March 2018
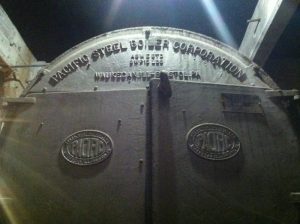
Here is another great explanation from Michael Housh of Housh Home Energy in Ohio. Thanks, Michael! I’m going to lay out and compare the sensible heat rate equations for both the air-side and water-side of HVAC to help draw similarities and dive deeper into the science behind these equations. This is the beginning of a […]
Read more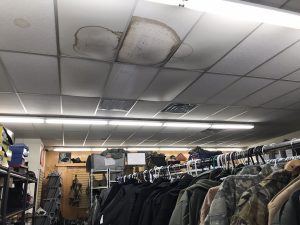
This tip was written by a 19-year service tech, Frank Mashione. Thanks, Frank. Here is a tech tip from the field that had stumped me. Luckily for me, I knew the right person to call to get back on track. This business has complained about heat calls for quite a while. I have heard other […]
Read more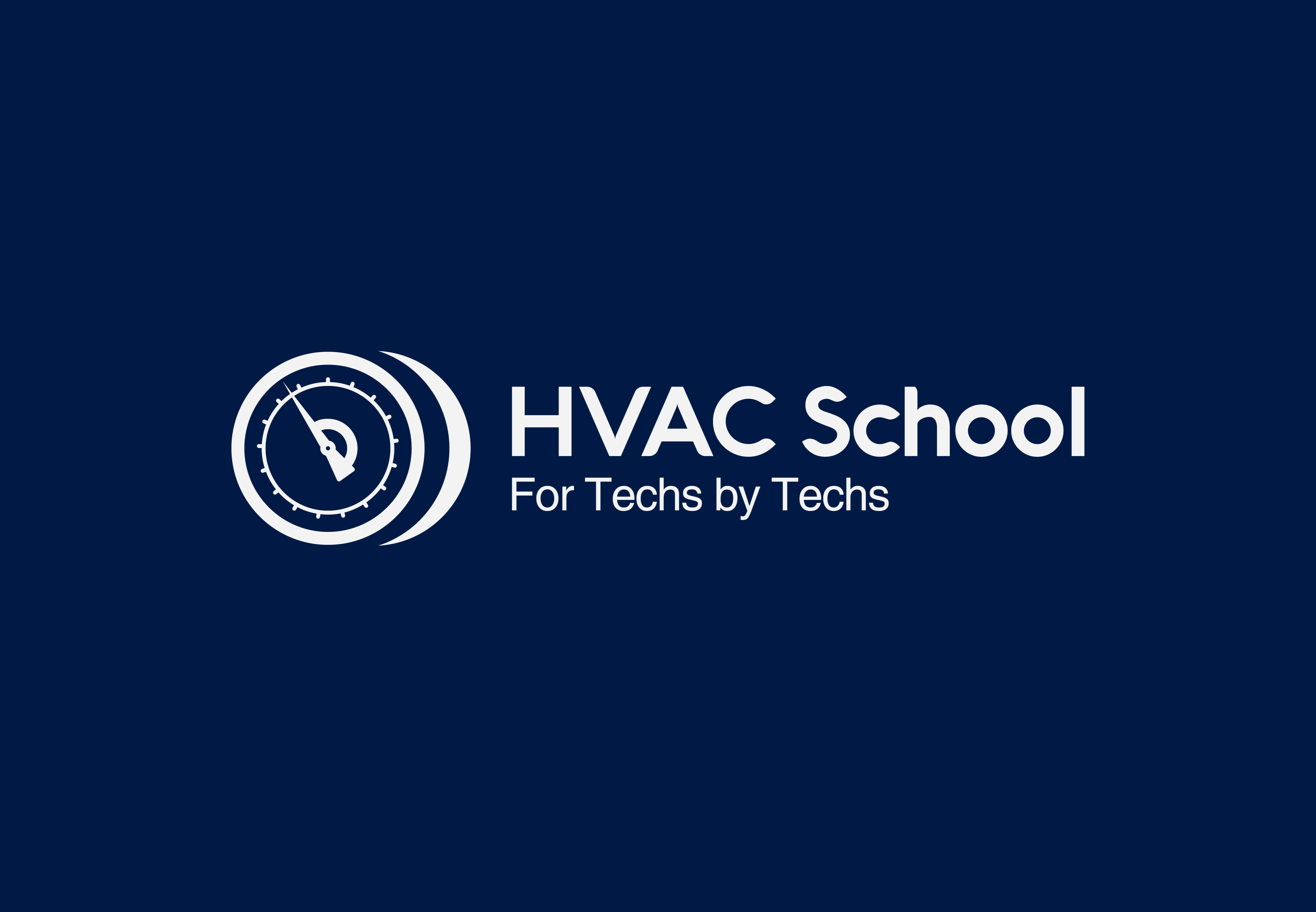
Jim covers setting up furnace input, clocking the meter, setting temperature rise and much more
Read more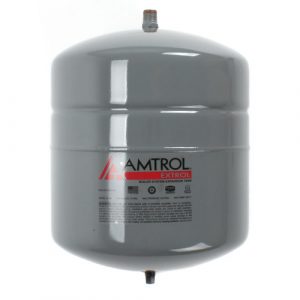
Michael Housh from Housh Home Energy in Ohio wrote this tip to help techs determine the air-side charge on a pressure tank. Thanks, Michael! Determining the air-side charge of an expansion tank in a hydronic heating system is a relatively easy task. A properly sized and charged tank is designed to keep the system pressure […]
Read more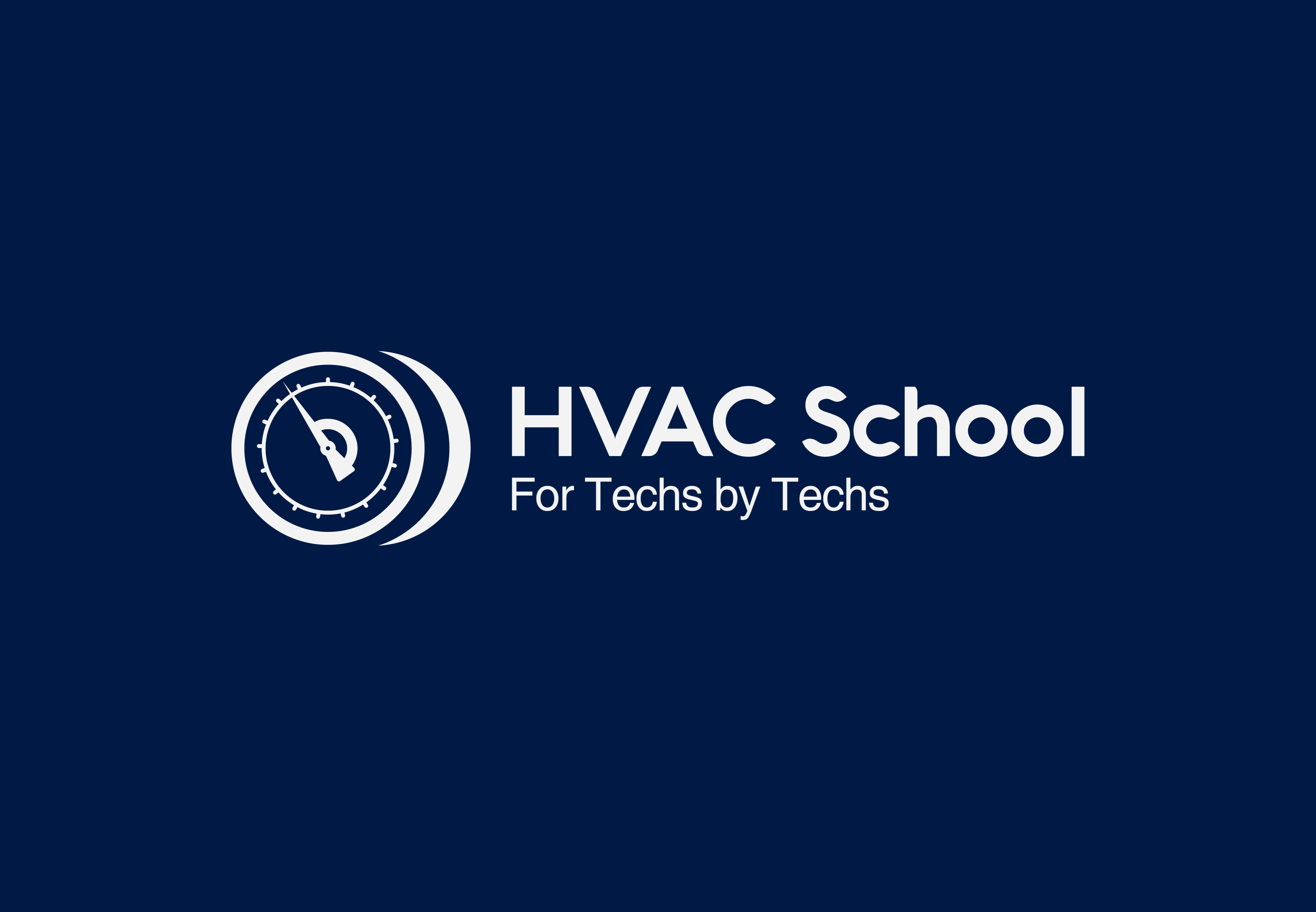
This episode is about saturation and what it means including boiling, evaporation and condensing.
Read more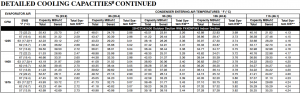
This tip was a COMMENT on the sensible heat ratio tip left by Jim Bergmann. As usual, Jim makes a great point; once you get the “sensible” capacity for a piece of equipment at a set of conditions, you can easily calculate a true target delta T. Another interesting thing you can do is use […]
Read more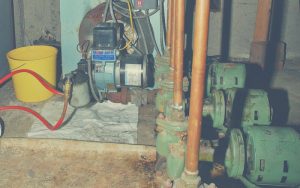
This tech tip was written by a friend of HVAC School, Brian Mahoney. He is an HVAC instructor at Western Suffolk BOCES/Wilson Tech. Thanks, Brian! The podcast on delta T for A/C the other day got me thinking about the formula I learned in school about calculating the GPM of a hydronic system. We will […]
Read more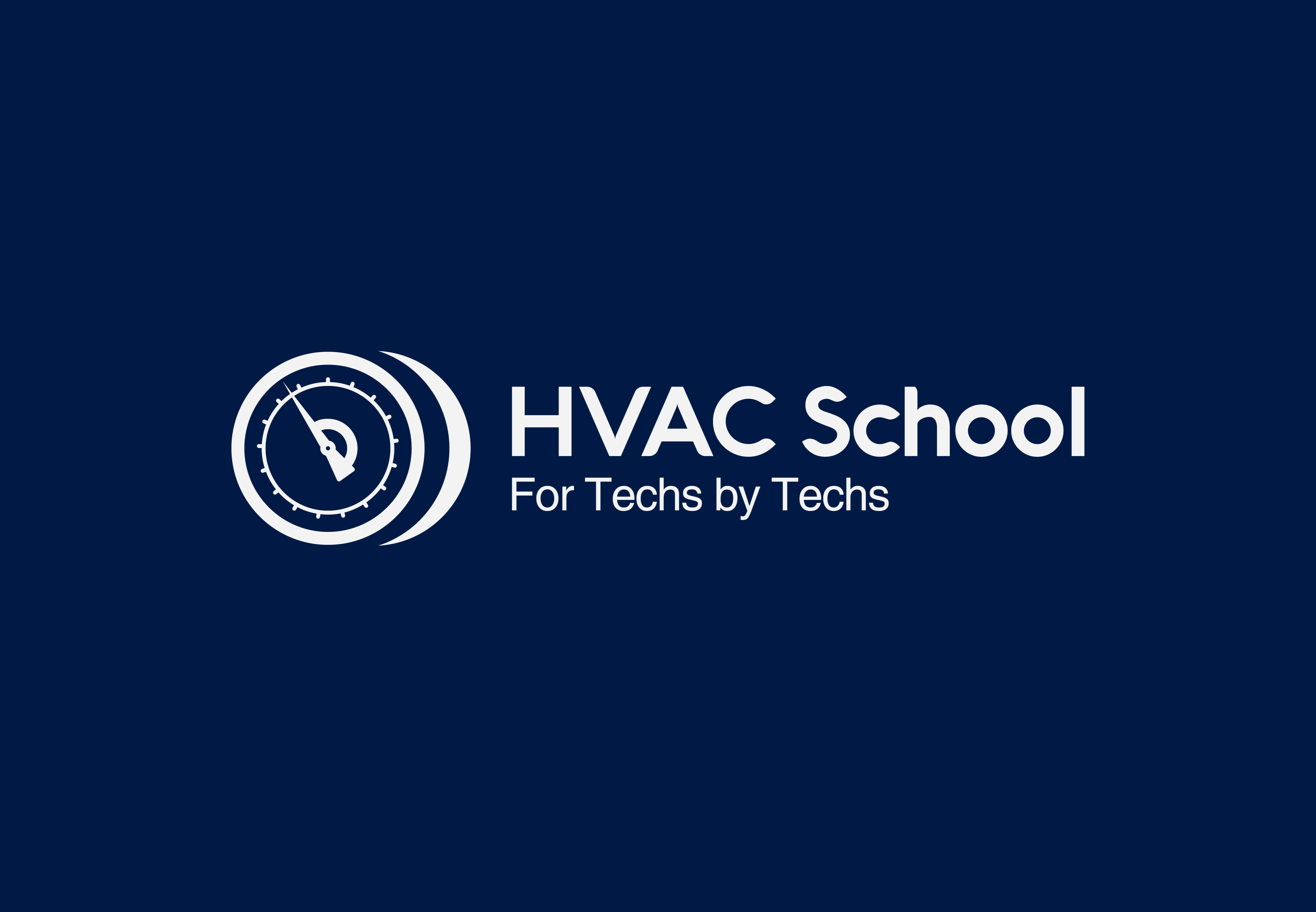
In this discussion with Bill Spohn from TruTechtools.com we cover the practical steps and tools for YOU to start measuring airflow today… if not sooner.
Read more