February 2021
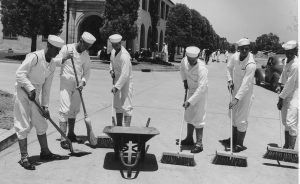
Two days prior to this article being published, I sent one out about the popular fallacy that nitrogen “absorbs” moisture. That tech tip went out at 7 PM eastern time like usual, and I was sitting on the couch watching something on the Food Network (as usual). At 7:10 PM, I get a call on […]
Read more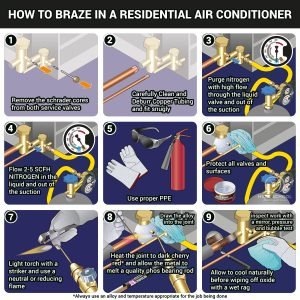
When we install systems, we should have three main goals in mind: maximizing longevity, efficiency, and capacity. We want our units to work as long as possible, use the lowest amount of energy, and move the greatest amount of BTUs possible with a proper mix of sensible and latent heat transfer. Unfortunately, some installation practices […]
Read more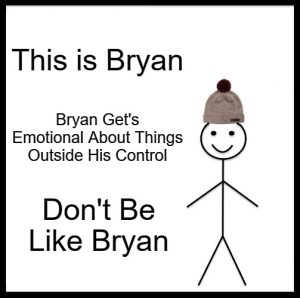
In our line of work, it's all too easy to let your bad experiences inform your present and future experiences. That is especially true if you have a high emotional range. Having “emotional range” is a polite way of saying that you're a bit up and down (maybe even neurotic). We don’t believe that sensitivity […]
Read more
Full disclosure: as a technician, I was guilty of setting the fan to “on” at the thermostat for many years. I never really thought of any of the negative impacts that could happen. I wanted to circulate the air and keep air moving through the high-efficiency air filter that most of our houses had. Later, I […]
Read more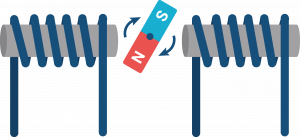
Ohm’s law is pretty straightforward; you multiply ohms by amps to get the voltage. Using variable E to represent voltage, variable I for amps, and variable R for ohms, the equation for Ohm’s law looks like this: E = I × R You can figure out the number of amps in a system using basic […]
Read more