August 2018
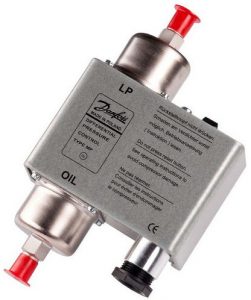
Oil pressure controls, oil failure controls, oil safety controls… They’re a pain in the neck when they trip, and diagnosing those problems can really tax even the best of techs. As semi-hermetic compressors get larger, they can no longer rely on simple splash or “sling” type lubrication strategies where oil is just flung around inside […]
Read more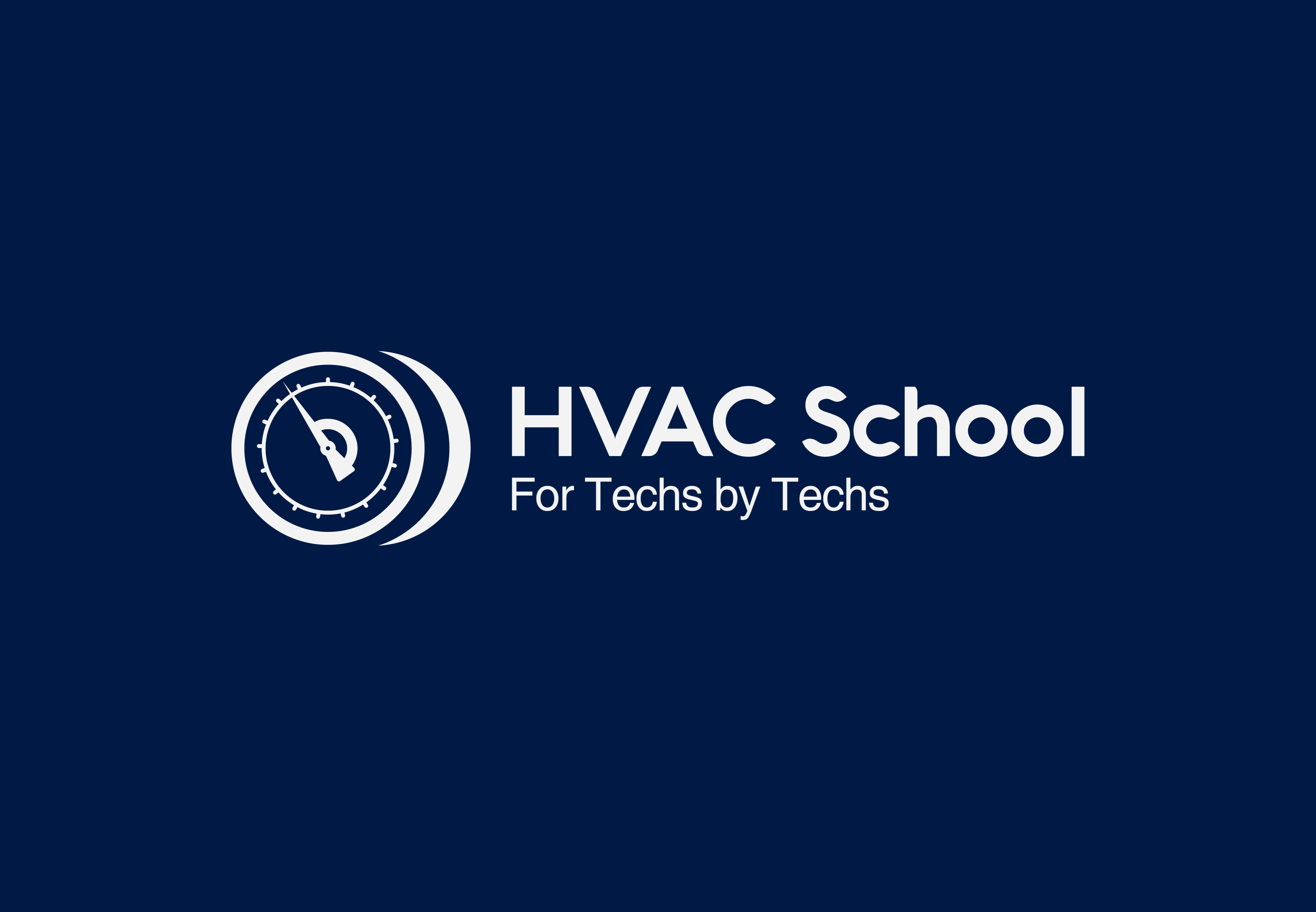
How does a vacuum pump work? When should you change the oil? What does that oil do anyway? We answer these questions and more in this episode
Read more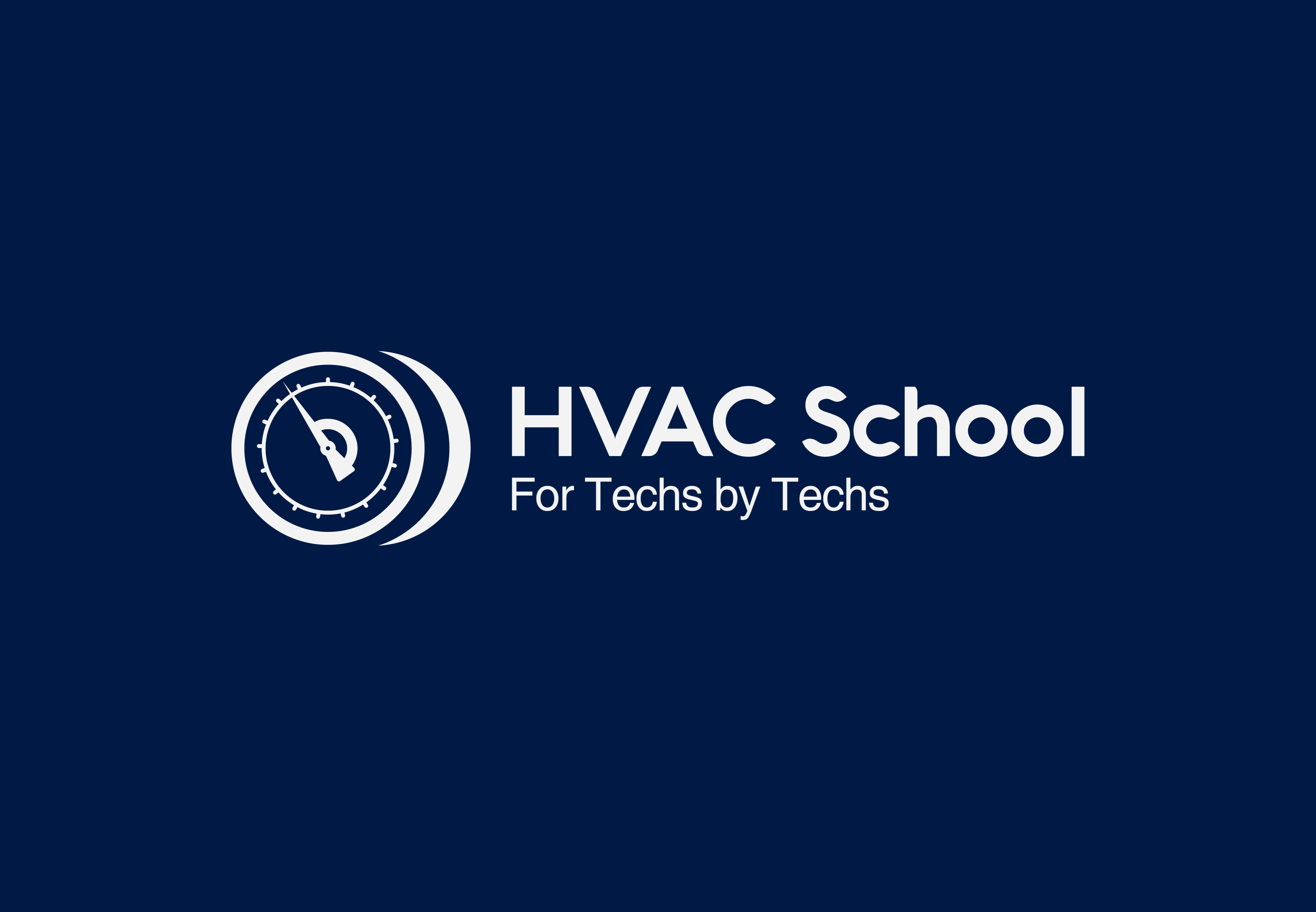
Some tips for HVAC/R service valves and caps for new technicians
Read more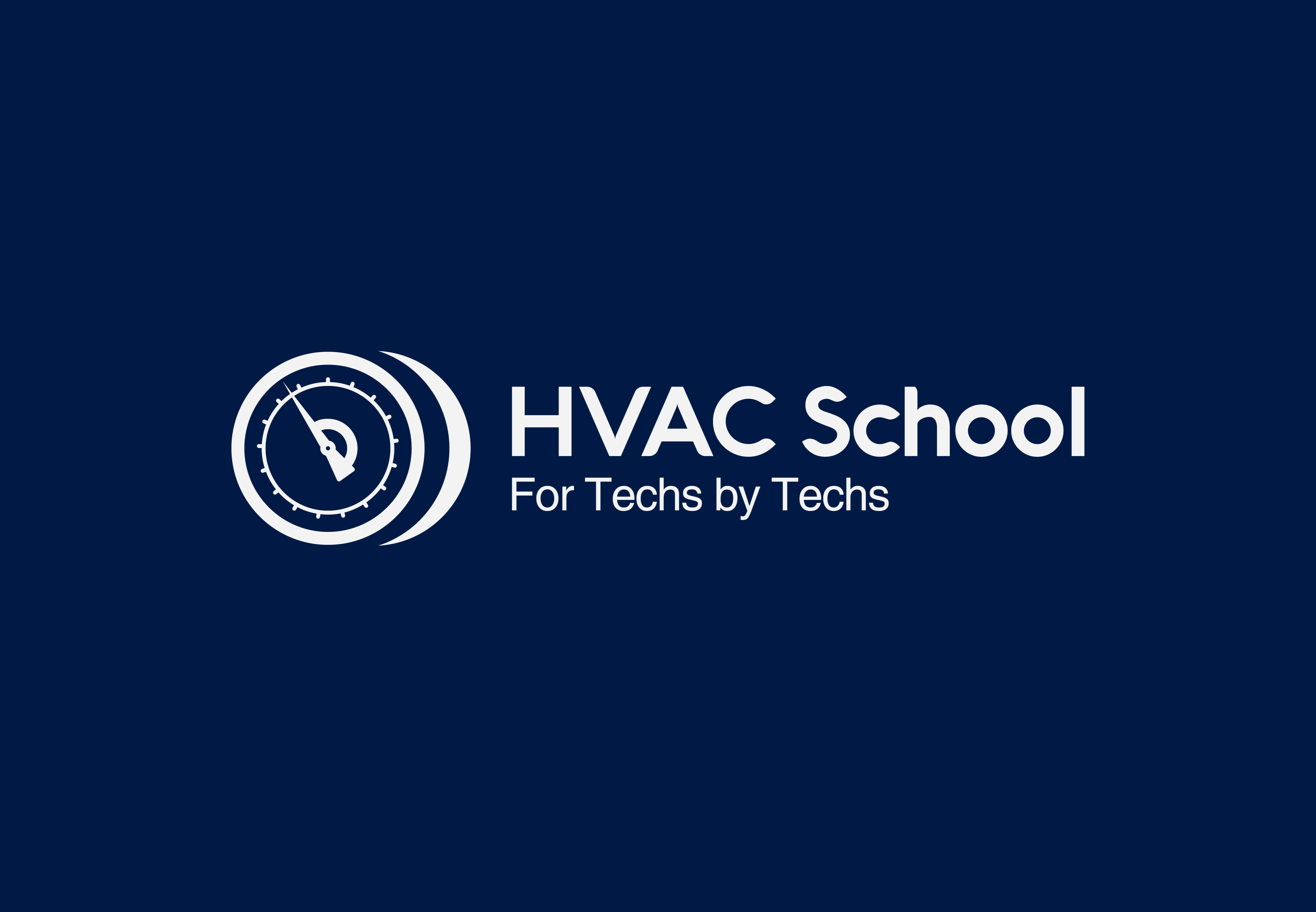
Jamie Kitchen is back on the podcast talking all about TXV / TEV bleed and non-bleed and why it matters to your compressor
Read more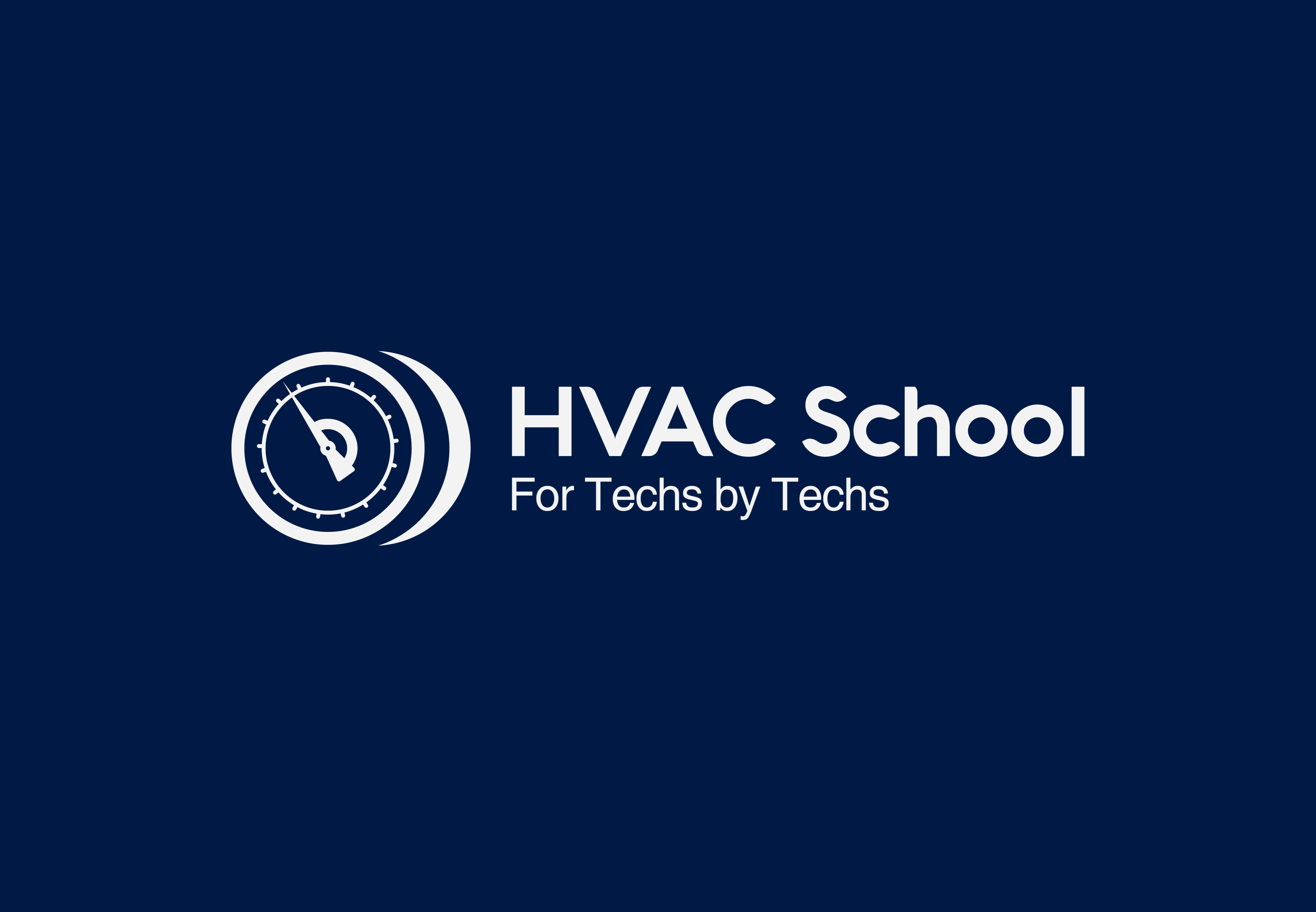
We cover why both compressor and evaporator superheat matter as well as address some common confusion related to each.
Read more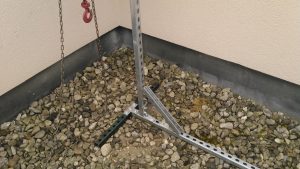
This is Part 4 series by Senior Refrigeration Tech (and prolific writer) Jeremy Smith. Pay attention to this one, folks. I know rigging and safe lifting practices may be boring to some of you, but it could very well save your back or your life. Disclaimer This article is written by a technician representing his […]
Read more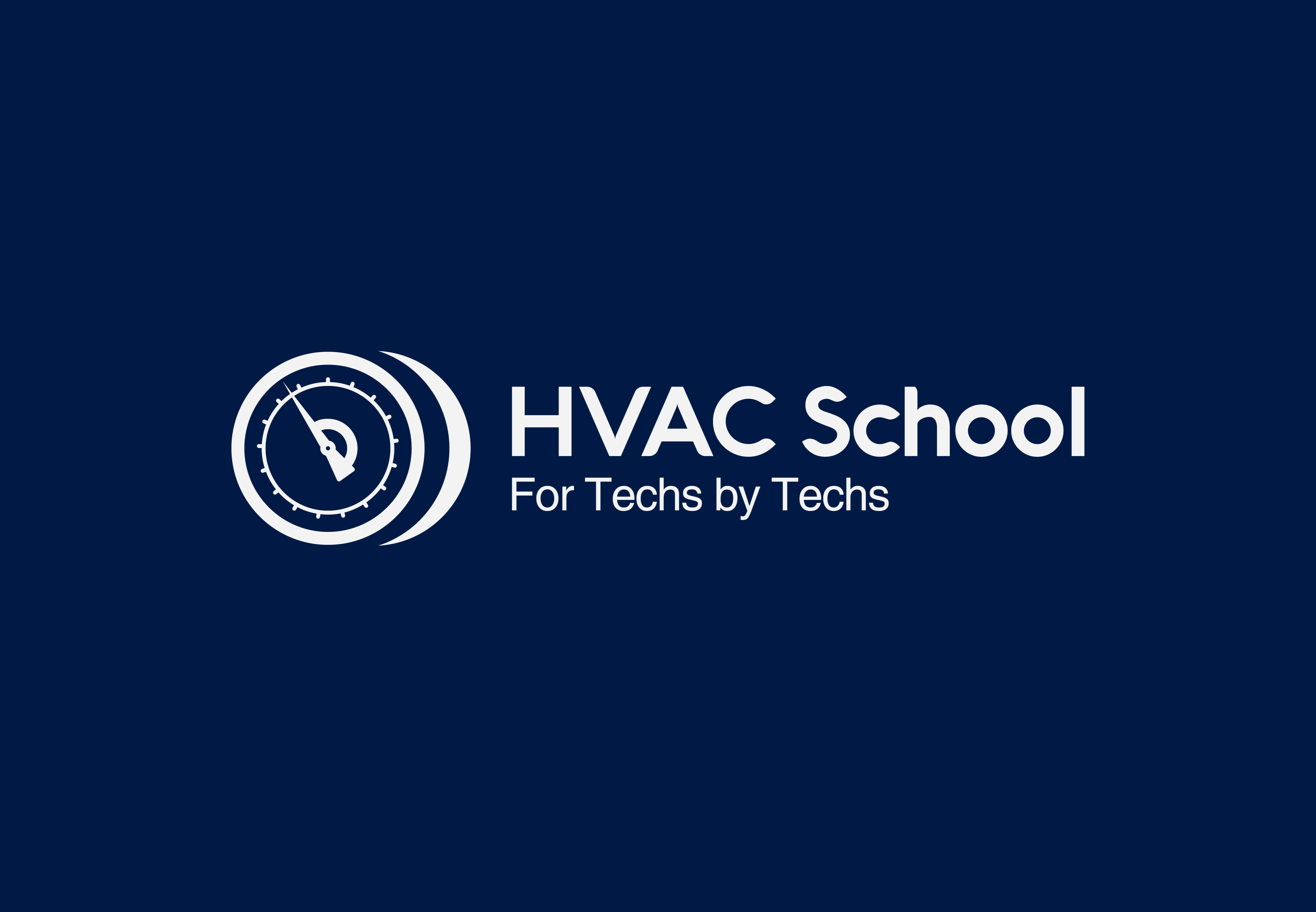
We talk evacuation, conductance speed, microns, core removal, decay rate and all that other nerdy vacuum stuff with Jim Bergmann
Read more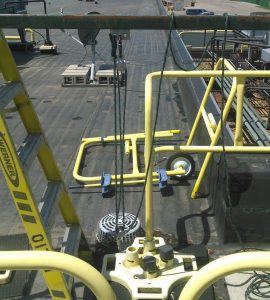
This is Part 3 series by Senior Refrigeration Tech (and prolific writer) Jeremy Smith. Pay attention to this one, folks. I know rigging and safe lifting practices may be boring to some of you, but it could very well save your back or your life. Disclaimer This article is written by a technician representing his […]
Read more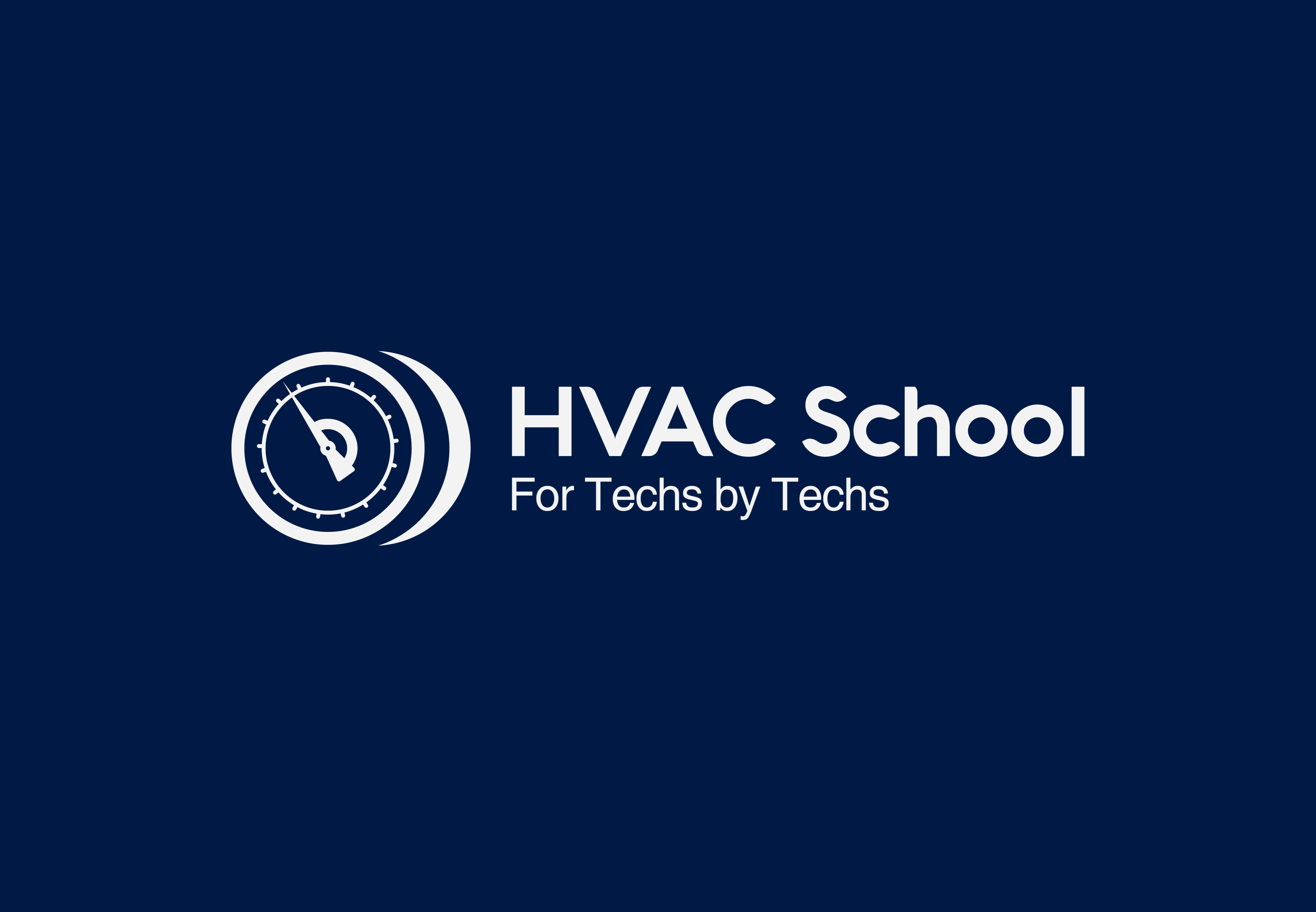
Can you really freeze water in a vaccum by pulling down too fast? what should you do about it?
Read more