September 2019
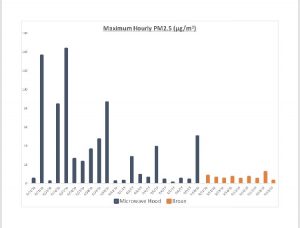
This article was written by my good friend Neil Comparetto, a contractor and industry influencer who is helping shape IAQ for the HVAC industry in the US for the better. Thanks, Neil! Indoor air quality (IAQ) monitors can tell you a lot about the air you are breathing. We find that the information is valuable […]
Read more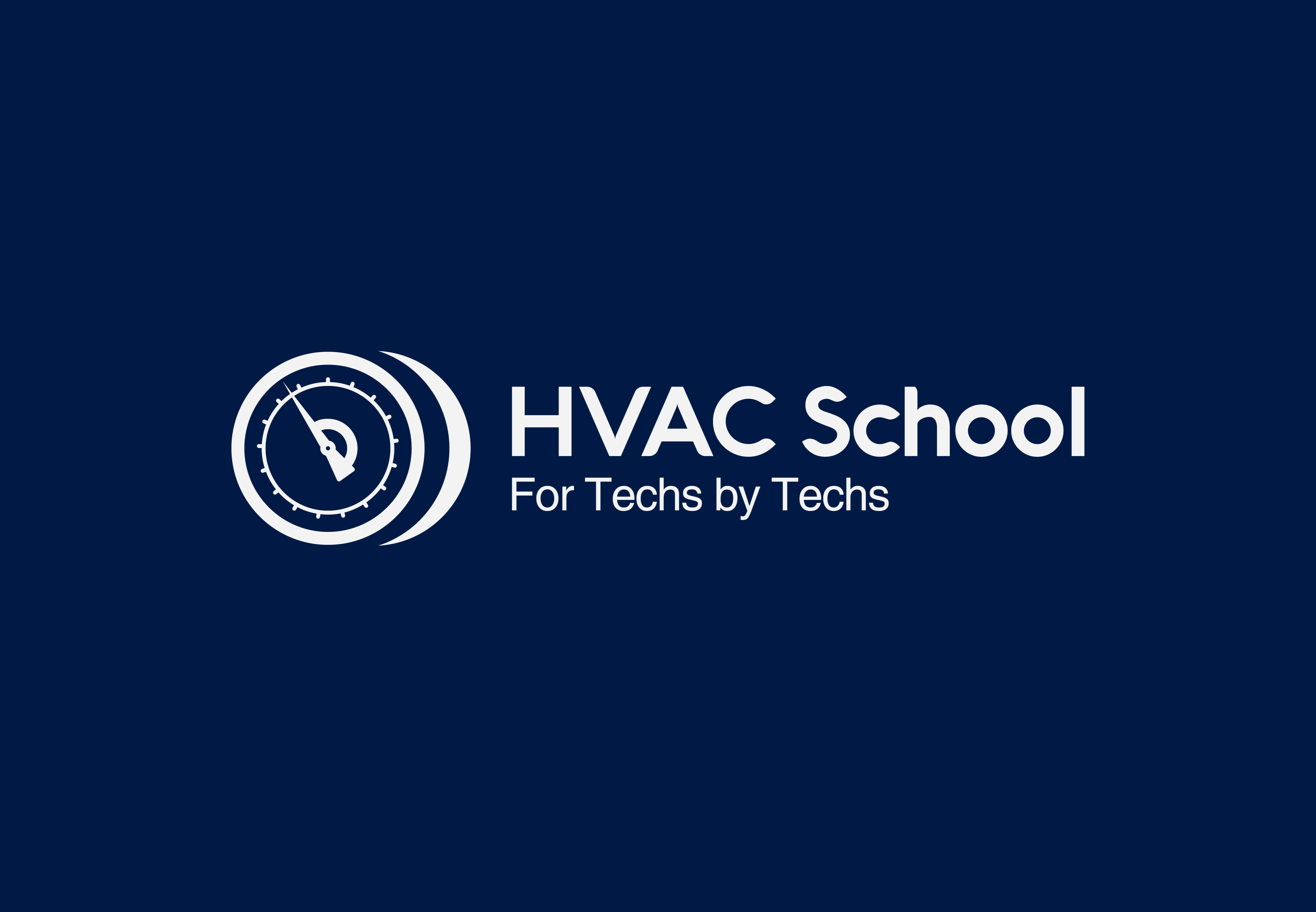
Alex Meaney from Wrightsoft joins us to talk about Manual J and S and how that applies to real world situations where contractors are tempted to replace “Like for Like”. Use the offer code POD2019 for a great discount on Wrightsoft products at Wrightsoft.com
Read more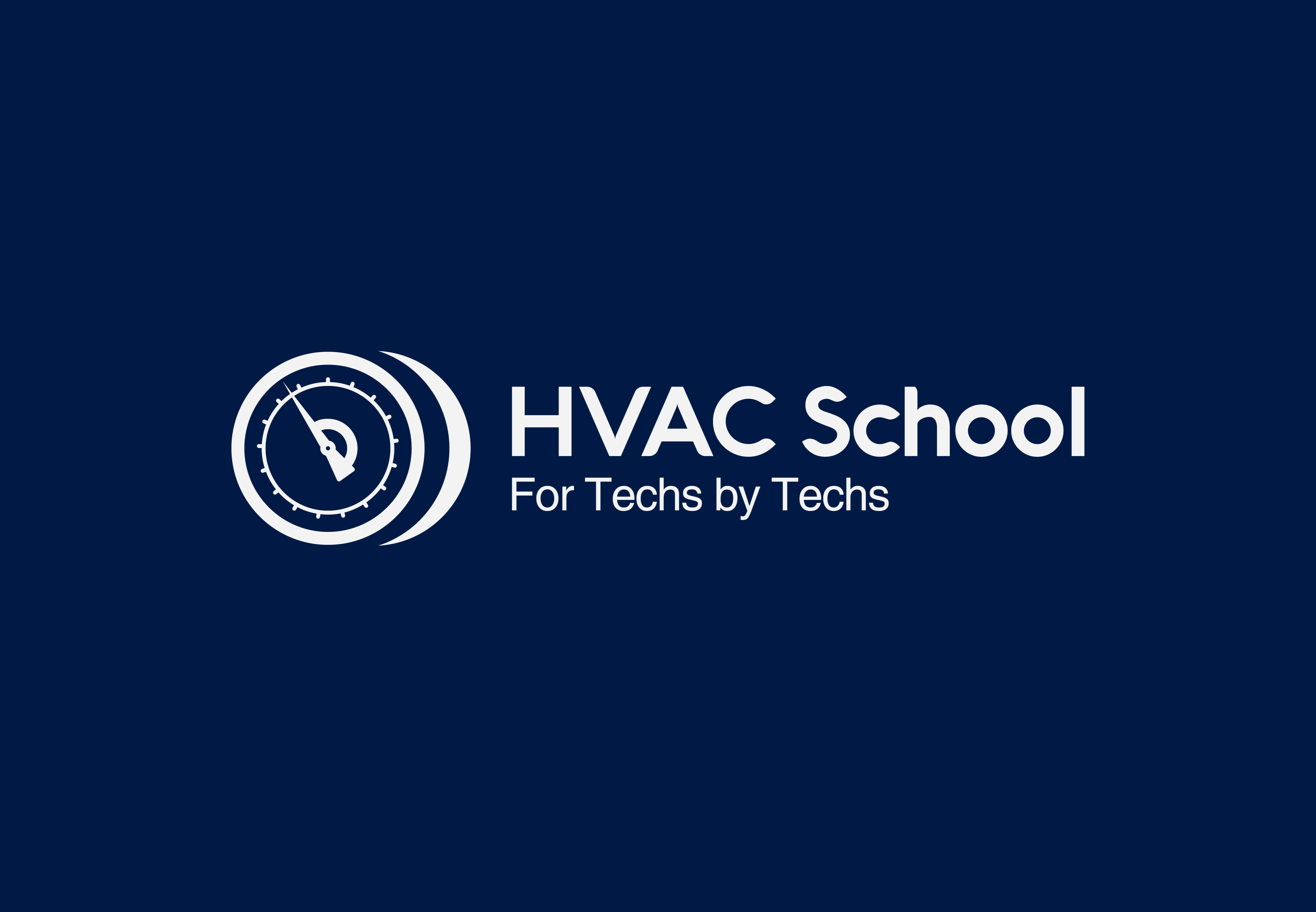
In this live podcast from the Castbox app we talk about analog vs. digital, digital vs. probes and probe vs. non-invasive testing of A/C and refrigeration as well as apps and various bluetooth tools
Read more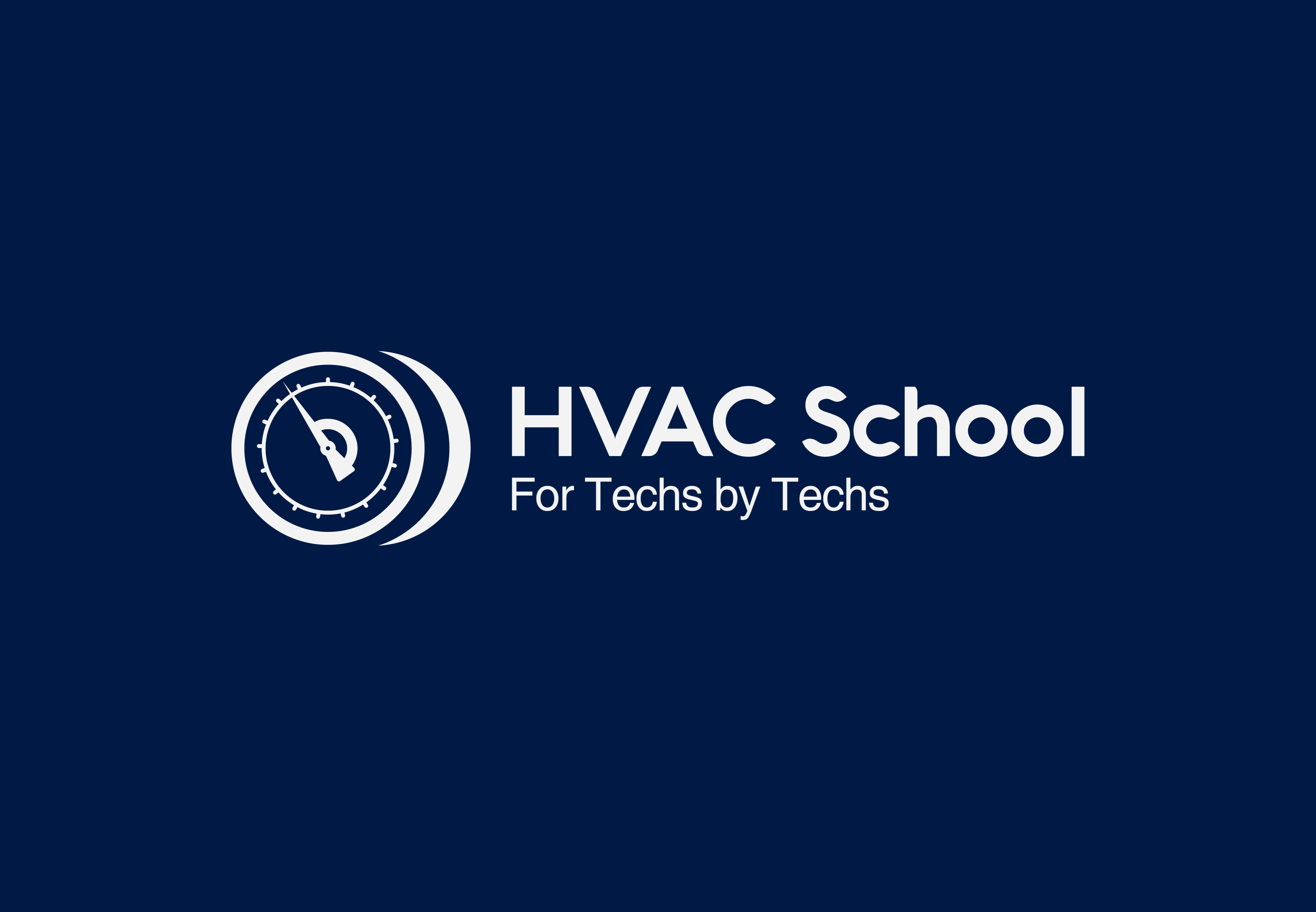
What is ambient CO? Why does it matter and what do you do to check for it.
Read more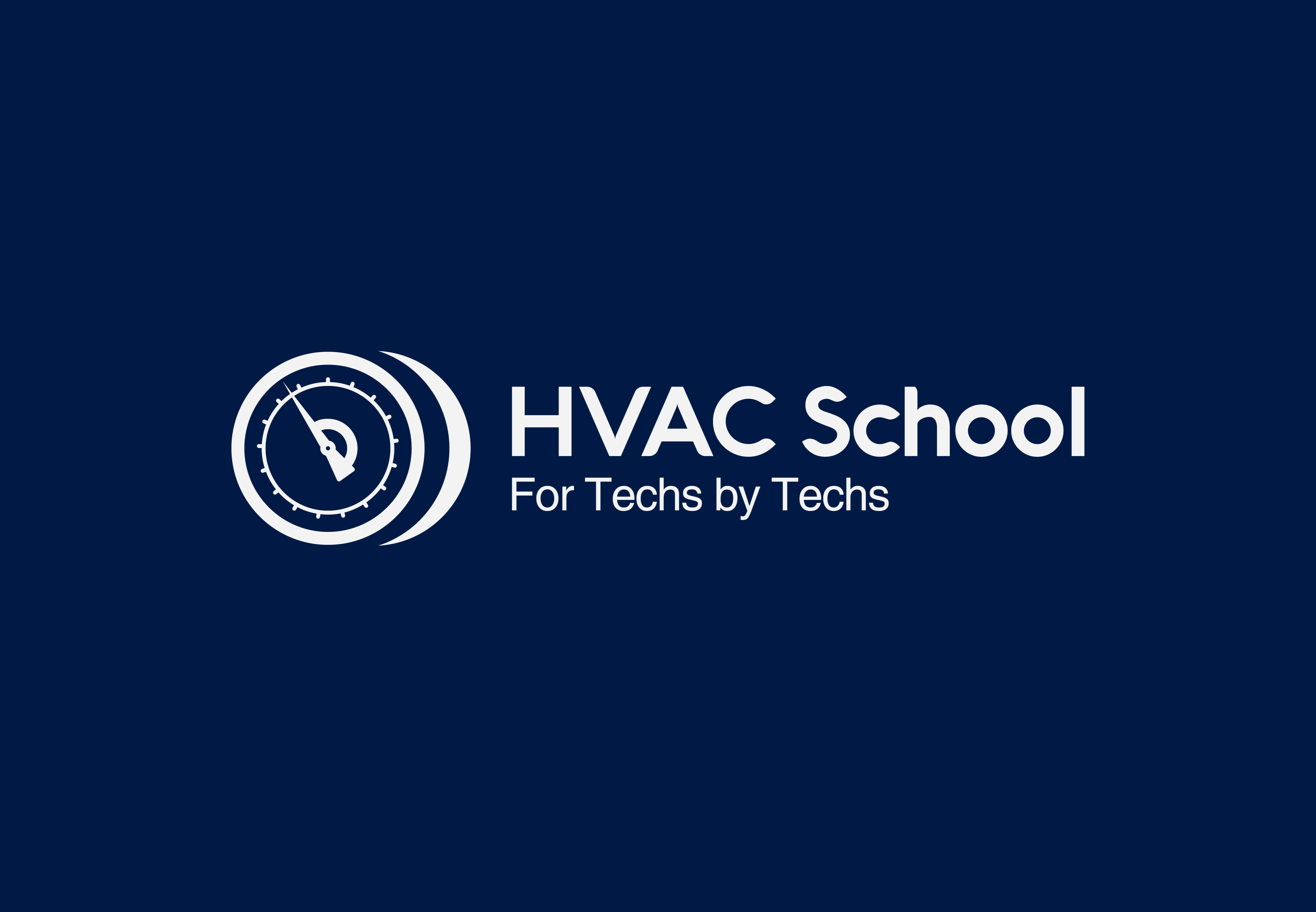
My buddy Micahel Housh joins us to discuss his years of experience w/ Geothermal Heat Pumps
Read more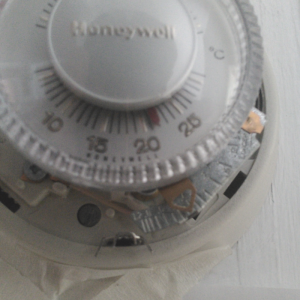
As a technician, you most likely know some customers who still have an oldie thermostat (you know, those old mercury bulb things, like the round Honeywell CT87 and such). Keep in mind that those usually have an adjustable heat anticipator. If you’re newer in the field, you may not have seen or worked with those […]
Read more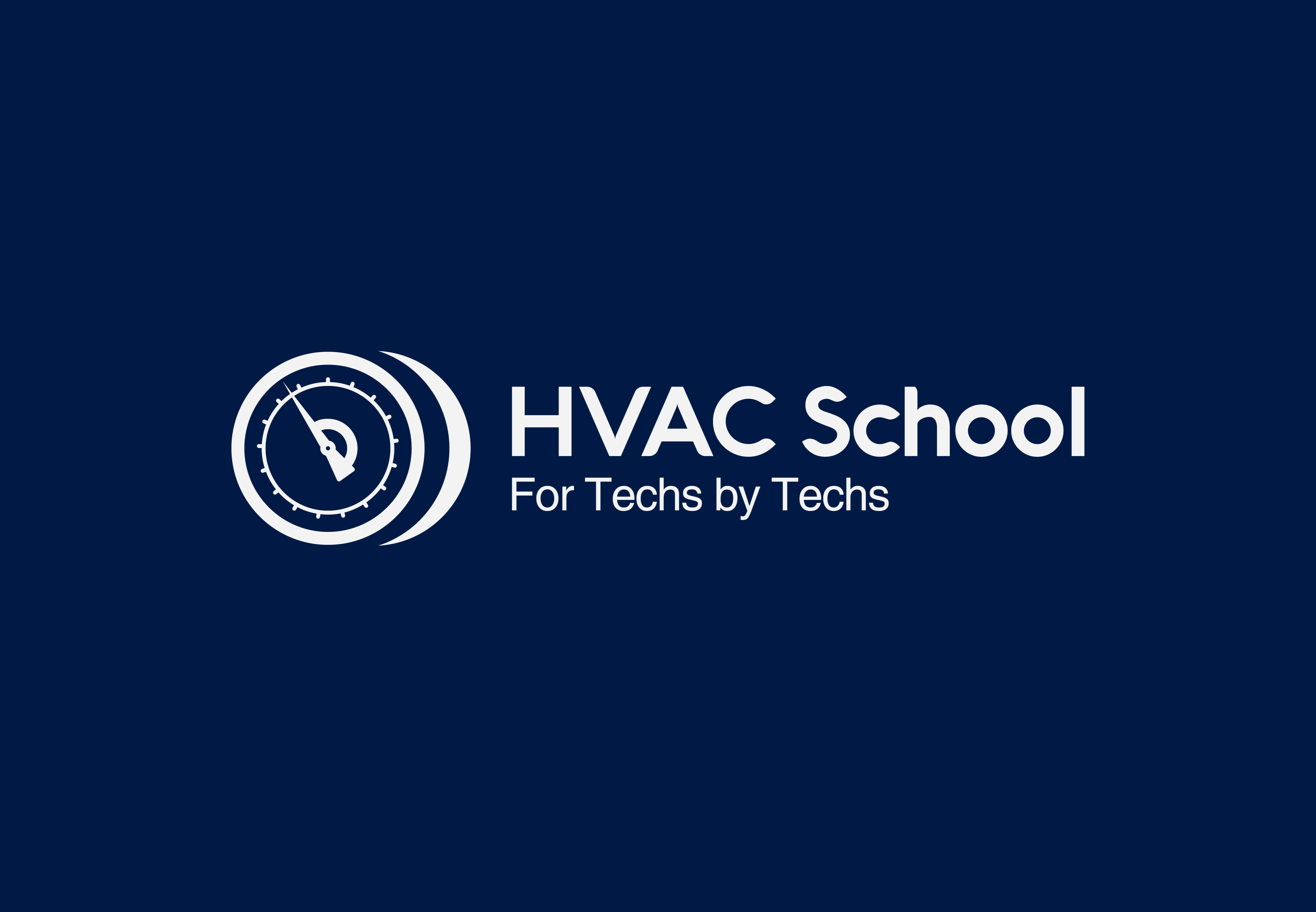
What is water vapor diffusion and why does it matter to the HVAC technician?
Read more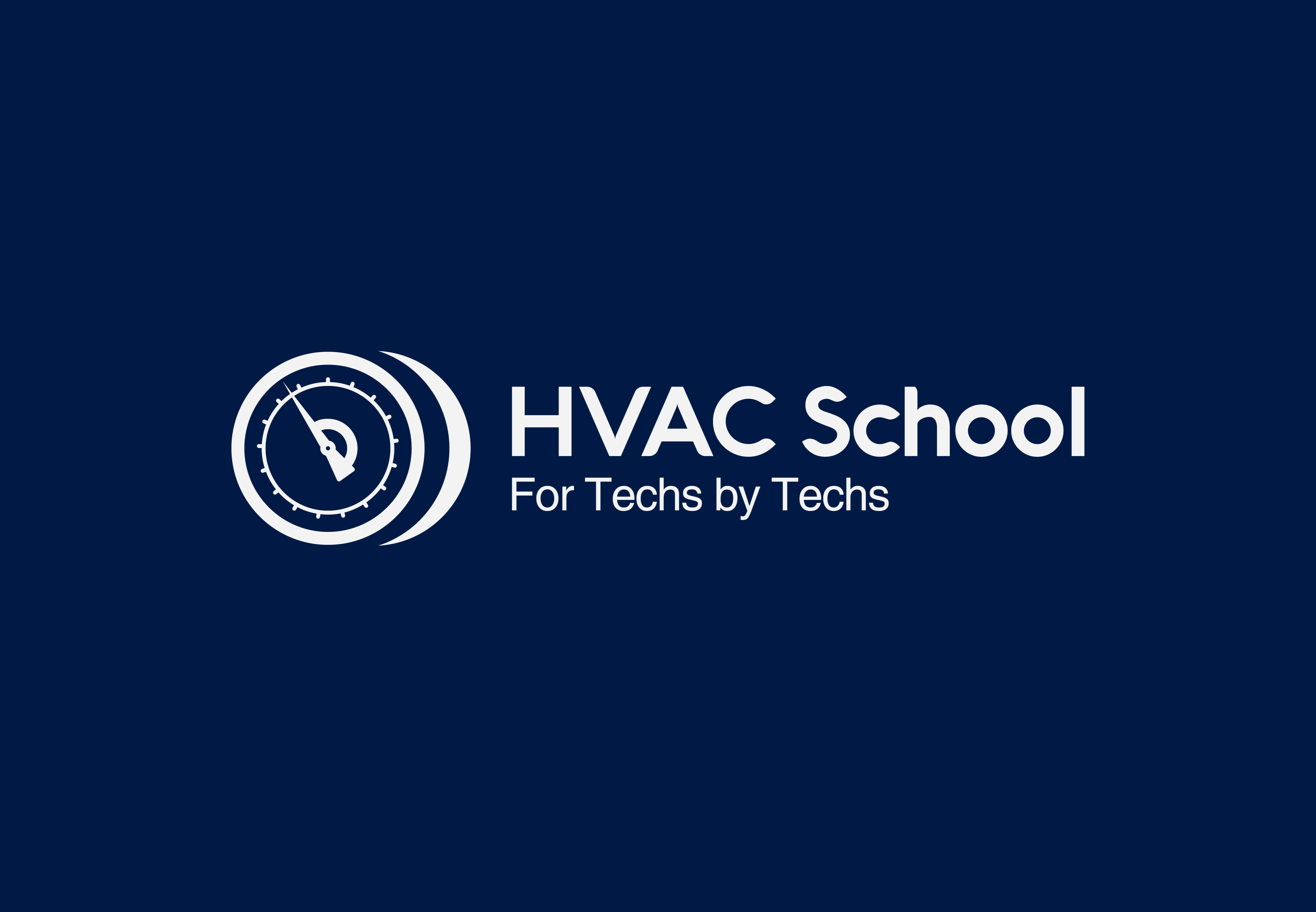
In this live conversation, we discuss some real-life difficult customer situations and what we learned along the way
Read more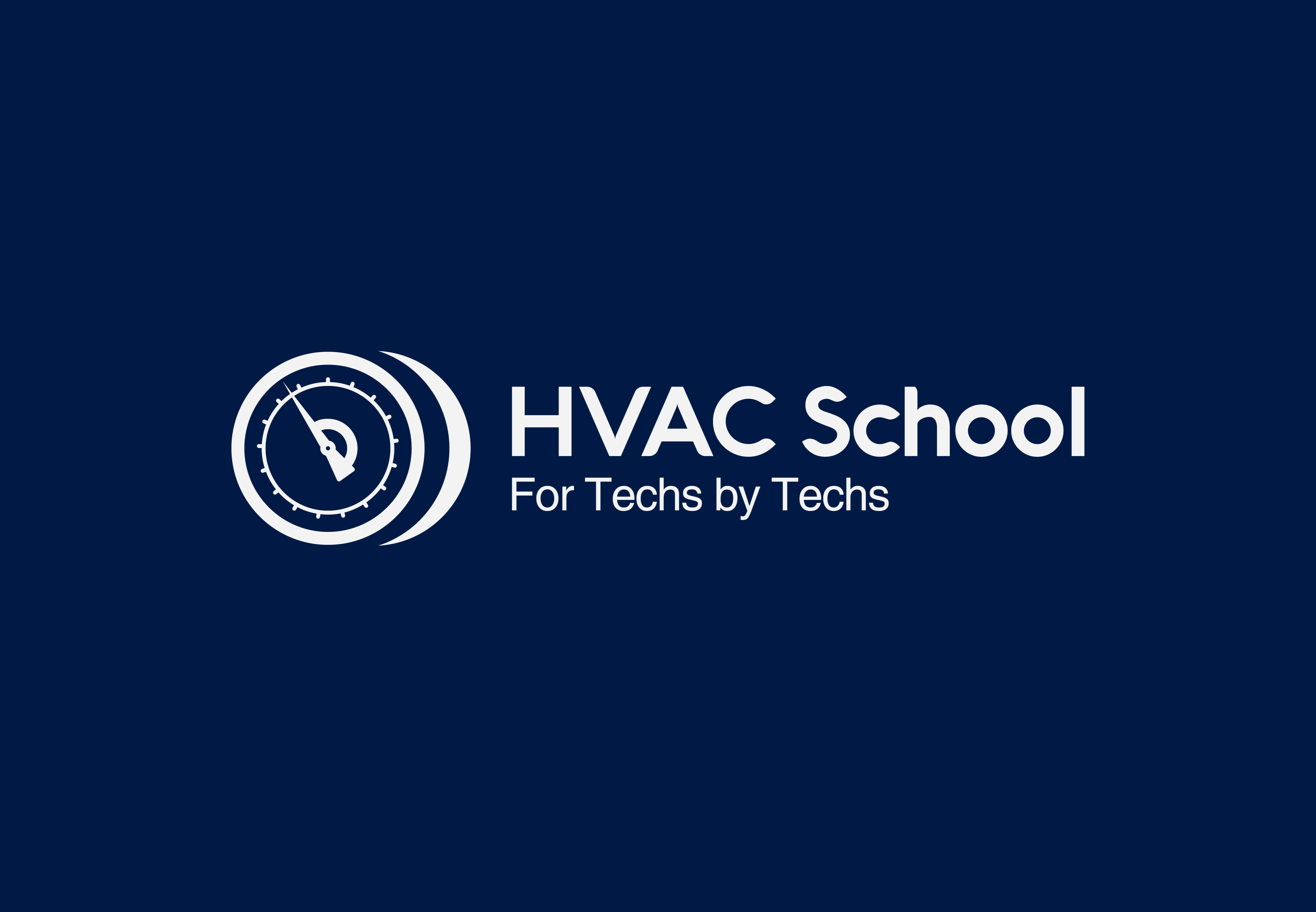
Henry Papa from Sporlan joins us in person to talk about refrigeration case controllers
Read more