March 2018

Almost everyone knows that CO (carbon monoxide) is really nasty stuff and nothing to play around with. Humans will often begin exhibiting symptoms of CO poisoning at 200 ppm (parts per million) of CO in a space. Studies have also shown that the effects of CO exposure can accumulate over time, resulting in health […]
Read more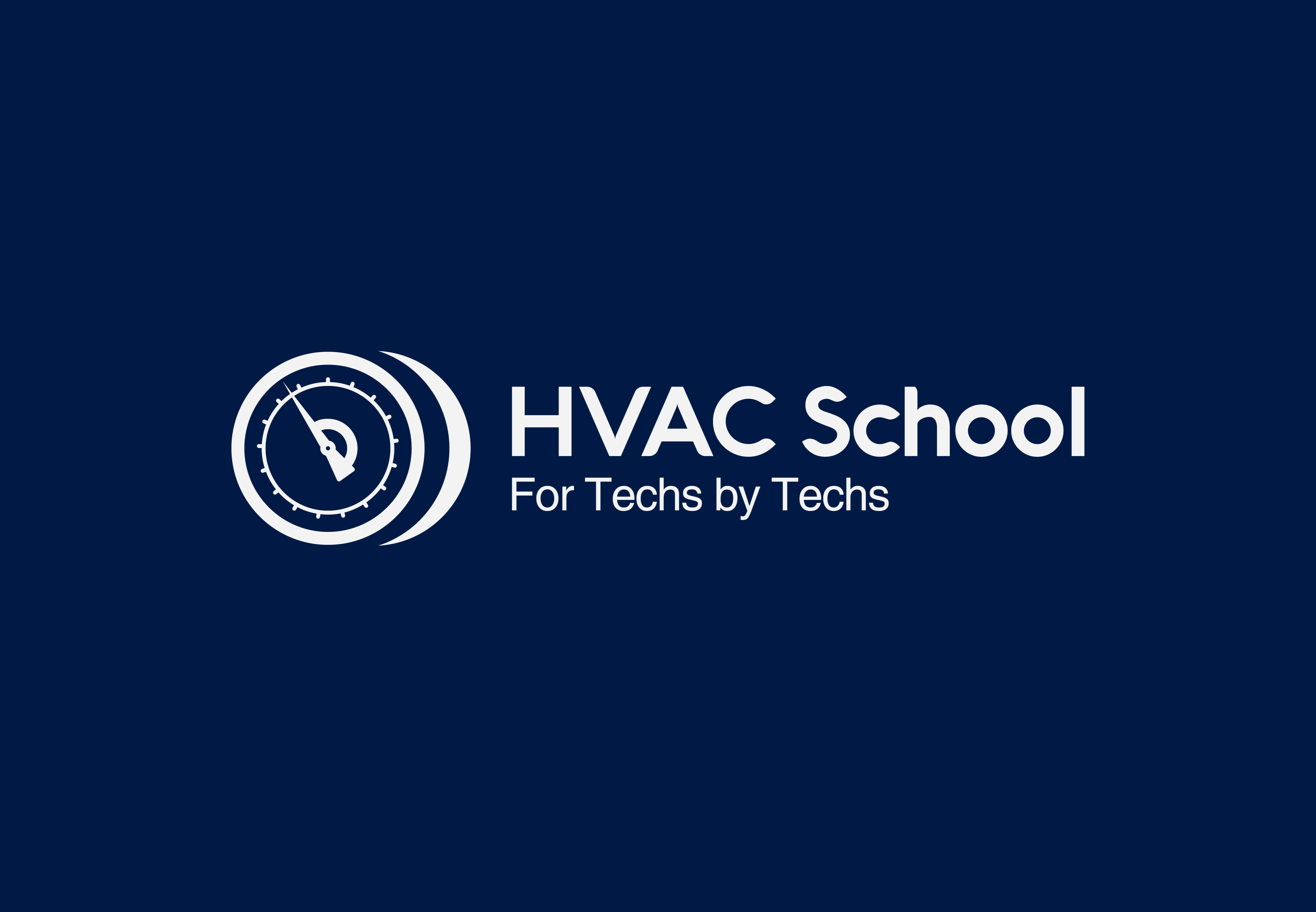
Eric Mele talks us through some common characteristics of walk-in freezers and refrigerators
Read more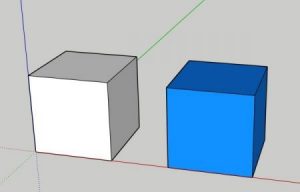
Here is part 2 from Michael Housh from Housh Home Energy in Ohio. Thanks, Michael! This is part two in a series on a deeper look into the sensible heat rate equations. You can find the first article here HERE if you missed it. This article will dive deeper into the density of “standard air” […]
Read more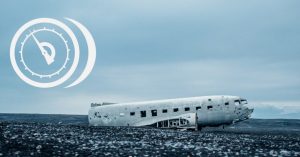
One of the most common questions we get from techs is about using a voltmeter to diagnose a high voltage circuit. It's especially tricky when a tech is used to working on a low-voltage or 120V circuit, where there is a clear “hot” side of the circuit and a clear “grounded” side of the circuit. […]
Read more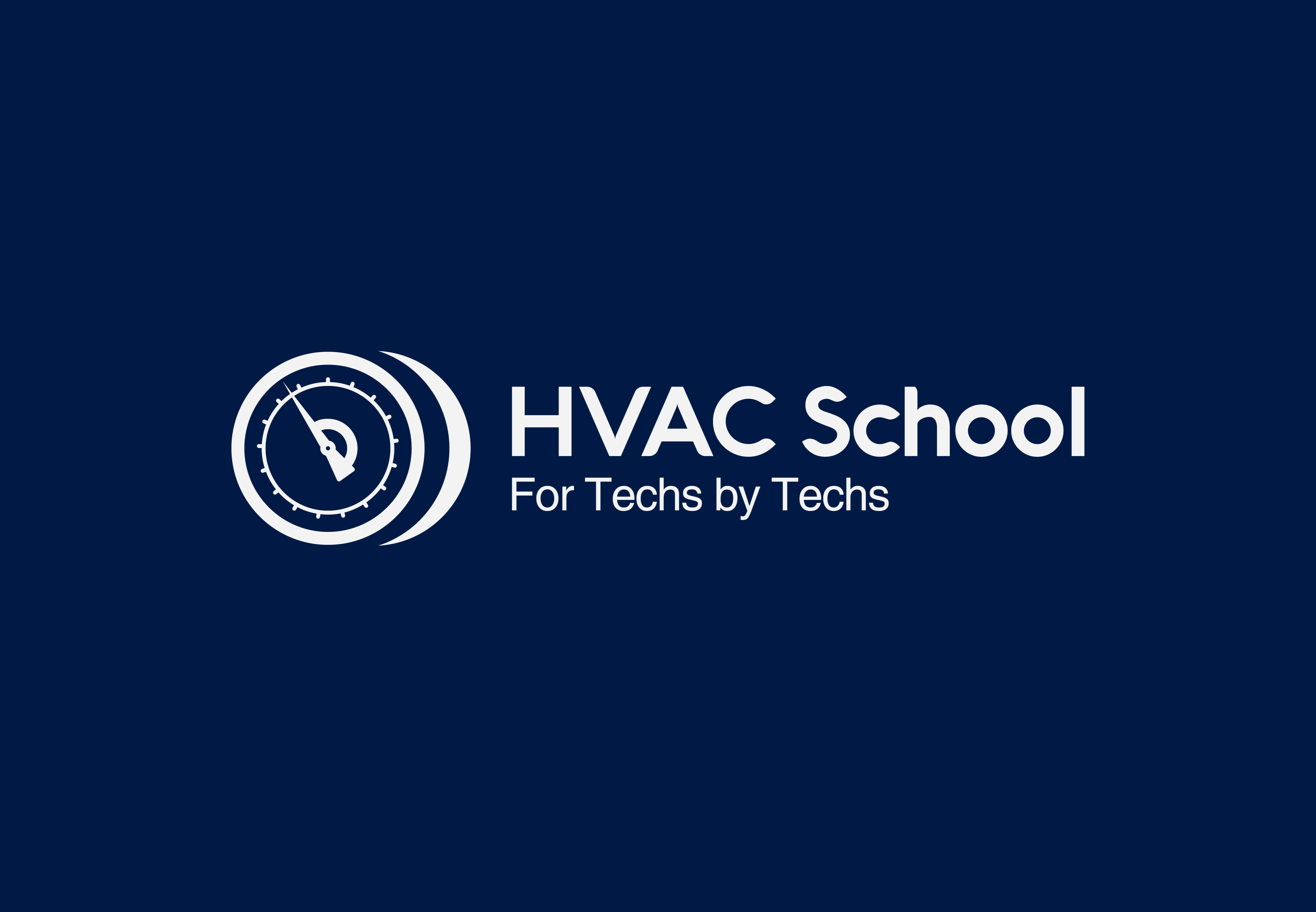
In this episode we cover some basic best practices for wiring and wire connections
Read more
We had a situation a few months back where we needed to monitor amperage on a grocery store panel over a period of time. The trouble was that we needed data-logging capability AND accurate measurement at 600+ amps. Finding an all-in-one solution proved to be quite expensive. Luckily, my friend Jim Bergmann happens to own […]
Read more
Note: My brother Nathan wrote this a few years back, and I only did some minor editing. A pool heat pump is essentially a water-cooled air conditioner in reverse. It usually has a large air evaporator on the outside that looks like a condenser coil and a heat exchanger (usually tube-in-tube) on the inside. A […]
Read more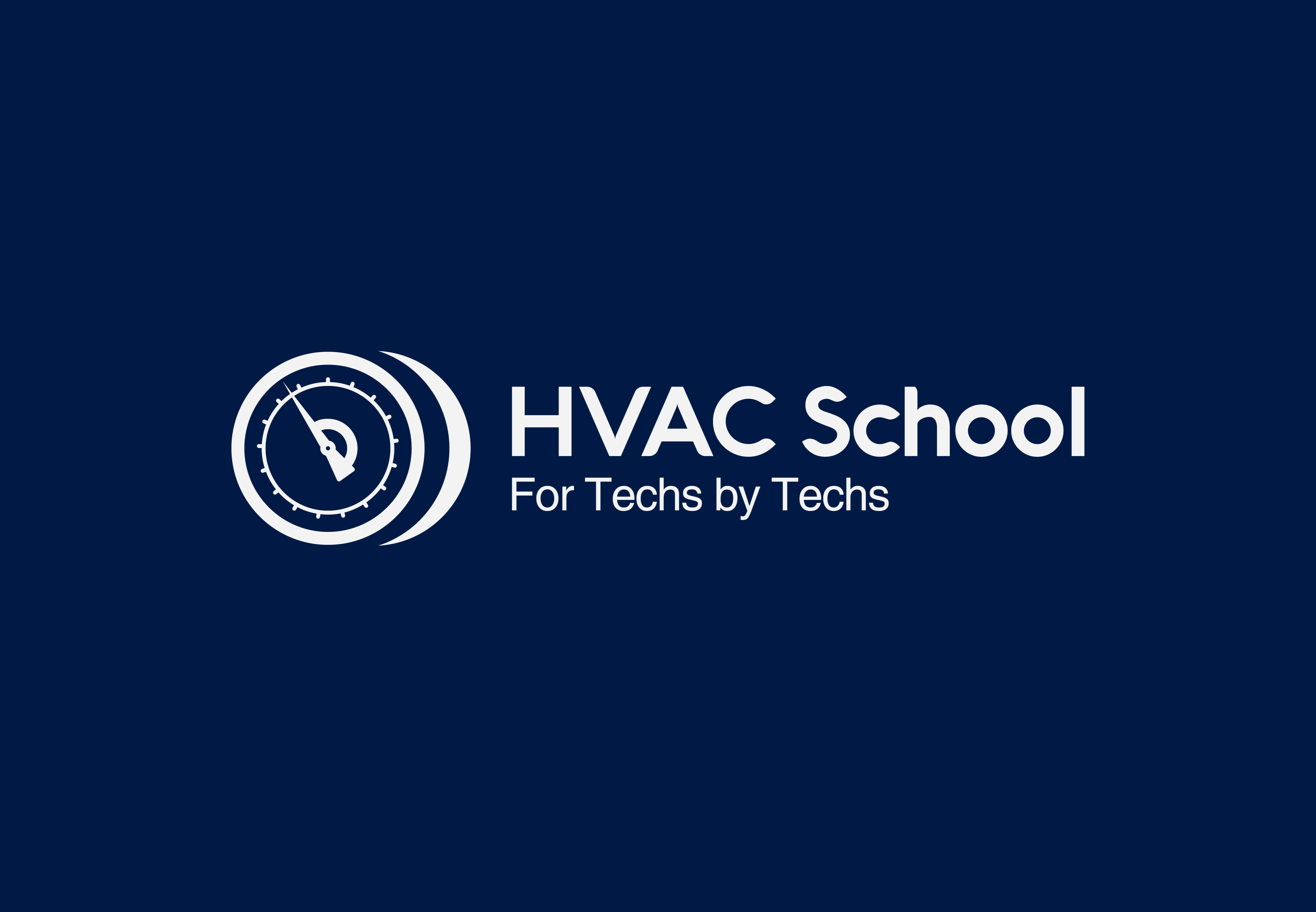
Jim covers the basics of furnace commissioning in more detail with some common sense practices
Read more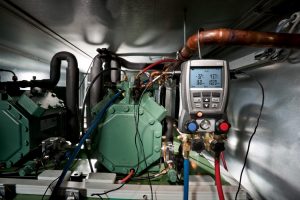
This article was written by Senior Refrigeration Tech Jeremy Smith. Before we get to it, I want to remind you that ALL of the tech tips are available in chronological order HERE, and you can sort through them alphabetically by selecting the letters and numbers above the tips. It's a great link to share with […]
Read more