June 2018
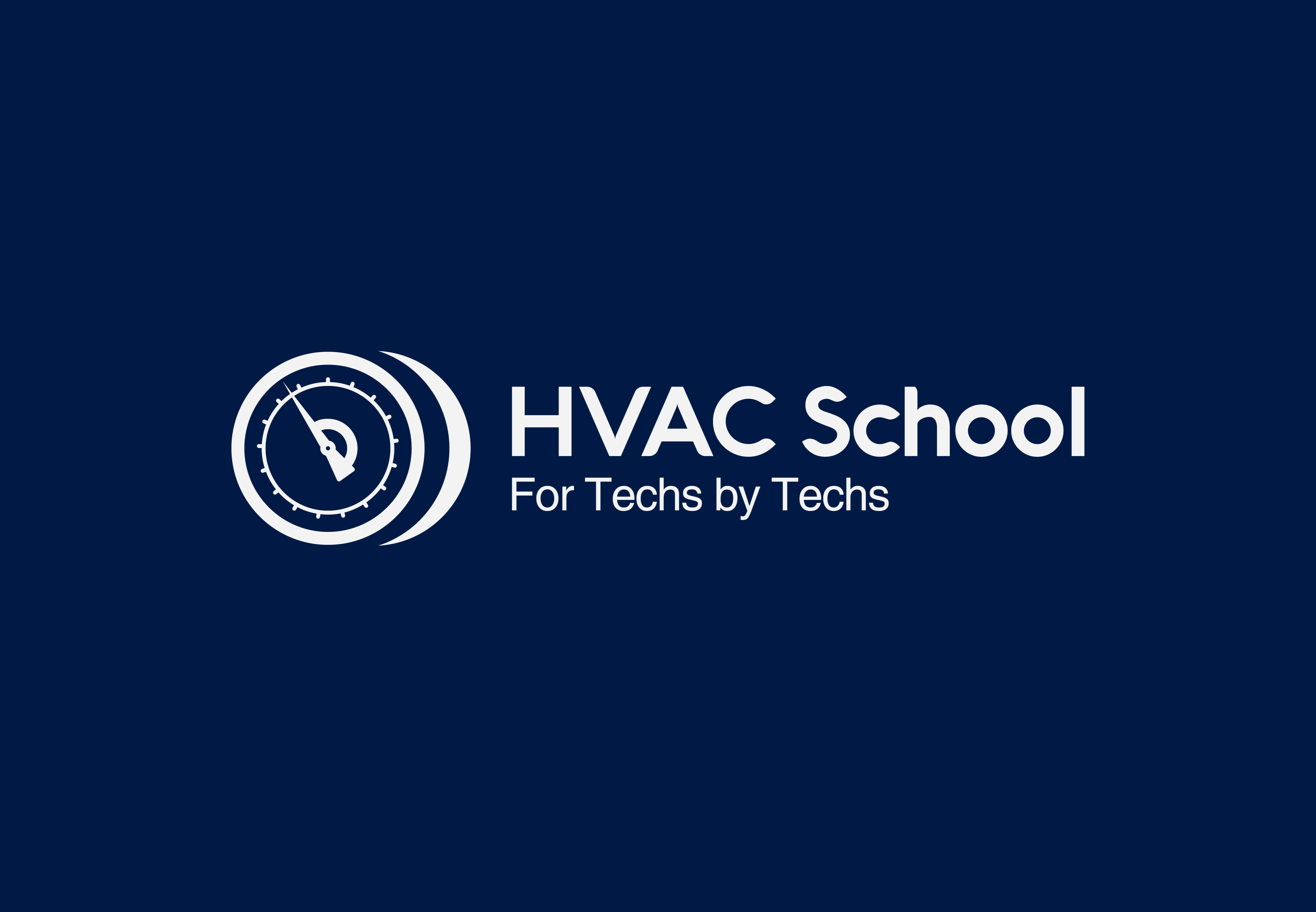
In this episode we talk air volume, density, weight and mass and why it matters to you
Read more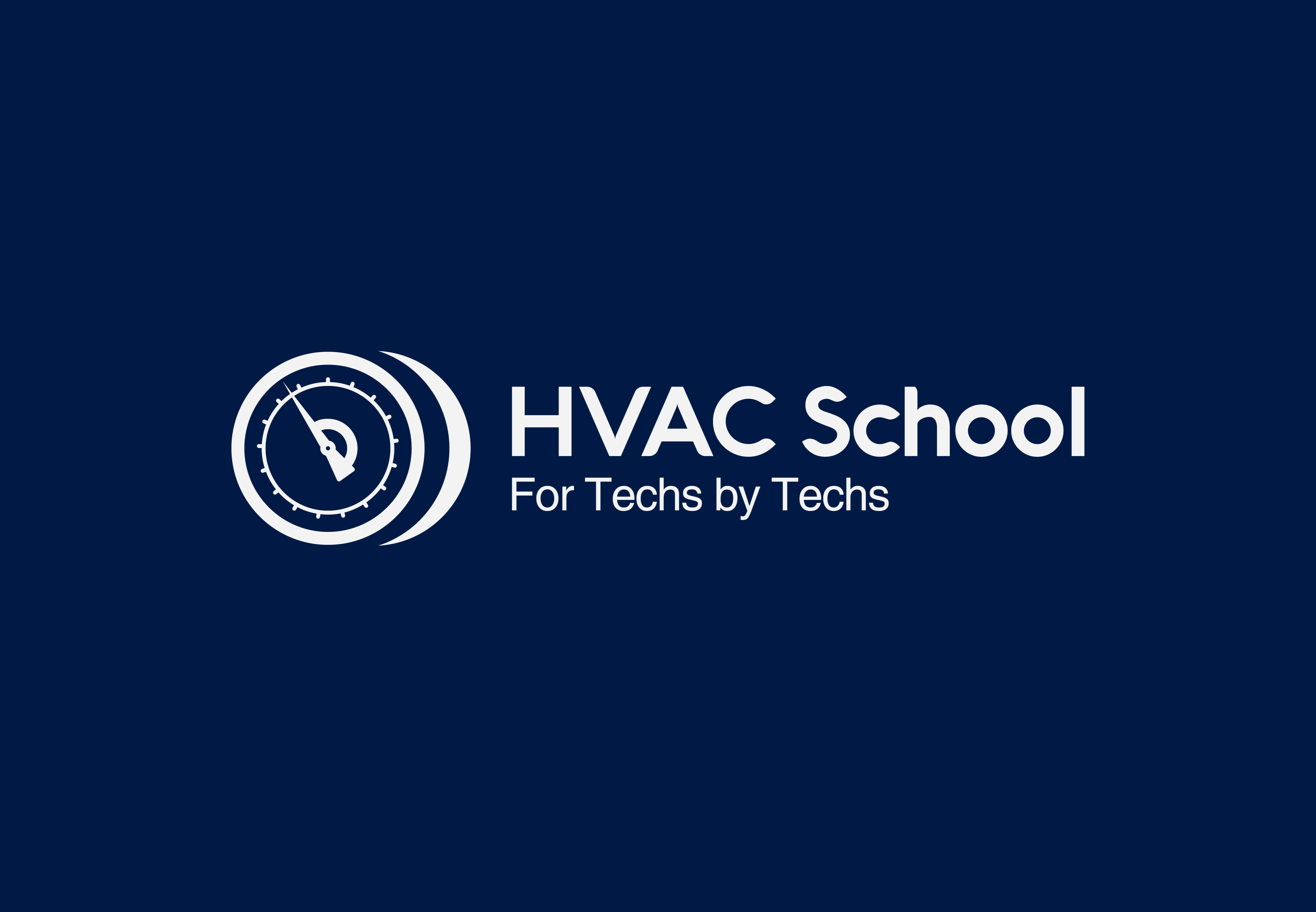
Ralph Wolf comes on and talks inverter systems, Mitsubishi, Bosch and what he’s up to nowadays
Read more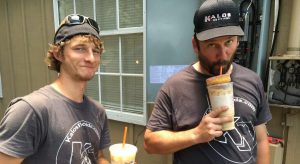
When I started in the field, I was a 17-year-old helper with one year of tech school under my belt. In other words, I knew nothing. As I've mentioned before, a few experienced techs took me under their wings at different stages, but the most influential was a guy named Dave Barefoot. For whatever reason, […]
Read more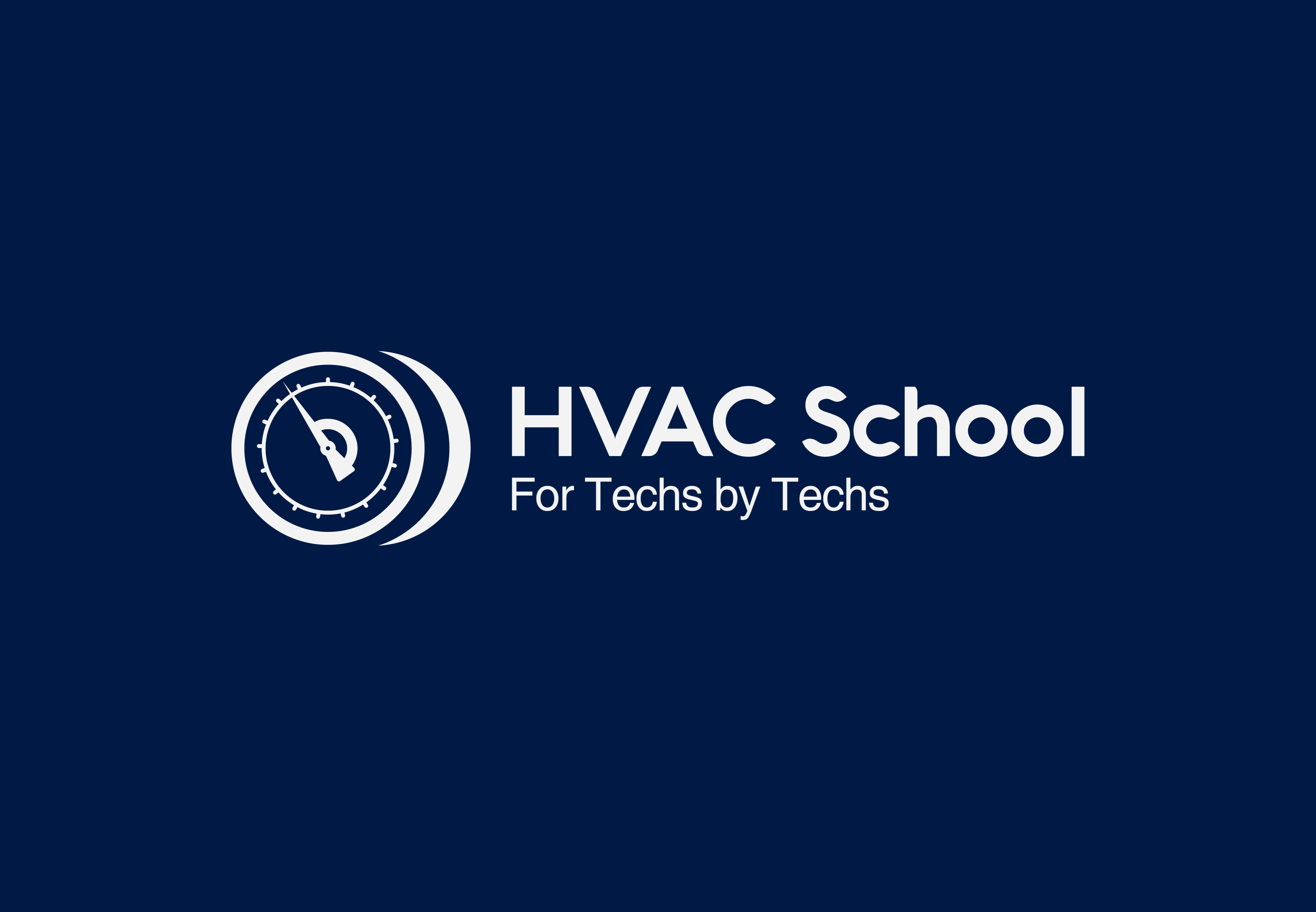
Part 2 – Bert (Kalos Tech) and Keiran (Kalos Apprentice) join Bryan in studio to talk through the basic refrigerant circuit and how it functions. They talk compressor, condenser, metering device and evaporator as well as the four lines and the states of the refrigerant as it travels
Read more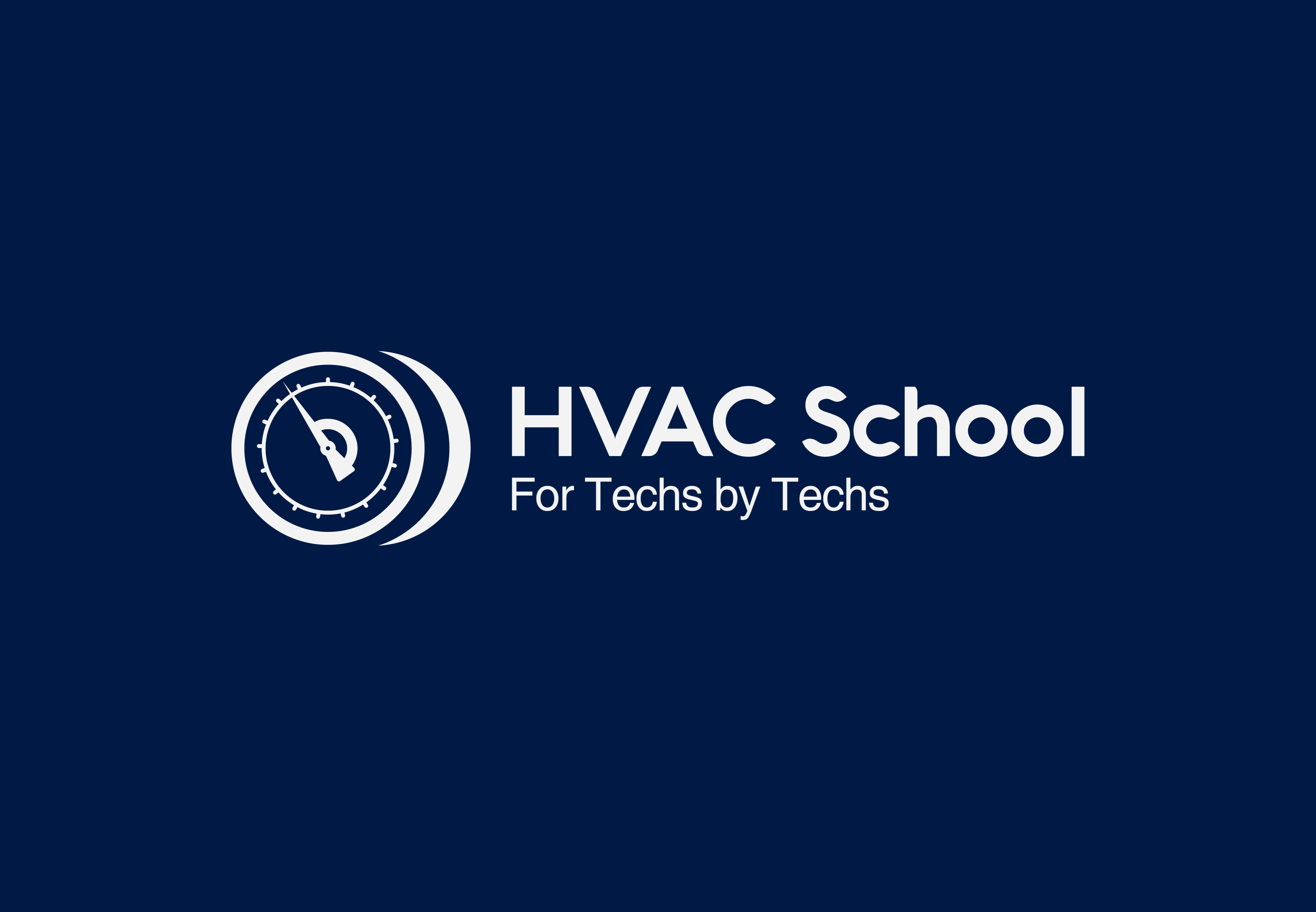
Part 1 -Bert (Kalos Tech) and Keiran (Kalos Apprentice) join Bryan in studio to talk through the basic refrigerant circuit and how it functions. They talk compressor, condenser, metering device and evaporator as well as the four lines and the states of the refrigerant as it travels
Read more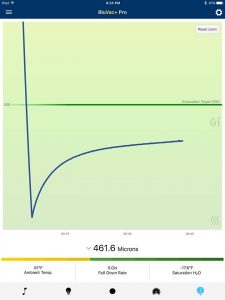
This article was written by Jim Bergmann with MeasureQuick. Anyone who has ever picked up a vacuum pump has asked or been asked this question. To be truthful, it is like asking, “How many licks will it take to get to the center of a Tootsie Roll Tootsie Pop?” In the words of the wise […]
Read more