April 2020
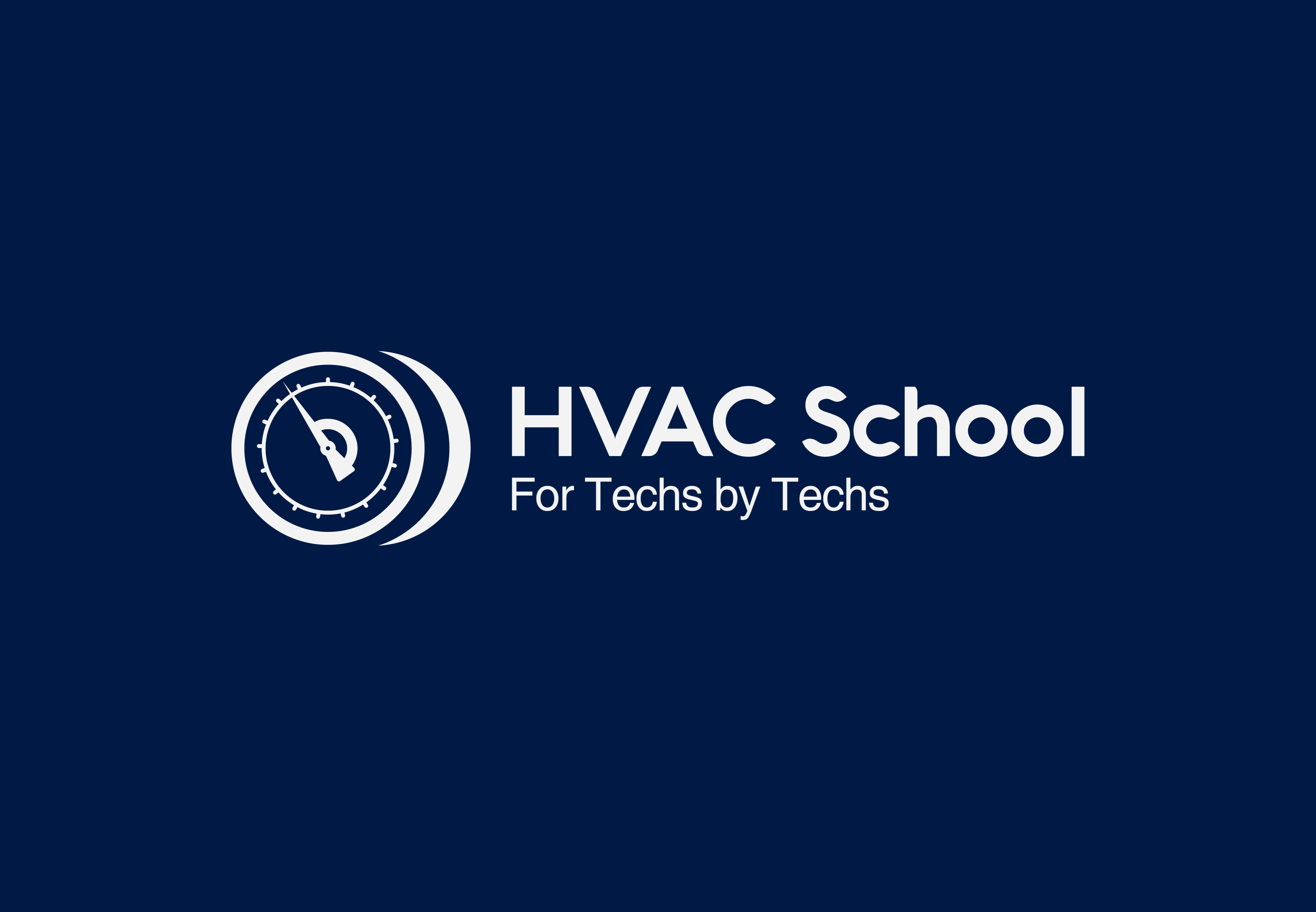
Bryan and Kaleb talk about the properties of air and discuss dry bulb, wet bulb, dew point, and relative humidity
Read more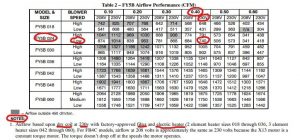
Many installers and service technicians know how to read and use a manufacturer fan table, but this is a quick review with a few extra tips for newer techs. It’s also a good reminder to senior technicians about how this easy-to-use practice can also be easily abused. At installation, properly setting up airflow is imperative to the […]
Read more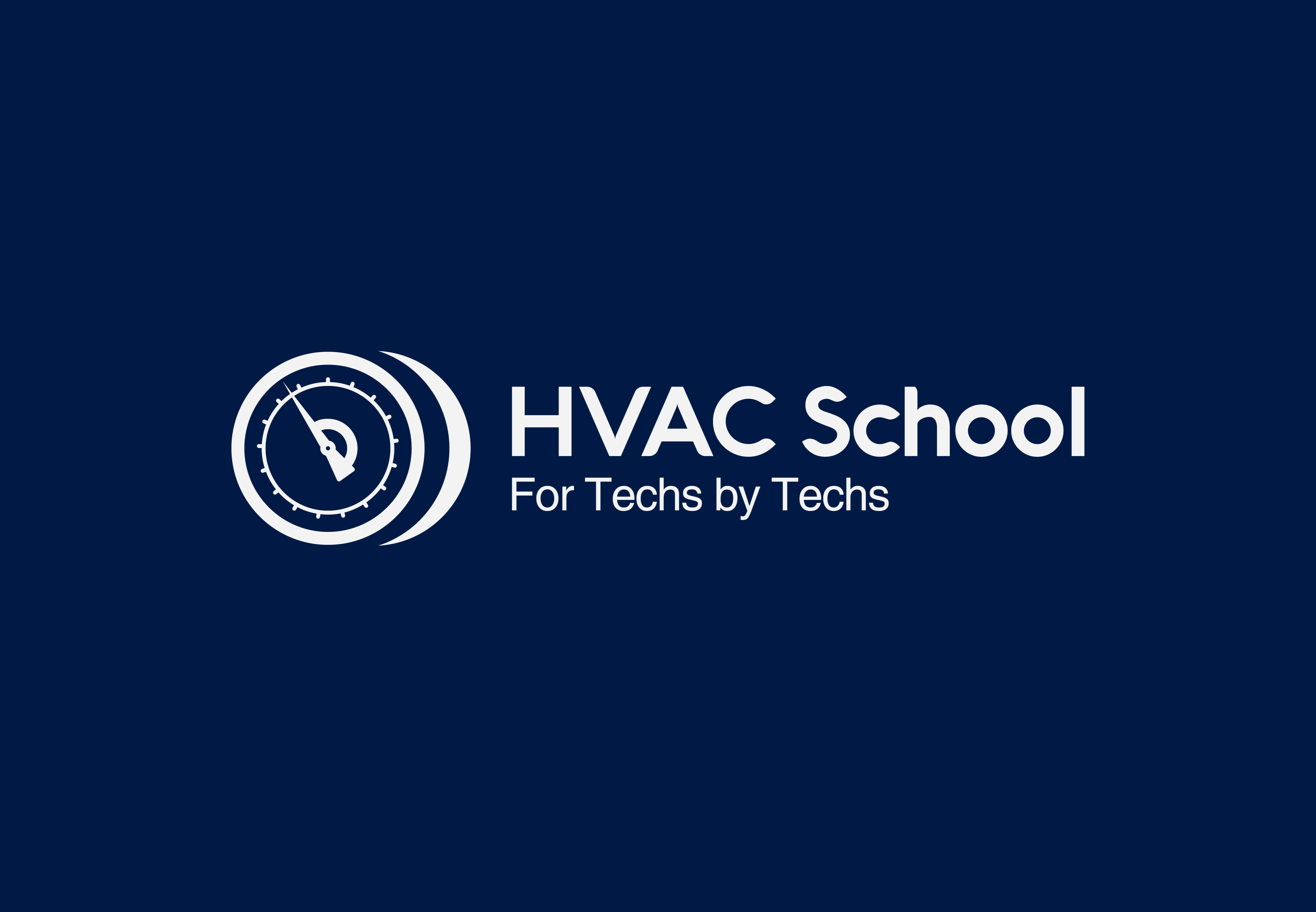
Many contractors confuse markup with margin and it can lead to the difference between being profitable and losing it all.
Read more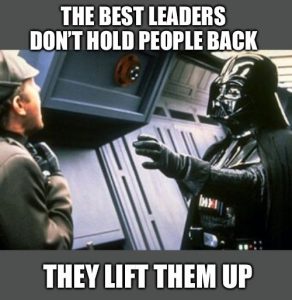
Business isn’t easy. Generally, when I look back at how much work it has taken to get a business off the ground, I wonder what I would have done if I had known what I know now. I wonder if I still would have been willing to put in all that work all over again. […]
Read more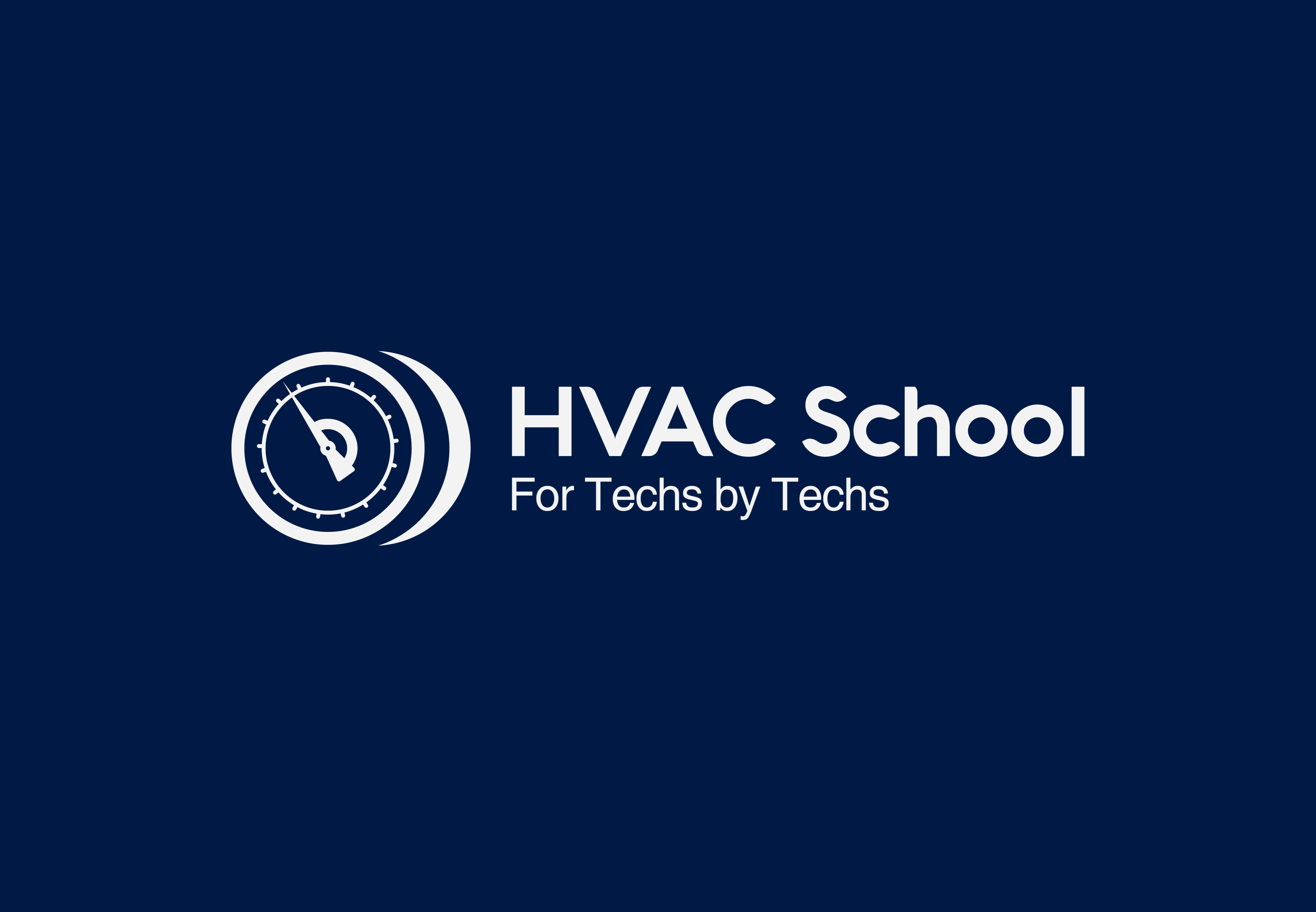
Ron comes on and answers questions about UVC and pulls no punches
Read more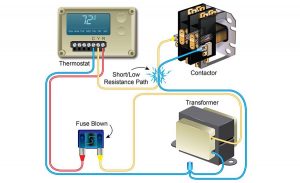
Newer technicians often get hung up and frustrated when searching for low voltage shorts. This is understandable due to the broad spectrum of possibilities for the location of the short. However, this doesn’t mean that the process needs to be complex. The time it takes to find a low voltage short may vary greatly depending […]
Read more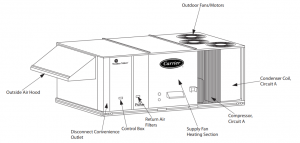
If you are primarily a residential technician working on equipment under 5 tons, there are many similarities between the systems you are used to and 5-20 ton rooftop units common to the light commercial market. There are MANY additional things to consider on larger equipment, and here are just a few. Wash Fresh Air Filters […]
Read more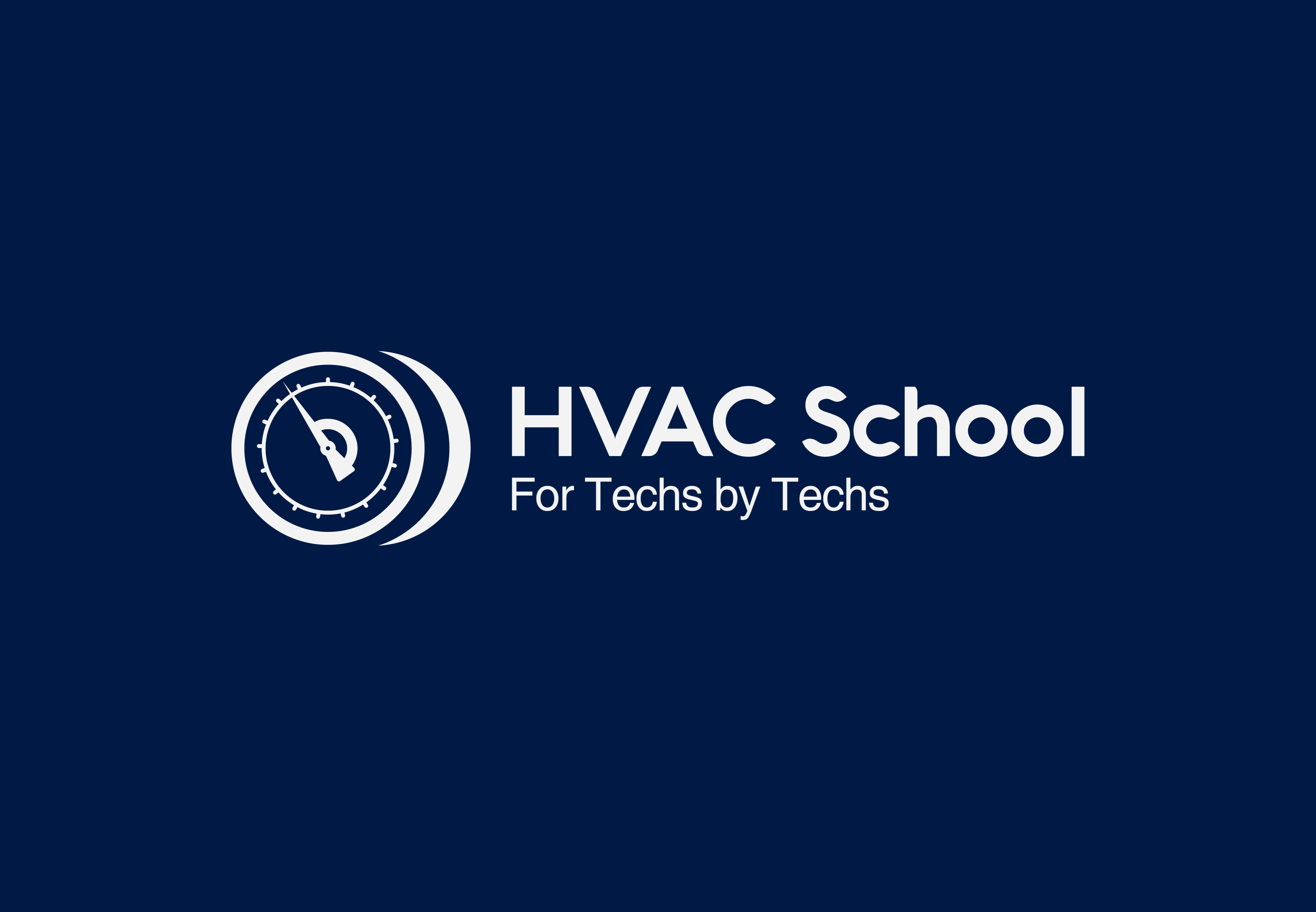
In this free-flowing conversation, Trethewey talk about growing up with This Old House, what the show is like behind the scenes, what Rich misses about the past, what the future holds for the trade and some nerdy specifics between Bryan and Ross. Thanks to Richard, Ross & Evan for making this happen. Check out […]
Read more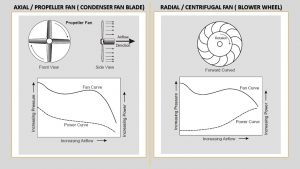
Fan laws and fan curves are a deep subject with a lot of nuance and variation. Just to get our heads around the subject, let's focus on two different types of fans that we see all the time in HVAC: the prop/axial type and the radial/centrifugal type. Centrifugal/Radial As we increase the pressure differential across […]
Read more