January 2020
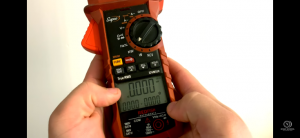
Capacitors are traditionally tested with a capacitance meter (commonly found as a function within a multimeter), with the component taken entirely out of the circuit. “Bench testing,” as this method is referred to, is hands-down the safest method of checking capacitance in microfarads. All other methods require the capacitor to be wired into the circuit […]
Read more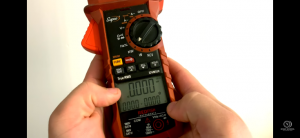
Capacitors are traditionally tested with a capacitance meter (commonly found as a function within a multimeter), with the component taken entirely out of the circuit. “Bench testing,” as this method is referred to, is hands-down the safest method of checking capacitance in microfarads. All other methods require the capacitor to be wired into the circuit […]
Read more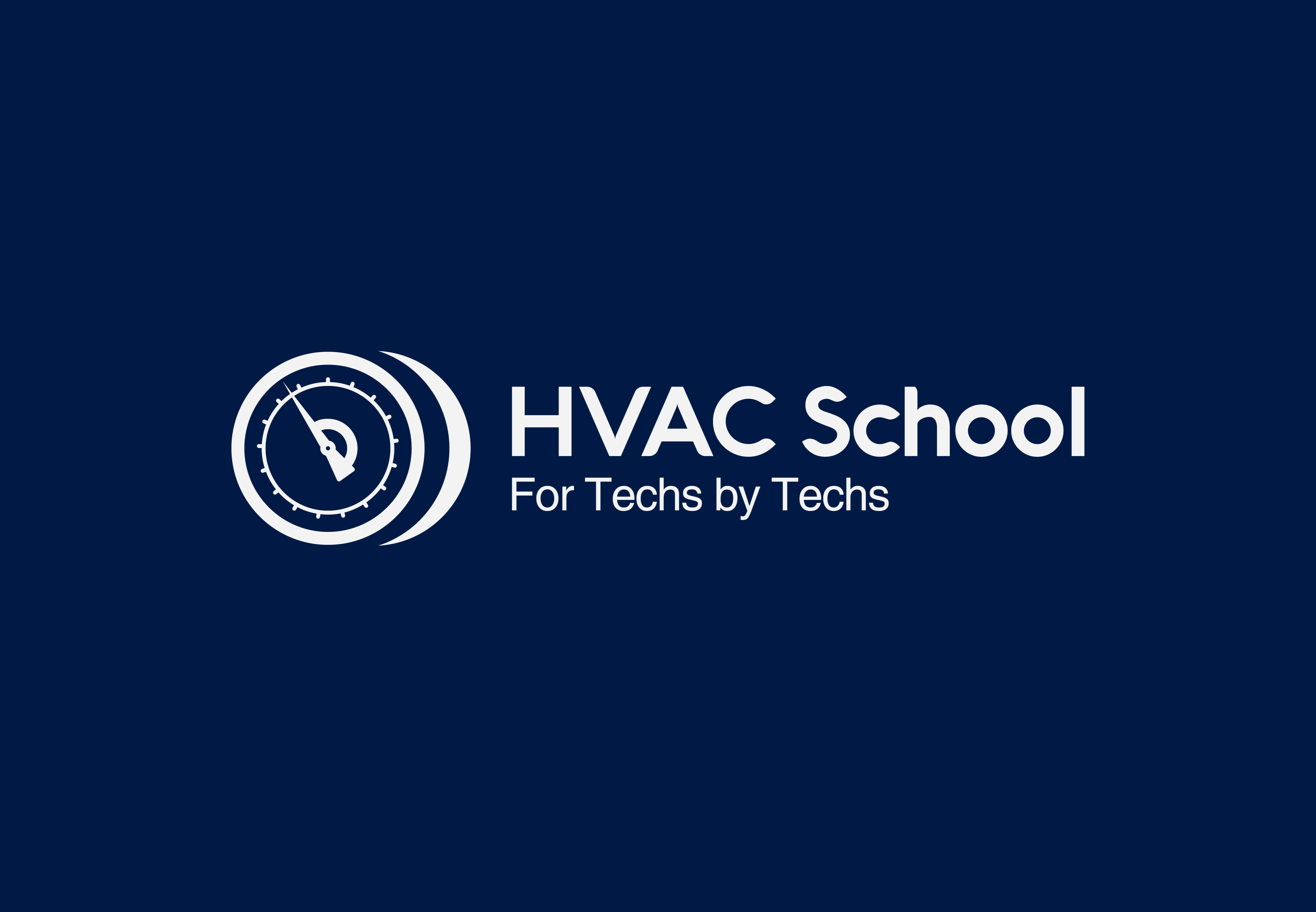
Rachel and Eric Kaiser join us to talk about making STEM concepts more common in the trades and how to teach STEM in a way that sticks
Read more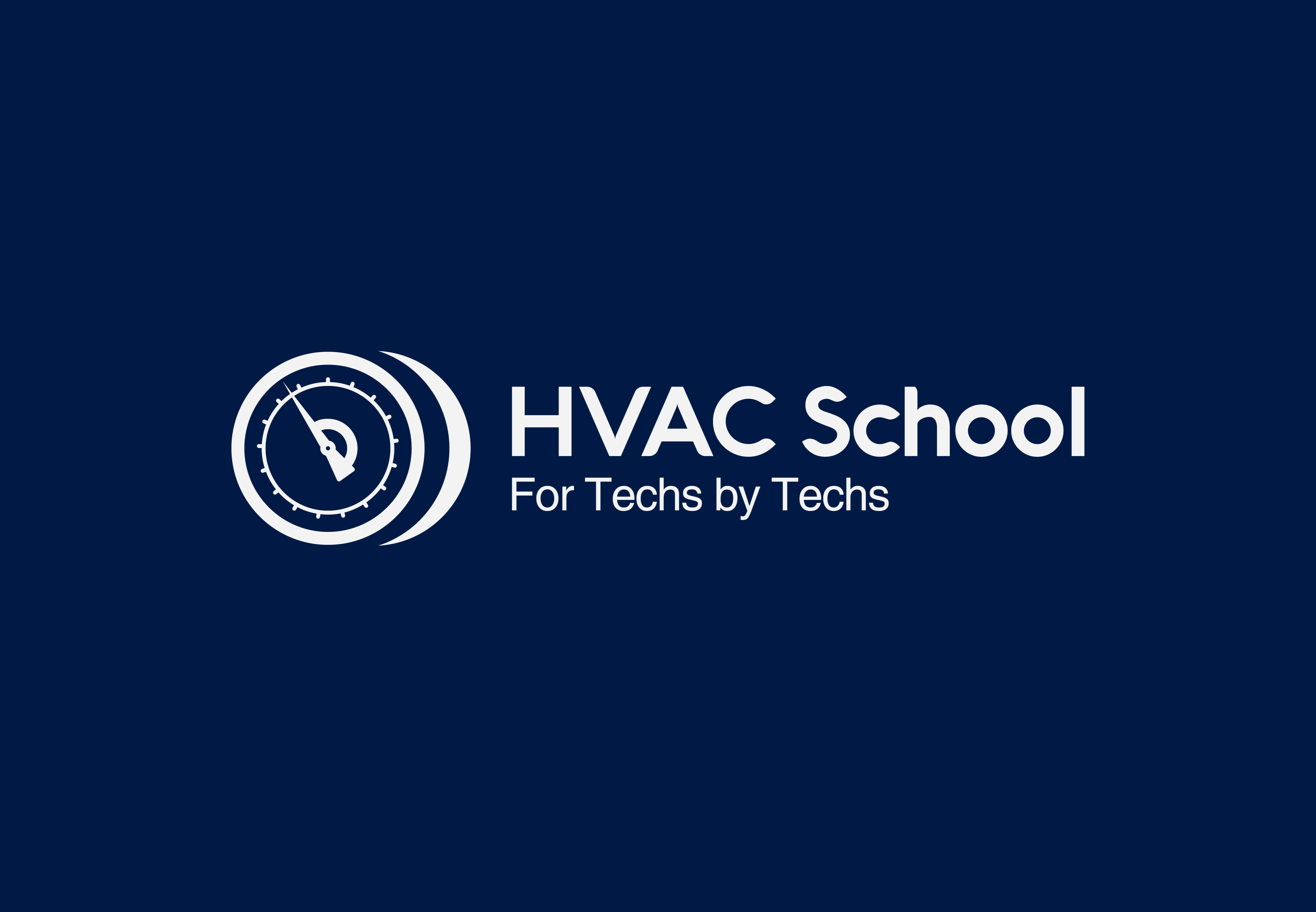
This short episode is a review of a list of installation reminders made by Kalos manager Jeff Crable for a bunch of installs we are doing for a commercial customer. I thought it was a nice list and worth going over here. Enjoy
Read more
When you ask many people nowadays how to check the charge on a heat pump during low outdoor temps, they will say that you need to “weigh in and weigh out” the charge. While this may be an effective method, it isn't always practical. Now, if you are making a refrigerant circuit repair, weighing out […]
Read more
I'm far from a country boy, but I did grow up in a rural area with animals, playing in the woods, and cleaning out chicken coops. Like many of you, we would play most of the day outside without our parents knowing or worrying about where we were. Was that an “unsafe” way to grow […]
Read more
Note: This short series is on the mindset of learning (and teaching), not really a “tech tip,” per se. We will be back to the tech tips in a few days. I've heard and repeated these phrases countless times over the years, both at home and work: That should be obvious. It's just common sense. […]
Read more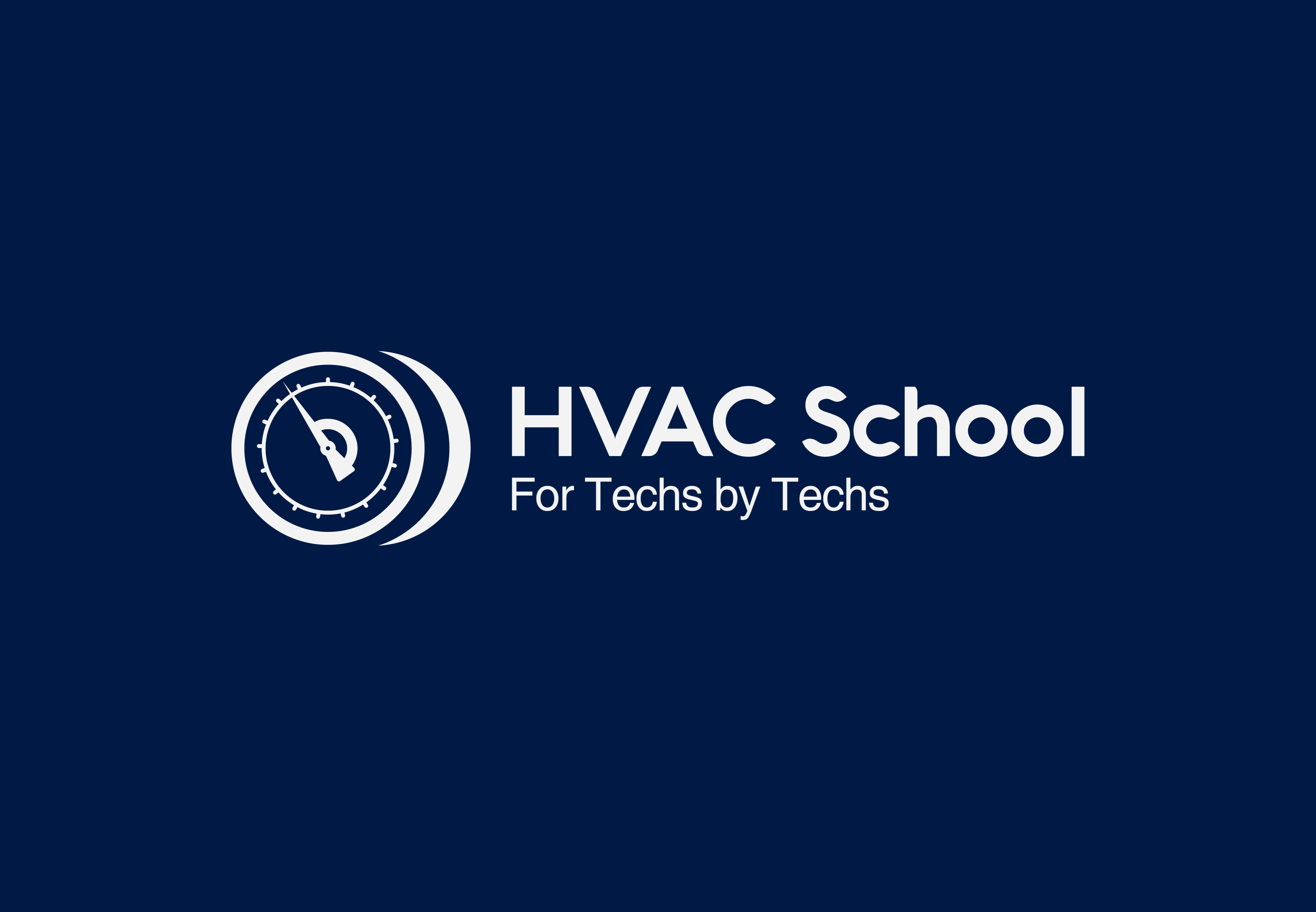
In this face to face discussion Bryan and Kaleb share some tips for diagnosing and replacing reversing valves
Read more