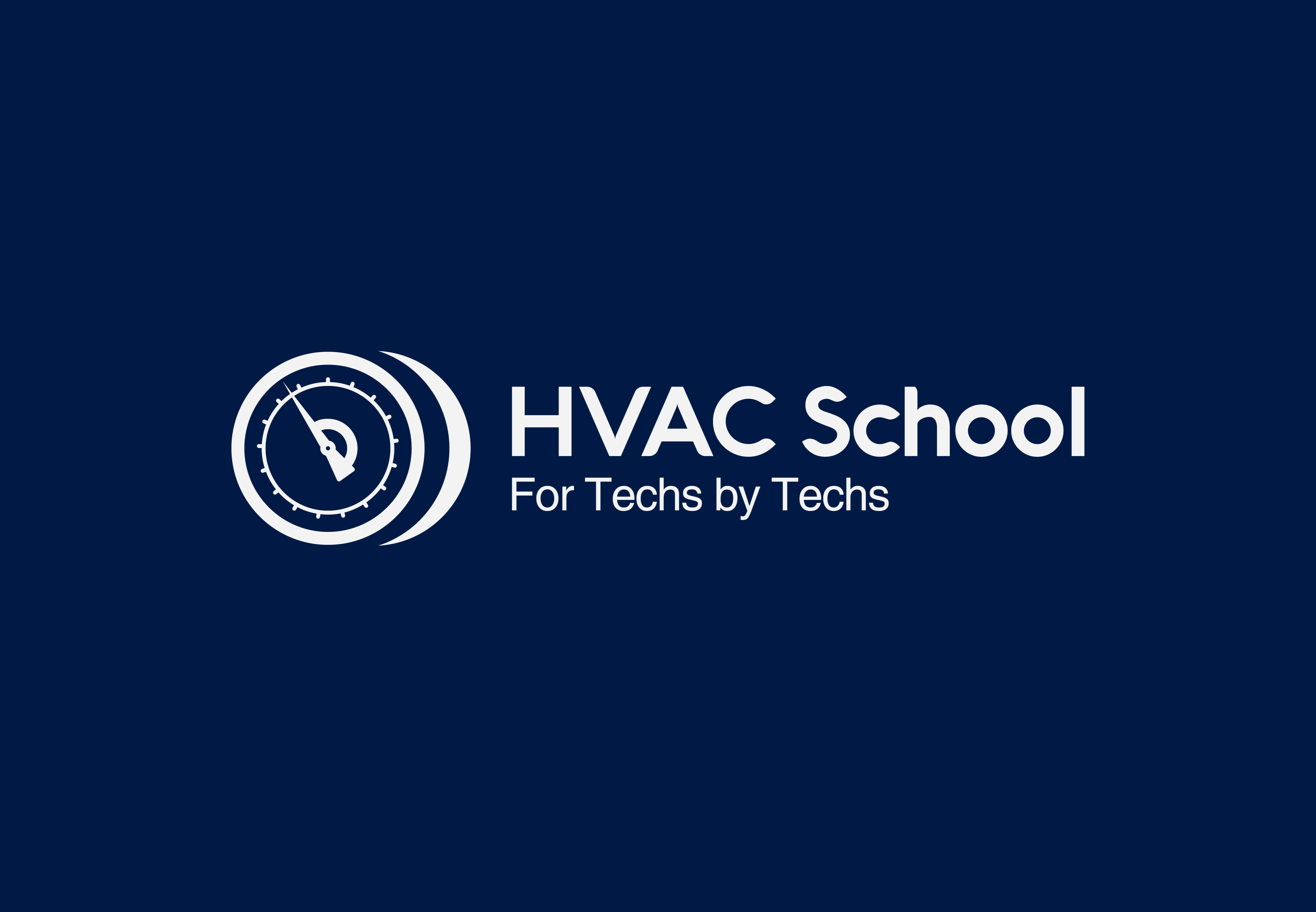
Eric Mele walks us through the components of water source heat pumps, how they work and what to look for
Read more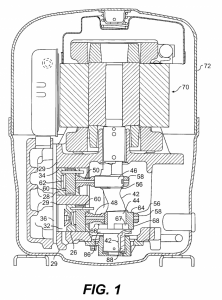
Can a single-phase motor run backward when start and run are swapped? The answer is (generally) yes. Is the motor designed to run backward by simply swapping run and start? The answer is (generally) no, with a few notable exceptions. Before we jump in, this article has two purposes. #1 – it helps you understand […]
Read more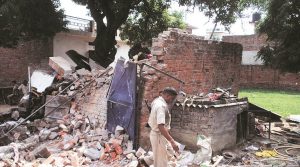
My friend Ami Slavin requested that I write about this important topic in response to the horrifying videos showing up online of death and gore associated with compressors exploding. He pointed out that the “diesel effect” can be the cause, so let's explore what may be—and likely is—leading to these horrible incidents. In a diesel […]
Read more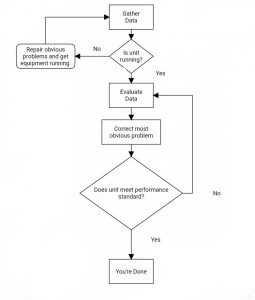
This article is part 5 of a 5-part series on troubleshooting by Senior Refrigeration and HVAC tech Jeremy Smith. This step might be the most challenging part of troubleshooting. We've got a “Most Likely candidate” for the trouble, but we don't know for certain that's what is wrong. So, we have to combine our customer […]
Read more