May 2020

I didn't install this unit. First off, attic installations are among my least favorite applications from the standpoints of serviceability, system longevity, and a laundry list of other items. Here in Florida, it's just a bad idea due to the high humidity and temperature in a vented attic and the condensation issues that can and […]
Read more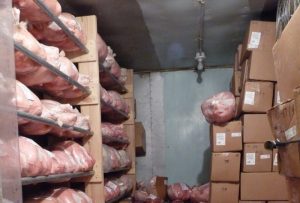
If you work in refrigeration, you may have heard the term “hot pull down.” This phrase describes a condition where the load on the evaporator is above design due to the box temperature or the temperature of the product in the box being higher than it would normally be. My grandpa called me a few […]
Read more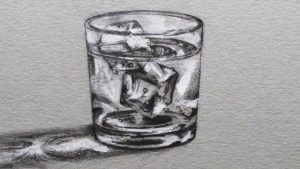
Imagine a glass of ice sitting on a table. Now, imagine you place a lid on the glass so that all the water and ice are contained in the glass. If the ice and water are well mixed, the water and ice will both be at 32°F because the ice is slowly changing state from […]
Read more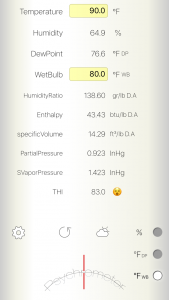
This is the second article in a three-part series where we explore advanced psychrometrics. The source material for each of the articles in this series is ACCA Manual P Sections 3, 4, and 5. This article is based on information found in Section 4. If you followed the previous advanced psychrometrics article, you now know […]
Read more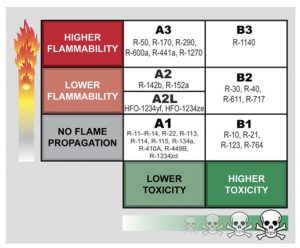
There has never been a more complicated and confusing time surrounding refrigerants than what we are in right now. We are seeing flammable HC (hydrocarbon) refrigerants with increasing regularity, and EPA rules that just changed appear to be changing again. With all this tumultuous change, it's important to know what to look for in refrigerants […]
Read more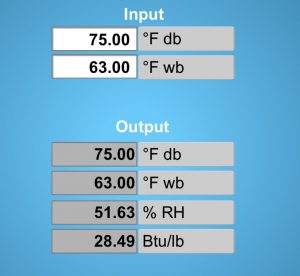
This is the first of a three-part series of articles that will dive deep into advanced psychrometrics. The source material for each of these articles may be found in ACCA Manual P Sections 3, 4, and 5. This article is based on information found in Section 3. Psychrometrics is the study of the physical and […]
Read more