February 2018

Measuring airflow is easy. Measuring airflow accurately is quite a bit more difficult. In many cases, when we as technicians measure airflow, we are trying to get to the almighty CFM (cubic feet per minute) volume measurement. You can take CFM readings fairly easily with a hood, like the Testo 420, but even a hood […]
Read more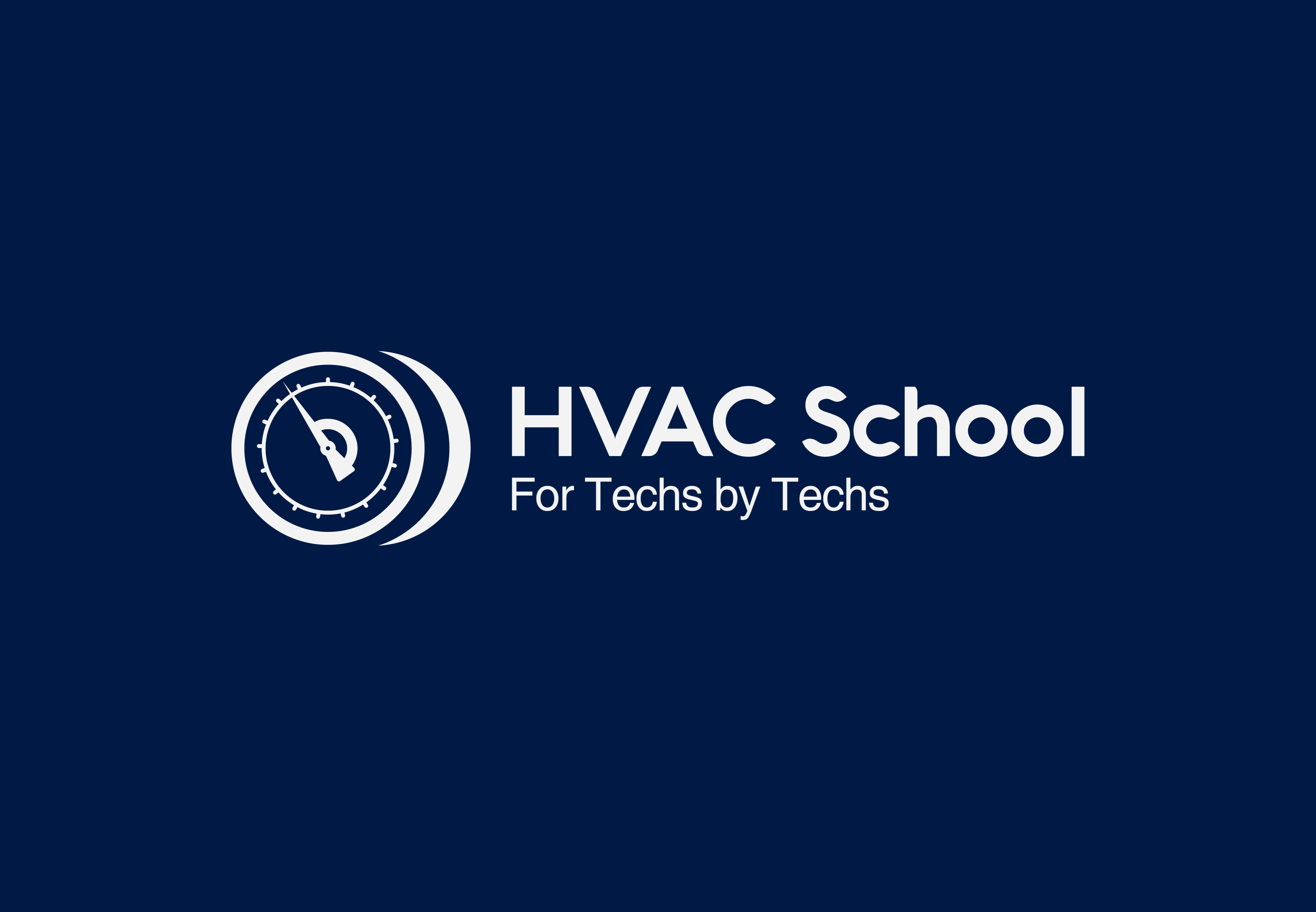
In this short episode we review the basics of the refrigerant circuit. Compressor, Condenser, Metering Device and Evaporator Find out more at HVACRSchool.com
Read more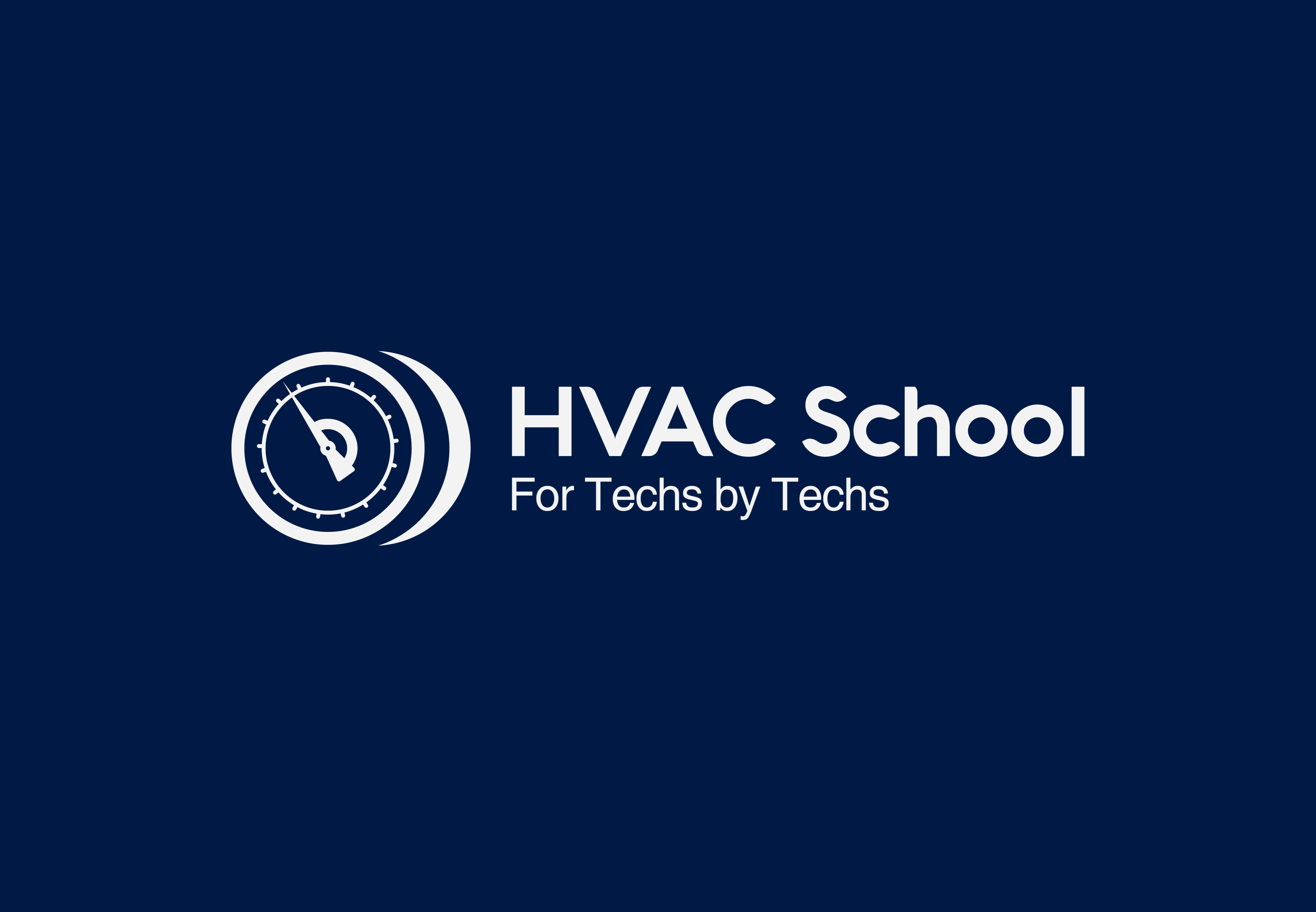
Jon Bennert from Air Oasis teaches us about PCO and Bi-Polar air purification and how it works.
Read more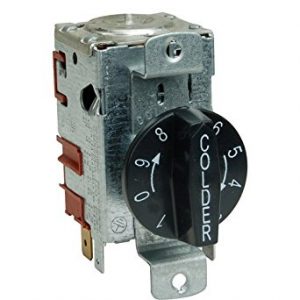
This article is written by Christopher Stephens of JVS Refrigeration in California, with just a few additions by me (Bryan) in italics. Thanks, Chris! Reach-in refrigerators are an interesting side of our industry, often looked at as frustrating and troublesome. Since we usually see reach-ins in kitchens or convenience stores, the refrigerators are never […]
Read more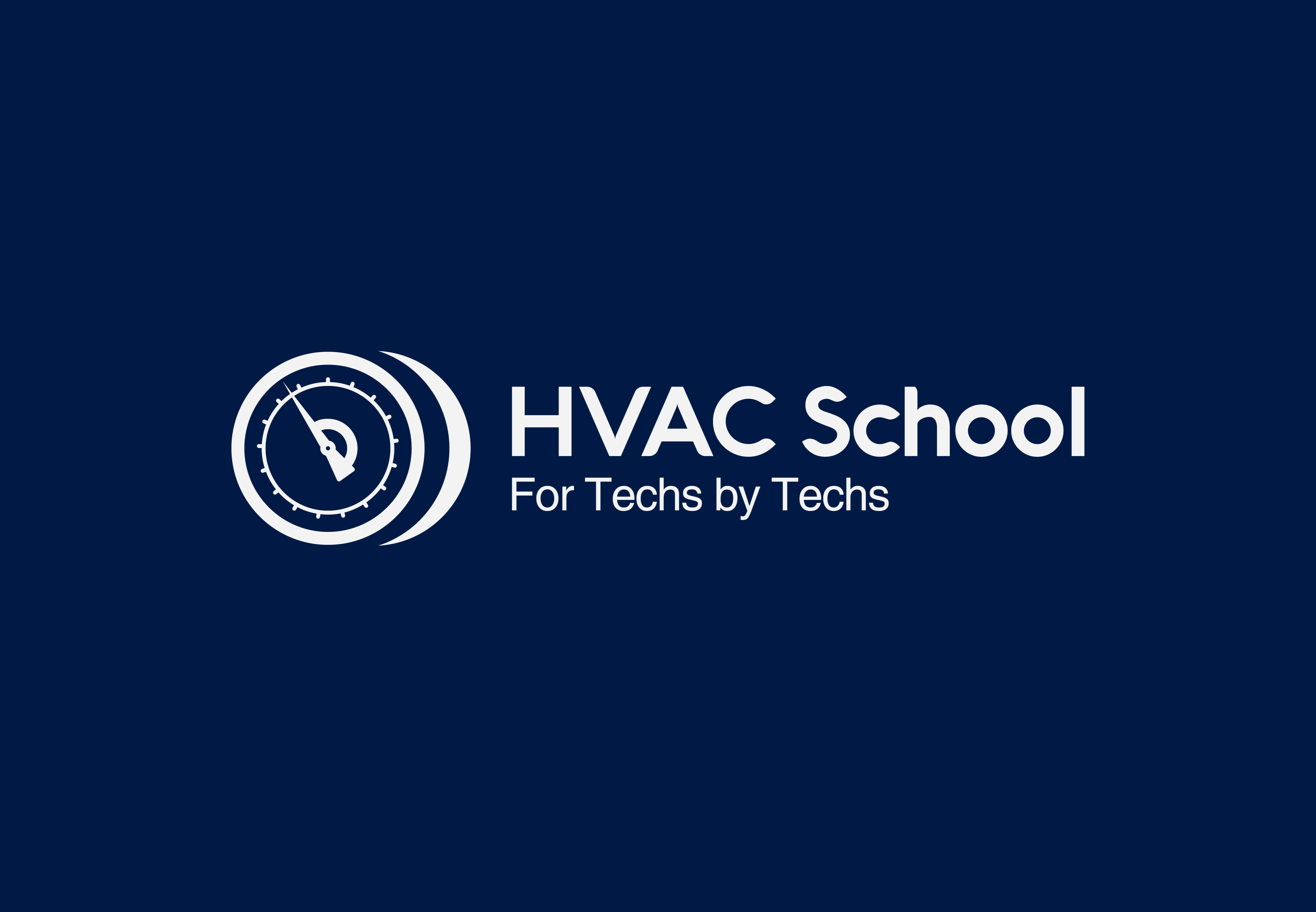
A summary of reach in coolers (refrigerators), freezers and wine coolers with some mindset and technical tips
Read more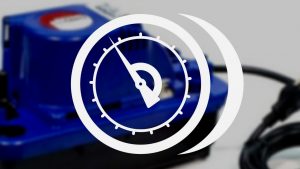
One of my techs (Jim Walch) brought another common “double trap”-style issue to my attention: techs and installers running a drain too far into a condensate pump. When you run the system drain too deep into the pump reservoir, the water level can rise high enough to cover the drain end. That can create the […]
Read more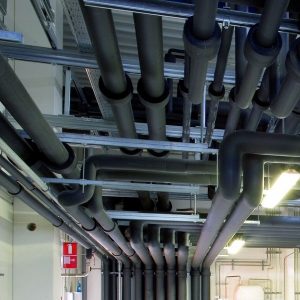
Although there are various line lift, sizing, and trapping guidelines depending on oil and refrigerant type, there is one guideline we can all understand easily and remember to apply. This guideline is to slope suction lines towards condensing units/compressors. Keeping the suction line sloped toward the compressor, especially with long overhead lines, helps return the […]
Read more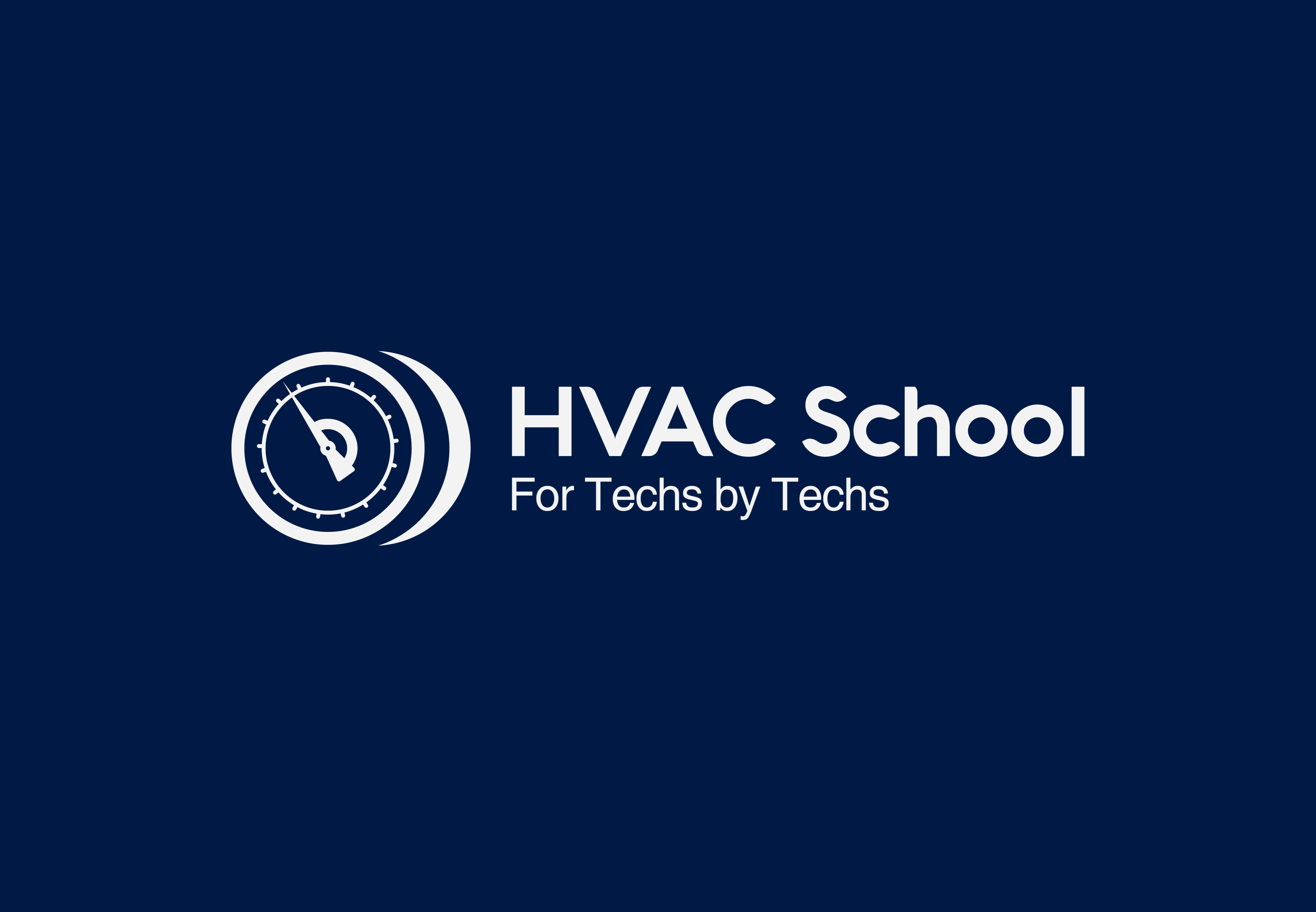
Neil and Stephen talk about their dive head-on into building performance and what that looks like day in and day out in an HVAC contracting business.
Read more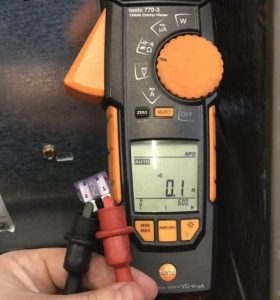
One of the most common mistakes I hear techs make is confusing zero ohms with infinite ohms. The fuse above is showing near-zero ohms, which indicates a good electrical path with very little resistance. If there is a perfect path, it would have zero ohms (which isn't actually possible unless you happen to be […]
Read more