October 2019
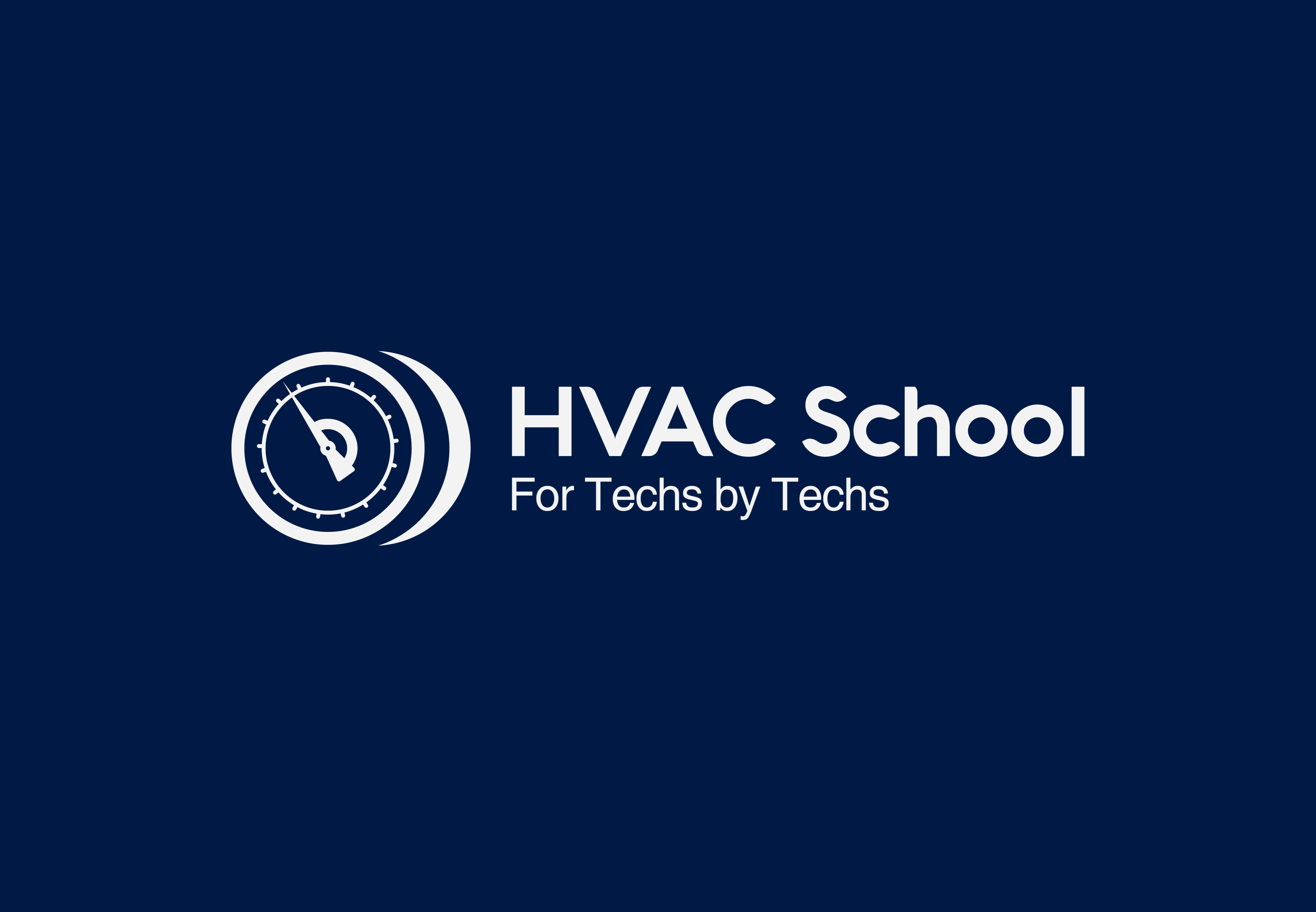
Bert joins Bryan to talk about what he's learned to help prevent the dreaded callback
Read more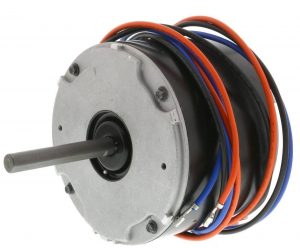
This article was written by technician and HVAC School community star Kenneth Casebier. Thanks, Kenneth! When looking at replacing a single-phase A/C motor with an aftermarket motor from your van, there are a few things you should know and pay attention to. First, the factory OEM motor will always be the best option, especially when […]
Read more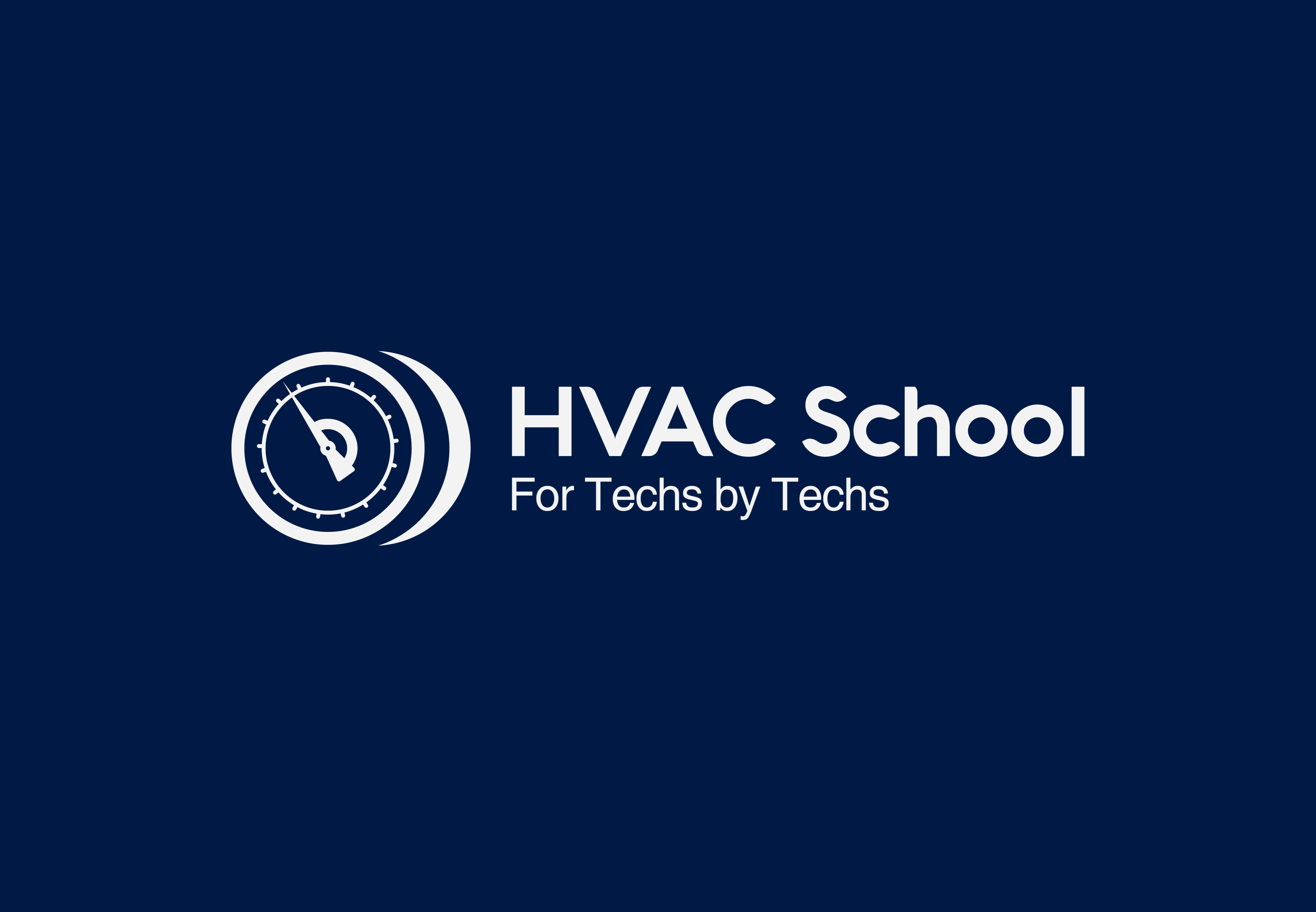
IF you are new to the HVAC trade here are 7 things to apply to help you win
Read more
First, a thermocouple is not a flame rectifier like a modern flame sensor. A thermocouple actually generates a millivolt potential difference when it is heated by a flame—just to get that out of the way for any of you newer techs who are used to modern flame sensors. With higher efficiency gas-fired equipment being the […]
Read more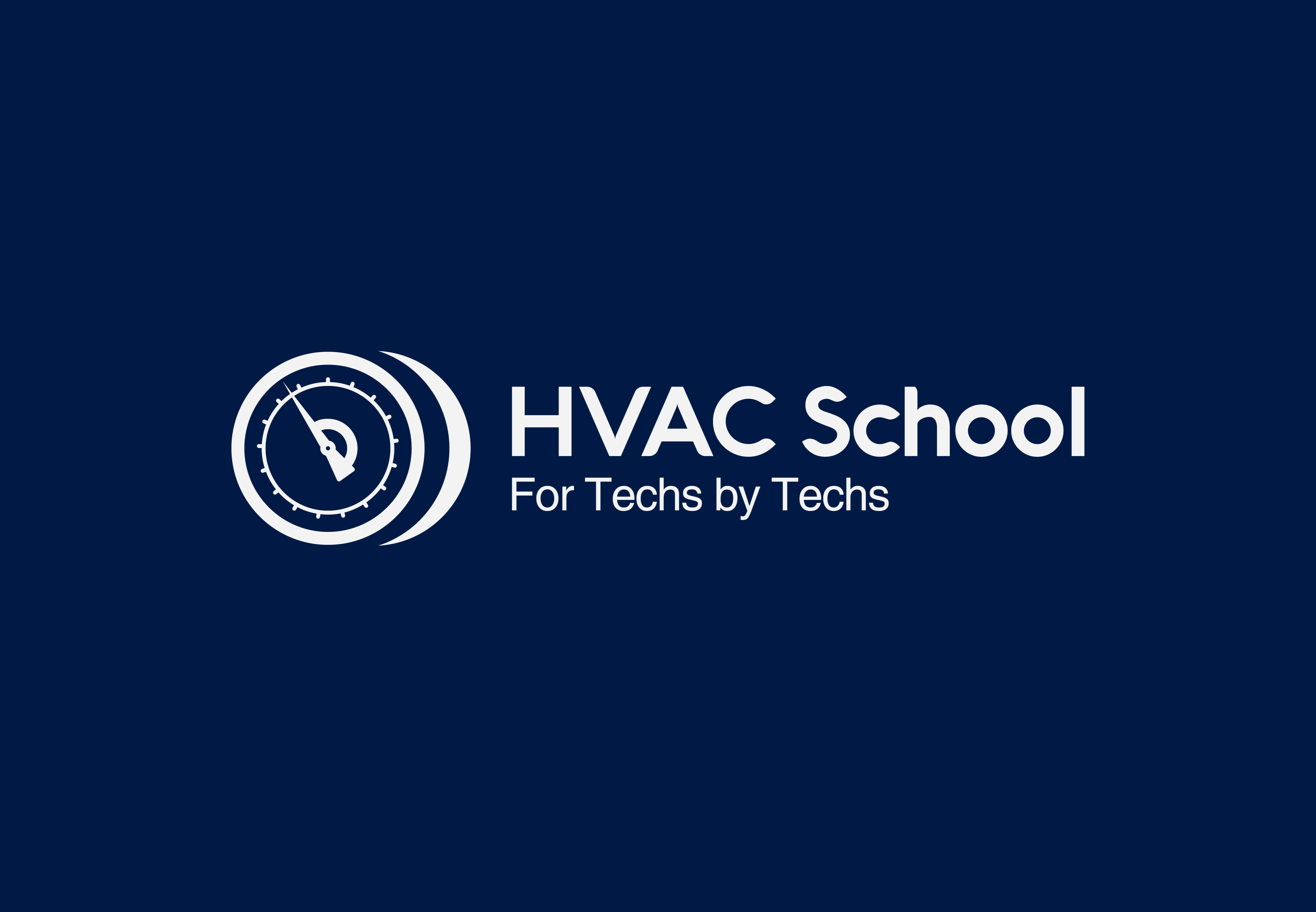
Jim is back to talk about power quality meters and what they are good for as well as how they are used
Read more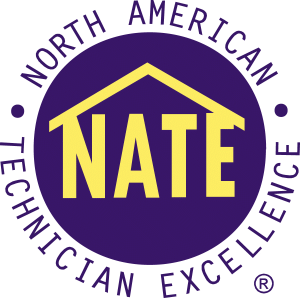
Title: NATE Testing & Review Description: Bryan Orr with HVACRSchool.com will offer a general, technical NATE review from 8am-11:30am and proctor a session of North American Technician Excellence (NATE) technician certification testing in the afternoon from 1pm-5pm. The Review will cover elements of the CORE, Air Conditioning and Heat Pump exams and how the concepts apply […]
Read more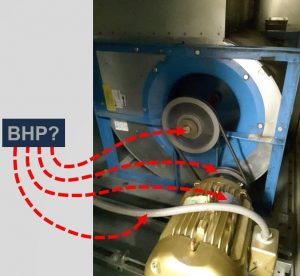
Brake horsepower (BHP), motor nameplate HP, and the actual electrical power (watts) a motor will consume are different but related concepts. They can get confusing. So, we will tackle them one at a time. Let us start with simple definitions of work, power, and horsepower. Work = distance in feet x force in pounds, both […]
Read more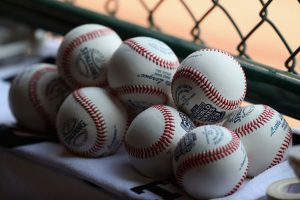
This is a VERY in-depth look at ACFM vs. SCFM and why it matters to airflow measurement from Steven Mazzoni. Thanks, Steve! Imagine your job is to figure out how fast baseballs were traveling before they hit a sheet-rock wall. The only method you have is to measure the depth of the dent left in […]
Read more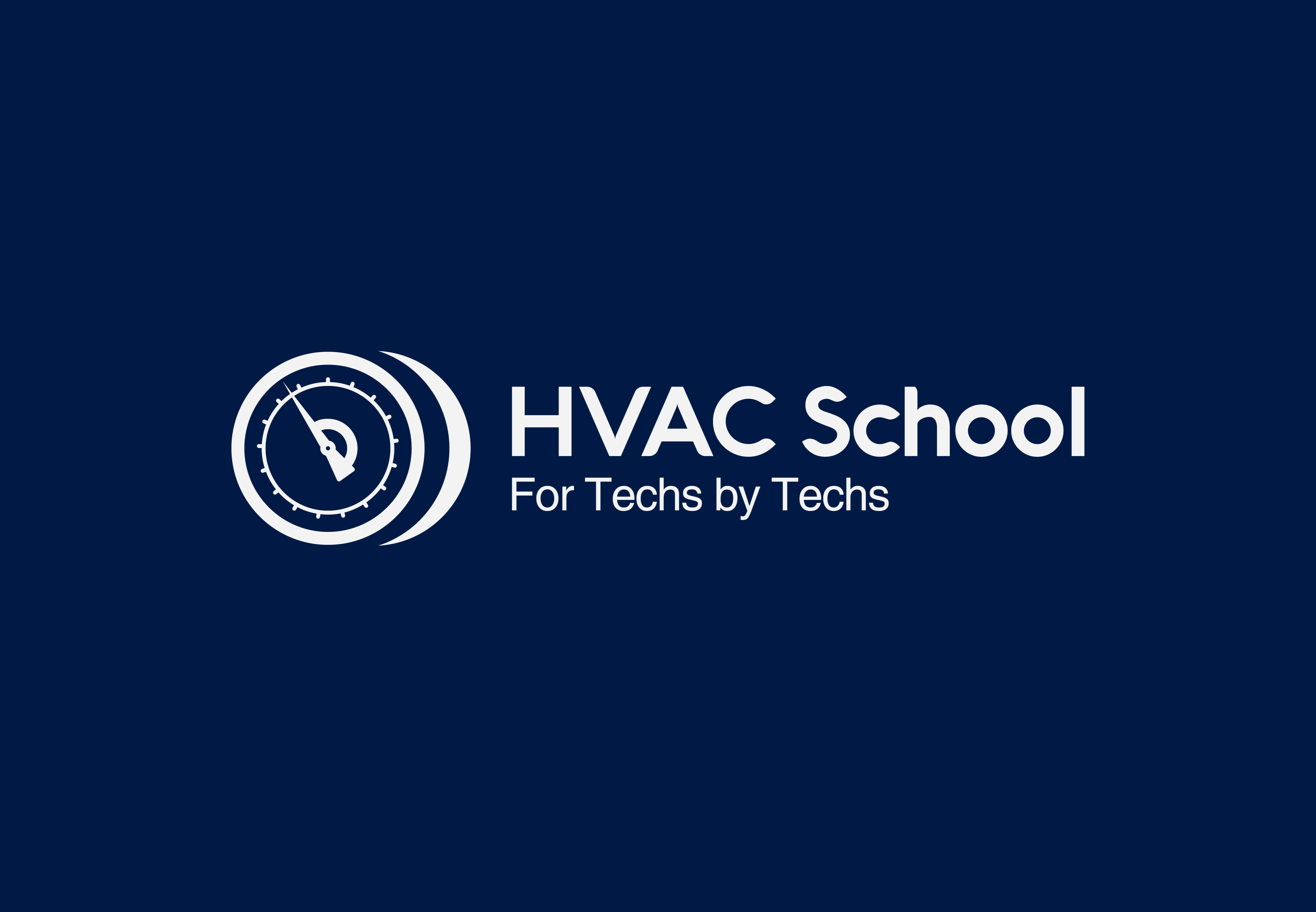
We talk through (once again) what REALLY causes capacitors to fail and what to do about it
Read more