September 2018
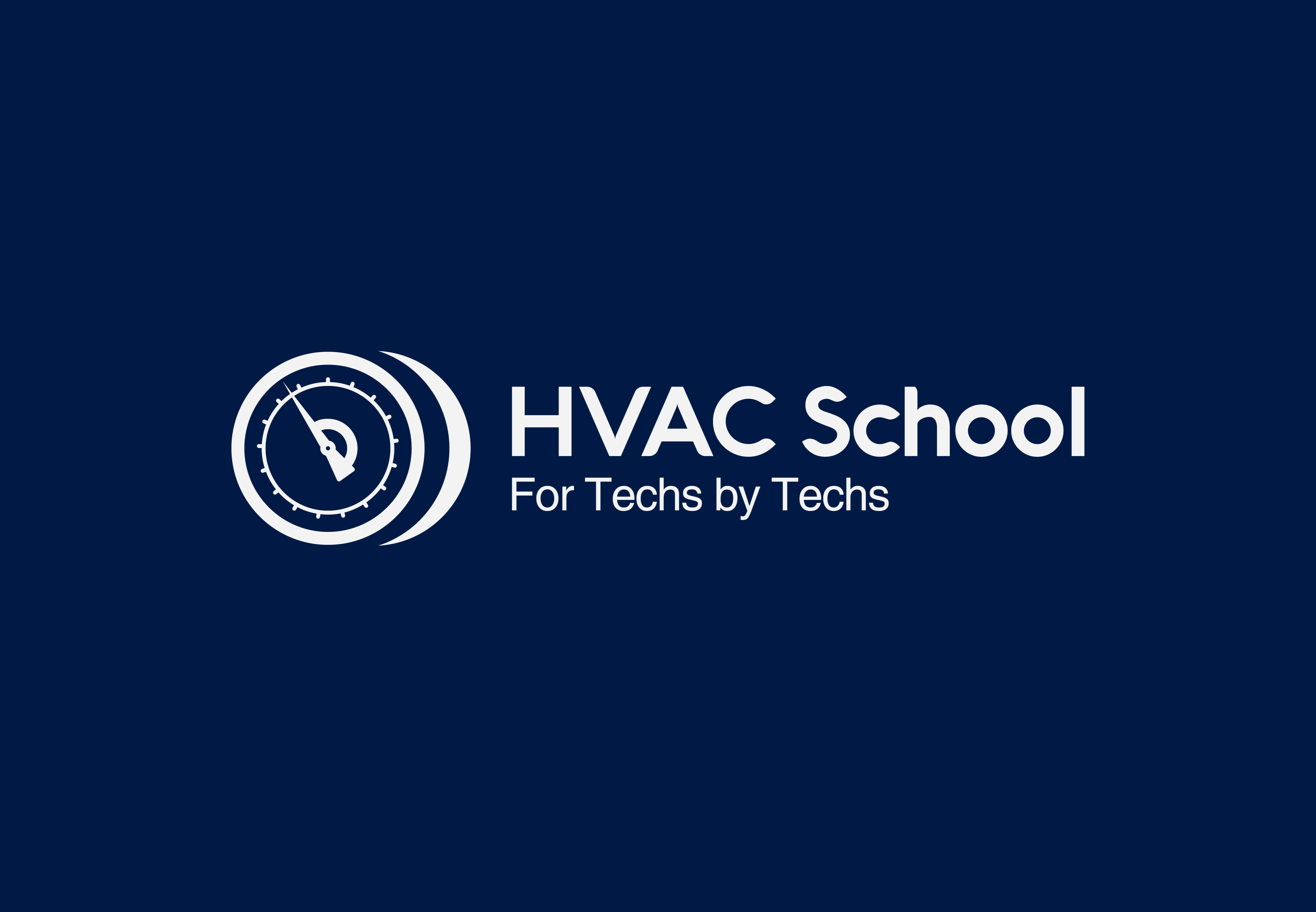
Kevin Mayer with NAVAC comes on and talks all about flaring best practices step by step. From cutting, to reaming to torque wrenches we cover flares start to finish
Read more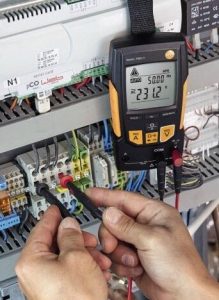
Testo 760 Category IV Multimeter I was standing at a booth at the HVAC Excellence Educators conference, and an instructor walks up, grabs a meter, and asks me, “What's the difference between a category 3 and a category 4 meter?” Well, I really wasn't sure, but I knew that the category 4 meter is rated […]
Read more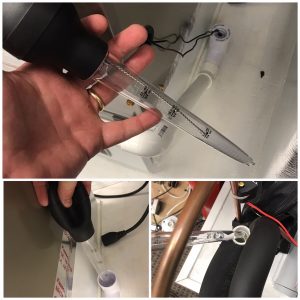
We all have some weird tools we keep in our tool bags. A baster may look suspicious, but it comes in really handy for removing water from a float switch. This one is extra handy because it comes with a nice tapered bottle brush inside it that works great to clean out the outlet port […]
Read more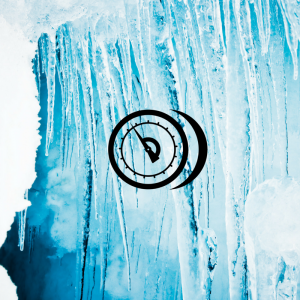
Let's take a walk through the startup and commissioning procedure of a conventional or “single” refrigeration condensing unit. We’re going to start with a unit that is fully piped in and has been pressurized for leak and strength testing. For brevity, we are going to assume a basic familiarity with industry standards, company and customer […]
Read more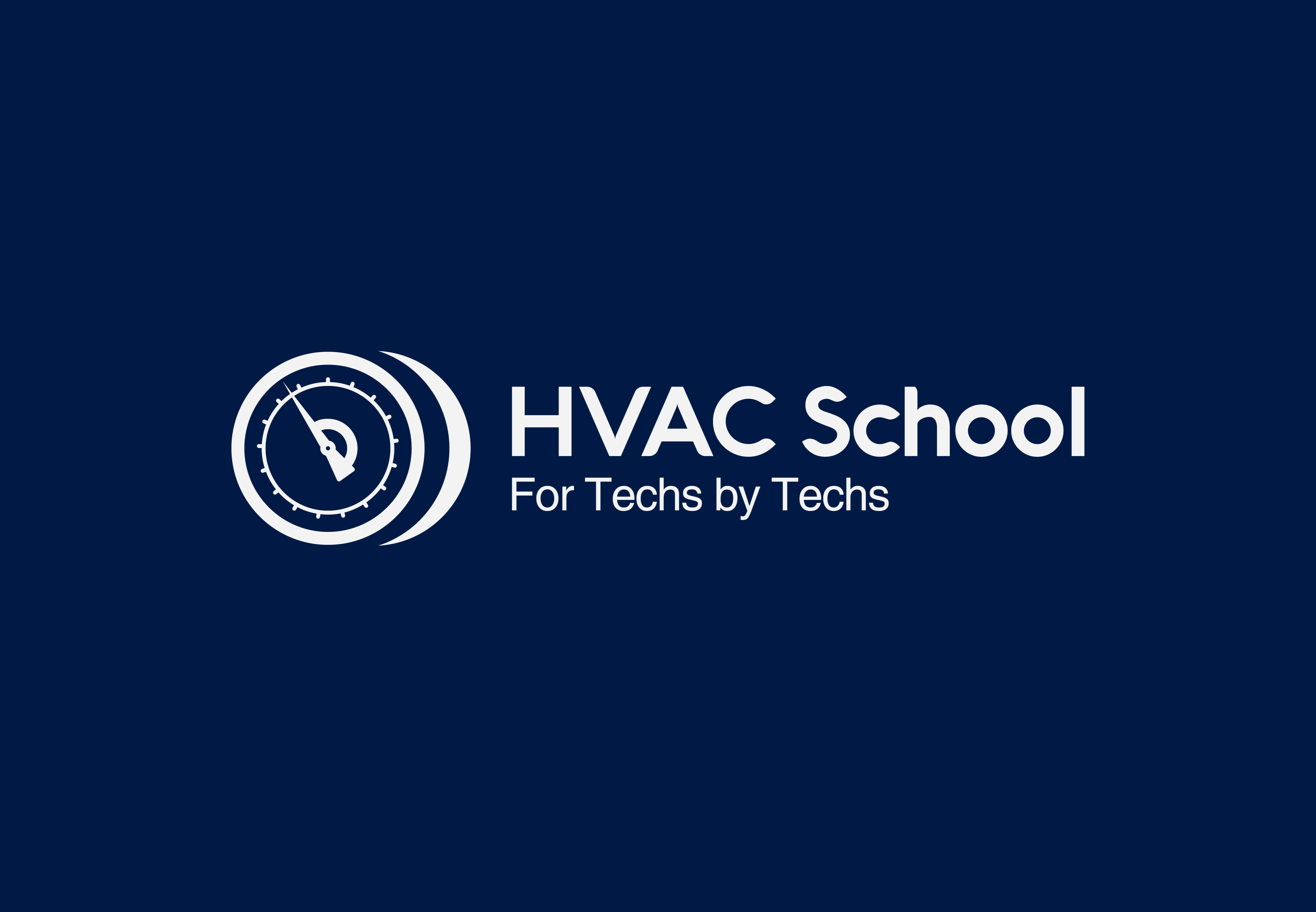
We talk about chilled water air handlers, their valve configurations and some key things to look out for
Read more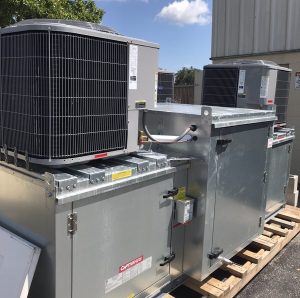
If you don't do a lot of commercial work, you may see a system like the one above and wonder what the heck it is. It is a 100% fresh air unit or a makeup air unit. You will see them more and more as codes start to reflect that balanced ventilation and conditioned outdoor […]
Read more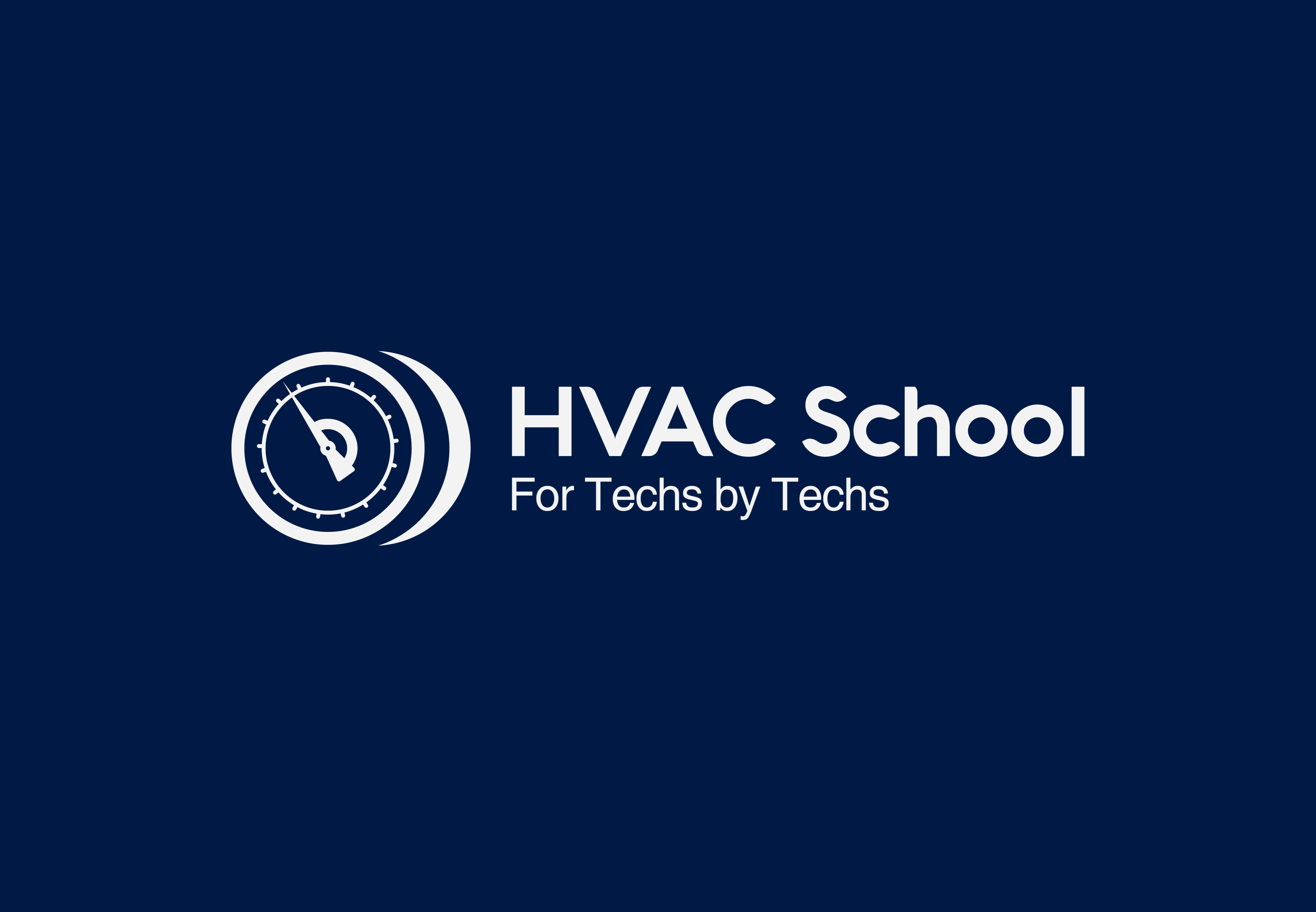
In this episode Bryan gets feedback on a podcast topic from Andy Holt and we discuss some interpersonal and other soft skills required to be a top level technician
Read more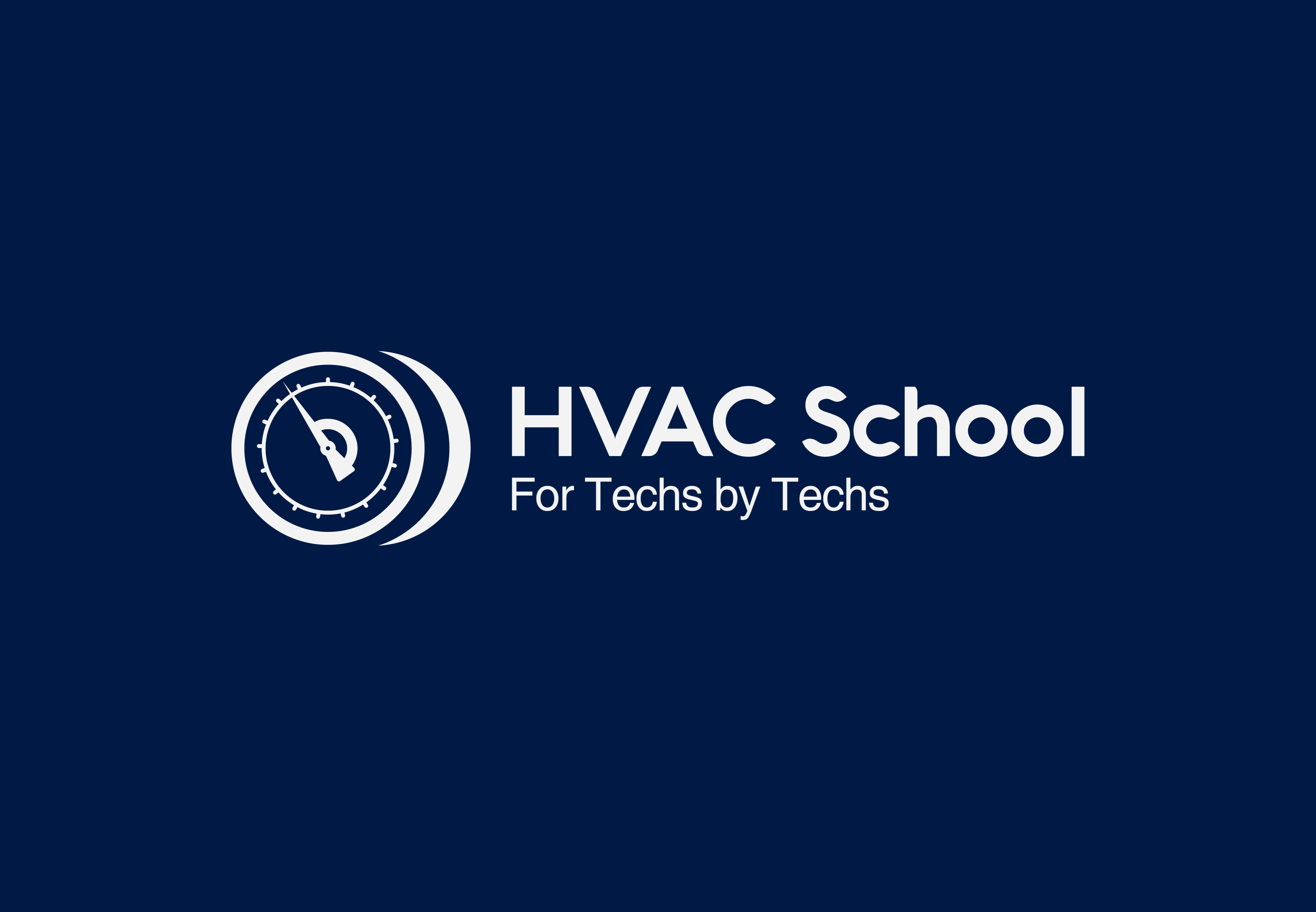
Chris Stevens from HVACR Videos on Youtube comes on and talks some refrigeration temperature controls basics
Read more